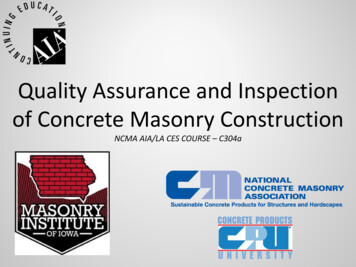
Transcription
Quality Assurance and Inspectionof Concrete Masonry ConstructionNCMA AIA/LA CES COURSE – C304a
DisclaimerThe National Concrete Masonry Association is a Registered Providerwith The American Institute of Architects (AIA/CES) ContinuingEducation System. Credit(s) earned on completion of this program willbe reported to AIA/CES for AIA members. Certificates of Completionwill be provided to all attendees upon request.This program is registered with AIA/CES for continuing professionaleducation. As such, it does not include content that may be deemedor construed to be an approval or endorsement by the AIA of anymaterial of construction or any method or manner of handling, using,distributing, or dealing in any material or product.Questions related to specific materials, methods, and services will beaddressed at the conclusion of this presentation.2
Course DescriptionThis presentation provides an overview of theinspection and quality assurance provisionsassociated with concrete masonry constructionas required by the 2015 International Buildingand Residential Codes (IBC and IRC) and TMS602-13, Specification for Masonry Structures.3
Learning ObjectivesAt the end of this course, participants will beable to:1. Distinguish between quality assurance andquality control.2. Understand the code requirements forconcrete masonry construction.3. Identify the code requirements for concretemasonry inspection.4. Evaluate construction tolerances.4
Project Specification ItemsCompressive strength, f’m, & verification methodSubmittal reporting & review processRequired quality assurance levelSample panel requirementsMasonry unit and mortar types, colors, etc.Reinforcement & accessory types, grades,corrosion protectionDetails of pipes, conduits, accessories,movement joints, joint fillers, anchors5
The Need for QA6
The Need for QA and QC Higher quality and better masonryperformance Increased confidence that the projectwill be constructed correctly and asdesigned Confidence in design reduces overdesign More cost efficient7
QA vs. QCWhat is the difference?Quality Assurance (QA): the owner’s ordesigner’s efforts to determine projectacceptability, accomplished through testing,field inspection, and QCQuality Control (QC): contractor’s ormanufacturer’s efforts to ensure the finalproperties of the product in effort to achieve aspecified goal8
InspectionInspection: the action(s) taken to ensure thatthe established quality assurance program willbe met9
Primary InspectorsBuilding Department Inspectors Periodic visits Issue permits based on inspections Degree of inspection variesSpecial Inspectors Qualified individual(s) to examine definedaspectsTypically hired by owner/designerDesigners – Architect/Engineer Observe construction10
Duty of Inspectors To monitor, observe,verify, document,and report results Bring problems orpotential problems to the attention of thearchitect/engineer and contractor***It is up to the architect/engineer to takeaction to resolve issues.11
TMS 602 SpecificationSynopsis and KeywordsPrefacePart 1 – GeneralPart 2 – ProductsPart 3 – ExecutionSpecification Checklist12
IBC Reference Documents2009 IBC2012 IBC2015 IBC2008 TMS2011 TMS2013 TMS13
TMS 602 Part 1: General SubmittalsLevels of inspectionMasonry compressive strengthDelivery, storage, and handlingProject conditions14
Article 1.5 – SubmittalsMix designs and test results Mortar and groutMaterial certificates Reinforcement, anchors, ties, and fasteners Units, mortar and grout materials Self-consolidating groutConstruction procedures Hot and cold weather procedures15
Submittals – Mortar and Grout Mortaro Type and proportions of ingredients forproportion speco Mortar test results for property spec Grouto Type and proportions for proportion speco Strength tests for property speco Strength tests, slump flow, and VSI for selfconsolidating grout16
Submittals – Material Certificates Reinforcement Anchors, ties,fasteners, metalaccessories Masonry units Mortar and groutmaterials Self-consolidatinggrout17
Article 1.6 – Quality AssuranceQuality Assurance Levels – Level A (Basic Level),Level B (Intermediate), Level C (Rigorous)Which to use? Building code typically prescribes based ontype of structure/construction and designmethod: essential vs. nonessential prescriptive/empirical vs. engineered18
Types of InspectionInspection, continuous – The InspectionAgency’s full-time observation of work by beingpresent in the area where the work is beingperformed.Inspection, periodic – The Inspection Agency’spart-time or intermittent observation of workduring construction by being present in the areawhere the work has been or is being performed,and observation upon completion of the work.19
Quality AssuranceQA Level Facility ConstructionEmpirically designedGlass unit masonryMasonry veneerEngineered masonryEmpirically designedGlass unit masonryMasonry veneerEngineered masonry20
TMS 602 QA - Level A (basic)Minimum VerificationPrior to construction, verify certificates of complianceused in masonry construction.21
TMS 602 QA – Level B(intermediate)Applies to essential facilities when inspecting: Empirically designed masonry Masonry veneers Glass unit masonryApplies to non-essentialfacilities when inspecting: Engineered masonry22
TMS 602 QA - Level B(intermediate)23
