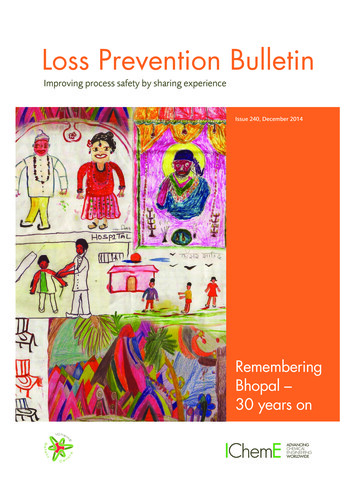
Transcription
Loss Prevention BulletinImproving process safety by sharing experienceIssue 240, December 2014RememberingBhopal –30 years 240.indd 117/11/2014 10:22
Process safetytrainingCourses to help you, your staff and your organisation improve safety,reduce risk and make the working environment safer.HAZOP Study, Leadership andManagement24–26 February 2015, Rugby, UKwww.icheme.org/hazopstudyLayer of Protection Analysis (LOPA)7–8 May 2015, Manchester, UKwww.icheme.org/lopaFundamentals of Process SafetyHAZOP Study for the Offshore Oil andGas Industry13–17 April 2015, Grimsby, UKwww.icheme.org/fps12–15 May 2015, Aberdeen, UKwww.icheme.org/hazopoilManaging the Hazards of FlareDisposal SystemsEstablishing and Maintaining a SafetyCulture27–28 April 2015, Rugby, UKwww.icheme.org/mfd13–14 May 2015, London, UKwww.icheme.org/emscHAZOP AwarenessApplied Hazard and Operability Study30 April 2015, Rugby, UKwww.icheme.org/hazopawareness15–17 June 2015, Manchester, UKwww.icheme.org/appliedhazardVisit www.icheme.org/courses to see our full course IDEprocesssafetyad.indd 117/11/2014 10:41
Loss Prevention Bulletin 240December 2014 1ContentsLoss Prevention Bulletin2Iqbal Essa and David Brownintroduce this specialcommemorative issueArticles and case studiesfrom around the worldIssue 240, November 2014Editor: Tracey DonaldsonPublications Director:Claudia Flavell-WhileSubscriptions: Hannah RourkeCopyright: The Institution of ChemicalEngineers 2014. A Registered Charity inEngland and Wales and a charity registeredin Scotland (SCO39661)ISSN 0260-9576/14The information included in lpb is given ingood faith but without any liability on thepart of IChemEPhotocopyinglpb and the individual articles are protectedby copyright. Users are permitted tomake single photocopies of single articlesfor personal use as allowed by nationalcopyright laws. For all other photocopyingpermission must be obtained and a feepaid. Permissions may be sought directlyfrom the Institution of Chemical Engineers,or users may clear permissions and makepayments through their local ReproductionRights Organisation. In the UK applyto the Copyright Licensing agencyRapid Clearance Service (CLARCS), 90Tottenham Court Road, London, W1P0LP (Phone: 020 7631 5500). In the USAapply to the Copyright Clearance Center(CCC), 222 Rosewood Drive, Danvers, MA01923 (Phone: (978) 7508400, Fax: (978)7504744).Multiple copying of the contents ofthis publication without permission isalways illegal.Institution of Chemical EngineersDavis Building, Railway Terrace,Rugby, Warks, CV21 3HQ, UKTel: 44 (0) 1788 578214Fax: 44 (0) 1788 560833Email: tdonaldson@icheme.orgor journals@icheme.orgwww.icheme.orgPrinted by Lock, Stock & PrintedEditorial – Lessons fromBhopal3Impressions of BhopalFiona Macleod summarises thetheories and aftermath of thetragedy and explains why, thirtyyears on, controversy and divisionremain strong.10 A call for extending theSafety Case approachJudith Hackitt highlights how thesafety case approach, coupled withopen and transparent enforcement,forms a strong basis for successfulprocess safety management.11 Thinking about Bhopal –the role of educationVijaya Varma argues how goodquality science education, availableto all sectors of society, plays avital role in facing future globalchallenges.13 Understanding the impactof unreliable machineryKenneth Bloch and Brianna Jungdescribe how a complex series ofinteracting events – design defects,repeat failures, missed warningsigns – sowed the seeds of thedisaster.17 Land use planning in IndiaAnadita Sengupta discusses thechallenges that India faces indeveloping land use methodsthat are already in place in othercounties.21 Export inherent safety –not riskDavid Edwards warns how risk isincreased when larger plants arebuilt in localities that are less ableto handle the increased hazards,and argues the case for inherentlysafer design.25 A review of UNEPprogrammes on industrialrisk reductionJohanna Suikkanen and JéromeLeroux highlight the UNEPprogrammes that have beenpromoting a participatory and multistakeholder approach to chemicalaccidents and preparedness.29 Site contamination threatremains for BhopalThe Centre for Science &Environment, India, set out theiraction plan for remediation andwaste