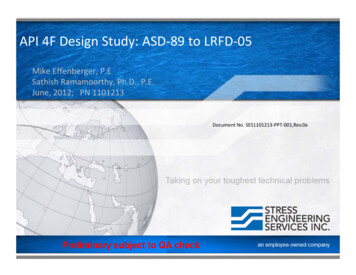
Transcription
API 4F Design Study: ASD‐89 to LRFD‐05Mike Effenberger, P.ESathish Ramamoorthy, Ph.D., P.E.June, 2012; PN 1101213Document No. SES1101213‐PPT‐001,Rev.0aPreliminary subject to QA check
Contents API 4F WorkBackgroundObjectivesDesign Study‐MethodologyModel DetailsAISC‐05 Analysis SpecificationsRig 1 Design Study Results Detailed Design Results Rig 3 Design Study Results Detailed Design Results2
API 4F 3API Funded Study – Check Effect of Load Factors for Drilling StructuresPaper – Code Conversion Issues Going From ASD to LRFD – Draft Provided– Comments Due June 24First Study Meeting – 2‐22‐2012 API 4F Work Group– Mark Trevithick (T&T Engineering) – Chair– Anthony Mannering (Precision Drilling)– Marcus McCoo (NOV)– Paul Landis (Lee C Moore) First Load Factors – ASCE7 Models Received (last): 03/05/2012 Finish Work Date: 11/05/2012
API 4F Design Study‐Status6‐13‐2012 Paper – Issued as Draft (Close 6-24-2012) Issue to API End of JuneRig 1 Boot-Strap Mast – Complete (Pending Review) ASD-89 (StruCAD & SAP) ASD-05 – 1st Order & ASD-05- P-Delta LRFD-05Rig 3 Derrick ASD-89 & LRFD-05Rig 2 Mast & Substructure In progress – Duplicate Plate Element Issues (Removed)Rig 4 Dual Derrick – Duplicate Element Issue (Merging Elements)Rig 5 Workover – Staad Model – Transfer Issues (Working withDesigner) 4
Background API 4F, Specification for Drilling and Well Servicing Structures API 4F committee is interested in going from the AllowableStress Design to the latest strength design Allowable StrengthDesign (ASD)/Load and Resistance Factor Design (LRFD)provision in AISC 360‐05 specification. Latest AISC specification is AISC 360‐10. The 2010 editionsupersedes and is an update of the 2005 edition. The 2010edition is yet to be supported by Computer Programs.5 states requirements and gives recommendations for suitable steelstructures for drilling and well‐servicing operations API 4F specifies the steel structures to be designed in accordance withAllowable Stress Design/Elastic design per AISC 335‐89
Background In the LRFD design methodology, design results areaffected by the load factors selected for the individualloads (self weight, hook load, and environmental loads) For building design, load factors and load combinations arespecified in ASCE 7, Minimum Design Loads for Buildings andOther Structures The load factors are generally estimated using thestatistical data for the individual loads and reliabilityconcepts Statistical data for Hook load is not readily available. Therefore,the load factors given in ASCE 7‐05 will be used for the designstudy (first case evaluation)6
Objectives Paper documenting the experience of other codes/specification while changing from ASD to LRFDmethodologyPerform design study on six structures (workover,mast, derrick & substructure) designed using the ASDand LRFD design provisions.Hook load will be considered as live load with a loadfactor of 1.6 (ASCE 7, First Case Evaluation) Decided by the API 4F work group on 02/22/20127
Methodology Design performed using the Allowable Stress 8Design/Elastic Design provisions in AISC 335‐89 willbe the base case.The structures will be evaluated according to AISC335‐89 ASD and LRFD design provisions per AISC360‐05 specificationThe design results between the Elastic design andStrength Design will be compared for evaluation
Derrick and Mast Models Provided toSES for Design StudyElevationNo of Setfrom WaterLines Back HeightLineOperating Unexpected Expected(kip) (ft)(ft)Reference Wind Speed(knots)ModelNameTypeHookLoad(kip)Rig 1Mast44110xxx92427093102.5Rig 2Mast &Substructure750125001603271.795.6Land RigRig 3Single Derrick150014xxx1955010011570Dual Derrick25001500(Aux)24265.1xxx10083.7104256075Rig 4Rig 5** Workover Mast2501614 1750(Aux)6xxxNotes:Analytical models for Rig1 to Rig 4 were developed in StruCADFor Rig 5, Analytical model was developed in STAAD9Land Rig
Rig 1441 kip Hook Load Mast10
Rig 2750 kip Hook Load Mast & SubstructureZX11Y
Rig 31500 kip Hook Load Single DerrickZX12Y
Rig 42500 kip Hook Load Dual Derrick13
Rig 5250 kip Hook Load Workover Mast14
Software Details SAP2000 Ultimate 15.1.0 from Computers and Structures, Inc (CSI) was used for the design study.SAP is a integrated software for structural analysisand design P‐Δ with large displacements Buckling analysis Design �10 (Later in 2012)
StruCAD to SAP2000 Conversion StruCAD models were imported in SAP. The imported 16models were compared with the StruCAD models.In general, most of the model features are importedwithout any issues. However, there are few StruCADcommands/features that are not imported in SAP.These are manually edited in the imported model.SAP technical support and development team werenotified about the import issues.
