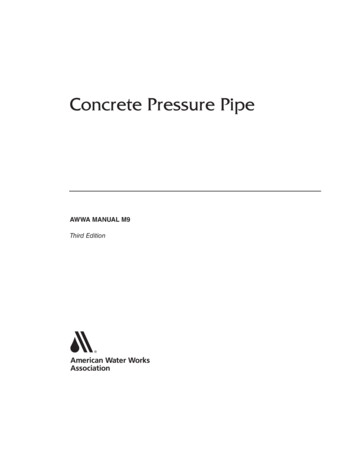
Transcription
Concrete Pressure PipeAWWA MANUAL M9Third Edition
MANUAL OF WATER SUPPLY PRACTICES — M9, Third EditionConcrete Pressure PipeCopyright 1979, 1995, 2008 American Water Works AssociationAll rights reserved. No part of this publication may be reproduced or transmitted in any form or by anymeans, electronic or mechanical, including photocopy, recording, or any information or retrieval system,except in the form of brief excerpts or quotations for review purposes, without the written permission of thepublisher.DisclaimerThe authors, contributors, editors, and publisher do not assume responsibility for the validity of the contentor any consequences of their use. In no event will AWWA be liable for direct, indirect, special, incidental, orconsequential damages arising out of the use of information presented in this book. In particular, AWWA willnot be responsible for any costs, including, but not limited to, those incurred as a result of lost revenue. In noevent shall AWWA’s liability exceed the amount paid for the purchase of this book.Project Manager and Technical Editor: Franklin S. KurtzProduction: Melanie SchiffManual Coordinator: Beth BehnerUnless otherwise noted, all photographs used in this manual are provided courtesy of the AmericanConcrete Pressure Pipe Association.Library of Congress Cataloging-in-Publication DataConcrete pressure pipe. -- 3rd ed.p. cm. -- (AWWA manual ; M9)Includes bibliographical references and index.ISBN 1-58321-549-21. Water-pipes. 2. Pipe, Concrete. 3. Pressure vessels. I. American Water Works Association.TD491.C66 2008628.1’5--dc222008010413Printed in the United States of AmericaAmerican Water Works Association6666 West Quincy AvenueDenver, CO 80235ISBN 1-58321-549-2978-1-58321-549-4
ContentsList of Figures, viiList of Tables, xiAcknowledgments, xiiiChapter 1Purpose and Scope . . . . . . . . . . . . . . . . . . . . . . . . . . . . . . . . . . . . . . . . . . . . . . . 1Chapter 2Description of Concrete Pressure Pipe. . . . . . . . . . . . . . . . . . . . . . . . . . . . . . . 3Prestressed Concrete Cylinder Pipe (ANSI/AWWA C301-Type Pipe), 3Reinforced Concrete Cylinder Pipe (ANSI/AWWA C300-Type Pipe), 7Reinforced Concrete Noncylinder Pipe (ANSI/AWWA C302-Type Pipe), 8Concrete Bar-Wrapped Cylinder Pipe (ANSI/AWWA C303-Type Pipe) , 10Fittings and Special Pipe, 11Reference, 12Chapter 3Hydraulics . . . . . . . . . . . . . . . . . . . . . . . . . . . . . . . . . . . . . . . . . . . . . . . . . . . . . 13Flow Formulas, 13Effects of Aging on Carrying Capacity, 20Head Losses, 20Determining an Economical Pipe Diameter, 21Air Entrapment and Release, 25Blowoff Outlets, 25References, 25Chapter 4Surge Pressure. . . . . . . . . . . . . . . . . . . . . . . . . . . . . . . . . . . . . . . . . . . . . . . . . . 27Equations and Variables, 27Negative Pressures, 30Causes of Surge Pressure, 30Control of Water Hammer, 31References, 32Chapter 5External Loads. . . . . . . . . . . . . . . . . . . . . . . . . . . . . . . . . . . . . . . . . . . . . . . . . 33Major Installation Classifications, 33Trench Conduits, 33Embankment Conduits , 37Positive Projection Installations, 37Earth Loads on Large Diameter ANSI/AWWA C303 Pipe, 41iii
Negative Projection Installations, 42Induced Trench Installations, 44Jacked or Tunneled Conduits, 47Determination of Live Load, 48References, 56Chapter 6Bedding and Backfilling . . . . . . . . . . . . . . . . . . . . . . . . . . . . . . . . . . . . . . . . . . 57Introduction, 57Rigid Pipe, 57Semirigid Pipe, 59Unstable Foundations, 60References, 61Chapter 7Design of Reinforced Concrete Pressure Pipe . . . . . . . . . . . . . . . . . . . . . . . . 