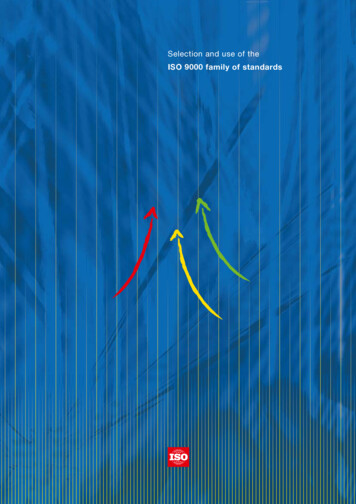
Transcription
Selection and use of theISO 9000 family of standards
ISO and internationalISO/TC 176, Qualitystandardizationmanagement and qualityassuranceISO is the International Organizationfor Standardization. It has a membershipof 158 * national standards institutes fromcountries large and small, industrializedand developing, in all regions of theworld, ISO develops voluntary technicalstandards which add value to all typesof business operations. They contributeto the dissemination of technology andgood business practice. They support thedevelopment, manufacturing and supplyof more efficient, safer and cleanerproducts and services. They make tradebetween countries easier and fairer.ISO standards also safeguard users andconsumers, and make many aspects oftheir lives simpler.ISO develops only those standards thatare required by the market. This work iscarried out by experts coming from theindustrial, technical and business sectorswhich have asked for the standard,and which subsequently put them touse. These experts may be joined byothers with relevant knowledge, such asrepresentatives of government agencies,consumer organizations, academia andtesting laboratories. Published under thedesignation of International Standards,ISO standards represent an internationalconsensus on the state of the art in thetechnology or good practice concerned.ISO’s portfolio of more than 17 800 *standards and related documentsaddresses all three dimensions ofsustainable development : economic,environmental and social.* Mid-January 2009.ISO technical committee ISO/TC 176 isresponsible for the ISO 9000 family ofstandards for quality management andquality assurance. National delegationsof 81 * countries participate in its work,while another 21 * countries have observerstatus.
Selection and useof the ISO 9000 familyof standardsThe ISO 9000 family of internationalquality management standards andguidelines has earned a global reputationas a basis for establishing effective andefficient quality management systems.The need for International Standardsis very important as more organizationsoperate in the global economy by selling orbuying products and services from sourcesoutside their domestic market.This brochure has been developedby ISO technical committee ISO/TC 176,Quality management and quality assurance,which is responsible for developing andmaintaining the ISO 9000 family. Supportingguideline standards and other documentsare developed and updated on a continualbasis to meet the needs and expectationsof users and the market itself.The brochure explains how you can usethem to improve your quality managementsystem. It provides a general perspectiveof the ISO 9000 family of standards.It is an overview of the standards anddemonstrates how, collectively, they forma basis for continual improvement andbusiness excellence.ISO 9001 specifies the basicrequirements for a quality managementsystem (QMS) that an organization mustfulfil to demonstrate its ability to consistentlyprovide products (which include services)that enhance customer satisfaction andmeet applicable statutory and regulatoryrequirements.The standard can be used forcertification/registration and contractualpurposes by organizations seekingrecognition of their quality managementsystem. ISO 9001 has been organized ina user-friendly format with terms that areeasily recognized by all business sectors.You will obtain the greatest valueby using the entire family of standardsin an integrated manner. It is highlyrecommended that you use ISO 9000 tobecome familiar with the basic conceptsand the language used before youadopt ISO 9001 to achieve a first level ofperformance. The practices described inISO 9004 may then be implemented tomake your quality management systemmore effective and efficient in achievingyour business goals and objectives.The ISO 9001 and ISO 9004 standardshave been written to enable you to relatethem to other management systems(e.g. environmental), or to sector specificrequirements (such as ISO/TS 16949 inthe automotive industry) and to assist youin gaining recognition through national orregional award programmes.This brochure provides you with :99 An overview of the ISO 9000 corestandards9 9 A step-by-step process to implementa quality management system99 Examples of typical applications ofthe documents, and99 Information on the ISO 9000 familyof standards.Selection and use 2009–1
