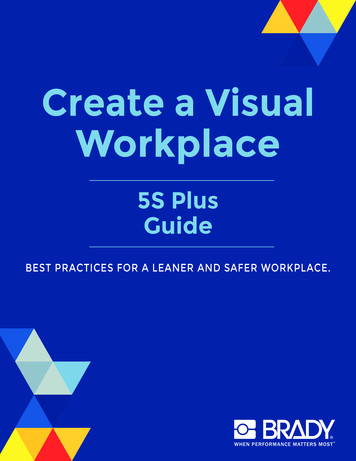
Transcription
Create a VisualWorkplace5S PlusGuideBEST PRACTICES FOR A LEANER AND SAFER WORKPLACE.
TABLE OF CONTENTS3CHAPTER 1What is Visual Workplace & Why Do You Need It?Get up-to-speed on how you can reduce waste, improveproductivity & increase employee knowledge.12CHAPTER 2Meet 5S Plus SafetyIt’s the foundation you need to create and sustain aclean, orderly and safe workplace.16CHAPTER 3“5S Plus” in Action!See examples of just what you can do with thepower of 5S Plus.29CHAPTER 4Faceoff: DIY vs. Pre-Made Signs & LabelsNow that you know workplace visuals are important –how do you implement them?
CHAPTER 1What is a VisualWorkplace & Why DoYou Need It?Let’s begin with the basics of just what it means tohave a visual workplace and why it’s important.
It All Starts with Visual WorkplaceVisual workplace is a lean concept that’s all about puttingimportant information right where employees need to see it.This concept plays a critical role in some of the most popularlean tools, including 5S. That’s because it creates a sustainingbase for lean improvements to remain clearly visible, readilyunderstood and consistently adhered to.To sum it up, using labels for safety information, procedures,facility identification and a variety of other applications is agreat way to help reduce waste, enhance knowledge andimprove productivity for the long haul.Did you know? 95%Waste accounts forChapter 1 / 4of allcostsin non-lean manufacturingenvironments.1
KANBAN BOARDKANBAN BOARDREORDERON ORDERANANB erKRadRDE m leREO e to tea lovesTak ylon G 222Nt #2ksPar 10 pacreOrdANANB erKRadRDE m leREO e to tea lovesTak ylon G 222Nt #2ksPar 10 pacreOrdWhat if a label.Reduced waste by giving employees theinformation they need to complete a taskefficiently?Chapter 1 / 5
Let’s explain how visual workplace helps youReduce Waste You might be surprised to learn that only a fraction of your activitiesactually add value for your customers. In fact, Taiichi Ohno,co-developer of the Toyota Production System, suggests thatwastes account for up to 95% of all costs in non-lean manufacturingenvironments.This waste is typically caused by information gaps – employeessimply not knowing the best way to get the job done. Instead, timeis wasted searching, waiting, retrieving and doing rework.With a visual workplace, employees have the information theyneed to effectively do their jobs. And when employees know howto tackle their jobs well, your facility benefits from significantimprovements. For example, when your storeroom shelves arewell labeled, employees don’t have to waste time searching forsomething or accidentally grabbingthe wrong thing. You improveefficiency by helping them findwhat they need at a glance.?Chapter 1 / 6Did you know?78 millionbaby boomers are expectedto retire over the next 10-15years?2 Visuals help lessexperienced employeeslearn the job quickly andeffectively.
