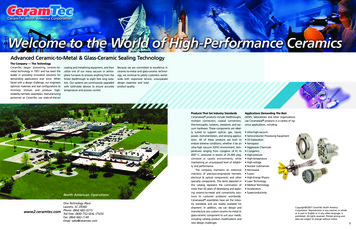
Transcription
Advanced Ceramic-to-Metal & Glass-Ceramic Sealing TechnologyThe Company — The TechnologyCeramTec began pioneering ceramic-tometal technology in 1951 and has been theleader in providing innovative solutions fordemanding applications ever since. Whenfaced with a design challenge, our engineersoptimize materials and seal configurations tominimize stresses and produce highreliability hermetic assemblies. Manufacturingpersonnel at CeramTec use state-of-the-artcoating and metallizing equipment, and thenutilize one of our many vacuum or atmosphere furnaces to process anything from thetiniest feedthrough to eight foot long isolators. Our systems are continuously upgradedwith solid-state devices to ensure accuratetemperature and process control.North American Operationswww2.ceramtec.comOne Technology PlaceLaurens, SC 29360Phone: (864) 682-3215Toll Free: (800) 752-SEAL (7325)Fax: (864) 682-1140Email: sales@ceramtec.comBecause we are committed to excellence inceramic-to-metal and glass-ceramic technology, we continue to satisfy customers worldwide with responsive service, unsurpasseddesign expertise and totalproduct quality.Products That Set Industry StandardsCeramaseal products include feedthroughs,multipin connectors, coaxial connectors,thermocouples, isolators, viewports, and vacuum hardware. These components are ideally suited to support optical, gas, liquid,power, instrumentation, and sensing applications. All of these products are built toendure extreme conditions, whether it be anultra-high vacuum (UHV) environment, temperatures ranging from cryogenic (4 K) to450 C, pressures in excess of 25,000 psig,corrosive or caustic environments, whilemaintaining an unsurpassed level of reliability and performance.The company maintains an extensiveinventory of precision-engineered hermeticelectrical & optical components and otherspecialty components. The items depicted inthis catalog represent the culmination ofmore than 50 years of developing and applying ceramic-to-metal and connectivity solutions to customer problems worldwide.Ceramaseal assemblies have set the industry standards and are readily available forshipment. In addition, we can design andmanufacture any custom ceramic-to-metal orglass-ceramic component to suit your needs,including catalog product modifications andnew design challenges.Applications Demanding The BestOEM’s, laboratories and other organizationsuse Ceramaseal products in a variety of rigorous applications, including: Ultra-high-vacuumSemiconductor Processing EquipmentOil ExplorationAerospaceAggressive gh-voltageNuclear SubmarinesMicrowaveFusionHigh-Energy PhysicsLaser TechnologyMedical TechnologyAcceleratorsSuperconductivityCopyright 2007 CeramTec North AmericaCorporation. Reproduction in any manner, in wholeor in part in English or in any other language, isprohibited. All rights reserved. Printed pricing anddata are subject to change without notice.1
Dry pressing of high volume ceramic insulators.Manufacturing CapabilitiesProcess Under ControlPowder ProcessingThe technical ceramic process starts with theformulating and mixing of the ceramic powders and binding agents into an aqueousslurry form. This process is referred to asbody preparation. The ceramic slurry goesthrough various milling and drying operations like spray drying, which can be seenhere. This creates a consistent grain size,which optimizes the powders for the formingprocess. All of our ceramic products, whichinclude more than 10 standard bodies, startwith our own in-house powder processing.FormingTypical ceramic forming technologies usedfor the production of the ceramic insulatorsused within our Hermetic products includeCapabilities: Far Beyond Vacuum BrazingWhen it comes to highly engineered hermetically sealed electrical or optical assemblies the joining orbonding technology is really about selecting materials with similar coefficients of thermal expansion.The importance of material purity, quality and consistency is paramount. For this reason, CeramTec iscompletely vertically integrated and thus controls the process from beginning to end. This begins withceramic powder production right through the machining and welding of precision metal components.extrusion, dry pressing and isostatic pressing.High volume insulators are usually drypressed, while tube or rod-like insulators areextruded and large or complex insulators areisostatically