The ISO 9000 family –core standardsThe ISO 9000 standard provides thefundamentals and vocabulary used inthe entire ISO 9000 family of standards.It sets the stage for understanding thebasic elements of quality managementas described in the ISO standards. ISO9000 introduces users to the eight QualityManagement Principles as well as theuse of the process approach to achievecontinual improvement. (See Figure 1 ).ISO 9001 is used when you areseeking to establish a quality managementsystem that provides confidence inyour organization’s ability to provideproducts that fulfil customer needs andexpectations.It is the standard in the ISO 9000 familyagainst whose requirements your qualitymanagement system can be certified byan external body. The standard recognizesthat the term “product” applies to services,processed material, hardware and softwareintended for your customer.There are five sections in the standardthat specify activities that need to beconsidered when you implement yoursystem :9 9 Overall requirements for the qualitymanagement system and documentation9 9 Management responsibility, focus, policy,planning and objectives9 9 Resource management and allocation9 9 Product realization and processmanagement, and9 9 Measurement, monitoring, analysis andimprovement.Continual improvement ofthe quality management systemManagementresponsibilityCustomers(and otherinterestedparties)Measurementanalysis igure 1 – the ISO 9000 process approach2 – Selection and use 2009Customers(and tisfactionOutput
The requirements in four of the sectionsare applicable to all organizations – Qualitymanagement system, Managementresponsibility, Resource management, andMeasurement, analysis and improvement.The Product realization section maybe tailored to meet the needs of yourorganization. Your quality manual or otherdocumentation will demonstrate how youmeet the ISO 9001 requirements in yourcompany.parties. Both standards apply a processapproach. Processes are recognizedas consisting of one or more linkedactivities that require resources and mustbe managed to achieve predeterminedoutput. The output of one process maydirectly form the input to the next processand the final product is often the result of anetwork or system of processes. The eightQuality Management Principles provide thebasis for the performance improvement.Together, the five sections of ISO 9001define what you should do to consistentlyprovide product that meets customerand applicable statutory and regulatoryrequirements. In addition, you will seek toenhance customer satisfaction by continualimprovement of your quality managementsystem.ISO 9004 gives guidance on awider range of objectives of a qualitymanagement system than does ISO 9001,particularly in managing for the long-termsuccess of an organization. ISO 9004 isrecommended as a guide for organizationswhose top management wishes to extendthe benefits of ISO 9001 in pursuit ofsystematic and continual improvement ofthe organization’s overall performance.However, it is not intended for certificationor contractual purposes.Further guidance can also be foundin the ISO 9001:2008 Introduction andSupport Package prepared by ISO/TC 176subcommittee SC 2 which provides furtherguidance on :9 9 Terminology9 9 ISO 9001:2008 Clause 1.2 (Application)9 9 Documentation requirements9 9 The process approach9 9 Outsourced processes9 9 Implementation9 9 Frequently asked questions (FAQs).ISO/TC 176 maintains a database ofapproved interpretations of the ISO 9001standard.ISO 9004 is used to extend the benefitsobtained from ISO 9001 to all partiesthat are interested in or affected by youroperations. Interested parties include youremployees, owners, suppliers, partnersand society in general.ISO 9001 and ISO 9004 arecompatible and can be used separatelyor in combination to meet or exceedexpectations of customers and interestedISO 19011 covers the area of auditingof quality management systems andenvironmental management systems.It provides guidance on the auditprogrammes, the conduct of internalor external audits, and information onauditor competence. ISO 19011 providesan overview of how an audit programmeshould operate and how managementsystem audits should take place.Effective audits ensure that animplemented QMS meets the requirementsspecified in ISO 9001.The nature of your organization andyour specific needs will determine howyou apply these standards to achieve yourgoals and objectives. Useful hints and tipsfor conducting audits have been developedby the ISO 9001 Auditing Practices Group.Information on third party auditing has alsobeen developed by the joint ISO-IAF(International Accreditation Forum)Accreditation Auditing Practices Group.Selection and use 2009–3
Implementing and maintaininga quality management systembased on the ISO 9001 standardThe implementation process is importantin achieving the full benefits of the qualitymanagement system (QMS). Most newusers will obtain measurable payback earlyin the process.For a successful implementationof your QMS, these seven steps arerecommended :1Fully engagetop management to¾ ¾ Define why you want to implementISO 9001¾ ¾ Define your mission, vision, andvalues in your organization¾ ¾ Define your organization’sstakeholders : customers, suppliers,stockholders, employees, society,etc.¾ ¾ Define your quality policy, and¾ ¾ Define and align organizationalobjectives and related product/service quality objectives.4 – Selection and use 20092Identify key processes and theinteractions needed to meetquality objectives3Implement and managethe QMS and its processes(using process managementtechniques)
