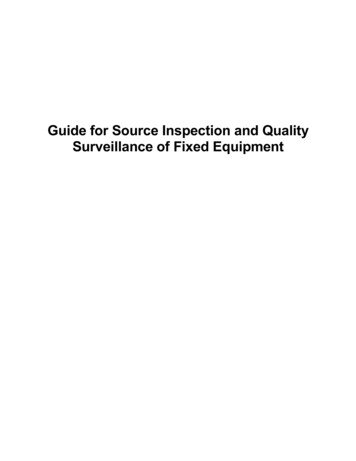
Transcription
Guide for Source Inspection and QualitySurveillance of Fixed Equipment
ForewordThis guide has been developed to provide information for source inspectors for the purpose of providing aconsistent method of Supplier/Vendor (S/V) quality surveillance for the oil, petrochemical and gasindustries. It is intended as a resource for individuals studying to take the API Source InspectorCertification examination. Other references contained herein will also be necessary for individuals tobecome familiar with in order to pass the examination and to perform satisfactorily in the sourceinspection job. This study guide is also intended as a draft from which an API Recommended Practice forSource Inspection could eventually be formulated and published utilizing the ANSI standardizationprocess.iii
Table of Contents1Scope/Purpose . 12Introduction . 23References . 24Definitions, Abbreviations and Acronyms. 35Training . 105.1General . 106Source Inspection Management Program. 107Project Specific Source Inspection Planning Activities . 117.1General . 117.2Equipment Risk Assessment . 117.3Development of a Source Inspection Project Plan. 137.4Development of Inspection and Test Plans . 137.5Selection of an Inspector . 137.6Coordination of Inspection Events . 137.7Report Review . 138Source Inspection Performance . 148.1Inspector Conduct and Safety . 148.2Review of Project Documents . 148.2.1General . 148.2.2Contractual Agreements . 148.2.3Engineering Design Documents. 148.2.4Company and Client Standards . 158.2.5Industry Codes and Standards. 158.2.5.1General . 158.2.5.2API Codes and Standards . 158.2.5.3ASME Codes and Standards . 168.2.5.4ASNT Standards . 198.2.5.5AWS Standards and References . 198.2.5.6SSPC Standards . 208.2.6Welding Procedures and Qualifications . 208.2.7NDE Procedures . 208.2.8Project Schedules . 218.3Performing the Source Inspection . 21v
8.4Source Inspection Work Process Scheduled Planning Events . 218.4.1General . 218.4.2Pre-purchase Meeting (Prior to Contract Placement) . 218.4.3Pre-inspection Meeting (Prior to Start of Fabrication) . 218.5Report Writing . 228.6Nonconformance/Deviations . 238.7Source Inspection Project Continuous Improvement . 238.8Source Inspector Continuous Improvement . 249Examination Methods, Tools and Equipment . 249.1General . 249.2Review and Confirmation of Materials of Construction . 249.3Dimensional Inspections . 259.4Visual Inspections . 259.5Nondestructive Examination (NDE) Techniques . 269.5.1General . 269.5.2Penetrant Testing (PT) . 269.5.3Magnetic Testing (MT) . 269.5.4Radiographic Testing (RT) . 269.5.5Ultrasonic Testing (UT) . 269.5.6Hardness Testing (HT) . 269.5.7Positive Material Identification (PMI) . 269.6Destructive Testing . 269.7Pressure/Leak Testing . 279.7.1General . 279.7.2Pressure Testing . 279.8Performance/Functional Testing . 289.9Surface Preparation/Coatings Inspections . 2810Final Acceptance . 2811Manufacturing and Fabrication (M&F) Processes . 2911.1General . 2911.2Welding Processes and Welding Defects . 3011.3Casting . 3011.4Forging . 3111.5Machining . 3111.6Assembly . 32vi
11.7Metallurgy Issues Associated with Manufacturing and Fabrication Processes . 3211.7.1The Structure and Metals . 3211.7.2Physical Properties of Metals . 3211.7.3Mechanical Properties of Metals . 3211.7.4Hardness and Hardenability of Metals . 3211.7.5Weldability of Metals . 3311.7.6Preheating and Postweld Heat Treatment . 331211.7.6.1Preheating . 3311.7.6.2Postweld Heat Treatment (PWHT). 3311.7.6.3Other Heat Treatments. 34Pressure Vessels . 3412.1General . 3412.2Vessel Methods of Construction . 3412.3Vessel Materials of Construction. 3412.4Vessel Internal Components . 3612.5Vessel Design and Construction Standards . 3612.6Dimensional Check of Pressure Vessels . 3712.7Heat Exchangers . 3813Piping . 3913.1General . 3913.2Valves . 3913.3Flanges . 4013.4Fittings . 4214Structural Components. 42Annex A . 44Annex B .45Annex C .51vii
Guide for Source Inspection and Quality Surveillance of Fixed Equipment1Scope/PurposeThis study guide covers the process of providing quality surveillance of materials, equipment andfabrications being supplied for use in the oil, petrochemical and gas Industry, including upstream, midstreaman
17.09.2015 · inspection work process events, filing nonconformance reports and source inspection report writing. The “Checking” part, covered in Section 8.7, involves looking back at all the source inspection activities that occurred in the Planning and Doing segments to see what went well and what should be improved based on the results of that look .