StruCAD to SAP 2000 ConversionOutstanding issues Effective Length Factors not imported Effective length specified/used in the StruCAD model isentered as “Design Overwrites” in SAP model Wind Loads/Area Cards are not imported Wind loads are converted to Member and Joint Loads inStruCAD and imported in SAP Acceleration Loads Discrepancy in the base reactions for the accelerationloads in the StruCAD and SAP models. Therefore, theacceleration loads are converted to Member/joint loads inStruCAD and then imported in SAP17
StruCAD to SAP 2000 ConversionDesign issues Cm factor Difference in calculating the Cm factor between StruCADand SAP Brace Spacing StruCAD has option to input to the brace spacing forestimating the effective length. SAP does not have anequivalent parameter to modify18
Design Basis AISC‐1989 Specification Allowable Stress Design (ASD‐89) AISC‐2005 Specification Load and Resistance Factor Design (LRFD‐05)19
Design BasisAllowable Stress Design‐89 The imported models were run in SAP and comparedwith the StruCAD results In general, the member forces are comparable to theStruCAD member forces. For some members, there is asmall discrepancy in the minor and major axis moments. Allowable Stress Design (ASD‐89)– Static linear analysis– With 1/3rd increase in allowable stress for expected andunexpected load case20
Design Basis Allowable Strength Design‐05For Rig 1 OnlyAllowable Strength Design (ASD‐05)––––Effective length methodSecond order analysis method (includes p‐Δ and p‐δ)Without 1/3rd increase in allowable for wind load combinationsAPI 4F load combinationsCase1a1b23a3b*4521Design edUnexpectedErectionTransportationDead Load(%)100100100100100100100Hook Load Rotary 10001000Setback Load(%)1001000100‐0100Environmental Loads(%)100100100100‐100100Note: Load combination 3b is for Earthquake loads and was not includedin this study
Design BasisLoad and Resistance Factor Design ‐05 Load and Resistance Factor Design (LRFD‐05)––––Effective length methodGeneral second order analysis method (includes p‐Δ and p‐δ)Without 1/3rd increase in allowable for wind load combinationsHook load is considered as live load with 1.6 load factor similar toASCE 7‐05 live loadsCase1a1b23a3b45Design Loading Dead Load Hook Load Rotary Load Setback Load Environmental 0100Note: Other loads should be classified (for ex loads in Rig 3 Model22
Comparison of Analysis MethodsAISC‐05 SpecificationDirect AnalysisMethodEffective LengthMethodFirst‐Order AnalysisMethodSpecification ReferenceAppendix 7Section C.2.2aSection C.2.2bLimits on irst‐OrderReduced EI and EANominal EI and EANominal EI and EANotional lateral loadYesYesYesColumn effective lengthK 1Sidesway bucklinganalysisK 1Type of analysisMember stiffnessNote: In AISC‐10 specification, Direct Analysis is moved to Section C.Effective length and Firs‐Order Analysis Methods are moved to Appendix 723
Comparison of Analysis MethodsDirect AnalysisMethodEffective LengthMethodFirst‐Order AnalysisMethodSpecification ReferenceAppendix 7Section C.2.2aSection C.2.2bLimits on irst‐OrderReduced EI and EANominal EI and EANominal EI and EANotional lateral loadYesYesYesColumn effective lengthK 1Sidesway bucklinganalysisK 1Type of analysisMember stiffnessNot considered in this study24
