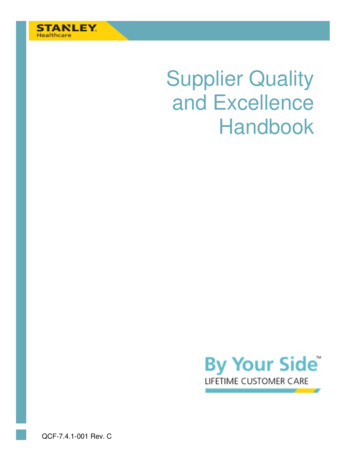
Transcription
Supplier Qualityand ExcellenceHandbookQCF-7.4.1-001 Rev. C
Table of Contents1.0 Introduction . 24.0 Quality Assurance . 51.1 About STANLEY Healthcare4.1 Qualification and Requalification1.2 STANLEY Healthcare ProductOfferings4.2 Quality Assurance Methodologies1.3 Purpose and Scope4.4 Escapes1.4 Non-Disclosure Agreement4.5 Supplier Corrective Actions4.3 First Articles2.0 Sustainability and EnvironmentalResponsibility. 32.1 Regulatory Compliance2.2 RoHS Compliance, REACH, WEEE,Conflict Minerals5.0 Supplier Performance . 65.1 On-Time Delivery5.2 PPM/Cost of Poor Quality5.3 Scorecards5.4 Annual Surveys2.3 Regulated SubstancesAppendix A: Resource Links . 72.4 Business Continuity3.0 Business Management System . 43.1 Quality Management SystemAppendix B: Supplier Corrective ActionProcess . 8Appendix C: Supplier PerformanceScorecard Overview . 93.2 Change Management3.3 Audit and Assessment3.4 Sub-Supplier Control and Flow DownQCF-7.4.1-001 Rev. C 2018STANLEY Healthcare1
1.0 Introduction1.1 About STANLEY HealthcareSTANLEY Healthcare is a recognized leaderin visibility and analytics solutions thattransform safety, security and operationalefficiency for senior living organizations,hospitals and health systems.STANLEY Healthcare is an operating divisionof STANLEY Black & Decker, a Fortune 500company with a track record of innovation andsustained profitable growths.1.2 STANLEY Healthcare ProductOfferingsSTANLEY Healthcare product offerings arefocused in five critical areas: 1) Security andProtection, 2) Patient and Resident Safety, 3)Clinical Operations and Workflow, 4)Environmental Monitoring, and 5) AssetManagement.STANLEY Healthcare has product offeringsthat are both FDA Medical Device listed, andnon-FDA listed. FDA listed product linesrequire compliance to FDA regulatoryrequirements codified in 21 CFR Part 820 orembodied in ISO 13485/ISO 9001. As suchSTANLEY Healthcare practices cGMP/ISO13485/ISO 9001 and has quality systemcertifications for these standards.1.3 Purpose and ScopeThe purpose of this Supplier Handbook is tocommunicate STANLEY Healthcare’s qualityrequirements and expectations to all new andQCF-7.4.1-001 Rev. C 2018existing suppliers. This document wasdeveloped as a baseline for qualifying newsuppliers and supporting our existingsuppliers in understanding and upholdingSTANLEY Healthcare’s requirements andexpectations.The requirements and expectations includedin this document apply to each stage relatedto the development, manufacture, delivery,and support of all products or servicesprovided to STANLEY Healthcare. ThisHandbook serves as a supplement and doesnot take precedence, nor serves as areplacement for pre-established agreements,engineering specifications, or STANLEYHealthcare purchase orders.We recognize that STANLEY Healthcare hasa wide-range of suppliers with varyingtechnologies and capabilities; theexpectations stated in this manual may applyin different ways, depending on the Product orService supplied.1.4 Non-Disclosure AgreementSTANLEY Healthcare may ask a Supplier tosign a Non-Disclosure Agreement in certaincases where proprietary information is sharedthroughout the course of business with aSupplier. STANLEY Healthcare utilizes astandard Mutual Confidentiality Agreementform for this purpose.STANLEY Healthcare2
2.0 Sustainability and Environmental Responsibility2.1 Regulatory ComplianceSuppliers must fully understand and complywith all country and local environmentalregulations for the areas in which they operate.In addition to STANLEY Healthcare employees, weexpect all of STANLEY Healthcare partners,distributors, resellers, advisors, consultants,contractors, agents and other intermediariesrepresenting STANLEY Healthcare to adhere to thedictates contained in our Code of Business Ethicsand Human Rights Policy Statement.More information on Corporate Social responsibilityis available on STANLEY Black and Deckerwebsite (See Appendix A: Resource Links).Suppliers should be aware of how theirbusinesses and Products impact theenvironment and the safety/health ofemployees.Suppliers should commit to