pressed. Many of these insulators will go through our “green” (compressed powder, before firing) machiningprocess before being fired. Green machiningcan typically achieve tolerances of /- 1% or /- .005", whichever is greater.FiringThe firing or sintering process is the prolonged baking of the ceramic parts in a gasor electric kiln at temperatures between1,300 – 1,800 C (based on the specificmaterial being sintered). Through reactionsthat occur during sintering, a strengtheningand densification of the ceramic takes place,resulting in a reduction in porosity. There isapproximately 20% controlled shrinkagewhen firing ceramics. Typical firing cycles canrange from 12 - 120 hours depending uponthe kiln type and product.Hard (diamond) grinding of ceramic productsto achieve tight tolerances.Ceramic MachiningTight tolerances and/or surface finishes typically require a post firing machining process,which is also done in-house. This couldinclude grinding, honing, lapping or polishingand is where the majority of the expense inmanufacturing ceramic parts is generated.Due to the high hardness of ceramic materials that have been fired, diamond tools arealmost exclusively used. Diamond grindingcan easily produce tolerances of /- .001"and much tighter tolerances within tenthscan be produced.Continuous tunnel kiln used to fireceramic insulators. Powder processing using our 24-ft-diam.Anhydro spray dryer3
MetallizingPlatingCeramTec employs a number of proprietarymetallizing processes but the vast majority ofthe metallized insulators used in ourCeramaseal assemblies are manufacturedusing thick-film metallization of aluminaceramics. The most common method used isthe refractory metal process, which utilizesmolybdenum as a sintered metal base layeron the ceramic. The wide selection of molybdenum based coatings along with the stringent furnace operating parameters insuresgood bond strength and reliability with alumina body compositions of 85-99% alumina. Typical applications methods includehand painting, screen printing or using oneof our automated metallizing banders. Inprocess inspection and verification of metallizing and plating thickness are performed byx-ray fluorescence (XRF).Metallized ceramic insulators that will beused in our moly-manganese sealing processhave to be nickel plated first. CeramTec hasboth electroless and electrolytic nickel platinglines, which are used for plating over themolybdenum metallizing on the insulators aswell as other metal components. A separategold plating line is primarily used to goldplate the pins and female contacts on finished connector assemblies to maximize theelectrical contact.Electrolytic nickel plating of metallizedceramic insulators and other metalcomponents.Thick film metallization of ceramic insulators.Vacuum brazing furnaces with computerprogrammed profiles.Assembly of Ceramaseal products in a controlled environment.Critical AssemblyWithin the Assembly Department themetallized insulators will be assembledwith the conductors/pins, weldadapters, sleeves or caps and brazealloys. The parts are assembled on a firing fixture and will be fired within one ofour many brazing furnaces, which arespecific to the braze alloy used and theconfiguration or size of the part. Criticalcomponents are assembled in an ultraclean environment using protective wearto prevent contamination.Vacuum BrazingCeramTec has a variety of furnaceswhich allow high temperature brazing invacuum, hydrogen, nitrogen, or partialpressure atmospheres. A broad selectionof brazing filler metals are used and areselected based on the optimization tothe base metals (or ceramic) to bebrazed. These include precious metal,copper, and high nickel alloys with melting ranges from 705 C to 1300 C. This4broad temperature capability allows forthe flexibility of step brazing when acomplex assembly has multiple brazejoints.The ‘active metal’ ceramic-to-metalbrazing process is a one-step operationcompared to the moly-manganeseprocess, which typically has five steps.This process requires an ‘active’ elementthat will react with the ceramic, forminga reaction layer between the ceramicand the molten braze that will reducethe interfacial energy to such a level thatwetting of the ceramic takes place. Thisactive element typically refers to a smallpercentage of titanium or zirconiumadded to the braze filler metal or directly applied to the ceramic. The activebraze process is ideally suited for