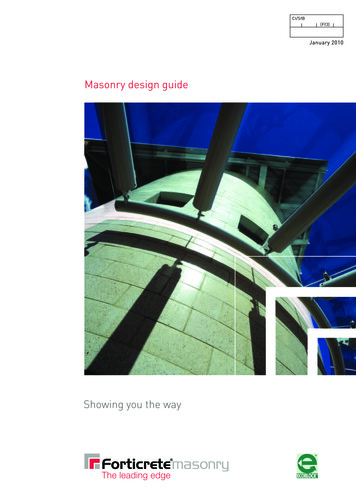
Transcription
CI/SfB(Ff3)January 2010Masonry design guideShowing you the wayECOBLOCK
Contents3Product performance333344444Quality assuranceThe British Standards KitemarkWeathering resistanceDimensional tolerancesCut productsCompositionUse of colourManufacturing control categoryAir permeability5Modular design5558888Use of tablesPrinciples of tablesUsing 5mm jointsRadius walls using standard blocksOverhangsPerpendsRadius wall using precastcurved units9Movement control and bed n of movementControl jointsFormation of control jointsHorizontal control jointsBed-joint reinforcementInternal wallsExternal wallsStack bondingBrick and block bandingThe use of bed joint reinforcementTypical manufacturersMedici masonry,Twelve Princess Dock, Liverpool14 Fixing and detailing14 Fixings14 Provision for services and fittings19 Structural performance22 Reinforced masonry lintels23 Cover for reinforcement23 Sequence of construction24 Fire resistance25 References and bibliographyIntroductionThe consistently high standards which Forticrete maintainthroughout its extensive product range are derived fromover 40 years established production experience.This experience is augmented by a Quality Assurance scheme which guarantees: high durability low water absorption low drying shinkage colour consistency additional water repellence for improved weathering dimensional tolerances to BS EN 771-3:2003Customer satisfaction is an integral aspect of Forticrete’s approach and is expressed ina ‘Customer Service Policy Statement’ in the Company’s Sitework Guide.Front cover:Florentine masonry,Gartnavel General Hospital,Glasgow2
Product performanceQuality assuranceDimensional tolerancesForticrete’s Total Quality Management philosophy embraces everyaspect of the company’s activities and manufacturing processes.The company’s main objective is to exceed the requirements ofits own criteria, as well as those of its customers and all relevantregulatory authorities.All Forticrete Masonry Products are manufactured to the requiredtolerances of BS EN 771-3: 2003, Class D1; Walling Stone toBS EN 771-5: 2003 and Cast Stone to BS EN 1217. However, inconjunction with the company’s Quality Assurance registration,Forticrete has targeted an improvement on the British Standardtolerances, as shown in Table 1.Forticrete has long recognised that its success is directly linkedto the continued satisfaction of its customers. The companyhas established strict procedures to ensure that every productmanufactured at each production plant throughout the UK meetsthe stringent requirements laid down in its quality control system.All Forticrete Masonry plants are BSI registered and operateto the requirements of BS EN ISO 9001:2000 - the National andInternational Standard for quality systems. On-going training andeducational programs for management, technical and productionpersonnel ensure that the company’s adherence to theserequirements is achieved at all levels.Table 1 Forticrete target n MasonryTextured 2,-2 2,-2 2,-2Fairface 2,-2 2,-2 2,-2Twinbloc 2,-2 2,-2 2,-2Ribloc 2,-2 2,-2 2,-2Sparstone 2,-2 2,-2 2,-2Strict adherence to quality procedures creates quality productsand many of Forticrete’s Specification Masonry products arelicensed to carry the prestigious British Standards Kitemark.Novastone 2,-2 2,-2 2,-2The British Standards KitemarkFlorentine 2,-2 1,-3 2,-2Venezia 2,-2 1,-3 2,-2The Kitemark is a BSI Certification Trade Mark. BSI licenses theuse of the Kitemark on products only after it has:Medici 2,-2 1,-3 2,-2i)Splitface Masonryhad a sample of the product tested independently to satisfyitself that the product conforms to the marked BritishStandard specification.ii) visited and assessed the manufacturer to BS EN ISO9001:2000 and has satisfied itself that the quality systemoperated by the manufacturer ensures the product’scontinuing conformity to specification.Weathering resistancePolished MasonrySplitface 