continuousenvironmental, safety and healthimprovement, including the lowering of thesupplier’s carbon footprint.Notify STANLEY Healthcare of any significantenvironmental compliance violations.Provide composition information onparts/components as requested wherenecessary.Materials of Special Interest to STANLEYHealthcare2.2 RoHS Compliance, REACH,WEEE, Conflict MineralsRestricted Materials for STANLEY Healthcaregenerally include:Suppliers are expected to state RoHS, REACH,WEEE, and/or Conflict Mineral compliance onthe Declaration of Compliance with eachpurchase order. Restricted substances for suppliers must bedeclared per ES100118 EngineeringSpecification & Form for Restricted SubstanceDeclaration (See Appendix A: Resource Links). Restricted materials will be defined in productrequirements per project scope with thesupplier.2.3 Regulated SubstancesSuppliers must fully understand currentlegislation on global material restriction.2.4 Business ContinuitySuppliers are expected to have adequatesystems in place designed to identify anddisclose to STANLEY Healthcare all materialcontent of an approved part, sub-component,sourced product, accessory, and packaging toensure that the requirements of the STANLEYBlack and Decker Controlled SubstancesStandard specifications are fully met.QCF-7.4.1-001 Rev. C 2018Latex.DEHP, including: Bis (2- ethylhexyl)phthalate (DEHP); Butyl benzyl phthalate(BBP); Dibutyl phthalate (DBP); DiisobutylPhthalate (DIBP).Nickel (Exceptions include populated circuitboards with Electroless nickel ImmersionGold (ENIG) surface finishes).Continuous supply of product is critical even inan emergency. To ensure consistent delivery,suppliers are expected to submit a formal copyof their contingency plan. STANLEYHealthcare will work with supplier to identifyany areas of risk and develop alternate plans.STANLEY Healthcare3
3.0 Business Management System3.1 Quality Management System3.3 Audit and AssessmentSuppliers to STANLEY Healthcare must havean established and documented Quality Systemthat includes all appropriate elements of aquality system best suited for the supplier’sbusiness management system.To ensure compliance to STANLEYHealthcare’s Quality Requirements, suppliersmust allow STANLEY Healthcare Personneland Regulatory Authorities to audit and haveaccess to the supplier or sub-tier supplier’sprocesses, quality systems, and facilities.The management system shall be designed toensure: (a) compliance with Supplier StandardOperating Procedures and customerrequirements related to the supplier’soperations, products and services; (b)conformance with an International standard oforganization quality systems (i.e. ISO 9001 orISO 13485) or cGMP; (c) identification andmitigation of risks related to products orservices provided to STANLEY Healthcare; (d)the facilitation of corrective/preventive actionand continuous improvement.When a supplier is part of a STANLEYHealthcare FDA medical device listed productsupply chain, Quality System certifications maybe necessary to ensure compliance to 21 CFRPart 820 as embodied in ISO 13485/ISO 9001.For STANLEY Healthcare’s medical devicemanufacturers, unannounced audits may beperformed by Notified Bodies. Notified Bodies(NB), which ensure the safety of medicaldevices sold in the European Union (EU)Member States, conduct unannounced audits ofmedical device manufacturers. Unannouncedaudits by a Notified Body (NB) may also beperformed at STANLEY Healthcare’s criticalcontract manufacturers or crucial suppliersinvolved with producing STANLEY Healthcareproducts sold in the EU.3.4 Sub-Supplier Control and FlowDown3.2 Change ManagementSuppliers are required to notify STANLEYHealthcare of changes made to materials,products, or processes. This should includefacility changes and/or changes associated withsub-tier suppliers.Suppliers must notify STANLEY Healthcareprior to implementing such changes bysubmitting a STANLEY Healthcare ChangeManagement Form (See Appendix B). It isSTANLEY Healthcare’s responsibility todetermine whether the changes could affect thequality of a finished device.QCF-7.4.1-001 Rev. C 2018Suppliers are expected to provide a promptresponse for all audit findings.STANLEY Healthcare suppliers must have adocumented supplier management system formanaging their suppliers. The suppliermanagement system should includeappropriate QMS requirements, qualityassurance practices, and quality controlmethodologies.STANLEY Healthcare suppliers may berequired to flow down quality requirements totheir sub-tier suppliers. Suppliers are expectedto monitor and measure compliance from subtier suppliers.STANLEY Healthcare4