?Did you know?75% of knowledgeis gained through visuals13% through hearing and 12% through smell,touch and taste.3Chapter 1 / 7
Enhance Knowledge We have another statistic for you. Did you know that people gain75% of their knowledge from visuals? That’s why employees needeffective workplace signs and labels that enhance training andmake doing their jobs easier. A good visual tells an employeeexactly what procedural and safety information they need to know,and when and where they need to know it.Knowledge-based visuals can include: Procedure labels – Get procedures out of binders and ontothe shop floor where employees can see them and usethem daily. B ilingual signs – With a growing workforce speakingdifferent languages, it’s important to have the right languageson your signs and labels to keep everyone in the know. P ipe markers – Quickly and easily give employees andcontractors the knowledge of what’s in a pipe and whichdirection it flows. S afety signs – Tell employees what is dangerous, why it isdangerous and the correct precautions to take to stay safe. E lectrical disconnect labels – Right on your equipment, tellemployees where to find the disconnect switch in order toavoid accidents and save lives.With workplace visuals like these, employees have the knowledgethey need to eliminate non-value-added waste, improve safety andcompliance, and enhance workplace organization.Chapter 1 / 8
What if a label.Saved time and ensured equipmentperformance by indicating proper workingconditions at a glance?Chapter 1 / 9
Improve ProductivityWe all know productivity is a big concern for any company. Andyou’re in luck, because creating an effective 5S visual workplacegoes a long way in improving productivity. But don’t just take ourword for it. Dr. Brian Harston, lean leader with a Master of Sciencedegree in manufacturing management with an emphasis in leanimplementation and a Doctorate of Business Administration inProject Management, shares his own experiences:Tool Labeling Saves 1 Million/DayA manufacturing company was experiencing an exorbitant amountof tools being checked out of the tool crib every day. Through a 5Srapid improvement event, it was identified that the core problemwas tool mis-identification, leading to workers wasting an averageof 45 minutes per shift searching for tools.The corporation decided to label each tool according to work-cell andoperator and create a new mobile work cart with shadowboards tostore tools. With this system in place, workers no longer needed tocheck out or purchase additional tools and the corporation increasedproduction capacity of its large mining trucks that average 8 millionprice per unit. This led to an additional 1 million per day* in revenueand saved an average of 60,000 monthly in tool costs.* Large scale of savings was so due to the fact that the high-end, defense technologyindustry has annual revenue exceeding 65 billion.Chapter 1 / 10
Chapter 1 / 11Did you know?Lean manufacturing can lead up-to a40% increasein productivity.4
CHAPTER 2Meet 5S Plus SafetyIf you haven’t implemented 5S, we’ll walk youthrough it. But let’s first start with what “5S Plus”is all about.
Meet 5S Plus SafetyWhile 5S is one of the most widely adopted techniques fromthe lean manufacturing toolbox, “5S Plus” goes a step further toemphasize a critical aspect of any workplace: Safety. That wayyou benefit from a workplace that is both efficient and safe.Now, let’s explain more about the famous 5S’s. These areessential elements in establishing the operational stability youneed to both make and sustain continuous improvement. Thepoint is to create a clean, orderly and safe environment – wherethere is a place for everything and everything is in its place. Andonce you have that, 5S helps you reduce unnecessary wasteand establish the framework and discipline needed to maintainand continually improve your workplace.PLUSChapter 2 / 13
Let’s Get to Know “5S Plus Safety”Sort Eliminate non-essential items by going throughall of the tools and materials in your facility anddiscarding unused items.Shine Get the workplace clean, maintain itsappearance and use preventative measuresto keep it clean.Set in Order Focus on organizing equipment, establishingsafety measures, and creating procedures,product quality standards, and effectiveinventory and material handling.Standardize Create best practices to make the improvedworkplace a standard.Sustain Maintain momentum, ensure employees knowthe importance of workplace organization andstrive to continuous improvement.Plus Safety Make the workplace safer by looking for anypotential hazards and resolving them.Chapter 2 / 14
Key benefits to having a“5S Plus” workplaceIMPROVE Non-value-addedactivities Floor spaceutilizationMistakes madeby employees orsuppliersEmployee safetyand moraleTime foremployee trainingTime searchingfor tools, partsand supplies Unnecessarytransportationof goods andnavigation aroundthe facilityREDUCEChapter 2 / 15Product quality Equipmentreliability throughfrequent cleaningand inspections
CHAPTER 3“5S Plus” in ActionTo create and maintain an orderly, efficient and safe“5S Plus” workplace, you need a variety of durablelabels, signs and tags. When it comes to thesevisuals, the key is to ensure the message isunderstood at a glance. That means avoidingputting too much information into one visual.