disposal at the contaminatedUnion Carbide site in Bhopal.30 Are we still doing enoughto reduce hazards atsource?Graeme Ellis explores the reasonswhy inherent safety principleshave not being applied as widely asmight be expected, and introducesnew guidance that might helpovercome this.32 Medical comment on theBhopal tragedyPaul Cullinan summarises, from amedical perspective, what is knownabout the effects of the methylisocyanate gas cloud on the localpopulation.33 A local perspective fromthe Chingari TrustAn interview with MohammedShifon, talking about his treatmentand rehabilitation at the ChingariTrust centre in Bhopal.34 Bhopal literature reviewMark Hailwood and Fiona Macleodreview a range of books and journalpapers covering various aspects ofthe tragedy.With special thanks to the children of theChingari Trust for their illustrations usedon the cover of this issue. Institution of Chemical Engineers0260-9576/14/ 17.63 0.00contentsdec.indd 217/11/2014 11:26
2 Loss Prevention Bulletin 240December 2014EditorialLessons from BhopalThis issue of LPBcommemorates the30th anniversary ofthe world’s worstindustrial accidenton record. The tragicincident happenedat the Union CarbideIndia Limited (UCIL)pesticide productionplant in Bhopal, Indiain the early hours ofthe 3rd December1984.Many of us recall that this incident was caused by theunintended violent reaction between methyl isocyanate andwater, which led to the release of approximately 40 tonnes ofthis highly toxic gas into the atmosphere. This fateful releasecaused thousands of deaths and hundreds of thousands ofinjuries, and an unknown number to suffer continued physicaland psychological conditions. An on-going tragedy is thatmuch of the site of the incident remains contaminated andunremediated to this day.Much has been learned as a result of the terrible accident: Anumber of countries have taken proactive steps in formulatingmore stringent controls on the use of land around hazardousindustries in light of Bhopal. Anandita Sengupta (see page17) explains how the experience in land use planning in theNetherlands could equally be applied to similarly denselypopulated, industrialised areas of India.Johanna Suikkanan outlines on page 25 how internationalorganisations such the United Nations EnvironmentProgramme (UNEP) have been developing policies,programmes and guidance for governments and industry tohelp reduce industrial and chemical accidents worldwide, as aresult of incidents such as Bhopal.If anything good came out of this tragically fateful accident,it is the realisation of the importance of safety by design. Asthe late Professor Trevor Kletz said, “what you don’t have can’tleak” and he urged designers to adopt concepts of inherentlysafer plants by design. Trevor went on to state that it isdevastating that it took such a huge loss of life to shatter thecomplacent reliance on bolt-on safety systems. Inherent safetyis discussed by Graeme Ellis (page 30) and David Edwards(page 21).Thirty years on, it is imperative for industry to developa culture that fosters the installation of well-structuredinherently safer designed processes and plants. Leaders withinthese industries should encourage all, including scientists,engineers, managers and operators, to contribute in all aspectsof their operations without inhibition or recrimination. Focusshould also be given to education and how we train up andcoming chemical engineers in our education establishmentsso that they understand and appreciate the challenges that lieahead of them in industry.Finally, I would like to extend thanks to my Editorial Panelcolleagues, Fiona Macleod and Mark Hailwood, for the leadingroles they have played in enabling this commemorative issue tocome to fruition.M Iqbal EssaChairman, LPB Editorial PanelThirty years on,the Bhopal tragedyshould give everyprocess industryprofessional causefor sober reflection.Our industries havebrought, and will bring,immense benefits tothe world: but thatwhich has potentialfor much good alsohas potential for great harm. It is our responsibilityas chemical engineers to make safety our top priority,in actions and in resources and not just in words; toplace the highest standards of ethics at the core of ourprofessional values; to live those values and to inculcatethem in future generations of engineers. The processindustries are safer, thirty years after Bhopal – but thereis much more to do.David BrownChief executive, IChemE Institution of Chemical Engineers0260-9576/14/ 17.63 0.00editorial.indd 217/11/2014 10:26