4Build your ISO 9001-based QMS¾ ¾ Identify ISO 9001 requirements¾ ¾ Map these requirements withyour implemented QMS, whereapplicable¾ ¾ Make a gap analysis : identifywhere in your existing systemthe requirements are fulfilled, andwhere they are not¾ ¾ Include in your QMS processes theactivities, procedures and controlsneeded.5Implement the system, traincompany staff and verifyeffective operation of yourprocesses6Manage your QMS¾ ¾ Focus on customer satisfaction¾ ¾ Monitor and measure the operationof your QMS¾ ¾ Strive for continual improvement¾ ¾ Consider implementing businessexcellence models in the companyoperations.7If necessary, seek third partycertification/registration of theQMS or alternatively, issue aself-declaration of conformitySelection and use 2009–5
Process modelof the ISO 9000 familyof standardsThe accompanying diagram depictsthe relationships of the standards in theISO 9000 family and where they may beapplied when implementing your qualitymanagement system.Figure 2 – Application of ISO/TC 176standards in the process approach.NOTE : See page 11 for a complete listing ofstandards developed by TC 176.Continual improvement ofthe quality management systemISO 1 0 0 1 3ISO 1 0 0 1 4PlanCustomers(and s(and otherinterestedparties)Measurementanalysis andimprovementResourcemanagementI S O 10 01 5I S O 10 01 nI S O 1 00 01I S O 1 00 02I S O 1 00 03I SO 1 9 0 1 1SatisfactionISO 1 0 0 0 4ISO 1 0 0 1 2ISO 1 0 0 1 7ProductI SOI SOI SOI SOOutput10005100061000710017Foundation for establishment of QMS:ISO 9000, ISO 9001, ISO 9004Quality Management Principles, ISO handbooks6 – Selection and use 2009I SO 1 0 0 0 1I SO 1 0 0 0 2I SO 1 0 0 0 3
Examples of usingthe ISO 9000 familyof standardsExample 1Example 3A metal parts fabricating companyrecognized the need to demonstrate theircapability to produce consistent qualityproduct. They first used ISO 9000 todevelop a plan to create an acceptableQMS. Next, they prepared the qualitymanual and quality system proceduresas required by ISO 9001, excluding therequirements covering product designand development because their productsare made to designs prepared by theircustomers. They implemented the QMSdescribed in their manual and proceduresand ensured the system functioned asplanned. Later, in order to bid on the supplyof parts to a major automotive company,they upgraded their quality system tomeet the automotive sector specificrequirements of ISO/TS 16949.An electrical appliance manufacturerhad a well-established company cultureof continual improvement and effectiveproduction control. The managementdecided to improve the company’sdevelopment processes and to implementISO 9001 to obtain certification forcommercial purposes. The companyused ISO 9004 to guide its improvementprocesses and ISO 10006 to develop aproject management plan. Regulatoryagencies demanded products be designedand packaged recognizing the end of lifedisposition of products and packaging.The company was able to use the designand document control requirements inISO 9001 to satisfy regulators ofcompliance to new requirements.Example 2A welfare agency decided to improvethe quality of the services it provided toclients. It adopted ISO 9004 as the basisfor implementing its system and planningfor improvements. The agency recognizedthat ISO 9000 provided very usefuladditional guidance in terminology andunderstanding and applying QMS conceptsto their system. They mapped the resultingsystem processes to requirementsidentified in ISO 9001. They planned to seekcertification to ISO 9001 to gain recognitionand credibility from clients and supporters.Selection and use 2009–7
Example 4Example 6A large chemical processing companywas required by its major customersto gain certification to ISO 9001 and tobe environmentally friendly. To addressthese issues, the company leadershipplanned a comprehensive managementstrategy linking their QMS and anenvironmental management system(EMS). A thorough review of their businessprocesses indicated that all elements ofISO 9001 were applicable to their qualitymanagement system and the Annex inISO 9001 provided the information neededto effectively link it to the ISO 14001 EMSstandard. The company used ISO/TR 10013to guide the development of the requireddocumentation in its various productiondivisions, ISO 10015 for guidance in thepreparation of training plans for theiremployees and ISO 19011 for auditingboth the QMS and EMS. Managementachieved additional benefits and continualimprovements using ISO 9000 andISO 9004.A computer software developerserving a niche market recognizedthat as their user base expanded theywould be faced with issues concerningproduct management including newproduct development and configurationcontrol. Changes