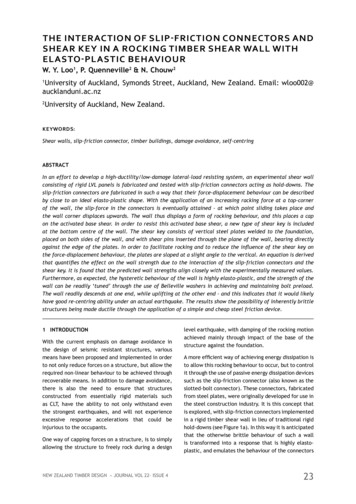
Transcription
THE INTERACTION OF SLIP-FRICTION CONNECTORS ANDSHEAR KEY IN A ROCKING TIMBER SHEAR WALL WITHELASTO-PLASTIC BEHAVIOURW. Y. Loo1, P. Quenneville2 & N. Chouw2University of Auckland, Symonds Street, Auckland, New Zealand. Email: wloo002@aucklanduni.ac.nz12University of Auckland, New Zealand.KEYWORDS:Shear walls, slip-friction connector, timber buildings, damage avoidance, self-centringABSTRACTIn an effort to develop a high-ductility/low-damage lateral-load resisting system, an experimental shear wallconsisting of rigid LVL panels is fabricated and tested with slip-friction connectors acting as hold-downs. Theslip-friction connectors are fabricated in such a way that their force-displacement behaviour can be describedby close to an ideal elasto-plastic shape. With the application of an increasing racking force at a top-cornerof the wall, the slip-force in the connectors is eventually attained - at which point sliding takes place andthe wall corner displaces upwards. The wall thus displays a form of rocking behaviour, and this places a capon the activated base shear. In order to resist this activated base shear, a new type of shear key is includedat the bottom centre of the wall. The shear key consists of vertical steel plates welded to the foundation,placed on both sides of the wall, and with shear pins inserted through the plane of the wall, bearing directlyagainst the edge of the plates. In order to facilitate rocking and to reduce the influence of the shear key onthe force-displacement behaviour, the plates are sloped at a slight angle to the vertical. An equation is derivedthat quantifies the effect on the wall strength due to the interaction of the slip-friction connectors and theshear key. It is found that the predicted wall strengths align closely with the experimentally measured values.Furthermore, as expected, the hysteretic behaviour of the wall is highly elasto-plastic, and the strength of thewall can be readily ‘tuned’ through the use of Belleville washers in achieving and maintaining bolt preload.The wall readily descends at one end, while uplifting at the other end - and this indicates that it would likelyhave good re-centring ability under an actual earthquake. The results show the possibility of inherently brittlestructures being made ductile through the application of a simple and cheap steel friction device.1 INTRODUCTIONWith the current emphasis on damage avoidance inthe design of seismic resistant structures, variousmeans have been proposed and implemented in orderto not only reduce forces on a structure, but allow therequired non-linear behaviour to be achieved throughrecoverable means. In addition to damage avoidance,there is also the need to ensure that structuresconstructed from essentially rigid materials suchas CLT, have the ability to not only withstand eventhe strongest earthquakes, and will not experienceexcessive response accelerations that could beinjurious to the occupants.One way of capping forces on a structure, is to simplyallowing the structure to freely rock during a designNEW ZEALAND TIMBER DESIGN » JOURNAL VOL 22· ISSUE 4level earthquake, with damping of the rocking motionachieved mainly through impact of the base of thestructure against the foundation.A more efficient way of achieving energy dissipation isto allow this rocking behaviour to occur, but to controlit through the use of passive energy dissipation devicessuch as the slip-friction connector (also known as theslotted-bolt connector). These connectors, fabricatedfrom steel plates, were originally developed for use inthe steel construction industry. It is this concept thatis explored, with slip-friction connectors implementedin a rigid timber shear wall in lieu of traditional rigidhold-downs (see Figure 1a). In this way it is anticipatedthat the otherwise brittle behaviour of such a wallis transformed into a response that is highly elastoplastic, and emulates the behaviour of the connectors23
(Figure 1b).This paper provides an overview of experimental workcarried out by the authors.Golondrino et al. [4]. The slip-friction connectorsenable these otherwise rigid frames to behave in ahighly ductile manner.The concept of uplifting and rocking structures is nota new one, and it was as early as 1963, that Housnerpublished an analysis describing the behaviour ofthese ‘inverted pendulum’ structures [5], and showingthat even tall slender structures can in fact be morestable against overturning than expected, due to ascale effect. Makrisand Konstantinidis [6] furtherestablished the correct conditions that would causea rigid block to overturn, and derived mathematicalexpressions providing the minimum accelerationsrequired for overturning.ElGawady et al. [7] experimented on rocking rigidblocks, but with various materials (concrete, timber,steel, and rubber) at the contact interface, and foundthat material type significantly influenced rockingbehaviour.Figure 1: (a) General concept, (b) intended hystereticbehaviour of wall with