Loss Prevention Bulletin 240December 2014 3OverviewImpressions of BhopalFiona MacleodIntroductionI had not realised how beautiful Bhopal is.View of Upper Lake, Bhopal (FM)Sambhavna Clinic Bhopal (FM)When news broke of the Union Carbide accident in India,I had just started my first job as a chemical engineer inScotland. Many years later, I found myself involved with amajor investment program in India along with a team of welleducated, hard-working, ingenious and inventive Indiancolleagues. Despite the common language (English), I wasstruck by the cultural differences and it awoke an intensecuriosity to understand what had really happened in the earlyhours of 03 December 1984 in Bhopal. I read every book thatI could get my hands on1234 and finally visited the capital ofMadhya Pradesh in June 2013.Some Indian friends arranged for me to visit the SambhavnaTrust clinic in Bhopal. Set up in 1995 it provides free treatmentto those who need it most. It is a beautiful, tranquil placefull of green open spaces, a children’s playground, a yogahall, an open garden meeting room. Alongside conventionalmedicine, the plants from the large garden are used incomplementary therapies. There are people who listen andoffer practical support.I made it clear that I worked for a multinational chemicalcompany and that I did not support the campaign againstDow Chemicals. I was made very welcome, and given the fullrun of the library and the assistance of a very knowledgeablearchivist, who helped me to find all the information that I waslooking for.Reading the eyewitness accounts of the accident and theaftermath so close to where it had happened was a harrowingexperience.Afterwards I went to the factory. It is still there.What remains of the Union Carbide India Limited (UCIL)pesticide factory is invisible from the road, lost inside ajungle of greenery. It would be easy to miss it, along with thememorial on Kali Parade. The brutalist modern representationof a grieving mother with her dead infant was being used todry jeans; the squat statue was artistically improved by thedenim decoration.On the wall behind is a colourful mural with a poem:History says, don’t hopeOn this side of the grave.But then, once in a lifetimeThe longed-for tidal waveOf justice can rise up,And hope and history rhyme.Factory complex from Kali Parade (FM) Institution of Chemical Engineers0260-9576/14/ 17.63 0.00impressions.indd 317/11/2014 10:28
4 Loss Prevention Bulletin 240December 2014JumperFlare and Bhopal tragedy memorial (FM)Figure 1– Water washing theoryIt is strange to see only the work of Dutch sculptor RuthWaterman and Irish poet Seamus Heaney here becauseBhopalis know how to do public art. The 1982 Bharat Bhavancomplex above the upper lake in Bhopal celebrates the verbal,visual and performing arts with style and panache. The newtribal museum that opened in June 2013 is simply gorgeous,overflowing with dramatic displays, not just the individualartefacts, but their combination. The concrete memorial onKali Parade stands in particularly stark contrast to the exquisitestone sculptures in the Bhopal state museum, including aterrifying statue of Chamunda wreaking death and havoc, theperfect symbol for the carnage of the night of 02/03 December1984.What really happened to lead up to the world’s worstindustrial accident? Why is there no proper public memorial?Why has the site not been cleaned up? Why do the victims,relatives and neighbours still feel betrayed?is contested on the grounds that there was insufficientpressure of water, there were closed valves in the way, andno water was found in the header when it was drilled atits lowest point two months later. Hydraulics are complexand we have no way of knowing what valves were openedand closed to aid the washing of the filter. In addition ahigh temperature, high pressure runaway in E610 couldhave cleared the header, or water could have escaped fromleaking flanges (several were reported).The accidentIn the early morning of 03 December 1984, a gas cloud wasreleased