63Information Required for Pipe Design, 63Design Procedure for Rigid Pipe (ANSI/AWWA C300- and C302-Type Pipe), 64Design Procedure for Semirigid Pipe (ANSI/AWWA C303-Type Pipe), 86References, 93Chapter 8Design of Fittings and Appurtenances. . . . . . . . . . . . . . . . . . . . . . . . . . . . . . . 95Fit tings, 95Fit tings Design, 98Specials, 117References, 119Chapter 9Design of Thrust Restraints for Buried Pipe. . . . . . . . . . . . . . . . . . . . . . . . . 121Thrust Forces, 121Hydrostatic Thrust, 121Thrust Resistance, 123Thrust Blocks, 124Joints With Small Deflections, 126Tied Joints, 132Design Examples, 141Combination Thrust-Restraint System, 167Other Uses for Restraints, 170References, 171Chapter 10Design of Pipe on Piers. . . . . . . . . . . . . . . . . . . . . . . . . . . . . . . . . . . . . . . . . 173Loads, 173iv
Cylinder Pipe, 173Location of Piers, 177Design of Pipe and Supports at Piers, 179Protection of Exposed Concrete Pipelines, 183References, 185Chapter 11Design of Subaqueous Installations. . . . . . . . . . . . . . . . . . . . . . . . . . . . . . . 187Application, 187Pipe Design Features, 187Subaqueous Pipe Details, 190Installation, 191Testing, 194Chapter 12Design Considerations for Corrosive Environments . . . . . . . . . . . . . . . . . 195History, 195Inherent Protective Properties, 195Special Environmental Conditions, 196Bonding Pipelines, 199Monitoring for Pipe Corrosion, 205Cathodic Protection, 213References, 214Chapter 13Transportation of Pipe . . . . . . . . . . . . . . . . . . . . . . . . . . . . . . . . . . . . . . . . . 215Truck Transportation, 215Rail Transportation, 215Barge Transportation, 218Loading Procedures, 218Delivery and Unloading, 218Chapter 14Installation by Trenching or Tunneling — Methods and Equipment. . . . . 221Trenching — General Considerations, 221Open Trench Construction, 223Bedding, 226Pipe Installation — General, 227Laying the Pipe, 228Backfilling, 230Tunnel Installations, 232Jacking Methods, 233v
Mining Methods, 235Grouting, 235References, 238Chapter 15Hydrostatic Testing and Disinfection of Mains. . . . . . . . . . . . . . . . . . . . . . 239Hydrostatic Testing, 239Disinfection of Mains, 241Reference, 242Chapter 16Tapping Concrete Pressure Pipe . . . . . . . . . . . . . . . . . . . . . . . . . . . . . . . . . 243Threaded Pressure Taps Up to 2 In. (51 mm) in Diameter, 243Pressure Taps for Flanged Outlets 3 In. (76 mm) and Larger, 245Tapping Noncylinder Reinforced Concrete Pressure Pipe, 248Supplemental Data, 248Chapter 17 Guide Specif ications for the Purchase and Installation ofConcrete Pressure Pipe. . . . . . . . . . . . . . . . . . . . . . . . . . . . . . . . . . . . . . . . . . . . . . . . . . . . 251Guide Specifications for Purchasing Concrete Pressure Pipe, 252Guide Specifications for the Installation of Concrete Pressure Pipe, 254Index. . . . . . . . . . . . . . . . . . . . . . . . . . . . . . . . . . . . . . . . . . . . . . . . . . . . . . . . . . . . . . . . . . . 261List of AWWA Manuals . . . . . . . . . . . . . . . . . . . . . . . . . . . . . . . . . . . . . . . . . . . . . . . . . . . . 269vi
FiguresFigure 1-1A typical installation in rugged terrain, 1Figure 2-1Prestressed concrete cylinder pipe (ANSI/AWWA C301-type pipe), 5Figure 2-2Fabrication of a steel cylinder on a “helical” machine, 6Figure 2-3Prestressing concrete embedded cylinder pipe, 6Figure 2-4Welding joint rings to cylinder, 7Figure 2-5Reinforced concrete cylinder pipe (ANSI/AWWA C300-type pipe), 8Figure 2-6Reinforced concrete noncylinder pipe (ANSI/AWWA C302-type pipe), 9Figure 2-7Concrete bar-wrapped cylinder pipe (ANSI/AWWA C303-type pipe), 11Figure 2-8Steel cylinder being hydrostatically tested on a mandrel-type tester, 11Figure 2-9Installation of a large-diameter wye with reducer attached, 12Figure 3-1Hydraulic profile for a gravity flow system, 15Figure 3-2Hydraulic profile for a pumped flow system, 15Figure 3-3The Moody diagram for friction in pipe, 18Figure 