slip-friction connectors2 PREVIOUS RESEARCHTo achieve ductility in seismic design, base shears arecapped to a level well below what would be the casehad the same structure been designed as fully elastic.Typically, a ductile structure deforms plastically atpre-defined points in the structure, while at the sametime the main structural members remain elastic. Inthis way catastrophic collapse is avoided and damagelimited. Nevertheless what damage does occur duringan ultimate limit state event is generally expected tobe irrecoverable.In order to allow nonlinear behaviour without damagein steel buildings, Clifton [1] developed the slidinghinge connector. The sliding-hinge connector is a typeof slip-friction connector that is implemented at thebeam-column joints of moment frames. Experimentalwork has verified the effectiveness of the sliding-hingeconnector, and it has now been included in severalmulti-storey buildings in New Zealand [2].Slip-friction connectors have also been tested for usein braced frames, by Popov et al. [3] and also Chanchi24Acikgoz and DeJong [8] investigated the behaviour ofrocking structures that consisted of a single-degree offreedom structure rigidly connected to a rigid base,and found that these structures have a behaviourthat consists of a complex interplay betweenelastic vibratory motion and non-linear rockingmotion. Sarrafzadeh et al. [9] have explored notonly the benefits of rocking, but also the additionaladvantages gained in terms of limiting base shearthrough consideration of the plastic deformation ofthe foundation soil.The concept of movable or rocking structures isnot only an abstract or theoretical one. Alreadypioneering research at the University of Canterburyhas led to the implementation of rocking shear wallsin the construction of the NMIT Arts and Media Buildingin Nelson, New Zealand. These walls include posttensioned cables along their vertical length to resistuplift up to a design level seismic event, and then toassist in re-centring during such an event. Devereuxet al. [10] describes in some detail the design andconstruction of this iconic building.Loo et al. [11] studied the feasibility of allowingrocking for both flexible timber shear walls with slipfriction connector hold-downs. Base shear is cappedwhen the sliding threshold, Fslip is achieved. Theforce-displacement behaviour of the connectors iselasto-plastic, and this connector behaviour governsthe overall performance of the wall. Another studyby Loo et al. [12] found that not only would the useof slip-friction connectors cap base shear, but wouldlikely reduce overly large response accelerations inVOL 22· ISSUE 4 » NEW ZEALAND TIMBER DESIGN JOURNAL
rigid timber buildings.Based on these promising numerical studies, theauthors fabricated and tested a rigid LVL wall usingslip-friction connectors as hold-downs. A shear key wasalso developed that would not unduly influence theload limiting capability and energy dissipation effectsof the slip-friction connectors. In the subsequentsections, details of the experimental set-up areprovided, the slip-friction connectors and shear keyand their interaction are discussed, and finally someresults of the tests carried out are presented.3 EXPERIMENTAL SET-UPA 2.44 x 2.44 m rigid wall panel was fabricated fromtwo 1.22 x 2.44 m and 45 mm thick LVL panels. Thepanels were joined together by studs and top andbottom plates (300 x 45 mm in cross section), alsoof LVL. Screw connections (around 700 4.9 x 75 mm)were adopted because of their inherent stiffness,required in order to maximise the rigidity of the wall.A maximum racking force of 70 kN was considered inthe design. The experimental wall is shown in Figure2.Figure 3: Actuator and force transfer platesThe plates were tightly bolted to the top wall cornerusing 25 mm bolts. The bolts were tensioned byturning the nut against Solon 16L150 washers until thewashers were completely flattened. With the flat loadof the washers being around 50 kN, and an assumedcoefficient of friction of wood on steel being around0.65, 325 kN of static friction was mobilised (5 boltsx 2 surfaces x 50 kN x 0.65). In this way the potentialproblem of ‘slop’ that is characteristic of boltedconnections, would be obviated for loading within theintended range (up to 70 kN). It is noted that duringall the tests carried out on the rig, these plates weremonitored for movement and none was observed.The hydraulic actuator controller, and data acquisitionmodule and computer are shown in Figure 4.Figure 4: Hydraulic actuator controller and dataacquisition module and computerFigure 2: General set-up of experimental rigIn order to prevent the wall from displacing in theout-of-plane direction, a bracing ‘channel’ of LVLmembers was fabricated and secured between twosteel columns. This channel can be clearly seenin Figure 2. In order to apply the racking force, ahydraulic actuator with a 100 kN load cell used, withthe load applied to 900 x 100 x 10 mm mild steelplates on either side of the top corner of the wall (seeFigure 3).NEW ZEALAND TIMBER DESIGN » JOURNAL VOL 22· ISSUE 4LVDTs at the bottom corners recorded vertical upliftand a draw-wire was used to record horizontaldisplacement (see Figures 5a and 5b respectively).The slip-friction hold-downs were attached to theend chords by riveted connections. At the Universityof Auckland, Zarnani and Quenneville [13, 14, 15]have developed analytical models, substantiated byextensive experimental studies, that demonstratethe tremendous strengths and stiffness that can beachieved over a small transfer area through the useof riveted connections. To attach the slip-friction25
