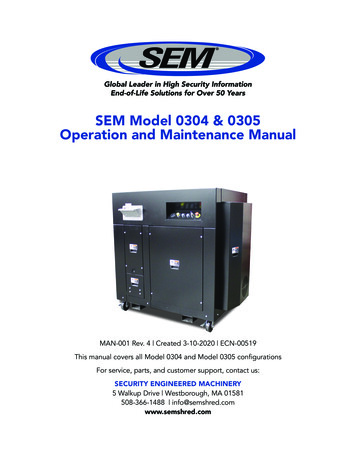
Transcription
SEM Model 0304 & 0305Operation and Maintenance ManualMAN-001 Rev. 4 Created 3-10-2020 ECN-00519This manual covers all Model 0304 and Model 0305 configurationsFor service, parts, and customer support, contact us:SECURITY ENGINEERED MACHINERY5 Walkup Drive Westborough, MA 01581508-366-1488 info@semshred.comwww.semshred.com
Model 0305 & 0304 Operation and Maintenance ManualContentsDisclaimers. 2Safety. 3About Your Shredder - 0304. 4Overview and Intended Use. 4Shredder Configuration. 4About Your Shredder - 0305. 5Overview and Intended Use. 5Shredder Configuration. 5Acceptable Media – HDD Combo Chute. 6Acceptable Media – SSD Combo Chute. 6Unacceptable Media. 6Unpacking and Installation . 7Uncrating. 7General Installation . 8Conveyor Shroud Installation. 9Assembling Dust Cover. 9Electrical . 11Installation. 11Voltage Specifications.12Operation . 13Standard and CE Control Scheme - 0304/0305. 13Pre-Start Up. 13Start Up Procedure and Operation . 14Shut-Down Procedure. 15Maintenance. 16Maintenance Tools and PPE. 16Maintenance Schedule. 16Air Filtration System . 18Current Relay Adjustment. 21Cutting Head Adjustment . 22Maintenance Diagrams. 23General Layout - 0305. 23General Layout - 0304. 24Drive System. 25Extra Options and Spare Parts. 26SEM www.semshred.com1
Model 0305 & 0304 Operation and Maintenance ManualDisclaimersEvery care has been taken by the staff of SEM in compilation of the data contained inall training and informational materials (“collateral”) and in verification of its accuracywhen published; however, the content of this collateral is subject to change withoutnotice due to factors outside the control of SEM and this collateral should thereforebe used as a guide only. The products referred to in these publications are continuallyimproved through further research and development, which may lead to the alterationof information contained in this collateral. SEM does not accept any responsibilitywhatsoever for misrepresentation by any person of the information contained inthis collateral and expressly disclaims any and all liability and responsibility to anyperson, whether a reader/viewer of this collateral or not, with respect to claims,losses, damage, or any other matter, either direct or consequential, arising out of or inrelation to the use and reliance upon any information contained or products referredto in this collateral. SEM does not warrant that the equipment will work properly inall environments and applications, and makes no warranty or representation, eitherimplied or expressed, with respect to the performance, throughput, or maintenancerequirements of the machine. Performance, throughput, and maintenance requirementsvary depending on screen size, feed rate, and media type as well as operationalprocedures. Information in this collateral is subject to change without notice and doesnot represent a commitment on the part of SEM. SEM assumes no responsibility for anyinaccuracies that may be contained in this collateral or any omissions that may haveoccurred. SEM makes no commitment to update or keep current the information in thiscollateral and reserves the right to make improvements to this collateral and/or to theproducts described therein at any time without notice.Proprietary Information: This document contains proprietary and confidentialinformation of SEM, and shall not be used, disclosed or reproduced, in whole or inpart, for any purpose, without the prior written consent of SEM. Title in and to thisdocument and all information contained herein remains at all times in SEM. Thisinformation is exempted from disclosure under FOIA, as amended.The combo SSD chute and SSD units intended for the destruction of solid statemedia only. Attempting to shred rotational drives in the SSD chute could causecatastrophic damage to the unit and will void warranty.2SEM www.semshred.com