Effective Length Method DetailsLinear Load combinationNo P‐DeltaAmplified First OrderK 1Force effects are amplified by B1and B2 factor to account for P‐Delta**Effective LengthMethodNon‐linear load combinationP‐deltaGeneral SecondOrderEffective length from StruCADmodel (side sway bucklinganalysis was not performed)Notional lateral load for gravityload combinations is notincluded** B1 and B2 factors account for the P‐δ and P‐Δ. For the current API 4Fstudy, to study the effect of changes in the specification for memberstrength, the B1 and B2 factor of 1.0 was used. Comparison of design resultsbetween the ASD‐05 (First order) and ASD‐89 will show the effect of changesin specifications.25
Rig 1 Design Study Results(Boot Strap Mast) Total number of Members 347 (excluding 16 dummy members) SAP classifies the members Beams (all elements parallel to the X‐Y plane)– 184 Brace (all elements not classified as beams or columns)– 85 Column (all elements parallel to the Z‐axis)– 7826
Rig 1441 kip Hook Load MastRig 127Rig 1Beams184Rig 1Braces85Rig 1Columns78
Rig 1‐ Design Study Results441 kip Hook Load MastMemberswith unityratio 1.0Type tress Design(ASD‐89)StruCADAllowableStress Design(ASD‐89)SAPAllowableStress 5)AmplifiedFirst OrderMethod**AllowableStrength Design(ASD‐05)Load andResistanceFactor Design(LRFD‐05)(ASCE erFirst‐OrderSecond‐Order(P‐Δ and P‐δ)Second‐Order(P‐Δ and P‐δ)YesYesNoNoNoNoNote: **The amplified first order method is modified (B1, B2 1) tocompare the difference in design results between ASD ‐89 and ASD‐05specifications
Rig 1 Design Study ResultsUnity Check StatisticsSAP Models‐ ASD‐89 and LRFD‐05No of members with UC 1Maximum UCAverage UCBeamBraceASD‐89 LRFD‐05 % change ASD‐89 LRFD‐05 % change12171.161.05‐9.14%1.092.28 109.15%0.490.549.16%0.390.4412.60%ColumnASD‐89 LRFD‐05 % change12171.191.3614.53%0.720.753.69%Notes1.SAP ASD‐89 results are with 1/3rd increase in Allowable Stress for Expected and UnexpectedStorm2.LRFD‐05 results are without 1/3rd increase. Load factor for Hook Load is 1.63.Even without the 1/3rd stress increase for LRFD‐05, there is no significant increase in number ofmembers exceeding the unity check ratio4.The significant change in UC for beam member from ASD‐89 to LRFD‐05 is due to the differencein the interaction equation for doubly symmetric members in LRFD specification5.Detailed results for the highest UC members for beam, brace and column are provided indetailed results section29
Rig 1‐ Design Study ResultsASD‐89 StruCAD and SAPASD‐89‐StruCAD Model13 members with UR lumnBraceBraceBeamBeamBeamBeam30Member No Load Comb Unity .109339181.005340220.851341200.941With 1/3rd Stress Increase forExpected and Unexpected StormASD‐89‐SAP model14 members with UR 1.StruCAD model Importinto SAP2000Design withAISC‐89 specificationwith1/3rd Stress IncreaseMember 79284285337339340341Load SCAD24SCAD24SCAD18SCAD24SCAD18SCAD21SCAD20With 1/3rd Stress Increase forExpected and Unexpected StormUnity 1.0890.9870.4560.482
Rig 1‐ Design Study ResultsASD‐89‐SAP Model14 members with UR mnColumnColumnBraceBraceBeamBeamBeamBeam31Member 278279284285337339340341Load AD20Unity 1.1640.9611.0890.9870.4560.482With 1/3rd Stress Increase forExpected and Unexpected StormASD‐89 SAPAISC‐89 specificationDesign resultswithout the1/3rd Stress IncreaseASD‐89‐SAP model17 members with UR 1.Member 278279284285337339340341Load AD20Unity 1.2311.3061.0890.9870.4560.482Without 1/3rd Stress Increase forExpected and Unexpected Storm