While asymmetric connectors, when installed at thebeam-column joint can provide a re-centring effect,this is not required for the shear wall, where gravityis expected to provide most of the re-centring action.Therefore symmetric connectors, which altogetherhave a simpler mechanism (with the bolts only intension, compared to tension, shear, and bending,for the asymmetric connector), and a hystereticbehaviour closer to the elasto-plastic ideal, wereadopted for these tests.Figure 5: (a) Draw-wire to measure and record horizontaldisplacement and (b) LVDTs were used for verticaldisplacement at the bottom-corners of the wallconnectors to the end chords of the wall, 6 rows and4 columns of 65 mm long rivets were used (see Figure8).The shear-key assemblage (see Figure 9) consisted oftwo solid steel 25 mm diameter pins inserted throughthe base of the wall, and bearing against upright mildsteel plates on both sides of the wall. These mild steelplates were welded to the 32 mm thick foundationsteel plates.The slip-friction connectors and shear key arediscussed in further detail in the following twosections.4 SLIP-FRICTION CONNECTORSSlip-friction connectors are typically of two types,asymmetric and symmetric. With asymmetricconnectors the force, Fslip, is applied directly to thecentre plate, and only one of the outside plates (see6(a)), whereas with symmetric connectors the forceFslip on centre plate, is resisted equally (1/2 Fslip)by external forces on the outside plates (see Figure6(b)).It was found by Popov et al. [3] that mild-steelagainst mild-steel produced extremely uneven stickslip sliding, and that in order to improve the slidingcharacteristics and avoid sudden and unexpected loadincreases, 3 mm brass shims were required. However,during testing of asymmetric connectors, Khoo et al.[16] found that replacing the expensive cartridge hardbrass with shims of wear resistant Bisalloy 400 steel,in asymmetric worked just as well.In the case of the symmetric sliding mechanism,Loo et al. [17] tested connectors with a centreplate of Bisalloy 400, and mild-steel outside plates.This concept simplifies the fabrication process withshims not required, and the sliding interfaces aredirectly between the outside and centre plates. Itwould be expected that problems of corrosion arereduced because with only two sliding interfaces asopposed to four (in the case where shims are used),the opportunity for the inflow of constituents thatcould accelerate corrosion is lessened. It shouldalso be noted that thin shims (3 mm thick) wouldnaturally have a greater likelihood of losing thicknesswith corrosive attack from both sides. A series ofcomponent tests were carried out and the connectorsdemonstrated excellent elasto-plastic behaviour [17].A typical result is shown in Figure 7.Figure 6: Slip-friction connector with (a) asymmetricmechanism, and (b) symmetric mechanismFigure 7: Hysteretic behaviour of connector with Bisplate400 slotted centre-plate26VOL 22· ISSUE 4 » NEW ZEALAND TIMBER DESIGN JOURNAL
Figure 8(a) shows a slip-friction connector attachedto the experimental wall and Figure 8(b) shows theconnector undergoing sliding (the slot in the centreplate is clearly visible).other.For a more detailed discussion of the procedure referto Loo et al. [18].Figure 9: A depth micrometre was used to measure theheight of the Belleville stack5 SHEAR-KEYFigure 8: (a) Slip-friction connector attached to wall withrivets, (b) connector undergoing sliding, with flat washeron top of Belleville stack in viewBelleville washers were used to obtain and maintaintension, Tb, in the bolts (see Figure 8(b)). It is this boltpreload which provides the normal force mobilisingfriction between the plates. The force threshold ofthe slip-friction connectors, Fslip, is given by:where ns is the number of faying surfaces (two inthis case), nb the number of bolts (two), and μ thecoefficient of friction, and Tb is the preload in the bolts.Assuming a linear force-displacement relationship, arelationship was developed to provide the requireddeflection of a stack of Belleville washers in order toobtain Tb. The equation for the final height, hTb ofthe Belleville washer stack after compression, and asa function of Tb is:where nparallel and nseries is the number of washersin parallel and series respectively, and δflat and Pflatthe flat deflection and flat load of a single washer,respectively.The authors measured this deflection directly using adepth micrometre (see