Model 0305 & 0304 Operation and Maintenance ManualSafetyRead and understand instruction manual and be aware of all warning stickers.Always follow proper PPE and lock out tag out procedures (LOTO).Make sure that all guards and access panels are in place at all times, EXCEPT when thepower is locked off for maintenance work or cleaning.Always know where emergency stop buttons are located.Always know or have quick access to emergency phone numbers.Always ensure that all maintenance and operating personnel read and understand thismanual, including those personnel working second or third shift.Always have a standard break-in time for a new operator. A minimum of two hours issuggested.Always wear safety glasses when operating shredder.Always lock-out power at the disconnect when shredder is not in use, when servicingshredder, or when performing routine shredder maintenance. This includes cleaning.Never operate this or any other machine while under the influence of drugs, alcohol,or medications.Never wear loose fitting clothing, ties, or jewelry while in the vicinity of this shredder.Never allow long hair to be in the vicinity of the machine without use of a protectivehair net.Never place any part of your body in or on any part of the machine while in operation.Never allow other personnel within ten feet of this machine while in operation.Never remove guards, perform maintenance, or clear jam up debris without firstlocking out power disconnect.Never allow horse play around machine.Never bypass or interfere with any safety limit switches or guards. They are safetydevices and serious injury can result if bypassed.Never allow minors to operate the machine.SEM www.semshred.com3
Model 0305 & 0304 Operation and Maintenance ManualAbout Your Shredder0304For information about other cutting head configurations and features, such as widerfeed chutes, 11” X 2.5” (option to 19.25”W), contact SEM customer care.The maintenance and operation information in this manual is also applicable to theModel 0301 and 0302. Contact SEM Customer Care for electrical information or detailsabout these devices.Overview and Intended UseThe SEM Model 0304 HDD/SSD Shredder employs a 20 horsepower motor to destroy up to 3,000 rotational or solid state hard drives or up to 3,500 e-media devices(phones, RAM, etc.) per hour depending on the cutting head configuration chosenat purchase. This unit is also capable of destroying enterprise drives at a rate of upto 800 per hour, and up to 1,400 enterprise SSDs per hour. Solid state media can bedestroyed with a combo HDD chute but SEM recommends using the combo SSD chutefor higher security destruction.Size and Weight: When fully assembled, the SEM Model 0304 is approximately 67”(170.18cm) tall by 65” (165.1cm) wide and 114” (289.56cm) deep. It weighs approximately 4,700 lbs (2,100 kg).Note: The images shown in this manual may appear slightly different due to the ageof your machine and the features ordered with it. All functionality and locations remain the same or very similar to your machine. Contact SEM customer service with anyquestions. Some iimages may show optional features that must be ordered at time ofpurchase.Shredder ConfigurationThe SEM Model 0304 is designed to shred standard rotational hard drives, solid statedrives, tapes and various electronic media depending on the cutting head configuration chosen at the time of purchase. Hard drive shreds at 1.5” or 0.75” shred widths.This can also shred SSDs but not to secure particle sizes.HDD/SSD combo units have two cutting heads allowing destruction of both types ofmedia. HDD can be shredded to 38mm/1.5”, while SSD can be shredded to 0.375”.4SEM www.semshred.com
Model 0305 & 0304 Operation and Maintenance ManualAbout Your Shredder0305For information about other cutting head configurations and features, such as widerfeed chutes or .375 SSD shred widths contact SEM customer care.The maintenance and operation information in this manual is also applicable to theModel 0301 and 0302. Contact SEM Customer Care for electrical information or detailsabout these devices.Overview and Intended UseThe SEM Model 0305 HDD/SSD Shredder employs a 10 horsepower motor to destroy up to 3,000 rotational or solid state hard drives or up to 3,500 e-media devices(phones, RAM, etc.) per hour depending on the cutting head configuration chosenat purchase. This unit is also capable of destroying enterprise drives at a rate of upto 800 per hour, and up to 1,200 enterprise SSDs per hour. Solid state media can bedestroyed with a combo HDD chute but SEM recommends using the combo SSD chutefor higher security destruction.Size and Weight: When fully assembled, the SEM Model 0305 is approximately 66”(167.64 cm) tall by 58” (147.32 cm) wide and 89” (226.06 cm) deep. It weighs approximately 2,800 pounds (1270 kg).Note: The images shown in this manual may appear slightly different due to the ageof your machine and the features ordered with it. All functionality and locations remain the same or very similar to your machine. Contact SEM customer service with anyquestions. Some images may show optional features that must be ordered at time ofpurchase.Shredder ConfigurationThe SEM Model 0305 is designed to shred standard rotational hard drives, solidstate drives, tapes and various electronic media depending on the cutting headconfiguration chosen at the time of purchase. Hard drive shreds at 1.5”shred widths.This can also shred SSDs but not to secure particle sizes.HDD/SSD combo units have two cutting heads allowing destruction of both types ofmedia. HDD can be shredded to 1.5”, while SSD can be shredded to 0.375”.SEM www.semshred.com5