Rig 1‐ Design Study ResultsASD‐89 and ASD‐05 First OrderASD‐89‐SAP17 members with UR mnColumnColumnBraceBraceBeamBeamBeamBeam32Member 278279284285337339340341Load AD20Unity 1.2311.3061.0890.9870.4560.482Without 1/3rd Stress Increase forExpected and Unexpected StormASD‐05‐SAP Amplified First Order14 members with UR 1.Transition fromAISC‐89 specificationto AISC‐05 specificationMember 278279284285337339340341Load AD21Without 1/3rd Stress Increase forExpected and Unexpected StormUnity 0.9390.9081.2941.1731.9762.216
Rig 1‐ Design Study ResultsASD‐89 and ASD‐05 First OrderASD‐89‐SAP14 members with UR mnColumnColumnBraceBraceBeamBeamBeamBeam33Member No Load Comb Unity 82With 1/3rd Stress Increase forExpected and Unexpected StormASD‐05‐SAP Amplified First Order14 members with UR 1.Transition fromAISC‐89 specificationto AISC‐05 specificationMember No Load Comb Unity 16Without 1/3rd Stress Increase forExpected and Unexpected Storm
Rig 1‐ Design Study ResultsSAP Models: ASD‐89, ASD‐05 First order and ASD‐05ASD‐8917 members with UR umnColumnColumnBraceBraceBeamBeamBeamBeam34Member 278279284285337339340341Load AD20Unity 1.2311.3061.0890.9870.4560.482Without 1/3rd Stress Increase forExpected and Unexpected StormASD‐05‐Amplified First Order14 members with UR 1.0Member 278279284285337339340341Load AD21Unity 0.9390.9081.2941.1731.9762.216ASD‐0519 members with UR 1.0Member 278279284285337339340341Without 1/3rd Stress Increase for Expected andUnexpected StormLoad AD21Unity 0.9920.9611.3461.2222.0822.327
Rig 1‐ Design Study ResultsSAP Models: ASD‐89, ASD‐05 and eamBeamBeamBeamBeamBeamBeam35ASD‐8917 members with UR 1.0ASD‐0519 members with UR 1.0LRFD‐0526 members with UR 1.0Member 74276277278279284285337339340341342343344Member 74276277278279284285337339340341354355363Member 74276277278279284285337339340341354355363Load AD24SCAD18SCAD21SCAD20SCAD48SCAD42SCAD18Unity 0.3990.196Without 1/3rd Stress Increase forExpected and Unexpected StormLoad AD24SCAD18SCAD22SCAD21SCAD24SCAD24SCAD18Unity 0.9650.989Without 1/3rd Stress Increase for Expected andUnexpected StormLoad AD24SCAD42SCAD22SCAD21SCAD24SCAD24SCAD18Unity 1.0201.053
Rig 1‐ Design Study ResultsSAP Models: ASD‐89, ASD‐05 and LRFD‐05ASD‐8914 members with UR mBeamBeamBeamBeamBeam36Member 74276277278279284285337339340341354355363Load AD24SCAD18SCAD21SCAD20SCAD24SCAD24SCAD18Unity 0.9860.989With 1/3rd Stress Increase forExpected and Unexpected StormASD‐0519 members with UR 1.0LRFD‐0526 members with UR 1.0Member 74276277278279284285337339340341354355363Member 74276277278279284285337339340341354355363Load AD24SCAD18SCAD22SCAD21SCAD24SCAD24SCAD18Unity 0.9650.989Without 1/3rd Stress Increase for Expected andUnexpected StormLoad AD24SCAD42SCAD22SCAD21SCAD24SCAD24SCAD18Unity 1.0201.053
Rig 1Detailed Design Results for SelectedMembers37
Rig 1Detailed Design Results for Selected Members Beam Brace Column38
Rig 1Detailed Design Results MembersRig 1ColumnMember # 274Rig 1BraceMember # 28539Rig 1BeamsMember # 313
Rig 1Detailed Design Results for Selected Members Beam Brace Column40
