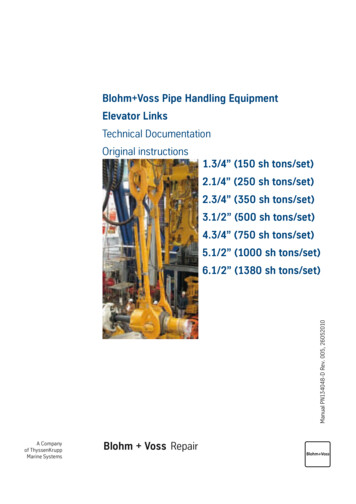
Transcription
Blohm Voss Pipe Handling EquipmentElevator LinksTechnical DocumentationOriginal instructions1.3/4” (150 sh tons/set)2.1/4” (250 sh tons/set)2.3/4” (350 sh tons/set)3.1/2” (500 sh tons/set)4.3/4” (750 sh tons/set)5.1/2” (1000 sh tons/set)Manual PN134048-D Rev. 005, 260520106.1/2” (1380 sh tons/set)A Companyof ThyssenKruppMarine SystemsBlohm Voss Repair1
GENERAL INFORMATIONWarnings and NoteWARNING: A “warning”indicates a definite risk ofequipment damage or dangerto personnel. Failure toobserve and follow properprocedures could resultin serious or fatal injuryto personnel, significantproperty loss, or significantequipment damage.NOTE: A “note” indicatesthat additional information isprovided about the currenttopics.WARNING: This technicaldocumentation containsinstructions on safety,installation, operation andmaintenance for the Blohm Voss Repair GmbH tool. It must be studied beforeworking with the tool.Intended use of thismanualThis manual is intendedfor use by field service,engineering, installation,operation, and repairpersonnel. Every effort hasbeen made to ensure theaccuracy of the informationcontained herein. Blohm Voss Repair GmbH, willnot be held liable for errorsin this material, or forconsequences arising frommisuse of this material.Anyone using serviceprocedures or tools, whetheror not recommended byBlohm Voss Repair GmbH,must be thoroughly satisfiedthat neither personal safetynor equipment safety will bejeopardized.Intellectual propertyCE MarkingAll rights retained. No partof this document may bereproduced in any form(print, photocopy, microfilmor any other procedure)or be processed using anelectronic system withoutwritten approval of Blohm Voss Repair GmbH.All information containedin this manual is basedupon the latest productinformation available at anytime of printing.Dependent on ongoingtechnical improvements(ISO 9001) “Blohm VossRepair GmbH” reserves theright to change the designand specifications withoutannouncement.The values specified inthis manual represent thenominal values of a unitproduced in series. Slightdeviations in the case ofthe individual devices arepossible.The tool complies with theMachinery Directive98/37/EC and 2006/42/EC.NOTE: In the event ofproblems that cannot besolved with the aid of thismanual, please contactone of the addresses listedbelow.For machines containingany hydraulic or pneumaticpowered parts, the Directive94/9/EC “Equipmentand protective systemsin potentially explosiveatmospheres” applies.The marking is as follows:CE Ex II 2G T5 (hydraulictools) or CE Ex II 2G T6(pneumatic tools).Limited WarrantyThe warranty provided will bevoid if the tool is either:1. Repaired or serviced bya service facility whichwas not authorised byBlohm Voss RepairGmbH.2. Replacement parts notmanufactured by Blohm Voss Repair GmbH areused.3. Modifications were madeto the tool which werenot approved by Blohm Voss Repair GmbH.Manufacturer & Agents World wideBlohm Voss Repair GmbHOil Tool DivisionHermann-Blohm-Straße 220457 HamburgGermanyBlohm Voss Oil Tools, LLC7670 Woodway, Suite 266Houston,Texas 77063United States of AmericaPremier Sea & Land Pte. Ltd.1, Scotts Road#19-12 Shaw CentreSingapore 228208Republic of SingaporeWoodhouse International LLCPhone: 49(0)40/3119-1826/1162Fax: ohmvoss-oiltools.comPhone: 1-713-952 0266Fax: 1-713-952 Phone: 65-6734-7177Fax: 65-6734-9115enquiries@premier-ips.com.sgPhone: 04-3472300Fax: 04-3474642woodhouse@emirates.net.ae2PO Box 23724DubaiUnited Arab Emirates
General safety issuesWARNING: One should avoidcreating ignition sources, likeheat, as a result of the use ofthe tool with other tools orequipment.WARNING: Do not use the toolfor any other purpose thangiven in this document within itsspecification.WARNING: Failure to conductroutine maintenance couldresult in equipment damage orinjury to personnel.WARNING: The tool must onlybe serviced by trained and byan Blohm Voss Repair GmbHauthorized personnel.WARNING: Wear personalprotection equipment whileworking with the equipment.WARNING: All warning plates,signs and labels attached tothe equipment must be observed.The warning plates, signs andlabels must be present on thetool. Do not remove the labels.If they are missing, replacing ismandatory.WARNING: Any modification tothe tool carried out withoutthe approval of Blohm VossRepair GmbH will void anywarranty.WARNING: Using the tool withdamaged or worn parts cancreate serious incidents.WARNING: It is not allowed touse any components which areof "non-B V" origine, or use"non-OEM" parts which are notapproved by B V. It will voidany warranty and may effectthe correct functioning of thetool and it's safety features.3