Model 0305 & 0304 Operation and Maintenance ManualAcceptable MediaHDD Combo ChuteThe following media is acceptable to be destroyed with combo HDD chute: Rotational Hard Drive Enterprise Hard Drive TapesSSD Combo ChuteThe following media is acceptable to be destroyed with an combo SSD chute: Solid State Drives Enterprise SSDsDo not shred rotational hard drives using the combo SSD chute as damage to themachine may occur and your warranty will be voided.Unacceptable MediaThe following materials should never be destroyed used a SEM Model 0305 shredder. Batteries Capacitators LCDsBatteries and capacitors should never be destroyed using this machine. Both can befound inside of cell phones, tablets, etc. They must be removed from all devices beforeshredding. Destruction of batteries could lead to safety hazards and cause damage tothe machine. All batteries must be removed from cell phones, PDAs, tablets, etc. priorto destruction.6SEM www.semshred.com
Model 0305 & 0304 Operation and Maintenance ManualUnpacking and InstallationYour new SEM shredder has been secured to a pallet for shipping. Please inspectequipment immediately for shipping damage. Note any damage to the packaging or unit on the bill of lading and contact SEMcustomer service. Retain packaging for 90 days. Using a lift truck with a minimum capacity of 4,000 lbs. Remove the machine fromthe carrier and transport to operation site. Remove pallet and discard responsiblyafter 90 days. SEM shredders are equipped with swivel casters for ease of handling. Inspect the machine for any damages prior to installation and operation. Check theoil level and check for any oil leaks. After inspection, make certain that all guards and safety devices are installedproperly. If purchased, make sure to install the conveyor shroud and gaylord dust coverbefore operation. Consumables are also included within shipments.Uncrating Fork lift with 4,000 or 6,000 lb. capacity, see above. Pry bar Strap cutters Hammer, drill #2 Phillips, T20, T25 Bits, 9/16”socket wrenchUnpacking: Remove front and top of crate with drill and appropriate bits marked withspraypaint. Cut straps holding the unit with strap cutters. Remove bolts holding brackets at the base of the unit in the front and back.Remove boards in front and on top of the unit. Remove the unit from the pallet and bring as close to installation point as possiblewith fork lift truck.SEM www.semshred.com7
Model 0305 & 0304 Operation and Maintenance ManualGeneral InstallationThis machine may be installed in an office or warehouse setting within six feet of anappropriate electrical receptacle.Note: The unit’s weight is mostly on the left side. Use care when moving and stay clearif it begins to tip.Note: It is recommended to move the unit as close to the installation area as possibleusing a fork lift, particularly if it requires traversing uneven surfaces.Storage: If unit requires storage, it can be stored in its shipping crate or unpackaged. Ifunpackaged, ensure that all caster locks are engaged.To transport, unlock all caster locks and then push on a flat surface. Do not push thisunit on inclined or declined surfaces as control of the unit may be lost and damage tothe machine or injury to personnel may occur.Install the output conveyor if notinstalled. Requires metal shears,one 1-1/8” open wrench oradjustable wrench, 9/16” socketwrench, and 1/2” wrench. With the assistance of anoverhead crane or a forklift, theconveyor can be hoisted intoposition. Use a sling to lift theconveyor assembly into place,then, using the bolts suppliedat rear of machine, attachconveyor and tighten bolts.Removehardwarefrom end ofconveyor.Reinstall boltswhere theywere removed(both sides). Install conveyor belt arounddrive pulley (under cuttinghead) and pull belt along bellypan and top plate. A secondperson may be necessary to bring both ends together. When both ends are puttogether, take extra care to align the lacing. When aligned properly, put connectingpin (supplied) through the lacing. Clip off any excess pin which may be hanging out. Tighten belt snug. Belt must be tight enough so that it cannot be stopped by ahand.8SEM www.semshred.com