sealingto sapphire, larger ceramic to metalassemblies, and non-oxide ceramics.CeramTec’s third sealing process isreferred to as glass-ceramic sealing. Thisis glass-to-metal sealing whereby theamorphous glass material is "crystallized" through a subsequent heat treatment. The resulting material is primarilycrystalline in nature and takes on similarproperties to ceramic. The high temperature glass-ceramic materials that havecharacteristics suitable for high vacuum,high pressure, high thermal expansion,and temperature capability from cryogenic to 450 C bake out. This glassceramic sealing process is ideal forsealing to high expansion metals such as304 or 316 stainless steel and is commonly used for our high density connectors and matched impedance coaxialconnectors.During the design process, CeramTectypically uses Finite Element Analysis(FEA) to initially test different joint configurations, braze alloys and brazingconditions prior to any actual brazing. Ascanning electron microscope (SEM) isused to analyze the braze joints duringproduct development.5
Machining of Metal ComponentsMachining of complex metal components is all done within our in-housemachine shop. We utilize multiple EDMand wire EDM machines, CNC andmechanical lathes, milling machines andother metal machining equipment toprecision machine the components usedwithin our assemblies. We also machineour own firing fixtures and the dies usedwithin our pressing equipment.Machining of metal components forCeramaseal assemblies using a CNC lathe.Testing & InspectionCeramTec’s products and assemblies areapplied to the most rigorous applications, which require a very high level ofquality assurance. For this reason 100 %of CeramTec's Ceramaseal Products areleak-tested on one of our many dry helium mass spectrometers before they arestocked or shipped. All parts are guaranteed to 1x10-10 Atm cc/sec He. Leaktest certificates are available uponrequest. For dimensional accuracy,CeramTec tests all critical componentson one of our coordinate measuringmachines (CMM).There are stringent cleaning processes that are adhered to throughout themanufacturing and packaging process.Class-1000 clean room facilities are alsomaintained for those customers thatrequire special cleaning & packaging.Throughout all of our processes thereare rigorous quality standards that aremet and thorough inspections of incoming parts, in-process parts and finalassemblies. CeramTec North America isISO 9001:2000 quality system registered. Exceeding the customers’ expectations is about more than shipping aquality product on time. It is about ahigher level of customer service and support than is required, which is what oursales and customer service staff aim toaccomplish throughout the salesprocess.Customer service representativesstanding by to serve you.itSysteredQualyis te m R e gWeldingMany of CeramTec’s standard and customCeramaseal products require the welding of the feedthroughs into flanges orplates. We are equipped with both automatic and manual pulsed T.I.G. weldingstations. For precision welding applications that require a lower welding temperature to protect the seal joint, weutilize laser welding technology.Induction brazing equipment is also used.Welding of Ceramaseal products usingan automatic T.I.G. welding lathe6Helium leak testing of our Ceramaseal products.Helium Leak Test
Testing and RatingsThe ratings in this catalog are providedas a guide only. Product should be independently tested to determine suitabilityfor your application. Custom testing isavailable upon request.Temperature RatingsInsulation resistance for ceramic materials decreases as temperature increases.Most products in this catalog have aminimum room temperature resistanceof 5000 megohms at 500 volts.Maximum temperature ratings listed arefor bake-out only. The insulation resistance at these temperatures may not besuitable for all applications.Note that the thermal gradient forany of the ceramic-to-metal or glassceramicseals in thiscatalog shouldnot exceed 25 Cper minute. Severethermal gradients can bedetrimental to joint designdue to variations in expansioncoefficients and the thermal conductivityof components.The upper temperature ratings in thiscatalog are determined by a sequence ofvacuum bake outs at 50 C incrementsand 1 hour holds starting at 200 C andproceeding until failure or 550 C.The lower temperature rating isdetermined by progressive thermalshocks starting with 5 