Rig 1Beam Member 313‐Loads and Design 89 SCAD27ASD‐05** SCAD27ASD‐05 SCAD27LRFD‐05 ‐1.944‐3.290MrMajor MrMinor 3.301‐13.927‐22.41Equation TotalRatioTextUnitlessPRatio .0187* StruCAD results** First Order Results (no P‐Δ)ASD‐05 and LRFD‐05 results are without the 1/3rd increase in allowable stressMember 313Joint A: 172Joint B: 173Section: T8D41
Rig 1 ASD‐89‐StruCADBeam Member 313, U.C Ratio 0.33Member No. 313 172‐ 173GRUPT8DSection ‐ TS8X4X3/16Total Length‐7.5Load CaseDistanceSegmentDesign CodeAmodCmyCmzCbYield StrengthSkip Local Buckling ChecksBasic PropertiesSection TypeAxial AreaTors. ConstantMax. Unbraced LengthMax. Unbraced LengthSect. Modulus TopSect. Modulus BotSect. Modulus LftSect. Modulus RhtSlenderness ratioSlenderness ratioCol. Slenderness RatioInteraction CoefficientInteraction CoefficientBending cLuSytSybSzlSzrKl/ryKl/rzCcCmyCmzCbJoint ThicknessSlenderness coeff. KySlenderness coeff. KzEffective Length LyEffective Length LzBrace SpacingTub. Mod. / Stiff. 1.5540.3250.2362.3Forces & MomentsAxial ForceShear ForceShear ForceTorsional MomentBending MomentBending MomentFxFyFzMxMyMzGoverning EquationsCritical Buckling (API)Tension AllowableCompression AllowableBending Tension Allow.Bending Compression AllowBending Tension Allow.Bending Compression AllowShear AllowableShear AllowableCombined Unity ��0.03‐1.792‐13.58795.6184.244(SEC D1)(E 2‐1)(F 3‐3)(F 3‐3)(F 3‐3)(F 3‐3)(F 4‐1)(F 4‐1)(H1‐3)Actual StressesAxial StressBending Stress TopBending Stress BotBending Stress LftBending Stress RhtShear StressShear StressTors. Shear StressTors. Shear StressCombined Shear StressWarping Normal StressCombined 7‐1.216‐1.2161.8140‐11.9740Allowable StressesEuler StressEuler StressCritical Buckling (API)Tension AllowableCompression AllowableBending Tension Allow.Bending Compression AllowBending Tension Allow.Bending Compres. AllowShear AllowableShear 24.52724.527Unity RatiosAxial ComponentBending ComponentBending ComponentShear ComponentShear ComponentCombined Unity RatioCritical Unity 30.33
Rig 1 ASD‐89‐SAPBeam Member 313, U.C Ratio 0.33443
Rig 1 LRFD‐05 SAPBeam Member 313, U.C Ratio 0.39144
Rig 1Detailed Design Results for Selected Members Beam Brace Column45
Rig 1Brace Member 285‐Loads and Design D‐89*42ASD‐89 SCAD42ASD‐05** SCAD42ASD‐05 SCAD42LRFD‐05 1‐114.886‐114.886‐116.006‐175.461MrMajor MrMinor 0.00.00.00.0Equation TotalRatioTextUnitlessPRatio .1162* StruCAD results** First Order Results (no P‐Δ)ASD‐05 and LRFD‐05 results are without the 1/3rd increase in allowable stressMember 285Joint A: 3Joint B: 246Section: T8A46
Rig 1 ASD‐89‐StruCADBrace Member 285, U.C Ratio 0.719Member No. 285 3‐ 246GRUPT8ASection ‐ TS8X8X3/8Total Length‐31.545Load CaseDistanceSegmentDesign CodeAmodCmyCmzCbYield StrengthSkip Local BucklingChecksBasic PropertiesSection TypeAxial AreaTors. ConstantMax. Unbraced LengthMax. Unbraced LengthSect. Modulus TopSect. Modulus BotSect. Modulus LftSect. Modulus RhtSlenderness ratioSlenderness ratioCol. Slenderness RatioInteraction CoefficientInteraction CoefficientBending .526.5104.854104.854111.5540.60.61.75Joint ThicknessSlenderness coeff. KySlenderness coeff. KzEffective Length LyEffective Length LzBrace SpacingTub. Mod. / Stiff. Spacing111272731.54531.545Forces & MomentsAxial