RED TAGTag #1003Item Description:RED TAGLocation Found:Found by:Tag #1002Date Taged:n:Item Descriptiod:Disposition:Location Found:Found by: Date DispositioneDate Taged:Dispositioned by:Disposition:Eye Care Companyned:Date DispositioDispositionedby:panyEye Care ComWhat if a label.Helped you sort through all of your equipmentand supplies to determine what you need andwhat you don’t – right at a glance?Chapter 3 / 17
SortThe very first step of 5S is deciding what to keep and what toget rid of. This is done by sorting through all of the tools andmaterials onsite and only keeping essential items. Everythingelse is discarded to keep your workplace free of clutter andhazards. You’ll be amazed by how many materials sit aroundyour facility going unused on a daily basis and taking up space.You could use: Tags – To red-tag unused items and store them in adesignated area for employees to sift through and grabanything that is still needed. Any items left at the end offive days are discarded. F loor marking tape – To signify the “red tag” section,where employees can find equipment that will bediscarded if not claimed. R ed tag record forms – To track supplies that are keptand discarded. C amera – To take before and after photos of the area.5SSORTSHINESET IN ORDERSTANDARDIZESUSTAINChapter 3 / 18PLUS SAFETY
What if a label.Increased productivity by reducing time spentlooking for the broom?Chapter 3 / 19
ShineAnd by shine we mean clean! By eliminating dirt, dust, sourcesof contamination and other debris, as well as inspectingequipment, you can improve the safety and productivity of yourfacility. Not to mention that your workplace will look like new,making your employees proud to come to work each day.You could use: Cleaning supplies (of course!) – Including brooms, dustpans, rags, degreasers and floor cleaners. Shadowboard – To store cleaning equipment. P ersonal Protective Equipment (PPE) – Including glovesand safety glasses to keep employees safe fromhazardous cleaning supplies and debris. L ockout equipment – To protect workers from therelease of hazardous energy when performingequipment cleaning or maintenance.5SSORTSHINESET IN ORDERSTANDARDIZESUSTAINChapter 3 / 20PLUS SAFETY
Max. 4 RollsREORDERMin. 4 RollsWhat if a label.Reduced waste by showing employees thestock levels of materials at a glance?Chapter 3 / 21
Set in OrderYou’ve sorted. You’ve cleaned. Now it’s time to look for ways to reducethe sources of waste and errors in your facility and make it morevisually instructive. Easy? Not exactly. Worth it? Definitely!You need to focus on:Organizing Equipment S ign and label printers, label materials and label-creationsoftware – To quickly and easily print your own facility andequipment identification. S hadow boards – To store tools and equipment at the point of need.Establishing Safety Measures Safety signs – To inform employees of any workplace hazards. P ipe markers – To instantly tell you everything you need to knowabout pipe contents, directions of flow and level of safety.Creating Procedures P rocedure labels – To get procedures out of binders and onto theshop floor so employees can see them and use them daily. T raining signs – To put the necessary safety information right atthe point of need, leading to less training and improved safety.Establishing Product Quality Standards F loor marking tapes – To mark traffic lanes, storage locations, productsthat need to be inspected for quality assurance and more. G auge labels – To easily detect pressure or temperatureabnormalities at a glance.Creating Effective Inventory and Material Handling M agnetic or repositionable material labels – To label and organizeworkbenches, shelves, racks, bins, cabinets and totes. M inimum and maximum level indicators – To highlight overstocksituations and points where stock should be re-ordered.Chapter 3 / 22
LEAN DAILY MANAGEMENTSAFETYQUALITYDELIVERYCASHWhat if a label.Helped employees take pride in their work?Chapter 3 / 23
StandardizeYou have a good start on making your workplace leaner. Nowit’s time to expand your efforts and create best practices tokeep this a company standard. This is done with clear andconsistent roles and responsibilities, and visual controls.You could use: Job scheduling board – To visually sequence job ordersand indicate work delays or missed deadlines. S chedules and check sheets – To show whichemployees should be performing certain tasks and whenthose tasks should be completed. S upplies checkout board – To control supply usage andensure quick location. L ean Daily Management (LDM) boards – To track metricsand drive improvement. S afe state visuals – To indicate if valves or air pumps aretypically opened or closed to help prevent accidents.5SSORTSHINESET IN ORDERSTANDARDIZESUSTAINChapter 3 / 24PLUS SAFETY
ROCO TATEBE LLAR THISFTH ORE BAC GUAKRRENE AD YOU DO DWWNJO AB!What if a label.Reminded employees about that one criticalstep that always gets overlooked?Chapter 3 / 25
SustainDon’t stop now! You’ve done the work – now you need to keepit up. Maintain momentum, ensure employees understand thatworkplace organization is a top priority and strive to continuallyimprove the workplace.You could use: On-site printer, label materials and label creationsoftware – To create signs, labels and tags as needs arise. D ance charts – To help employees remember tasksequences based on a standard flow diagram. P reventative maintenance targets – To keeppreventative maintenance readings consistent bylabeling vibration and ultrasound probe points. R eplacement part visuals – To clearly identify correctreplacement parts. O ne-point lessons and labels – To help employeesremember a particularly forgettable or essential part ofa procedure.Chapter 3 / 26?Did you know?In 2014 alone, there wereOSHAHazComviolations55,161Not only does effective safetysignage help you maintaincompliance with this standard,but it helps reduce workplaceaccidents across the board.
