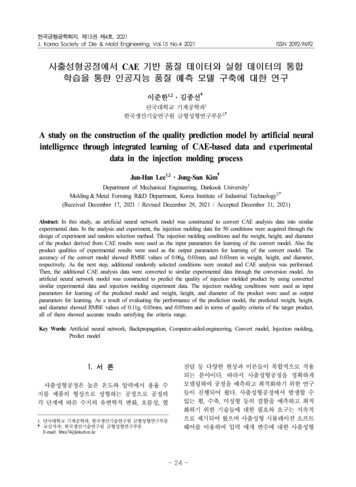
Transcription
, 154 , 2021J. Korea Society of Die & Mold Engineering, Vol.15 No.4 2021ISSN 2092-9692CAE1,212,A study on the construction of the quality prediction model by artificial neuralintelligence through integrated learning of CAE-based data and experimentaldata in the injection molding processJun-Han Lee1,2 Jong-Sun KimDepartment of Mechanical Engineering, Dankook University1Molding & Metal Forming R&D Department, Korea Institute of Industrial Technology2,(Received December 17, 2021 / Revised December 29, 2021 / Accepted December 31, 2021)Abstract: In this study, an artificial neural network model was constructed to convert CAE analysis data into similarexperimental data. In the analysis and experiment, the injection molding data for 50 conditions were acquired through thedesign of experiment and random selection method. The injection molding conditions and the weight, height, and diameterof the product derived from CAE results were used as the input parameters for learning of the convert model. Also theproduct qualities of experimental results were used as the output parameters for learning of the convert model. Theaccuracy of the convert model showed RMSE values of 0.06g, 0.03mm, and 0.03mm in weight, height, and diameter,respectively. As the next step, additional randomly selected conditions were created and CAE analysis was performed.Then, the additional CAE analysis data were converted to similar experimental data through the conversion model. Anartificial neural network model was constructed to predict the quality of injection molded product by using convertedsimilar experimental data and injection molding experiment data. The injection molding conditions were used as inputparameters for learning of the predicted model and weight, height, and diameter of the product were used as outputparameters for learning. As a result of evaluating the performance of the prediction model, the predicted weight, height,and diameter showed RMSE values of 0.11g, 0.03mm, and 0.05mm and in terms of quality criteria of the target product,all of them showed accurate results satisfying the criteria range.Key Words: Artificial neural network, Backpropagation, Computer-aided-engineering, Convert model, Injection molding,Predict model.,1.,,,:E-mail: libra74@kitech.re.kr- 1 -- 24 -,
CAE1-3).,CAE4-6).7,8).,.Fig. 1(polypropylene).LGE150- -DHS,,Fig. 2,LS Mtron,,,(set)Factor.,Fig. 3ValueUnitMaximumMinimumMelt temperature200240Mold temperature4060Injection speed40100mm/sPacking pressure150250barPacking time618secCooling time3858sec.Table 12723.- 2 -- 25 -
CAE5027Fig. 4Autodesk.1340(validation data)10.Moldflow 20195.,(test data).5.(hyper-band)Table 2(hyper-paramter).,,,.,Fig. 5,.,.,,,,Fig. 6,,0.06 g, 0.03 mm, 0.03 mm,,(training data)- 3 -- 26 -RMSE.
- 4 -- 27 -
CAE.FactorValueOptimizerAdamsLearning rate0.003Number of hidden layers1Number of neurons perhidden layer23ActivationElu (1st hidden layer)Linear (output layer)Weight initializerHe normal (1st hidden layer)Glorot normal (output layer)Dropnumber per hidden layer0.0 (1st hiddn layer),,,,.Fig. 7,,,,,.80Epochs987ETCL2 normalizationBatch normalization27.1010.1:150.3.50.50Table 3.5050,50.- 5 -- 28 -100
FactorValueOptimizerAdamsLearning rate0.046Number of hidden layers1Number of neurons perhidden layer16 (1st hidden layer)ActivationElu (1st hidden layer)Linear (output layer)Weight initializerHe normal (1st hidden layer)Glorot normal (output layer)Dropnumber per hidden layer0.0 (1st hiddn layer)Epochs310ETCL2 normalizationBatch normalization.,,.,,,0.12 g, 0.03 mm,.RMSE0.04 mmFig. 8.,5.Figure 8(b), (c), 1.0 %Fig. 8(a)ISO-20457. 0.09 mm.,,.- 6 -- 29 -
CAE.1),,,0.06 g0.03 mm, 0.03 mm,(Project No. KM210153, 20013311).RMSERMSE,.1) Park, K. Y., “CAE Analysis and Optimization ofInjection Molding for a Mobile Phone Cover”, KoreanSoc. Manuf. Process Eng., 11(2), pp. 60-65, 2012.2) Nam, S. D., “A study on the injection mold designapplication method of CAE mold analysis data”, J.D&M Eng., 13(3), pp. 1-6, 2019.3) Sung, S. M. and Jung, S. J., “A study on themotorcycle lear cowl injection molding by CAEanalysis”, J. D&M Eng., 13(4), pp. 34-39, 2019.4) Jong, W. R., Huang, Y. M., Lin, Y. Z., Chen, S.C., Chen, Y. W., “Integrating Taguchi Method andArtificial Neural Network to Explore MachineLearning of Computer Aided Engineering”, J. Chin.Inst. Eng., 43(4), pp. 1-11, 2020.5) Yang, D. C., Lee, J. H., and Kim, J. S., “A Studyon the Prediction of Mass and Length ofInjection-molded Product Using Artificial NeuralNetwork”, Korean Soc. Manuf. Process Eng., 14(3),pp. 1-7, 2020.6) Hwang, S., Han, S. R., and Lee, H., “A Study onthe Improvement of Injection Molding ProcessUsing CAE and Decision-tree“, J. Korea Acad.Ind. cooperation Soc., 22(4), pp. 580-586, 2021.7) Tercan, H., Guajardo, A., Heinisch, J., Thiele, T.,Hopmann, C., and Meisen, T., “Transfer-learning:Bridging the gap between real and simulation datafor machine learning in injection molding“,Procedia Cirp, 72, pp. 185-190. 2018.8) Lee, C., Na, J., Park, K., Yu, H., Kim, J., Choi, K.,Park, D., Park, S., Rho, J., and Lee, S., “Development of Artificial Neural Network Systemto Recommend Process Conditions of InjectionMolding for Various Geometries”, Adv. Intell.Syst., 2(10), 2020.2).,0.12 gmm,3)RMSE0.04 mm0.03RMSE.,RMSE0.11g0.1 %0.05 mm RMSE 0.03 mm, 0.09 mm.,CAE.,.,- 7 -- 30 -
201722017320153:(2005):(:2006 3), ,,- 8 -- 31 -8:():,
Autodesk Moldflow 2019. , ., , . Fig. 5, , , , . (training data) 50 27 13 40. (validation data) 10 5. (test data) 5. (hyper-band) Table 2 (hyper-paramter). . , , . . , , , , Fig. 6, , RMSE 0.06g, 0.03mm, 0.03mm . - 27 - - 4-- 28 - CAE - 5-Factor Value Optimizer Adams Learning rate 0.003 Number of hidden layers 1 Number of neurons per hidden layer 23 Activation Elu (1st hidden layer) Linear .