from the Union Carbide pesticide factory in Bhopal.Within a few hours, thousands of people were dead andhundreds of thousands were injured.The causeMost people agree that the release of toxic gases was causedby a runaway reaction in a tank E610 containing about 40tonnes of methyl isocyanate after it came into contact withabout one tonne of water. There are at least four competingtheories as to how this happened.The sabotage theoryDeliberate entry of water by a disgruntled employeeconnecting a water hose directly to the tank E610 on 02December.The sabotage theory was proposed in the Arthur D.Little (ADL)6 report commissioned by Union Carbide.The evidence is circumstantial (disgruntled employees, amissing pressure gauge, a water hose left running, evidenceof altered log sheets and general commotion during a teabreak) and is hotly contested by all those on shift at thetime. It used to be common practice to blame individualworkers for accidents but more sophisticated understandingof process safety, layers of protection and human factorshas thankfully reduced this practice. In 1985 this was thecompany defence – that no safety system can ever bedesigned to protect against deliberate malicious acts.Flare and VGSPICThe water washing theoryAccidental entry of water through a common vent line duringa filter washing operation over a hundred metres away on 02December.The water washing theory is the accepted explanation inthe official Council of Scientific and Industrial Research (CSIR)report.5 During the routine cleaning of a filter, no physicalbarrier (spade) was inserted contrary to correct procedureand attributable to the cut backs in maintenance staff on shift.Water found its way back though a common header andtravelled up 7m and along 150 metres to E610. This ionFILTERPIE610DrainFigure 2 – Sabotage theory Institution of Chemical Engineers0260-9576/14/ 17.63 0.00impressions.indd 417/11/2014 10:28
Loss Prevention Bulletin 240JumperFlare and nnectionPIPITIFILTERPIThe decomposition theoryGradual entry of water and other contaminants over manyweeks prior to 02 December.Although extensive trial work was done (based on residuesin E610), it is impossible to know the exact composition ofthe tank contents before the accident, or what happenedto it between October (when the last MIC was added) andDecember (when the runaway reaction occurred). It is knownthat the composition in E610 was unusual; it contained highlevels of chloroform due to distillation to a higher temperaturewhen shutting down and emptying the MIC plant. If E610 wasnot pressurised with nitrogen it is possible that water or causticfrom the scrubber, along with other contaminants, could haveentered the tank over the six week period when it sat full andunused. While the chemists were able to replicate the residuefound in E610 by adding a single slug of water to a sample ofMIC and chloroform, it does not prove that there were no otherpossible ways to arrive at the same residue.The nitrogen mix up theoryMix up of hose connections leading to accidental entry of waterinstead of nitrogen on or prior to 02 December.There is some evidence that repeated attempts to transfertank E610 had failed because it was not holding pressure.There was chloroform found in the SEVIN feed tank suggestingthat some material had been transferred from E610. CouldNitrogena worker have tried to connect nitrogen directly to the tankand inadvertently connected water instead? This theory wasdiscounted on the basis that “The water lines are blue, nitrogenlines grey and air lines white They are also labelled. And thenitrogen and water lines have nozzles of different sizes.”7 It isworth noting, however, that despite clear labelling and colourcoding and nozzle differences, the Automobile Association(AA) estimate that 150,000 drivers put the wrong fuel in theircar every year in Britain alone.It is now too late to be sure how the accident happened or toknow the exact composition of the gases released.What we do know is that, whatever the cause, had themultiple safety systems been working as designed, then thecatastrophe could have been avoided altogether, or had muchless severe consequences, i.e.:E610Figure 3 – Decomposition theoryFlare and VGSDecember 2014 5 If the tank had been filled to less