EC-DECLARATION OF CONFORMITYWe,Blohm Voss Repair GmbHOil Tool DivisionHermann-Blohm-Strasse 220457 HamburgPhone: 49(0)40 3119-1139Fax: 49(0)40 3119-3305declare that the productElevator linkswhich is the subject of this declaration, is in conformity with the following standard(s) or normative documents98/37/EC:Machinery DirectiveDIN EN ISO 12100 :Safety of machinery, part 1 and 2DIN EN ISO 14121-1:Safety of machinery, Risk assessmentDirective 94/9/EC:Devices and protection systems for intended use in explosive areasISO 13535:2002/API 8C:Petroleum and natural gas industries-Drilling and production equipment-Hoistingequipment4
TABLE OF CONTENTSEC-DECLARATION OF CONFORMITY4TABLE OF CONTENTS51. DESCRIPTION8General descriptionCapacity and weightIdentification numberDimensionsMain dimensions of Elevator LinksTemperature range888910102. INSTALLATION12LiftingInstallation restrictions12123. OPERATION14Extreme Low Temperature144. MAINTENANCE & INSPECTION16GeneralDeterioration of equipmentRecordsDismantlingCleaningInspection ProcedureInspection categories acc. to API RP 8BFrequencyPeriodic inspectionNon-periodic inspectionInspectionCritical Load InspectionDismantling InspectionInspection check listsCheck Category I (Ongoing observation)Check List Category II (Daily)Check List Category III (every 6 months)Check List Category IV (every year)Measuring of wearBeyond RepairUse of Worn Elevator LinksCapacity of worn Elevator Link setsExplanation how to use the table 2DESCRIPTION2222223INSTALLATIONWarnings and NoteIntended use of this manualIntellectual propertyManufacturer & Agents World wideCE MarkingLimited WarrantyGeneral safety issuesOPERATIONS2MAINTENANCE& INSPECTIONGENERAL INFORMATIONTABLE OF CONTENTSTable of contents5
TABLE OF CE& INSPECTION6
DESCRIPTIONDESCRIPTION7
1. DESCRIPTIONGeneral descriptionElevator links are designed to hang elevators. They are tobe used for their designated purpose only. The links areavailable in 150, 250, 350, 500, 750, 1000 and 1380 mtonratings.Capacity and weightDESCRIPTIONElevator Link PNSizeRated capacity (ton)Weight (kg / lbs)134048-Y1.3/4" x 48"150154 / 34012" increases15018 / 40134144-Y1.3/4" x 144"150298 / 655214048-Y2.1/4" x 48"250180 / 39612" increases25023 / 51214180-Y2.1/4" x 180"250433 / 953214240-Y2.1/4" x 240" (20 ft)250544 / 1197214360-Y2.1/4" x 360" (30 ft)250780 / 1720214480-Y2.1/4" x 480" (40 ft)2501000 / 2205234048-Y2.3/4" x 48"350270 / 59412" increases35029 / 64234216-Y2.3/4" x 216"350734 / 1615234240-Y2.3/4" x 240" (25 ft)350790 / 174260 " (5 ft) increases350145 / 320234600-Y2.3/4" x 600" (50 ft)3501766 / 3894312072-Y3.1/2" x 72"500478 / 105012" increases50052 / 115312216-Y3.1/2" x 216"5001102 / 2425312240-Y3.1/2" x 240" (20 ft)5001200 / 264060" (5 ft) increases500260 / 575312660-Y3.1/2" x 660" (55 ft)5003236 / 7135434108-Y4.3/4" x 108"7501030 / 226512" increases75076 / 170434216-Y4.3/4" x 216"7501714 / 3770434240-Y4.3/4" x 240" (20 ft)7501862 / 410560" (5 ft) increases750380 / 838434660-Y4.3/4" x 660" (55 ft)7504514 / 9552512180-Y5.1/2" x 180"10002630 / 5786612180-Y6.1/2" x 180"13803580/7876For the 1000 and 1380 ton elevator links other sizes can beobtained upon request.Identification numberEvery Elevator link should have an idenification number. Thisnumber is stamped near an eye.8
1.3/4"2.1/4"-3.1/2"4.3/4"5.1/2"cUPPER EYEfelength as orderedbDESCRIPTIONagd6.1/2"DimensionsLOWER EYEx9
Main dimensions of Elevator DESCRIPTIONTemperature rangeLinksTemperature working range ambient* If not otherwise stated in the databook.10- 20 C to 80 C *- 4 F to 176 F *
INSTALLATIONINSTALLATION11
2. INSTALLATIONLiftingLift the elevator links by means of acrane.The lifting procedures should becarefully observed!Installation restrictionsThe elevator link is to be used as aconnecting element beween hook andelevator. It must never by used forany other purpose. Never exceed thedesignated load.INSTALLATION12
OPERATIONSOPERATIONS13
3. OPERATIONExtreme LowTemperatureRatings have been established at atemperature of minus 20 C. The effectof low temperature on steel must berecognized although no changes in designsafety factors have been provided. Whenoperating at low temperatures, cautionmust be exercised to take into account thelower impact capabilities of many steelswhich are typically employed. The risk offailure may be reduced by a critical loadinspection.OPERATIONS14