to base products, userhardware and regulatory requirementswere compounding customer serviceissues. The company used ISO/IEC 90003(QMS for software) when developing newsoftware and incorporating new features inexisting product lines. ISO 9004 providedthe guidance they needed to establishdocumented procedures to implementchange control and software improvement.ISO 10006 and ISO 10007 providedadditional assistance as they managedthe project and prepared procedures forconfiguration management. They lateracquired another software developer andwere able to use their QMS to guide theintegration of the acquisition into their ownstructure very quickly with a minimum ofdisruption to customers.Example 5A firm of international lawyers wantedto improve their client managementprocesses using the systematic approachfound in ISO 9001, but did not intend togain certification. Their QMS providesfor the design and development ofnew services such as internationaltax planning and modifying traditionalservices to meet the requirements of newor amended legislation. They includedpurchasing control to cover the selectionof computer hardware and software, aswell as purchasing the services of specialistlawyers as needed. After successfullyimplementing ISO 9001, they used theself-assessment guidelines of ISO 9004 tomonitor their progress as they improvedtheir QMS to achieve greater clientsatisfaction.8 – Selection and use 2009Example 7A bank decided to implement a qualitymanagement system for its on-line Internetbanking services. They used ISO 10019in the selection of a consultant to guidethem in their QMS implementation. Theyensured that their quality manual madeclear that their other conventional bankingservices were not included in their qualitymanagement system. While adoptingthe requirements of ISO 9001, the bankobtained guidance from ISO 9000to interpret words and phrases used inthe standard for their application. Theyapplied all the requirements of the productrealization section (Clause 7), recognizingthat design and development is animportant part of creating new serviceprocesses. The bank used ISO/TR 10013 toprepare their documentation, which theyposted on their internal computer networkto ensure current procedures are availableto their staff.
Example 8A franchise organization had difficultymaintaining consistent operation byfranchisees and determined that anenhanced management system wasrequired. They learned that ISO 9001included the tools they needed and withthe help of ISO/TR 10013 they developedthe quality manual and quality systemprocedures to be used throughout thefranchise network. To ensure a consistentapproach in managing customersatisfaction, they used guidance found inISO 10001, ISO 10002 and ISO 10003.When the system was implemented, thefranchise organization used ISO 19011 toestablish an audit programme to confirmthat the ISO 9001-based QMS continued tofunction as required and was improved ona continual basis.Selection and use 2009–9
Maintaining the benefits andcontinual improvementquality system objectives are to changingcircumstances. This information can alsobe used to improve the performance of allyour business processes.Most new users of the ISO 9000 familyof standards obtain measurable benefitsearly in the process of implementingthe requirements in their operations.These initial benefits are generally due toimprovements in their organization andinternal communication. The benefitsmust be strengthened through effectiveinternal auditing and management reviewof system performance. Like all systems, iteither improves or becomes less effective.It does not remain static for long.ISO 10014 provides guidelines forrealizing financial and economic benefitsfrom the application of the ISO 9000 QualityManagement Principles. It is directed totop management of the organization andcomplements ISO 9004 for performanceimprovements.When you adopt ISO 9001, you muststrive to satisfy your customers and toachieve continual improvement of youroperations through the QMS.Continual improvement is a processof increasing the effectiveness of yourorganization to fulfill to quality policy andyour quality objectives that you haveestablished which are updated periodically.ISO 9001 requires that you plan andmanage the processes necessary tocontinually improve your QMS.ISO 9004 provides information you canuse to go beyond ISO 9001 to strengthenthe competitive position and to provideimprovements to operational efficiency.It is recommended that you obtain datafrom various sources, both internal andexternal, to assess how appropriate your10 – Selection and use 2009Many organizations expand theirmanagement systems by extendingthe ISO 9001 structure to include therequirements of other managementsystems standards, including ISO 14001,Environmental management systems.The structural and organizationalrequirements of ISO managementsystems standards are designed to becompatible.