2,-2N/A 2,-2Ribloc 2,-2N/A 2,-2Sparstone 2,-2N/A 2,-2Glazed MasonryAstra-Glaze -SW To ASTM C90- Type 1Walling StoneAll Forticrete Specification Masonry products are manufacturedwith water repellent additives which dramatically reduce bothwater absorption and penetration.Anstone To BS EN 771-5: 2003Shearstone To BS EN 771-5: 2003These additives are incorporated in the constituent mix designand are therefore an inherent feature of the products even aftercutting, splitting or texturing of the surface.Cast StoneThis improved ability to repel moisture greatly accelerates thedrying process following inclement weather, thereby reducingthe adhesion of atmospheric dirt particles which normally lead tounsightly staining.An additional benefit during construction is a reduced initialsuction of moisture from the joints, allowing improved curing ofthe mortar without any loss of adhesion.Dressings (see table 2)Regency Ashlar 2,-2 2,-2 2,-2Arenabloc 2,-2 2,-2 2,-2Painting Quality 2,-2 2,-2 2,-2Commons 3,-5 3,-5 3,-5Standard MasonryTable 2Dimensional tolerances cast stone & precast masonryUnit LengthTolerance0-600mm 2mm601-1000mm 3mm1001-2500mm 4mm2501-4000mm 5mm 4000mm 6mm3
Cut productsManufacturing control categoryForticrete is able to offer a comprehensive cutting service for thecreation of special shapes and sizes.BS 5628 is the British Standard Code of Practice for the designand use of masonry. It is based on Limit State Design principleswhich allow the designer to choose a partial safety factor γm formaterial (See table 4) which is in turn affected by the choice ofcontractor or material supplier.The general tolerance on cut dimensions is 2mm, although incertain circumstances it is not possible to achieve this, e.g. wherea shallow cut is less than 25 to a face.The general tolerance on cut angles is 1.5 and taper-to-cutfaces will be within 1mm.CompositionForticrete masonry products are manufactured from thehighest quality raw materials which are rigorously checkedfor performance and consistency. This process results in highquality products which meet the demanding requirements of ourcustomers and the appropriate regulatory standards.To ensure consistently coloured and textured products, particularemphasis is placed on the tight control of material gradings andon-line process equipment.As this safety factor is applied directly to structural calculationsit can be seen that the design performance of masonry canbe improved by choosing a manufacturer supplying productsconforming to Category I Manufacture Control. The benefitin terms of this alone is in the order of a 12% increase, in thedesign vertical load capacity of the blockwork.Please note that these are the partial factors of safety onmaterial strength only.Table 4Partial safety factors for material strengthManufacturing Constructioncontrol category control categorySpecial NormalUse of colourI2.5 3.1II2.8 3.5Forticrete has pioneered the use of coloured masonry.The colours are specially matched to cater for regionaldifferences, so that if needed they can blend comfortably intothe local vernacular.In addition to their harmonising and economical advantages inconservation areas, the Forticrete range of colours has a wideraesthetic potential. Bands and shapes of colour can be used tocreate both visual devises and dramatic effects.If combined with particular bond patterns and textures thepermutations are endless.Table 3 Typical material gross dry density Textured , Fairface ,Sparstone , Florentine , Venezia & Standard MasonryFace low17001600140P1Solid21002000The latest amendments to Part L (Conservation of Fueland Power) of the Building Regulations include a limit onair permeability. Forticrete products have been testedindependently for air leakage and return excellent results, assummarised in Table 5.Table 5Air permeabilityProductFormatAir Permeabilitym3/hr/m2Textured Solid2.16Textured Hi-Light 2.59Textured Hollow0.58Fairface Solid2.07Fairface Hi-Light 4.66Florentine Solid0.98Florentine Hi-Light 1.42Solid1.03140P3Hollow12501150140P2Hi-Light 15001400Medici 1220Anstone Solid0.18Solid0.14Solid0.134Gross Dry Density (Kg/m3)SpecificationStandardMasonryMasonryAir 21002000Shearstone Walling100D1Solid21002000Regency llow14001400140H2Hi-Light 14601450215F1Solid21002000215F3Hollow14001400