MAINTENANCE& INSPECTIONMAINTENANCE& INSPECTION15
4. MAINTENANCE & INSPECTIONGeneralDismantlingIf cracks, excessive wear etc. isrecognised, contact Blohm Voss RepairGmbH or an authorised service company.Weldings of the castings should be doneonly by Blohm Voss Repair GmbH or anauthorised service company in accordingto Blohm Voss welding procedure.The elevator links should be dismantledfrom the rig and inspected in ausitably equipped facility for excessivewear, cracks, flaws or deformation.Corrections should be made inaccordance with recommendationswhich can be obtained from Blohm Voss.Deterioration ofequipmentNormal wear in course of use willeventually reduce the capability of theelevator links. The existence or cracks, orthe appearance of defects, can indicatesevere deterioration, even impendingfailure, and prompt attention is requiredeither to remove the elevator link fromservice immediately, or to undertakeappropriate repair as required.RecordsMAINTENANCE& INSPECTIONInspection procedure are listed in thisrecommended practice and generalizedsketches of the elevator links showingpoints to be inspected are to be provided.Written records should be maintainedwhich accurately record the inspectionand maintenance history of each elevatorlink. Records should include the date,personnel involved, and results of eachinspection or maintenance procedureperformed.WARNING: Never weld on Elevator Links!16CleaningBefore inspection, all foreign materialsuch as dirt, paint, grease, oil, scale,etc. should be removed from the areasto be inspected by a suitable method.Inspection ProcedureThe inspection should be made bytrained, competent personnel.
Inspection categories acc. to API RP 8BCategory IIThis is Category I inspection plusfurther inspection for corrosion,deformation, loose or missingcomponents, deterioration, properlubrication, visible external cracks, andadjustment.Category II may involve somedisassembly to access specificcomponents and to identify wear thatexceeds the allowable tolerances.Category IIIThis is Category II inspection plusfurther inspection, which should includeNDT of critical areas and may involvesome disassembly to access specificcomponents and to identify wear thatexceeds the allowable tolerances.Prior to inspection, all foreign materialsuch as dirt, paint, grease, oil, scale,etc. shall be removed from theconcerned parts by a suitable method(e.g. paint-stripping, steam-cleaning,grit-blasting).Category IVThis is Category III inspection plusfurther inspection for which theequipment is disassembled to theextent necessary to conduct NDT of allprimary-load-carrying components.Equipment shall be: disassembled in a suitableequipped facility to the extentnecessary to permit fullinspection of all primary-loadcarrying components and othercomponents that are critical to theequipment. inspected for excessive wear,cracks, flaws and deformation.Procedure: Corrections shall be madein accordance with themanufacturer’s recommendations. Prior to inspection, all foreignmaterial such as dirt, paint, grease,oil, scale, etc. shall be removedfrom the concerned parts bya suitable method (e.g. paintstripping, steam-cleaning, gritblasting)FrequencyPeriodic inspectionThe recommended schedule forinspection of all kind of Elevators:Daily:I II6 Monthly:III1 Year:IV Spiders:Daily:Weekly:6 Monthly:1 Year:IIIIIIIV Power Slips:Daily:Weekly:6 Monthly:2 Year:IIIIIIIVThe recommended frequencies applyfor equipment in use during thespecified period.The inspection frequencies are onlyrecommendations. The schedule ofinspection heavily depends on thefollowing factors: environment load cycles regulatory requirements operating time testing repairs re manufactureNon-periodic inspectionA complete, on-job, shut-downinspection equivalent to the periodicalCategory III or Category IV should bemade before (if anticipated) and aftercritical jobs (e.g., running heavy casing/ drill strings, jarring, pulling on stuckpipes and/or operating at extreme lowtemperatures) -20 C ( -4 F).InspectionA thorough inspection should becarried out periodically (every 3months) or as special circumstancesmay require. Before starting aninspection disconnect hydraulic/pneumatic system and removeall foreign materials (dirt, paint,grease Oil, scale, etc.) from surfac
Inspection categories acc. to API RP 8B 17 Frequency 17 Periodic inspection 17 Non-periodic inspection 17 Inspection 17 Critical Load Inspection 18 Dismantling Inspection 18 Inspection check lists 19 Check Category I (Ongoing observation) 20 Check List Category II (Daily) 20