3-4Approximate loss coefficients for commonly encountered flow configurations, 22Figure 4-1Idealized surge cycle for instantaneous pump shutdown, 28Figure 5-1Underground conduit installation classifications, 34Figure 5-2Essential features of types of installations, 35Figure 5-3Settlements that influence loads—positive projecting embankment installation, 38Figure 5-4Settlements that influence loads—negative projecting embankment installation, 38Figure 5-5Settlements that influence loads — induced trench installation, 39Figure 5-6Load coefficient for positive projection embankment condition, 43Figure 5-7Load coefficient for negative projection and induced trench condition ( p′ 0.5), 45Figure 5-8Load coefficient for negative projection and induced trench condition ( p′ 1.0), 45Figure 5-9Load coefficient for negative projection and induced trench condition (p′ 1.5), 46Figure 5-10Load coefficient for negative projection and induced trench condition ( p′ 2.0), 46Figure 5-11Live load distribution, 50Figure 5-12Live load spacing, 50Figure 5-13Wheel load surface contact area, 51Figure 5-14Distributed load area—single dual wheel, 52Figure 5-15Effective supporting length of pipe, 53Figure 5-16Cooper E80 design load, 56Figure 6-1Bedding and backfill for rigid pipe, 58Figure 6-2Bedding and backfill for semirigid pipe, 60Figure 7-1Olander moment, thrust, and shear coefficients for 90 bedding angle, 72Figure 7-2Force diagrams for reinforced concrete pipe design, 73Figure 7-3Section for proportioning tensile steel, 74Figure 7-4Section through AWWA C303-type pipe wall, 92vii
Figure 8-1Common fittings, 96Figure 8-2A 90-in. (2,290-mm) bend ready to install, 97Figure 8-3A reducer or increaser makes a gradual change in ID of the line, 97Figure 8-4A tee or cross is used for 90 lateral connections, 98Figure 8-5Bifurcations for splitting flow, 99Figure 8-6Various types of reinforcing, 100Figure 8-7Adapters used to connect pipe to valves, couplings, or pipe of a different material, 101Figure 8-8Typical end configurations, 102Figure 8-9aTypical four-piece bend, 105Figure 8-9bFree body diagram of one-fourth of a miter segment and fluid, 105Figure 8-9cSchematic of Atrap, 105Figure 8-10Replacement of steel at openings in fabricated fittings requiring collar or wrapped type ofreinforcement, 109Figure 8-11Assumed hydrostatic load distribution for an equal-diameter wye with two-crotch-platereinforcement, 110Figure 8-12Nomograph for selecting reinforcement plate depths of equal-diameter pipes, 111Figure 8-13N -factor curves for branch deflection angles less than 90 , 112Figure 8-14Q -factor curves for branch diameter smaller than run diameter, 112Figure 8-15Selection of top depth, 113Figure 8-16Wye-branch reinforcement plan and layout, 115Figure 8-17Three-plate wye-branch reinforcement plan and layout, 117Figure 8-18Typical outlets built in to pipe, 118Figure 9-1Thrusts and movement in pipeline, 122Figure 9-2Hydrostatic thrust T applied by fluid pressure to typical fittings, 122Figure 9-3Typical thrust blocking of a horizontal bend, 125Figure 9-4Typical profile of vertical-bend thrust blocking, 126Figure 9-5Tee and reducer on large-diameter line. Note sandbags behind tee as forms for placementof thrust block, 127Figure 9-6Locking of pipe at small deflections, 128Figure 9-7Four sections of unrestrained 36-in. (910-mm) prestressed concrete pipe span an 80-ft(24-m) wide washout in Evansville, Ind., 128Figure 9-8aRestraint of thrust at deflected, nontied joints on long-radius horizontal curves, 129Figure 9-8bHorizontal bearing factor for sand vs. depth-to-diameter ratio (H/D0)(adapted fromO'Rourke and Liu [1999]), 129Figure 9-9aRestraint of uplift thrust at nontied, deflected joints on long-radius vertical curves, 131Figure 9-9bEarth load for restrained joint calculations, 131Figure 9-10Free body diagram of forces and deformations at a bend, 133Figure 9-11Schematic strain and stress distributions at cylinder yield design criterion ( f y steelcylinder yield strain, fy steel cylinder yield stress, fs steel cylinder stress,fc concrete stress), 139Figure 9-12Schematic strain and stress distributions at ultimate strength limit state ( f y steelcylinder yield strain, fy steel cylinder yield stress, fs steel cylinder stress, fc concreteviii