Current standards from ISO/TC 176and its subcommitteesStandard/ documentTitleEditionISO 9000:2005Quality management systems – Fundamentals andvocabularyThirdISO 9001:2008Quality management systems – RequirementsFourthISO 9004:2000Quality management systems – Guidelines forperformance improvementsSecondISO 10001:2007Quality management – Customer satisfaction –Guidelines for codes of conduct for organizationsFirstISO 10002:2004Quality management – Customer satisfaction –Guidelines for complaints handling in organizationsFirstISO 10003:2007Quality management – Customer satisfaction –Guidelines for dispute resolution external to theorganizationFirstISO 10005:2005Quality management – Guidelines for quality plansSecondISO 10006:2003Quality management – Guidelines for qualitymanagement in projectsSecondISO 10007:2003Quality management – Guidelines for configurationmanagementSecondISO 10012:2003Measurement management systems – Requirementsfor measurement processes and measuring equipmentSecondISO/TR 10013:2001Guidelines for quality management systemdocumentationFirst *ISO 10014:2006Quality management – Guidelines for realizing financialand economic benefitsFirstISO 10015:1999Quality management – Guidelines for trainingFirstISO/TR 10017:2003Guidance on statistical techniques for ISO 9001:2000SecondISO 10019:2005Guidelines for the selection of quality managementsystem consultants and use of their servicesFirstISO/TS 16949:2002Quality management systems – Particular requirementsfor the application of ISO 9001:2000 for automotiveproduction and relevant service part organizationsSecondISO 19011:2002Guidelines for quality and/or environmentalmanagement systems auditingFirstNote : TR – Technical Report, TS – Technical Specification* First edition as a TR, replacing the International Standard ISO 10013:1995.Selection and use 2009–11
The futureFor further informationof the ISO 9000 familyIn order for the ISO 9000 family tomaintain its effectiveness, the standardsare periodically reviewed to benefitfrom new developments in the qualitymanagement field and also from userfeedback. ISO/TC 176, comprising expertsfrom businesses and other organizationsaround the world, monitors the use ofthe standards to determine how they canbe improved to meet user needs andexpectations when the next revisionsare due. All ISO standards are reviewedregularly for relevancy; changes are madewhen there is a demonstrated need toimprove the standard.Based on input from the usercommunity, ISO/TC 176 will continueto evaluate and adopt new conceptsin the field of quality management forincorporation into ISO standards.This can include sector specific initiativesand supporting documents within theISO 9000 family. Most ISO technicalcommittees recognize the structure ofISO 9001 when new management systemsstandards are developed for other orspecific purposes.ISO’s commitment to sustaining theISO 9000 momentum through reviews,improvement and streamlining of thestandards guarantees that your investmentin ISO 9000 today will continue to provideeffective management solutions well intothe future.12 – Selection and use 2009Web sitesISO :www.iso.orgISO/TC 176 :www.tc176.orgISO/TC 176 subcommittee SC 2 :www.iso.org/tc176/sc2Information on the ISO 9000 standardsis also available from ISO’s nationalmember bodies – www.iso.org/isomembers – and from the ISO Website – www.iso.org – Managementstandards pages.Sales enquiries should also be directedto the ISO members or to the ISO CentralSecretariat sales department –sales@iso.org.ISO publishes the bimonthly magazineISO Management Systems –www.iso.org/ims – which providesupdates on its families of standardsmanagement system and news on theirimplementation around the world.The magazine is available in English, Frenchand Spanish editions.ISO Focus magazine – www.iso.org/isofocus – gives an overview of ISOand its standards and also includes articleson its management systems standards. It ispublished 11 times a year in English only.
ISO Central Secretariat1, chemin de la Voie-CreuseCase postale 56CH - 1211 Genève 20SwitzerlandE-mail central@iso.orgWeb www.iso.orgISBN978-92-67-10494-2 ISO, 2009-02/5000. All rights reserved
Selection and use of the ISO 9000 family of standards The ISO 9000 family of international quality management standards and guidelines has earned a global reputation as a basis for establishing effective and efficient quality management systems. The need for Intern