TMS 602 QA - Level B(intermediate)Minimum TestsVerify f’m prior to construction*For self-consolidating grout (SCG), verify slump flowand Visual Stability Index (VSI), as delivered to site* except where specifically exempted by the Code (TMS 402)24
TMS 602 QA - Level B(intermediate)Minimum Special Inspection1. Verify compliance with approved submittals2. Verify the following are in compliance:PProportions of site-prepared mortarConstruction of mortar jointsPPPS tendon & anchorage grade and sizePLocation of reinforcement, connectors, etc.Prestressing techniquePP25
TMS 602 QA - Level B(intermediate)Minimum Special Inspection3. Prior to grouting verify the following comply:Grout spacePGrade, type, size of reinforcement, etc.Placement of reinforcement, etc.PPProportions of site-prepared grout & PS groutPConstruction of mortar jointsP26
TMS 602 QA - Level B(intermediate)Minimum Special Inspection4. Verify during construction:Size & location of structural elementsPType, size, & location of anchorsWelding of reinforcementPCPrep, construction, & protection during hotand cold weatherApplication & measurement of PS forceGrout placement is in compliancePCC27
TMS 602 QA - Level B(intermediate)Minimum Special Inspection5. Observe preparation of grout specimens,mortar specimens, and/or prismsP28
TMS 602 QA - Level C (rigorous) Can be used for both essential andnon-essential facilities Must be usedwith essentialfacilities requiringengineereddesign29
TMS 602 QA – Level C (rigorous)Minimum TestsVerification of f’m prior to construction & for every5,000 ft2 during constructionVerification of material proportions in premixed orpreblended mortar, PS grout, & grout other than SCGas delivered to the project siteFor self-consolidating grout, verify slump flow andVisual Stability Index (VSI), as delivered to site30
TMS 602 QA – Level C (rigorous)Minimum Special Inspection1. Verify compliance with approved submittals2. Verify the following are in compliance:PProportions of site-mixed mortar & groutGrade, type, size of reinforcement, etc.PPPlacement of units & mortar joint constructionPPlacement of reinforcement, etc.CGrout space prior to groutingC31
TMS 602 QA – Level C (rigorous)Minimum Special Inspection2. Verify the following are in compliance (cont’d):Grout placement is in complianceSize & location of structural elementsCPType, size, & location of anchorsCWelding of reinforcementCPrep, construction, & protection during hot andcold weatherApplication & measurement of PS forcePC32
TMS 602 QA – Level C (rigorous)Minimum Special Inspection3. Observe preparation of grout specimens,mortar specimens, and/or prismsC33
Article 1.6D Sample Panels Required for QALevels B & C Workmanshipcriteria for contractor Min. 4 ft x 4 ft Display range of materials Used to accept/reject masonry work34
Article 1.7 – Delivery, Storage,and HandlingStipulates protection of materials on site: Don’t use damaged products. Keep mortar and grout materials dry. Don’t use contaminated materials. Store aggregates separately. Protect metal materials from permanentdistortion and store off the ground.35
Article 1.8 – Project ConditionsDefines conditions for: Protection of masonry during construction Cold weather construction Hot weather construction36
Article 1.8 – Project ConditionsCold weather construction procedures: 40 oFModify:constructionproceduresbased onmasonry protectionambient temperaturemin. daily temp forgrouted masonrymean daily temp forungrouted37
Article 1.8 – Project ConditionsHot weather construction procedures100 oF or 90 oF and wind speed 8 mphModify:based onpreparationambient temperatureconstructionprotectionmean dailytemperature38
TMS 602 SpecificationPart 1 – GeneralPart 2 – ProductsPart 3 – Execution39
Verify MaterialsUnitsMortarGroutReinforcementPrestressing tendons,anchorages, and couplersJoint reinforcementAnchors, ties, accessoriesCorrosion protection40
Verification of f’mArticle 1.4 defines the minimum compressivestrength requirements for concrete masonryconstruction (f’m). There are two ways to verifythe assembly compressive strength:1) prism testing; or2) unit strength method41
Verification of f’mUnit Strength MethodNet areacompressive strengthof masonry, psi1,7001,9002,0002,2502,5002,7503,000Net area compressive strengthof concrete masonry units, psiType M or SType 03,900-----4,500-----42
Verification of f’mPrism Test MethodMasonry prisms are constructed and tested inaccordance with ASTM C1314.43
Proportions of Site-Mixed Mortar44
ASTM C270 Property SpecificationMortarTypeCompressivestrength, min psiMSNO2,5001,800750350Waterretention,min %75757575AirContent, max %121214*14** 20% for masonry cement, may also vary if mortarcontains structural reinforcement
Mortar is Proportioned by Volume46
Article 2.6 – MixingMixing instructions for mortar and grout47
Proportions of Site-Prepared GroutType of Portland or Hydratedgroutblendedlime orcement lime puttyFine10 – 1/10Coarse10 – 1/10Aggregate*FineCoarse21/4 - 321/4 - 31-2* Aggregate proportion is relative to the sum of thevolumes of the cementitious materials; aggregate ismeasured in a damp loose condition.48
Verification of Grout PropertiesCompression testing49
Verification of Grout PropertiesSlump50
Self-Consolidating GroutWhat is self-consolidating grout?SCG is a stable, highly fluid grout that doesnot segregate when placed and requires noconsolidation or reconsolidation.SCG is not a watered-down grout.