What if a label.Prevented your employee from losing a finger?Chapter 3 / 27
Plus SafetyYou’ve got efficiency – but don’t forget about safety! Makeyour workplace safer by looking for any potential hazards andresolving them. With custom, on-demand signage you caneasily prevent costly accidents before they occur. Mostimportantly, when you have the right signage in the rightplaces, you can send employees home safely every day.You could use: GHS labels – To identify primary and secondary chemicalcontainers. ANSI safety signs – To clearly and effectivelycommunicate potential hazards throughout theworkplace and how to respond to them. LOTO labels and tags – To keep employees safe fromunexpected equipment startups during cleaning andmaintenance. Arc flash labels – To promote electrical safety andprevent electrical arc flash accidents. Fire visuals – To indicate the location of fire extinguishersand fire hose cabinets so they are readily accessible incase of an emergency. First aid identification – To identify where first aidsupplies can be found. Machine and equipment identification –To alert employees ofmachine hazardsand protect themfrom personal injuryor equipment failure.5SSORTSHINESET IN ORDERSTANDARDIZESUSTAINChapter 3 / 28PLUS SAFETY
CHAPTER 4Faceoff:Do-It-Yourself vs. Pre-MadeLabels and SignsNow that you know what types of visuals you needto create a “5S Plus” visual workplace, it’s time totake action. You’ve got two options:do-it-yourself (DIY) printing orordering pre-printed labels and signs.
SPRINKLER WTR TO EAST WHSEHOT WTR RET FROM BLR #2COLD WTR TO EXTR #7What if a label.Saved you 7,500 annually in breakdown costsby helping contractors and employees locatethe right line?Chapter 4 / 30
When compared to ordering pre-printed materials, choosingDIY is simple – It’s more cost effective, more efficient andconvenient, and you can create your own customized content.Let us explain more:It’s more COST EffectiveCan you believe printing your own labels and signs is cheaperthan purchasing them pre-printed? That’s because there is: NO purchase order charges for every order NO minimum order quantity NO inventory costs for stocking large quantities of signsand labelsWith an onsite label printer, you can simply print what youwant to print, whenever you want to print it, right at the pointof need.DIYCOST EFFECTIVEEFFICIENTCONVENIENTChapter 4 / 31CUSTOMIZED
What if a label.Reduced the severity of an accident becausethe safety equipment was clearly identified?Chapter 4 / 32
It’s more EFFICIENTThere’s no need to wait – You’ll have your labels in seconds,not days. That means there’s no time away from your currentproject because you don’t have to wait around for yourpre-made signs and labels to arrive. When you recognize theneed for new visuals in your facility, you can walk up and printwhat you need – Just like that!DIYCOST EFFECTIVEEFFICIENTCONVENIENTChapter 4 / 33CUSTOMIZED
Let’s put this into perspective:Do-it-Yourself LabelsDay 1You have a need for a label.Pre-Printed LabelsYou have a need for a label.You walk up to your printer,You do some research onchoose a material, create the label where to order and what toon a simple user interface, print it order.and apply it. Then you print more,because you can and it wouldbenefit your workplace.Your facility is just a little bitsafer and more efficient thanks toyour new labels.You either customize yourlabel or choose a generic labelto order.Day 2You decide to place the order,taking time to process theorder and provide all of thenecessary information.Day 3The waiting begins.Day 4An accident almost occursbecause the label you neededwasn’t in place to informemployees of the hazard.Day 5You wait for the label toarrive.Day 6 Still waiting.Day 7The label arrives! You put it inplace and realize you couldreally use a few more. Back tothe drawing board!Chapter 4 / 34