4.0 Quality Assurance4.1 Qualification and Requalification4.3 First ArticlesAll new suppliers for STANLEY Healthcare arerequired to complete STANLEY Healthcare’ssupplier qualification process. SupplierQualification process may include: ProcurementAgreements, Supplier Self-Assessments,Audits, and potential Statement of WorkAgreements.Suppliers are required to provide STANLEYHealthcare First Articles submissions for newproduct qualification and any changes madeduring the product lifecycle.Existing suppliers for STANLEY Healthcare maybe required to complete the STANLEYHealthcare requalification process whichincludes the review of various agreements,supplier performance, and continuousimprovement. On-site audits may be conductedduring requalification.4.2 Quality Assurance MethodologiesSTANLEY Healthcare expectations for qualityassurance includes utilization of measurementsystems and analysis (MSA), process capabilitystudies (CP, CPK, PP, PPK), control plans,pFMEAs, and cost of poor quality (COPQ).Supplier Quality Control procedures mustensure personnel are trained and competent toperform defined inspection and test methods.QCF-7.4.1-001 Rev. C 2018First Articles inspections are used todemonstrate that all STANLEY Healthcaredesign and specification requirements are fullyunderstood by the supplier and that the processis capable of producing products that meetthese requirements during an actual productionrun.4.4 EscapesSuppliers are required to immediately notifySTANLEY Healthcare in the event whereproducts have been released by the supplier orsub-supplier and are subsequently determinedto be nonconforming.4.5 Supplier Corrective ActionsSuppliers are expected to fully cooperate withSTANLEY Healthcare’s investigation andcontainment actions per STANLEYHealthcare’s Supplier Corrective ActionProcedure (Appendix C).STANLEY Healthcare5
5.0 Supplier Performance5.1 On-Time DeliverySuppliers are expected to deliver all ordersto STANLEY Healthcare on the requireddate agreed upon with each purchase order.STANLEY Healthcare utilizes a working daycalendar where exclusions are made forholidays and weekends associated with thecountry of purchase order origin. Typically,deliveries are considered on-time when theyare delivered within a four-day window ofthe required date of the purchase order. Thefour-day window includes shipmentsdelivered two days before, one day after,and including the required date of thepurchase order.5.2 PPM/Cost of Poor QualitySTANLEY Healthcare will notify suppliers ofnonconforming product in the event asupplier nonconformance report is raised.Suppliers are expected to provideimmediate support to prevent disruption ofSTANLEY Healthcare production.Disposition of nonconforming product mayinclude returning the nonconformingmaterial for a replacement, repair, or acredit. However, suppliers are expected tocover freight costs related to the dispositiondecision. STANLEY Healthcare may bewilling to dispose of nonconforming productlocally upon supplier authorization.5.3 ScorecardsSTANLEY Healthcare’s Supplier PerformanceScorecard will measure supplier performanceon a periodic basis. Supplier performance datawill be collected and used for periodic supplierbusiness reviews and decision making in thecontinuation, extension, or termination ofsupply.5.4 Annual SurveysSTANLEY Healthcare conducts internalSupplier Surveys on an annual basis with thepurpose of capturing internal employee’sopinion of their interactions with our suppliersthroughout the year. The surveys measuresupport aspects such as, Communication &Responsiveness, Customer Support,Reliability, and Supply Chain Support.Please Note: Acceptance of a STANLEY Healthcare purchase order (PO) constitutesacknowledgment that the Supplier has read and understands the expectations of this Manual.QCF-7.4.1-001 Rev. C 2018STANLEY Healthcare6