than 50% full (as designed)instead of over 80% there would have been less material torelease. If the caustic scrubber had been connected and workingcontinuously, it would have lessened the severity of therelease. If the refrigeration system had been working along withreliable temperature gauges, there might have been time foroperators to react and prevent the release altogether. If the flare had been connected and lit, it could havesignificantly reduced or possibly prevented theconsequences of the event.Also, an emergency water spray could not reach the height ofthe vent stack, having been designed to alleviate the effects of aground level spill rather than a high level release.It is generally accepted that the plant and safety systemswere allowed to fall into disrepair while the plant was losingmoney and closing down. There were a series of cost savinginitiatives culminating in the 1983 Operation ImprovementProgram, which imposed savage cuts in staffing, maintenanceand training. The local factory management underestimatedthe risk of the stored chemicals after the MIC production unitclosed down.Vent gas scrubberLeaking gas could have been detoxified,but the scrubber was turned offWater curtainNot high enoughto reach gasPICNitrogenhoseconnectionVGSFlare towerDesigned to burn off gas, buta connecting pipe had beenremoved for maintenanceWaterhoseconnectionPIPITIFILTERFigure 4 – Nitrogen mix up theoryE610PIMIC storage tanks40 tons in E610, 15 tons in E611,E619 was empty. Water leakedinto E610 causing runaway heatproducing reactionFigure 5 from www.bhopal.orgRefrigeration systemFreon system to cool liquid MICwas shut down in June 1984 tosave money and Freon shippedto other plants Institution of Chemical Engineers0260-9576/14/ 17.63 0.00impressions.indd 517/11/2014 10:28
6 Loss Prevention Bulletin 240December 2014Several warnings went unheeded: The union safety concerns were not addressed and theunion leaders who raised them were fired. A local journalist, Raj Keswani, repeatedly drew attention tosafety issues at the site but was ignored. UCC (the parent company) carried out a safety audit in1982 but did not follow up on the recommendations.The number of dead and injured increased because: There was no offsite alarm or emergency plan; The public and emergency services were not aware of thehazards or safest response; The factory was sited close to the old town and to bus andrailway hubs; Slum dwellings had also grown up around the factory onland zoned as industrial.It is particularly painful to realise that a wet cloth over mouthand nose might have been enough to save many lives if theyhad also known to stay indoors or to flee across instead ofdown-wind.There are known facts and competing theories, but inthe absence of a thorough independent investigation, withforensic preservation of evidence at the time and detailedinterviews immediately afterwards, it is impossible to be surewhat caused the accident.The aftermathAfter the accident, the inadequate response in support ofthose affected was shocking. There were people in desperateneed and there was a rich US corporation willing and able tofinance some alleviation of their suffering, but it somehowseems to have all got tangled up in a mess of endless courtproceedings.Others have documented the years of legal wrangles butamong them were two key events in 1989 and 2010.In 1989, almost five years after the accident, an out ofcourt settlement of US 470 million was reached betweenthe Government of India (acting on behalf of the victims) andUnion Carbide Corporation (UCC). There are several problemswith the settlement: It underestimated the number killed. It underestimated the number and severity of the injuries. It ignored the fact that chronic ill health prevented someEmergency sign in 2014 (Julia Green www.bhopal.org) from ever returning to work.It failed to value the contribution of “non-working” women,children and the elderly within a family unit.It ignored mental health injuries.It ignored the loss of livelihood for the former workers andthe network of small businesses dependent on the factory.It ignored inflation.Compensation was meagre even by Indian standards*Distribution made no allowance for the fact that the worstaffected groups were poor and ill-educated, and