ForceShear ForceShear ForceTorsional MomentBending ending MomentMz51.65Governing EquationsCritical Buckling (API)Tension AllowableCompression AllowableBending Tension Allow.Bending Compression AllowBending Tension Allow.Bending Compression AllowShear AllowableShear AllowableCombined Unity RatioFxcrFatFacFbytFbycFbztFbzcFvayFvazUc(SEC D1)(E 2‐1)(F 3‐3)(F 3‐3)(F 3‐3)(F 3‐3)(F 4‐1)(F 4‐1)(H1‐1)Actual StressesAxial StressBending Stress TopBending Stress BotBending Stress LftBending Stress RhtShear StressShear StressTors. Shear StressTors. Shear StressCombined Shear StressWarping Normal StressCombined Allowable StressesEuler StressEuler StressCritical Buckling (API)Tension AllowableCompression AllowableBending Tension Allow.Bending Compression AllowBending Tension Allow.Bending Compres. AllowShear AllowableShear ��13.6950Unity 6.79124.52724.527Axial ComponentBending ComponentBending ComponentShear ComponentShear ComponentCombined Unity RatioCritical Unity RatioUaUbyUbzUsyUszUcUc0.60.0410.078000.7190.719
Rig 1 ASD‐89‐SAPBrace Member 285, U.C Ratio 0.71948
Rig 1 LRFD‐05‐SAPBrace Member 285, U.C Ratio 1.05849
Rig 1Detailed Design Results for Selected Members Beam Brace Column50
Rig 1Column Member 274‐Loads and Design 89 SCAD18ASD‐05** SCAD18ASD‐05 SCAD18LRFD‐05 89.107‐193.827‐308.857MrMajor MrMinor on TotalRatioTextUnitlessPRatio 0011* StruCAD results** First Order Results (no P‐Δ)ASD‐05 and LRFD‐05 results are without the 1/3rd increase in allowable stressMember 274Joint A: 124Joint B: 128Section: T6U51
Rig 1 ASD‐89‐StruCADColumn Member 274, U.C Ratio 1.016Member No. 274124‐ 128GRUPT6USection ‐ TS6X6X3/8Total Length‐7.443Joint Thickness0Slenderness coeff. Ky1Actual StressesAxial StressfaSlenderness coeff. Kz0.9Bending Stress TopfbytEffective Length Ly9.1Bending Stress Botfbyb1.389Effective Length Lz7Bending Stress Lftfbzl‐2.9582.958‐23.491‐1.389Load Case18Distance0Brace Spacing7.443Bending Stress RhtfbzrSegment1Tub. Mod. / Stiff. Spacing7.443Shear Stressfvy0.21Shear Stressfvz‐0.059Design CodeSA9Forces & MomentsAmod1Axial ForceFx‐189.804Tors. Shear Stressfvyt0.552Tors. Shear Stressfvzt0.5520.762CmyCShear ForceFy0.945Combined Shear StressfvCmzCShear ForceFz‐0.268Warping Normal StressFbztrCbBTorsional MomentMx13.102Combined Stressfcomb50Bending MomentMy19.262Bending MomentMz‐41.019Yield StrengthSkip Local Buckling Checks0‐27.8380Basic PropertiesSection TypeBOXAxial AreaGoverning Equations8.08Critical Buckling (API)Allowable StressesFxcrUnity RatiosEuler StressF'ey64.529134.635Tors. ConstantJ68.5Tension AllowableFat(SEC D1)Euler StressF'ezMax. Unbraced LengthLc9.75Compression AllowableFac(E 2‐1)Critical Buckling (API)Fxcr0Max. Unbraced LengthLu0Bending Tension Allow.Fbyt(F 3‐1)Tension AllowableFat30Sect. Modulus TopSyt13.867Bending Compression AllowFbyc(F 3‐1)Compression AllowableFac24.643Sect. Modulus BotSyb13.867Bending Tension Allow.Fbzt(F 3‐1)Bending Tension Allow.Fbyt33Axial ComponentUaBending Component Uby0.9530.036Sect. Modulus LftSzl13.867Bending Compression AllowFbzc(F 3‐1)Bending Compression Allow Fbyc33Bending Component Ubz0.026Sect. Modulus RhtSz
provision in AISC 360‐05 specification. Latest AISC specification is AISC 360‐10. The 2010 edition supersedes and is an update of the 2005 edition. The