Appendix A: Resource LinksAbout STANLEY HealthcareFor more information regarding STANLEY Healthcare and its Solutions, Services, Partners,Technology, Company Information. Please visit the website at: www.stanleyhealthcare.com.Stanley Black and DeckerStanley Black & Decker is committed to setting strategic targets and adhering to policies andarrangements that support human rights, equality and environmental sustainability.Stanley Black and Decker Resources and Policies are located bility/resources-policiesStanley Black and Decker Quick Links for Suppliers:Corporate Social ResponsibilityRestricted Substances-ES100118Code of Business EthicsTerms and ConditionsHuman Rights Policy StatementSTANLEY Healthcare Supplier ManagementSTANLEY Healthcare forms for suppliers are available on Stanley Black and Decker’s GlobalSupplier Portal website: https://gsp.sbdinc.com. No log in required, simply click on the “PublicTab” in the center, select “Department Information” and then “Healthcare” from the drop-downmenu. An array of options will appear to the right.STANLEY Healthcare Quick Links:Supplier Quality and Excellence HandbookSupplier First Article Inspection-GeneralSupplier Self-Assessment FormSupplier First Article Inspection -PCBSupplier Change Request FormSupplier Annual Self-AssessmentSupplier Performance ScorecardQCF-7.4.1-001 Rev. C 2018STANLEY Healthcare7
Appendix B: Supplier Corrective Action ProcessSupplier Corrective Action OverviewWhen deemed appropriate, STANLEY Healthcare will issue a Supplier Corrective ActionRequest (SCAR) form. Suppliers may use STANLEY Healthcare provided SCAR form or theirown 8D CAPA form.Please note STANLEY Healthcare’s definitions of stages, activity per stage, and anticipated timelineper activity are listed below.STANLEY Healthcare recognizes that the timeline will vary per situation, so please keep yourSTANLEY Healthcare Representative updated.Should additional time be required to investigate the root cause or suitable corrective actions, arequest for extension may be made. Failure to provide this information could result indisqualification as a supplier source.Parts deemed unacceptable for use will be returned to the Supplier for evaluation unless theSupplier provides other disposition instructions.QCF-7.4.1-001 Rev. C 2018STANLEY Healthcare8
Appendix C: Supplier Performance Scorecard OverviewSupplier Performance ScorecardPurpose: STANLEY Healthcare Supplier Performance Scorecard will measure supplierperformance on a quarterly basis. Supplier performance data will be collected and used forperiodic supplier business reviews and decision making in the following areas: Continuation of supply Extension of supply (additional business) Termination of supplyScope: The scope of the scorecard includes purchased materials, primarily focused on directmaterials. One scorecard per supplier will be generated* encompassing all parts procured on aquarterly basis.*STANLEY Healthcare reviews supplier performance and determines which supplier will receive ascorecard on an annual basis. Selection is dependent on regulatory requirements of product procured,previous supplier performance, current level of spend with supplier and criticality of purchased productwithin STANLEY product or system designsQuality - Includes Three Parts:1. Defective Parts Per Million (DPPM)2. Count of Supplier Corrective Action Requests (SCARs) initiated during the currentscorecard period.3. Count of Supplier Nonconformance Reports (SNCRs) initiated during the currentscorecard period.On Time Delivery - Includes One Part:1. Percentage of on-time deliveries per purchase order line within scorecard period.QCF-7.4.1-001 Rev. C 2018STANLEY Healthcare9
embodied in ISO 13485/ISO 9001. As such STANLEY Healthcare practices cGMP/ISO 13485/ISO 9001 and has quality system certifications for these standards. 1.3 Purpose and Scope The purpose of this Supplier Handbook is to communicate STANLEY Healthcare’s quality requirements and expectat