Lockout/Tagout Posted ed:9/13/20135LockoutPointsPurpose:Facility:Site 1 - RefrigerationDescription:Refrigeration Compressor #4Note:Location:Engine RoomThis is an example of Link360's "Long Form". The long form allows you to freelydefine theactions of each step, add photos for each step, andadd further detail that is requiredforcomplex lockout procedures. For simple lockout procedures, see the "Short Form".This procedure establishes the minimum requirements for the lockout of energyisolating deviceswhenever maintenance or servicing is done on machin es or equipment.Scope:Authorization:This procedure shall be used to ensure that the mac hine or equipment is stopped,isolated from allpotentially hazardous energy sources and locked out before employees performany servicing ormaintenance where the unexpected energization or st art-up of the machine or equipmentor release ofstored energy could cause injury.Enforcement:This procedure shall only be used by employees that have been trained as "Authorized"employeesunder OSHA 1910.147. Employees with the following j ob roles are authorized touse this procedure: lis tjob roles Failure to properly follow lockout-tagout procedure may result in corrective action.Lockout Application Process1. Notify affected personnel. 2. Properly shut down machine. 3. Isolate all energysources. 4. Apply lo ckout devices, locks, &tags. 5. Verify total de-energization of all sources.Step #1ElectricalE-1 480VLockout StepsActionPROPER PPE REQUIRED:Arc flash shield, 8 cal/cm2, class E gloves,electrical rated hardhat.InfoThe E-1 Disconnect is located to the West ofthe machine. Turn Disconnect to the offposition and lock out. Use a Lock and haspdevice.2!-1NoteFor the next step, you will need to obtain auniversal lock and chain device from theLockout/Tagout Station, located on the Westwall of the Engine Room.E-1Upon re-energization, return universal lock andchain device to the Lockout/Tagout Station.Page 1 of 3What if a label.Used a Visual Lock Out Procedure (VLOP) to tellyou the right way to lockout each unique pieceof equipment, keeping employees safe duringmaintenance?Chapter 4 / 35
It’s CONVENIENTEverything that needs a label, gets a label!When you have an easy-to-use printing tool ready and waitingright at your own facility, you can: C reate labels using built-in label templates for commonapplications, such as lockout/tagout, GHS, signs, pipemarkers, right to know and much more U tilize a wide offering of labeling materials to meet yourapplication needs P ace your labeling projects, instead of doing it all atonce in the case of ordering pre-made labels and signs C omplete projects quickly by sharing the responsibilityamongst multiple employeesDIYCOST EFFECTIVEEFFICIENTCONVENIENTChapter 4 / 36CUSTOMIZED
What if a label.Warned workers of a potential hazard inmultiple languages?Chapter 4 / 37
It’s CUSTOMIZEDThis isn’t a one-size-fits-all approach. We know it’s importantto be able to customize workplace visuals to align with yourunique safety, compliance and productivity goals. Withon-demand printing, you can decide what to make, how itshould look and how many you need.By creating your own signs, labels and tags, you can ensureyou have: M ultiple languages to ensure warnings are understoodby everyone. O perating instructions at the point of need to get newemployees up to speed and ready to master criticaltasks. As the experienced workforce ages and retires,effective instructions ensure that training is thoroughand efficient for new employees. C onsistent messaging to enforce safety and maketasks easier to understand with at-a-glance, identifiedsignage. The plant also looks more professional, soemployees can take pride in their workplace and makea positive impact on visitors.DIYCOST EFFECTIVEEFFICIENTCONVENIENTChapter 4 / 38CUSTOMIZED
Now that you know why your workplace needs5S Plus Safety, let’s get to work.YOUR SIGN AND LABEL SOLUTIONBrady has the innovative products, reliable labelmaterials and dedicated experts to bring you the facilityidentification you need to stay lean, compliant and safe.Our printers offer reliable, on-demand labeling and a rangeof durable materials to meet your industrial printing andlabeling needs.To learn more, visit BradyID.com
Are you interested in chatting witha professional about visual workplaceand 5S Plus? Call 888-311-0775 today!Kilpatrick, J. (2003). Lean Principles. Utah Manufacturing Extension Partnership.1 Moltz, D. (2011). Completion Agenda for Baby Boomers. Association for theStudy of Higher Education.2 Laird, D. (1985). Approaches to training and development . Addison-Wesley.3 Kilpatrick, J. (2003). Lean Principles. Utah Manufacturing Extension Partnership.4 Cable, J. (2014). NSC 2014: Fall Protection, Hazard Communication Repeat asOSHA’s Most Frequently Cited Standards. EHS Today.5
Meet 5S Plus Safety While 5S is one of the most widely adopted techniques from the lean manufacturing toolbox, “5S Plus” goes a step further to emphasize a critical aspect of any workplace: Safety. That way you benefit from a workplace that is both efficient and safe. Now, let’s expla