co Modular designco When detailing masonry panels, the designer should set outmasonry units to full or half block lengths where possible to avoidunsightly and unnecessary cutting of units on site. Co-ordinatingdimensions will also ensure that the masonry is properly bonded.Bed Joint Reinforcement should beintroduced in the blockwork panels,above and below the openings inFig 1. See also page 12.CO-Helpful hintcoco co-ordinated size minus a jointThis is the(ie, actual block length or height).Figure 1, contrasts the effects of an unco-ordinated and coordinated approach to setting out of masonry. (Using 440 x 215mmblocks as an example).coco-Step 2Fig. 1 Setting outFrom the selected co-ordination factor column, find therequired blockwork dimension and then read off therelated number of blocks.Tables are provided for guidance purposes only. Considerationshould be given to allow for the discontinuation of panels whenmovement joints are incorporated (generally 9m externally and amaximum of 12.2m internally.)1500204084587587014501725Forticrete cannot be held responsible for errors in the finaldesign. All dimensions should be checked by the designer.Reference should also be made to BS 8000 Part 3 ‘Code of practicefor masonry’ which covers allowable building tolerances on site.750Unco-ordinated approachPrinciples of tablesAll blockwork dimensions are determined by one of threealternatives which relate to specific wall configurations.1. Co-ordinated size plus a joint (CO ) i.e. door and windowopenings15852260CO 89090091013401810665CO CO to internal corner)return end (internalCo-ordinated approachTables 6 to 9 enable the vertical and horizontal co-ordination of390 x 190mm and 440 x 215mm block face sizes to be set out atthe design stage.2.Co-ordinated size (CO) CO CO COi.e. block panels with oppositereturn ends or quoins.return end (externalCO- to internal corner)CO COUse of tablesStep 1CO Using the wall configuration to be considered, selectthe appropriate co-ordination factor column from thetables,ie CO , CO or CO- :3.CO-Co-ordinated size minus a joint (CO-)COi.e. block piers or panels between openings.COCO-This is the co-ordinated size plus a joint (ie, actual blocklength or height 2 joints)openingco co COCO-panel betweenopeningCO-co co co-ordinated size (ie, actual block length orThis is theUsing 5mm jointsheight 1 joint)Regency Ashlar Traditional and City Bonds in the Regency rangeare also manufactured to larger sizes to accommodate 5mmmortar joints.cocoThis requires careful consideration with regard to setting out andalso in the use of wall ties and bed joint reinforcement.cococococo-5
Table 6 Horizontal blockwork co-ordinating dimensions using 390 x 190mm blocksNo of blocksCO COCO-No of 48.549CO COCO-No of blocksCO 9028790289902919029390CO CONo of 7400760078008000Table 7 Vertical blockwork co-ordinating dimensions using 390 x 190mm blocksN
When detailing masonry panels, the designer should set out masonry units to full or half block lengths where possible to avoid unsightly and unnecessary cutting of units on site. Co-ordinating dimensions will also ensure that the masonry is properly bonded. Figure 1, contrasts the effects of File Size: 2MBPage Count: 28Explore furtherTechnical Guidance Concrete Block Strength Compressive .www.thomasarmstrongconcreteblo TECHNICAL INFORMATION SHEET - Ibstock Brickwww.ibstockbrick.co.ukExpansion joints in brickwork and blockwork - what you .www.growtivation.comBrickwork and Blockwork - New Build Inspectionswww.newbuildinspections.comMovement joints in masonry walls - NHBCwww.nhbc.co.ukRecommended to you based on what's popular Feedback