Figure 9), and this allowed theconnectors, one at each bottom corner of the wall,to achieve sliding strengths (Fslip) very close to eachNEW ZEALAND TIMBER DESIGN » JOURNAL VOL 22· ISSUE 4The shear-key consisting of two upright 12 mm thickG350 mild steel plates on both sides of the wall (atotal of 4 plates) welded to the foundation, and twoshear pins of Grade AISI 4140 steel is shown in Figure10.Figure 10: Shear keyThe shear-pins togetherconstitute the shear-key.withtheshear-platesFrom Figure 10 it is apparent that the direction of theracking force resisted is in the same direction of shearpin to shear plate – thus for the case displayed, theleft pin/plate pair resists rightward racking forces,and the right pin/plate pair resists leftward rackingforces.Note that the bearing edges of the plates are set atan angle slightly off vertical (12 degrees in this case).This was done in order to reduce the contributionof the mobilised friction between pin and plateto overturning resistance - it is desirable that thehysteretic behaviour of the wall be governed largelyby the behaviour of the slip-friction connectors, andnot the shear keys.27
How to account for the effect of the shear-keyon moment resistance and overall wall strength isdiscussed in the next section.6 INTERACTION BETWEEN THECONNECTORS AND SHEAR-KEYSLIP-FRICTIONIn order to develop expressions to describe theinteraction of shear-key and slip-friction connectorsconsider the wall uplifting under a quasi-static load P.that for the wall shear key, the coefficient of frictionwould be expected to be around 0.6). It can beseen that the influence of the shear key on momentresistance declines rather quickly with increasingangle of bearing – this can be considered to be apositive effect, in that the relatively unpredictablefrictional effects arising from within the shear key aremitigated.Figure 12: The contribution of the shear key to the overallmoment resistance – variation with increasing bearingangle, φ, for μ ranging from 0.2 to 0.87 EXPERIMENTAL RESULTSFigure 11: Activated forces on wall during uplift underquasi-static load, PFrom Figure 11, considering the equilibrium ofmoments about the bottom right hand corner ofthe wall, it can be shown that the racking force, P,required to cause rocking is:A series of reversed quasi-static cyclic tests werecarried out on the wall, firstly without floor diaphragmeffects, and then with floor diaphragm effects. Amodified ISO protocol was adopted, with 3 or 4 cycleseach of 25%, 50%, 75%, and 100% of a maximumhorizontal drift of 4% of the wall height (approximately100 mm). Figure 13 shows a displacement protocol, asideally implemented.Kmrp is a constant that is a function of the placementand slope of the shear key, and the coefficient offriction between the shear plate and shear pin. Theexpression is:The contribution of the shear key, Mrsk, to the overallmoment resistance, Mr, can be expressed as a ratioand plotted against increasing angle of bearing for theshear plates, φ, and for various coefficients of friction,μ. Figure 12 shows the variation of Mrsk/Mr with φ forvarious coefficients of friction, μ, and calculated forparameters pertaining to the the experimental wall,with h 0.06 m, b 0.91 m, and Wself 2.8 kN (note28Figure 13: Displacement protocolVOL 22· ISSUE 4 » NEW ZEALAND TIMBER DESIGN JOURNAL
However, the point should be raised that this protocolwas not adopted for all the tests, and in many casesabridged displacement schedules were used sothat a reasonable idea could be obtained of forcedisplacement behaviour, without wearing out theslip-friction connectors and thus requiring furthertesting to be abandoned. It is noted that each of theconnectors experienced at least 20 m of cumulativetravel without diminution in performance, and thistestifies to the robustness of the connector designdescribed in Section 4.Figure 14 shows the typical force-time history for thewalls – note how in this case, the force on the wall isconsistently capped to approximately 40 kN, as wasintended.Figure 15: Vertical displacement time-history at wallcornerforces on the wall were essentially the same, for bothloading directions, and this testifies to the precisionachieved in adjusting the slip-friction connectorforces at both ends of the wall. The behaviour of thewall closely corresponds to the ideal elasto-plasticcase.Figure 14: Typical force time history resultIn order for the wall to be able to descend at one endsimultaneous with the wall ascending at the oppositeend, the difference in strength of the connectors,Fslip, must be less than the total of the verticalforces on the wall, including self-weight. Additionalloads on the wall were not imposed, and apart from acomponent of vertical force from friction in the shearkey, only self-weight assists in re-centring. Note thatit is important that
turning the nut against Solon 16L150 washers until the washers were completely flattened. With the flat load of the washers being around 50 kN, and an assumed coefficient of friction of wood on steel being around 0