cycles from roomtemperature (RT) to -25 C, followed byRT to -65 C. The thermal shock procedure follows MIL-STD-202F, Method107G. This is followed by cycling fromRT to liquid nitrogen (LN2) temperature(approx. -200 C). The part is then vacuum baked out and helium leak tested.Pressure RatingsPressure ratingswithin this catalog were determined by firstwelding the component into asuitable flange oradapter,thenatpressurizing8Table of Contents50 – 500 psi increments up to 50,000 psior until failure. All pressure testing isdone at room temperature (20 C). Aftereach pressure increment, critical dimensions are measured to monitor plasticdeformation of metal components and ahelium leak test is performed to verifyhermeticity. An appropriate safety factor is applied depending on the failuremode of the test sample (Catastrophicfailures - no observable yielding of ametal component prior to ceramic failure or Ductile failures - observable yielding of a metal component ( .003”) hastaken place.)Current RatingsThe current ratings for the standardproducts within this catalog are basedon the amount of current necessary tocause a maximum allowable temperature rise of 60 C. The conductors of theassembly are connected with jumpers sothat the applied current passes throughall conductors simultaneously. The temperature rise is measured with a thermocouple placed on the assembly in thelocation of the conductor seals.Temperature rise is measured as a function of time for a given applied currentuntil the steady state temperature isachieved.Voltage RatingsThe voltage ratings in thiscatalog are based upon operation with one side in dryatmospheric conditions whilethe opposite end (right side indrawings) is in a stable vacuum environment with a system pressure of 1x10-4 torr.Other comparable environments wouldbe air pressure of 80 psi or high dielectric oil. Note that the voltage rating onmany of our high voltage products arewhen used with the mating air side plugor cable assembly and are noted as such.During testing, voltage is appliedbetween a conductor and the outerground shell of the assembly. The voltage is slowly increased until flashoveroccurs. Based on the magnitude of theflashover voltage, an appropriate safetyfactor is applied.VSWR (Voltage Standing Wave Ratio)The VSWR vs. Frequency charts in theCoaxial section of this catalog were generated through the testing of parts ona network analyzer using NISTtraceable calibration standards.Dimensional InformationAll drawing dimensionswithin this catalog arefor reference only.Tolerances willvary by specific product line and will depend on various geometric parameters. Vacuumand pressure specifications apply to theright side of the drawings. All dimensions are in inches [millimeters].4RoHS Compliant99.5% ofthe productswithin thiscatalog areRoHS compliant. Those parts that aren’tcompliant will be noted as such.RoHSCompliantAInstrumentation / PowerPowerPin HeaderMultipin HeaderMicro & Mini HVPower PlugHigh Power – Liquid CooledHigh VoltageRF Power – Liquid CooledBaseplateBMicrodotSMBSMABNCMHVType NHNSHV 5 KVBSHV 7.5 KVSHV 10 KVSHV 20 KVBetween SeriesDLoop TypeSpade TypeSpade & PowerMIL-C-5015 TypeA.1A.2A.3A.4A.5A.6A.7A.8A.9A.10Page 14-15Page 16-17Page 18-19Page 20-21Page 22-25Page 26-35Page 36-41Page 42-47Page 48-49Page 50-51MultipinConnectorMicro D Type: MIL-DTL-83513Sub D Type: MIL-C-24308Circular Type: MIL-C-26482Circular Type: MIL-C-5015Circular Type Power: MIL-C-5015High Page 56-57Page 58-59Page 60-63Page 64-65Page 66-69Page 70-71Page 8C.9C.10C.11C.12Page 80-83Page 84-87Page 88-95Page 96-105Page 106-113Page 114-117Page 118-119Page 120-125Page 126-127Page 128-131Page 132-133Page Page 184-187Page 188-189Page sAir Side CablesIn-Vacuum CablesStandoffs & 18-219Technical ReferenceEngineering DataCable Plug AttachmentInstallationThermocouplePage 156-157Page 158-159Page 160-167PressureNPTCeramTite Tec-Seal IE.1E.2E.3ViewportSapphireFused SilicaExtended RangeDifferentially PumpedHCoaxialIsolatorPart Number IndexQuote Form/Terms & ConditionsI.1I.2I.3Page 222-228Page 229-241Page 242-247Page 248-254Page 255-2569
Toll Free: (800) 752-SEAL (7325) Fax: (864) 682-1140 Email: sales@ceramtec.com www2.ceramtec.com Advanced Ceramic-to-Metal & Glass-Ceramic Sealing Technology The Company — The Technology CeramTec began pioneering ceramic-to-metal technology in 1951 and has been the leader in providing innovative solutions for demanding applications ever since .