Model 0305 & 0304 Operation and Maintenance ManualConveyor Shroud InstallationInstall conveyor shroud if not installed. It is recommended that two people dothis and requires 1/2” wrench, 1/2” socket, and 1-1/8” wrench. This section onlyapplies to units purchased with the optional conveyor shroud. Remove hardware from the end of the conveyor.Loosen the nut holding the conveyor’s bearing covers and remove the covers. Have second person hold the shroud in place at the end of the conveyor and installthe bolts into the holes from which they were removed. Ensure conveyor shroud side covers are on the outside. Tighten bolts and reinstall conveyor bearing covers. With the assistance of an overhead crane or a forklift, the conveyor can be hoistedinto position. Use a sling to lift the conveyor assembly into place, then, using the sixbolts supplied at rear of machine, attach conveyor and tighten bolts. Install conveyor belt around drive pulley (under cutting head) and pull belt alongbelly pan and top plate. A second person may be necessary to bring both endstogether. When both ends are put together, take extra care to align the lacing.When aligned properly, put connecting pin (supplied) through the lacing. Clip offany excess pin which may be hanging out.Assembling Dust CoverThis section only applies to units purchased with the optional dust cover. Open the box (not included) and unfold. Fold open the walls inside the base. May help to place a piece of wood inside to hold the shape. (Fig. 1) Staple or otherwise secure the walls to the base. Slide the opening in the middle of the cover around the conveyor shroud andtighten the cord. (Fig. 2) Slide the rest of the cover over the box. (Fig. 3) Guide the belt through the loops and tighten snugly. (Fig. 4, 5)SEM www.semshred.com9
Model 0305 & 0304 Operation and Maintenance ManualFigure 1Figure 2Figure 3Figure 4Figure 510SEM www.semshred.com
Model 0305 & 0304 Operation and Maintenance ManualElectricalInstallationNOTE: All electrical MUST be completed by a licensed electrician. Be sure to follow proper “Lock Out Tag Out” (LOTO) procedures. A schematic can be found in both the electrical panel and debris drawer. Availablein PDF on request. All units work on 3-phase AC power. All electrical installation must be done by a qualified electrician. Follow all nationaland local electrical codes and ordinances. All internal wiring has been factory installed and tested prior to shipping. Electricalinstallation consists of providing adequate machine power only. Check building service to ensure correct voltage is available and that the electricalcurrent requirements can be met. Ensure area is clear. Turn the key switch on and turn E-STOP clockwise, ensuring it’snot engaged. Check for proper motor rotation. The conveyor belt should run awayfrom the operator if the forward button is pressed. Motor rotation is dependent onhow customer’s electrical panel is wired. If rotation is wrong, a licensed electriciancan correct it. Electrical installation is complete. Replace all guards and safety devices. Notes: SEM recommends a less than 3% voltage drop on the receptacle/disconnectfor optimal performance while under load. Run a few drives and adjust current relay as needed. See section 4.6 for informationregarding adjusting current relay. Recommend using a licensed electrician.SEM www.semshred.com11
Model 0305 & 0304 Operation and Maintenance ManualVoltage Specifications0305Voltage /FrequencyFull Load Amps (FLA)[FLA with Air System]RecommendedDisconnectApparent Power(Line to Line) kVA208V/60Hz31 [36]50 Amp11.2 [13]230V/60Hz28 [33]50 Amp11.2 [13.1]380V/50Hz18.1 [20.4]30 Amp11.9 [13.4]400-415V/50Hz 18 [20.3]30 Amp12.7 [14.3]460V/60Hz30 Amp11.2 [12.8]14 [16.1]0304Voltage /FrequencyFull Load Amps (FLA)[FLA with Air System]RecommendedDisconnectApparentPower (Lineto Line) kVA208V/60Hz52.4 [55.8]75 Amp11.2 [13]230V/60Hz48.4 [51.6]75 Amp11.2 [13.1]460V/60Hz24.2 [25.8]50 Amp11.9 [13.4]380,400-415V/50Hz 27.5 [29.2]50 Amp12.7 [14.3]12SEM www.semshred.com