living at themargins of society.The standard of evidence demanded to support claimsof death or injury caused by the release meant that muchof the compensation money went on medical, legal andloan interest costs. Those providing such services were ofvariable quality and took a disproportionate amount of themoney that should have gone to victims and their families.Distribution was slow – in 2004, twenty years after theaccident, claims were still being settled.Interim relief was deducted from the final settlement.No provision was made for the clean-up of the site.As a condition of the settlement, all criminal charges weresuspended (this was later overturned).In 2010, over twenty five years later, eight former executivesof Union Carbide India Limited (UCIL) – including one who hadalready died – were convicted of causing death by negligence.The seven surviving defendants were sentenced to two years inprison (the maximum allowed by law) and fined 100,000 rupees,or 2,100. They were given leave to appeal and immediatelyreleased on bail.Worlds apartWhat happened on the night of 02 December 1984 was anunspeakable, terrible tragedy, and the suffering of those whodied, were physically injured or mentally traumatised cannot beoverstated.And yet it is still very difficult to write about the Bhopalaccident dispassionately without offending or upsettingsomeone, not least because there was so much suffering andthen such polarised opinion, suspicion and hatred.There are those who believe that Union Carbide in Americadeliberately allowed an unsafe process to operate in adeveloping country and that their Chairman, Warren Anderson,personally approved this and was ultimately responsible foreverything that happened.On the other extreme there are those convinced that theprocess was fundamentally safe but that a single act of sabotageby a disgruntled worker caused the accident. The genuineconcern shown by UCC senior executives in rushing to the*Compensation was 100,000 rupees (US 3,000 at 30Rs/ ) for eachcertified death and 30,000 rupees (US 1,000) for proven injury or otherloss (livestock etc.), the equivalent of about 5 years’ wages for a death(assuming an average annual wage of 20,000 Rs). In the annual UCILaccounts for 1984 the lowest paid full time worker cost the company32,000 Rs/year and the highest 80,000 Rs/year. The family of the workerAshraf Mohammed Khan who died after an accident at the factory in 1982was offered 72,000 Rs in compensation. The family were still contestingthis when his three year old son Arshad died in the 1984 accident. Institution of Chemical Engineers0260-9576/14/ 17.63 0.00impressions.indd 617/11/2014 10:28
Loss Prevention Bulletin 240scene of the accident was met by a lynch mob mentality andthings went downhill from there.Whatever the cause, the operating company was responsiblefor ensuring that design, safety systems and communityemergency response contained the consequences of anyaccident to within the site.There are those who believe that, after the accident, UnionCarbide withheld information that could have assisted indetermining the treatment of victims, that they forced theIndian government to halt programs providing effective reliefbecause it might implicate them further and conspired with thegovernment of India to distort the data.On the other side, there are those who believe that most ofthe ongoing chronic illnesses, birth defects, disabilities andgeneral poor health of the population is due to socioeconomicfactors and no different from any other city slum population.No one knows the exact composition of the gas released thatnight. There is independent evidence of different effects atdifferent distances from the source of the release, suggestinga complex composition. There is no doubt that there washorrific physical suffering and mental trauma in the surroundingpopulation. Help should have been and should continue to beprovided unstintingly.There are those who believe that the 2007 initiative by theTata group to organise a “no blame” remediation of the Bhopalsite was part of a conspiracy to allow foreign entities to escapeany on-going responsibility** and that the only way to preventa future Bhopal is for justice to be done, and seen to be done.However, as a result of the political