Verification of SCG PropertiesASTM C1019:– Compressive strengthASTM C1611:- Slump flow, required, 24 – 30 inches- Visual stability index (VSI), required, 1- Relative viscosity, T20(T50), voluntary52
Verification of SCG PropertiesSlump flow53
Verification of SCG PropertiesVisual Stability Index (VSI)54
Article 3.1 – InspectionFoundation tolerance of /- ½” More stringent than ACI 117Specified plane elevationAs built top offootingZ 1 2 in.(13 mm)ZSpecified planeelevation- 1 2 in.(13 mm)55
3.2 – Preparation Clean reinforcement, anchorbolts and units No wetting units – wet cuttingpermitted Remove debris before groutingvia cleanouts for lifts over 5’4” – reasonably clean No wet sticking ofreinforcement56
3.3 – Masonry ErectionRunning bond is default bond patternHead and bed joints – size and tolerancesHollow units – see next slideSolid units – fully mortared head and bed joints No slushing of head joints. Shove unit against adjoining unit.57
3.3 – Masonry ErectionHollow unit masonry Face shell mortar bedding Webs mortared in all courses of piers,columns, and pilasters or for confinement Head joints mortared equal to face shellthickness Align vertical cells to be grouted58
3.3 – Masonry ErectionBrace to ensure stability Internal bracing accepted byOSHA and ASCE 37 DesignLoads on Structures DuringConstruction See TEK 3-4C Bracing ConcreteMasonry Walls UnderConstruction59
3.3 – Masonry ErectionPlacing adhered veneer Neat cement paste tobacking and unit Type S mortar – 3/8” to1¼” thickness Tool mortar joints No embedding ofaluminum unless isolated60
Construction TolerancesHead joint thickness 3 8 in. - 1 4 in., 3 8 in.Bed joint thickness 3 in. 1 in.88FootingInitial bed joint thickness 1 in. min.43 in. max.4
Level 1 4 in. (6.2 mm) in 10 feet (3,048 mm) 1 2 in. (13 mm) maximumDesired bedjoint location62
Size & Location of StructuralElementsLocation in Plan 1 2 in. (13 mm) in 20 ft (6,096 mm) 3 4 in. (19 mm) maximumTrue to a Line 1 4 in. (6.4 mm) in 10 ft (3,048 mm) 3 8 in. (9.5 mm) in 20 ft (6,096 mm) 1 2 in. (13 mm) maximumPlanned LocationActual LocationSpecified Location 1 4 in. (6.4 mm)in story height 3 4 in. (19 mm)maximum63
Plumb & AlignmentSpecified elevationAlignment tolerances 1 2 in. (13 mm) forloadbearing walls 3 4 in. (19 mm) fornonloadbearing wallsFloor slabSpecifiedcross-section1- 4 in. (6.4 mm) 1 2 in. (13 mm)- 1 4 in. (6.4 mm) 1 2 in. (13 mm)Upper wallLower wallOut of plumb 1 4 in. (6.4 mm) in 10 ft (3,048 mm) 3 8 in. (13 mm) in 20 ft (6,096 mm) 1 2 in. (13 mm) max.64
Reinforcement Requirements65
Article 2.7 – FabricationBend diameters for reinforcing steelStandard hooks66
Reinforcement PreparationRemove mud, oil, heavy rust, large amountsof mill scale, or other materials that willadversely affect or reduce the bond.Light rust, mill scale, or a
ASTM C1019: – Compressive strength ASTM C1611: - Slump flow, required, 24 – 30 inches - Visual stability index (VSI), required, 1 - Relative viscosity, T 20 (T 50), voluntary. Verification of SCG Properties. 53 Slump flow. Verification of SCG Properties. 54 Visual Stability Index (VSI) Article 3.1 – Inspection . 55 Foundation tolerance of /- ½” More stringent than ACI 117 .