Model 0305 & 0304 Operation and Maintenance ManualOperationStandard and CE Control SchemeDepending on model, buttons may be in slightly different positions.Emergency Stop: Immediately turns off power to the machine. Machine cannot turnon until disengaged. Twist to disengage.Shredder Forward: Starts the machine.Shredder Reverse: Makes the cutters rotate backwards to unjam the machine or helpin cleaning waste from cutting head. Must be held down to run in reverse. Machinemust be stopped before reversing.Key Switch: Turns power to the machine on or off.Shredder Stop: Stops the machine. Press the stop button anytime to stop themachine.Hour Meter: Shows number of hours machine has operated.Pre-Start Up Familiarize yourself with all controls and button locations. Ensure that all guards and covers are in place. A certified SEM service technician is available over the phone or on site for startupinstruction and training. Contact SEM customer service for details and have yourserial number available: service@semshred.com.SEM www.semshred.com13
Model 0305 & 0304 Operation and Maintenance ManualStart Up Procedure and OperationPPE: SEM recommends wearing safety glasses, mask, and gloves while operating thismachine. However, each site should determine its own PPE.Turn the KEY SWITCH on and disengage the E-STOP, then press the SHREDDERFORWARD BUTTON. The cutters will begin to rotate towards each other and theoutput conveyor will begin to run forward, away from the operator.In Case of Emergency: The E-STOP button or turn the KEY SWITCH.Feeding: Begin feeding material into the appropriate feed chute. Feed drives one at atime.Chute Blocker: If this unit is equipped with a chute blocker, be sure that it is coveringthe correct chute. To change chutes, lift the knob and slide it towards the chute that isnot in use.Reminder: DO NOT SHRED ROTATIONAL HARD DRIVES USING THE SSD CHUTE.New Operators: New operators should be given a minimum 2-3 hour equipmenttraining time, beginning with a slow feed rate, approximately one drive every 10-15seconds. The operator will soon be able to judge how quickly the shredder can be fed.Debris Drawer Lock (Optional): The debris drawer is equipped with a lock and bluekey if CE or specified at purchase. Turn the key before opening the drawer. Do notattempt to force the drawer open or open drawer while unit is running.Important/Warning: The debris drawer is attached to keep excess material from collecting on floor. Drawer must be emptied frequently (approx. every 100 drives) or damage to the belt and unit may occur. Debris drawer should be emptied at the beginningand end of each operator’s shift regardless of the number of drives shredded.14SEM www.semshred.com
Model 0305 & 0304 Operation and Maintenance ManualClearing a Jam In the event of a jam, ensure that all personnel are clear of both the input chute andthe cutting head. Hold the SHREDDER REVERSE button for 5-7 seconds. This will cause the cuttersto run backwards for as long as the reverse button remains pressed. Release the reverse button. The machine will come to a stop. After the machine hascompletely stopped, press the forward button and try to shred material. If machine jams again, reverse shredder, LOCK OUT POWER, and manually removethe jammed material. Restart machine in the forward direction to resume operation.Warning: NEVER hold the forward button as damage to the machine and the electrical system may occur.Shut-Down Procedure Allow input chute and output conveyor to clear all material before shutting down.Wait approximately 30 seconds. Press the Shredder Stop button. Turn Key Switch to off position and activateE-STOP. Turn off the disconnect switch.Begin daily cleaning. See section 4.2 for maintenance schedule.SEM www.semshred.com15
Model 0305 & 0304 Operation and Maintenance ManualMaintenanceMaintenance Tools and PPE Safety glasses and cut resistant gloves Pliers One 1-1/8” wrench or one adjustable wrench WD-40 7/16” and two 1/2” wrench or socket wrench Cleaning solution and rag Phillips head and flathead screwdriver 1-1/8” crowfoot wrenchBeam torque wrench 0-80in/lbrange Grease gun with standard fitting Adapters- 1/4” to 3/8”. and3/8” to 1/2”Maintenance ScheduleDaily: Empty debris drawer (every 100 drives and before and after every shift). Wipe down machine with cleaning solution. Rake waste in gaylord to prevent pyramiding.Every 15-20 Hours: Open the conveyor rear access panel and clean debris from the cutters and inspectair inlet. Remove any magnetic buildup over the air inlet. Grease main bearings, wear plates. There are eight grease fittings, four on eachside of conveyor. Add 4 pumps of grease into each fitting. Warning: do not overpump. Apply light machine oil to cutters. Check belt tension. If slipping or loose, tighten. Replace prefilter.Every 30-40 Hours: Apply oil to conveyor drive chains. Check oil level of spur gears. Clean HEPA filter (see air filtration section). Replace prefilter quarterly or as needed.16SEM www.semshred.com