stress, f c concrete stress), 139Figure 9-13Interaction diagram for example 2. The axial force-moment interaction diagramscorrresponding to the ultimate strength and the onset of yielding of the steel cylinder areboth nonlinear, but have been approximated by a linear relationship here for ease ofcomputation of the examples, 150Figure 9-14Infinite beam on elastic foundation with applied forces and moments at the ends of abeam segment, 154Figure 9-15Infinite beam on elastic foundation with applied force and moment at the end of a semiinfinite beam, 154Figure 9-16Schematic of mechanically harnessed joint with joint rotation, 155Figure 9-17Moment–rotation diagram, 156Figure 9-18Displacement along the pipe length, 161Figure 9-19Moment along the pipe length, 161Figure 9-20Rotation along the pipe length, 162Figure 9-21Shear along the pipe length, 162Figure 9-22Interaction diagram for example 3. The axial force-moment interaction diagrams corresponding to the ultimate strength and the onset of yielding of the steel cylinder are bothnonlinear, but have been approximated by a linear relationship here for ease of computation of the examples, 163Figure 9-23aThrust restraint requirements for 36 in. C301(LCP) bulkhead with restrained joints atPw 150 psi, Pt 80 psi, and Pft 200 psi with 4-ft earth cover in type III soil, 166Figure 9-23bThrust restraint requirements for 54 in. C303 45 bend with welded restrained joints atPw 200 psi, Pt 100 psi, and Pft 250 psi with 6-ft earth cover in type II soil, 166Figure 9-23cThrust restraint requirements for 42 in. C301 (ECP) 75 bend with mechanically restrainedjoints at Pw 140 psi, Pt 60 psi, and Pft 180 psi with 5-ft earth cover in type III soil, 167Figure 9-24Typical welded pipe joints, 168Figure 9-25Details of typical harnessed joints, 169Figure 9-26Typical anchor pipe with thrust collar, 170Figure 10-1Pipe on piers, 174Figure 10-2Pipe elements assumed effective in resisting bending, 175Figure 10-3Configuration of pile-supported installations with joints offset from the supports, 178Figure 10-4Typical supports for pipe on piling, 180Figure 10-5Assumed load and force configuration for design of rigid pipe on piers, 181Figure 10-650-ft (15-m) spans of 42-in. (1,070-mm) concrete pressure pipe were used in this aerial linecrossing of a highway and river levee, 184Figure 11-154-in. (1,370-mm) diameter pipe, preassembled to a 32-ft (9.75-m) unit, being lowered witha double bridge sling in a sewer outfall installation, 188Figure 11-2Typical subaqueous joint-engaging assembly, 191Figure 11-3Five 20-ft (6-m) sections of 84-in. (2,130-mm) diameter pipe were assembled on deck intoa 100-ft (30-m) unit. The 100-ft (30-m) unit was then mounted on precast concrete capsand cradles and installed as a single unit on piles. Two derricks were used to lower thestrongback, cradles, caps, and the 100-ft (30-m) pipe unit, 192Figure 11-4Large-diameter pipe being lifted with a special double bridge sling. Joint-engagingix