and legal impasse, the oldUnion Carbide site in Bhopal remains rusting and leaking, thirtyyears on.December 2014 7The MIC Storage tanks E610, 611 and 619 in 2014(Julia Green www.bhopal.org)MIC Unit in 2014 (Julia Green www.bhopal.org)MultinationalsChemical executives do not spend time stroking white catsand planning ways to poison the planet. The industry is fullof intelligent, honourable people whose efforts have helpedmake the world a better, cleaner place for its ever increasingpopulations, lifting people out of poverty, providing clean water,improving communication, reducing hunger, preventing andcuring disease.Companies fund innovation and growth by promising a returnto their shareholders. The requirement to maximise shareholdervalue puts increasing pressure on the cost of manufacturing.Together with changing demographics and growing aspirationsthis means manufacturing in developing countries, largelybecause that is where the new customers are.The people who rise to the top of large chemical companiesare those who set and meet the most challenging targets. Feware engineers and even fewer have direct experience of therealities of manufacturing. It is not enough to add lagging safetyand environmental measures to the financial targets of thesetop executives; major accidents are thankfully too rare to bea meaningful measure. There is an increasing danger that theSevin Unit in 2014 (Julia Green www.bhopal.org)** In 1986 UCC sold its pesticide division to Rhone Poulenc, acquiredby Bayer in 2002. In 1994 the UCC shares in UCIL were sold to McLeodRussel (India) which merged with Eveready Industries India and theproceeds used to found the Bhopal Memorial Hospital. In 1998, EvereadyIndustries surrendered the lease on the Bhopal factory site to the stategovernment of Madhya Pradesh. In 2001 Dow Chemical acquired theremains of UCC.MIC Unit in 2014 (Julia Green www.bhopal.org) Institution of Chemical Engineers0260-9576/14/ 17.63 0.00impressions.indd 717/11/2014 10:28
8 Loss Prevention Bulletin 240December 2014Jugaad (frugal innovation) is a concept that should never beapplied to high hazard chemical plants, or bandied around inthe boardrooms of the companies that run them.A personal journeyControl Room Feb 2014 (Credit BMA)Laboratory Feb 2014 (Credit BMA)lessons of the past will be forgotten. And accidents repeated.JugaadJugaad (pronounced “Joo-gaard”) is a Hindi word for a quick fix,a creative way of solving a problem, an improvised arrangementused because of lack of resource, a cost-effective way to solvethe issues of everyday life. It is commonly used when describingan innovative workaround to get through commercial, logistical,or legal issues. There are many great examples of frugalinnovation where good engineering matches product design tothe needs of the market: better, cheaper, faster.Anyone who has spent time in India cannot fail to come awayimpressed by the ingenuity and pragmatism, the local ability todo things fast and cheap. But not always well. And not alwayslegally. The theft of electricity by tapping into overhead cablesis a prime example of Jugaad.It is our job as engineers to ensure that risks are quantifiedand understood. Locally made motor vehicles, a diesel enginelashed onto a wooden cart, may provide low-cost transportationin rural India, but it comes at a price: no crumple zone, no seatbelts, no child restraints, no air bags, no anti-skid or pedestrianprotection. WHO Global Status Report on Road Safety revealsthe staggering number of deaths due to road accidents whenpedestrians are hit by unregistered vehicles.In the Union Carbide plant in Bhopal, the pumps that weredesigned to transfer methyl isocyanate proved unreliable.A work-around was found that used nitrogen pressure fortransfers. In order to do this the nitrogen was diverted fromthe vents. More than one possible contributing cause of thecatastrophe is directly related to this work-around8.I still re
hours of 03 December 1984 in Bhopal. I read every book that I could get my hands on1234 and finally visited the capital of Madhya Pradesh in June 2013. Some Indian friends arranged for me to visit the Sambhavna Trust clinic in Bhopal. Set up in 1995 it provides free treatment to those who need it most. It is a beautiful, tranquil place