Model 0305 & 0304 Operation and Maintenance ManualLube ScheduleITEMFREQUENCYTYPECuttersEvery 15-20 hoursLight machine oilMain bearings, WearPlates, Output ConveyorPulley BearingsEvery 15-20 hoursMulti-purpose grease(4 pumps per bearing)ChainEvery 30-40 hoursChain and cable lubeConveyor Belt AdjustmentSetting TensionTools Required: 1-1/8” wrench or adjustable wrench, beam torque wrench (0-80 in./lb.), drive adapters, and 1-1/8” crowfoot wrench. Be sure to check belt tension every 20 hours. Belts stretch after break in period. Read all safety warnings before proceeding. De-energize the unit using proper LOTO procedures. Loosen bearing cover nut and remove bearing cover. Loosen jam nuts on each side of machine (see figure below). Leave 1/2” gapbetween jam nut and adjustment bracket. Use beam torque wrench, adapters, and 1-1/8” crowfoot wrench to tightenadjustment nuts to ensure torque range is between 40-50 in./lb. Ensure all personnel are clear and that no tools are on machine belt, or input chute.Adjustmenttop nutSEM www.semshred.comJam NutBearing CoverNut17
Model 0305 & 0304 Operation and Maintenance Manual Turn machine on and run machine in forward for five minutes. Stop machine and turn power off. Draw a mark on each adjustment nut with asharpie to track changes made in next step. Make all adjustments in small increments. By design, the conveyor belt should have1/16” or less clearance between it and the side frames. Remove shroud if neededto check the alignment position. Adjust alignment by tightening adjustment nut one quarter turn at a time on theside of conveyor where the belt is rubbing the side frame. Tightening will move thebelt away from the nut being tightened. Fully tighten jam nuts up to plate. Replace bearing covers. Turn power on and run machine in forward for five minutes.If additional alignment is required, repeat the above steps.Note: When the machine is run in reverse the belt may run slightly off center to theeither side. This is normal. The belt will stretch during the first few days of operation.This will affect alignment since the belt alignment relies in part on proper tensioning foreffective tracking.Air Filtration SystemThe air filtration system (AFS) on this device is designed to help reduce possible odorsand possible contaminants from escaping into the atmosphere during the process ofhard drive destruction. The AFS is a low maintenance system that only requires periodicinspection, filter cleaning, and filter changes. The frequency of the inspections isdependent on usage.HEPA FilterPre-Filter18SEM www.semshred.com
Model 0305 & 0304 Operation and Maintenance ManualWarning: Always de-energize the unit using proper LOTO procedures before cleaning,lubricating, maintaining, removing any guards, and after shredding operation iscomplete.Note: See maintenance schedule for inspection, cleaning, and replacementfrequencies.Steps for checking Air Filtration System:1. De-energize the unit using proper Lock Out Tag Out (LOTO) procedures.2. Tools Required: 1/2” wrench or socket wrench3. Inspect the air inlet of the AFS by removing the two bolts in the conveyor accesspanel on top of the conveyor on the rear of the unit and pulling up the cover tolook inside. Inlet will be on the left from the rear of the machine.ConveyorAccess Bolts4. Replace the prefilter. This can be accessed from the front of the shredder byremoving the maintenance access panel below the control station. With panelremoved, the prefilter will be exposed, and the prefilter can be removed. Note:Handle the prefilter with care. Do not jar or drop the prefilter as it is covered withdust from shredded media/drives.5. Be sure to thoroughly clean the inside of the prefilter compartment, pulling out anystrips or tape.IMPORTANT: Prefilter must be installed so that the arrow is pointing towards the fan.The arrow on the frame of the prefilter points in the direction of the air flow. The airflow for the AFS goes from left to right.SEM www.semshred.com19
Model 0
Always wear safety glasses when operating shredder. Always lock-out power at the disconnect when shredder is not in use, when servicing shredder, or when performing routine shredder maintenance. This includes cleaning. Never operate this or any other machine while under the influence of drugs, alcohol, or medications.