assemblies were installed at the ends of the pipe at the springline, 192Figure 11-5Rail-mounted gantry crane used for installing sections of ocean outfall near shore, 193Figure 12-1Typical joint bonding details for embedded cylinder (AWWA C301-type) pipe, 200Figure 12-2Typical joint bonding details for AWWA C303-type pipe or lined cylinder AWWA C301-typepipe, 201Figure 13-1Unloading a typical flatbed truck trailer loaded with 36-in. (910-mm) concrete pressurepipe, 216Figure 13-2Special double-drop highway truck trailer loaded with a single large-diameter pipe, 216Figure 13-3Flatbed piggyback truck trailers loaded with small-diameter pipe, 217Figure 13-4Rail flat cars loaded with 144-in. (3,660-mm) diameter concrete pressure pipe, 217Figure 13-5Oceangoing barge carrying approximately 18,000 ft (5,486 m) of concrete pressure pipe, 218Figure 13-6Specialized equipment for handling and transporting 252-in. (6,400-mm) (ID) pipe weighing225 tons (204 metric tons) each, 219Figure 14-1Backhoe laying pipe, 224Figure 14-2Clamshell excavating inside sheeting, 225Figure 14-3Lowering 84-in. (2,140-mm) pipe to final bedding position in laying shield, 225Figure 14-4Pipe being laid on granular foundation, 227Figure 14-5Pipe bedding, 227Figure 14-6Applying lubricant to the gasket prior to installation, 229Figure 14-7Grouting a pipe joint, 231Figure 14-8Backfilling, 232Figure 14-9Tunnel casing pipe (132 in. [3,350 mm] in diameter) being jacked under a railroad using ametal push ring with a plywood cushion to protect the face of the pipe, 234Figure 14-10Concrete pressure pipe as a carrier pipe inside a casing, 236Figure 14-11Typical tunnel sections, 237Figure 14-12Special equipment, called a “tunnelmobile,” being used to install large-diameter pipe in atunnel, 237Figure 15-1Temporary internal test plug, 241Figure 16-1Small-diameter pressure tap using saddle with straps, 244Figure 16-2Small-diameter pressure tap using split studs, 245Figure 16-3Installation of a small-diameter threaded pressure tap using a saddle with straps, 246Figure 16-4Large-diameter tapping assembly, 247Figure 16-5Pressure tapping a 12-in. (300-mm) diameter flanged outlet on a larger-diameter pipe, 247Figure 16-6Pressure tap of a 12-in. (300-mm) diameter flanged outlet on a 24-in. (600-mm) diameterpipe, 248Figure 16-7Typical pressure-tapping site requirements, 249Figure 17-130-in. (750-mm) pipe ready for delivery, 255Figure 17-224-in. (600-mm) lined cylinder pipe strung along a right-of-way, 256Figure 17-3Prestressed concrete cylinder pipe being lowered into position. Note depth of embankmentcut in background, 257x
TablesTable 2-1Table 3-1Table 3-2Table 3-3Table 3-4Table 4-1Table 5-1Table 5-2Table 5-3Table 5-4Table 5-5Table 5-6Table 7-1Table 7-2Table 7-3Table 9-1Table 9-2Table 9-3Table 12-1Table 12-2Table 12-3Table 12-4General description of concrete pressure pipe, 4Various forms of the Hazen–Williams formula, 14Comparison of theoretical Hazen–Williams Ch values to tested Ch values, 16Kinematic viscosity of water, 19Equivalent length formulas, 23Design values—surge wave velocities, ft/sec (m/sec), 31Design values of settlement ratio, 42Design values of coefficient of cohesion, 49Impact factors for highway truck loads, 51Critical loading configurations, 51Highway loads on circular pipe (pounds per linear foot), 54Cooper E80 railroad loads on circular pipe (pounds per linear foot), 55Tabulation of strength method design for ANSI/AWWA C300-type pipe, 77Tabulation of strength method design for ANSI/AWWA C302-type pipe, 84Allowable external load for ANSI/AWWA C303-type pipe of minimum class, 88Soil type selection guide, 136Summary of design examples and results of detailed calculation, 143Summary of additional design examples, 144Assumed values for required joint bonds shown in Tables 12-2, 12-3, and 12-4, 205Number of bonds for 48-in. prestressed concrete cylinder pipe, 206Number of bonds for 84-in. prestressed concrete cylinder pipe, 208Number of bonds for 144-in. prestressed concrete cylinder pipe, 210xi
Figure 7-2 Force diagrams for reinforced concrete pipe design, 73 Figure 7-3 Section for proportioning tensile steel, 74 Figure 7-4 Section through AWWA C303-type pipe wall, 92. viii Figure 8-1 Common fittings, 96