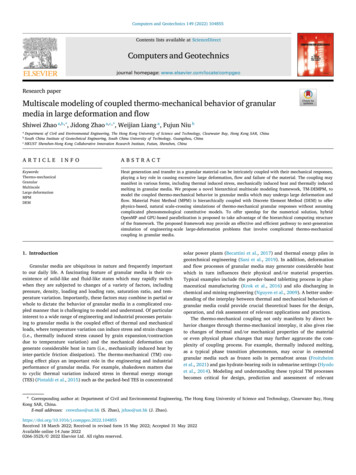
Transcription
Computers and Geotechnics 149 (2022) 104855Contents lists available at ScienceDirectComputers and Geotechnicsjournal homepage: www.elsevier.com/locate/compgeoResearch paperMultiscale modeling of coupled thermo-mechanical behavior of granularmedia in large deformation and flowShiwei Zhao a,b , , Jidong Zhao a,c , , Weijian Liang a , Fujun Niu babcDepartment of Civil and Environmental Engineering, The Hong Kong University of Science and Technology, Clearwater Bay, Hong Kong SAR, ChinaSouth China Institute of Geotechnical Engineering, South China University of Technology, Guangzhou, ChinaHKUST Shenzhen-Hong Kong Collaborative Innovation Research Institute, Futian, Shenzhen, iscaleLarge deformationMPMDEMINFOABSTRACTHeat generation and transfer in a granular material can be intricately coupled with their mechanical responses,playing a key role in causing excessive large deformation, flow and failure of the material. The coupling maymanifest in various forms, including thermal induced stress, mechanically induced heat and thermally inducedmelting in granular media. We propose a novel hierarchical multiscale modeling framework, TM-DEMPM, tomodel the coupled thermo-mechanical behavior in granular media which may undergo large deformation andflow. Material Point Method (MPM) is hierarchically coupled with Discrete Element Method (DEM) to offerphysics-based, natural scale-crossing simulations of thermo-mechanical granular responses without assumingcomplicated phenomenological constitutive models. To offer speedup for the numerical solution, hybridOpenMP and GPU-based parallelization is proposed to take advantage of the hierarchical computing structureof the framework. The proposed framework may provide an effective and efficient pathway to next-generationsimulation of engineering-scale large-deformation problems that involve complicated thermo-mechanicalcoupling in granular media.1. IntroductionGranular media are ubiquitous in nature and frequently importantto our daily life. A fascinating feature of granular media is their coexistence of solid-like and fluid-like states which may rapidly switchwhen they are subjected to changes of a variety of factors, includingpressure, density, loading and loading rate, saturation ratio, and temperature variation. Importantly, these factors may combine in partial orwhole to dictate the behavior of granular media in a complicated coupled manner that is challenging to model and understand. Of particularinterest to a wide range of engineering and industrial processes pertaining to granular media is the coupled effect of thermal and mechanicalloads, where temperature variation can induce stress and strain changes(i.e., thermally induced stress caused by grain expansion/contractiondue to temperature variation) and the mechanical deformation cangenerate considerable heat in turn (i.e., mechanically induced heat byinter-particle friction dissipation). The thermo-mechanical (TM) coupling effect plays an important role in the engineering and industrialperformance of granular media. For example, shakedown matters dueto cyclic thermal variation induced stress in thermal energy storage(TES) (Pintaldi et al., 2015) such as the packed-bed TES in concentratedsolar power plants (Becattini et al., 2017) and thermal energy piles ingeotechnical engineering (Sani et al., 2019). In addition, deformationand flow processes of granular media may generate considerable heatwhich in turn influences their physical and/or material properties.Typical examples include the powder-based tabletting process in pharmaceutical manufacturing (Krok et al., 2016) and silo discharging inchemical and mining engineering (Nguyen et al., 2009). A better understanding of the interplay between thermal and mechanical behaviors ofgranular media could provide crucial theoretical bases for the design,operation, and risk assessment of relevant applications and practices.The thermo-mechanical coupling not only manifests by direct behavior changes through thermo-mechanical interplay, it also gives riseto changes of thermal and/or mechanical properties of the materialor even physical phase changes that may further aggravate the complexity of coupling process. For example, thermally induced melting,as a typical phase transition phenomenon, may occur in cementedgranular media such as frozen soils in permafrost areas (Froitzheimet al., 2021) and gas hydrate-bearing soils in submarine settings (Hyodoet al., 2014). Modeling and understanding these typical TM processesbecomes critical for design, prediction and assessment of relevant Corresponding author at: Department of Civil and Environmental Engineering, The Hong Kong University of Science and Technology, Clearwater Bay, HongKong SAR, China.E-mail addresses: ceswzhao@ust.hk (S. Zhao), jzhao@ust.hk (J. 5Received 18 March 2022; Received in revised form 15 May 2022; Accepted 31 May 2022Available online 14 June 20220266-352X/ 2022 Elsevier Ltd. All rights reserved.
Computers and Geotechnics 149 (2022) 104855S. Zhao et al.typically employed to simulate the response of a representative volumeelement (RVE) as a surrogate of the conventional constitutive model ata material point to feed a continuum-based method, such as FEM (Guoand Zhao, 2014; Liu et al., 2016; Desrues et al., 2019), SPFEM (Guoet al., 2021) and MPM (Liang and Zhao, 2019), for solution of a boundary value problem. The hierarchical coupling structure offered in theseapproaches enables effective simulations of various engineering problems with complex boundary and initial conditions and yet effortlesslycapture the complicated granular material responses that are highlyloading path and state dependent. The hierarchical multiscale couplingscheme can be a promising alternative for thermo-mechanical modelingof granular media. Indeed, a hierarchical coupling of FEM and DEM forthermo-mechanical modeling was proposed in our previous study (Zhaoet al., 2020), which is, however, limited to thermally induced smalldeformation and stress regime. It is desirable to develop an alternativemultiscale approach that can rigorously tackle TM coupling of granularmedia in the regime of large deformation and flow.This work aims at developing an entirely new hierarchical multiscale framework to simulate coupled thermo-mechanical behavior inlarge deformation and flow of granular media. The framework will bebuilt upon a pure mechanical hierarchical coupling formulation of MPMand DEM (termed as DEMPM) that was developed for modeling largedeformation of granular media (Liu et al., 2017; Liang and Zhao, 2019;Zhao et al., 2021). In DEMPM, a material point serves as an interfacefor information exchange between the macro-scale MPM solver andthe meso-scale DEM solver. Notably, a velocity gradient at a givenmaterial point can be obtained first from the MPM solver. It is thenpassed on to the corresponding RVE assembly as constraints for a DEMsolution which is further used to extract required material responses(e.g., stress) to feedback to the MPM solver. The new development incorporating thermo-mechanical coupling will be termed as TM-DEMPMhereafter. To further consider thermo-mechanical coupling in diversified conditions, the generalized interpolation material point method(GIMP) (Bardenhagen and Kober, 2004) will be adopted in TM-DEMPMas the continuum MPM solver to solve both thermal and mechanicalfields in a staggered manner at the continuum scale, whereas physicsbased thermo-mechanical coupling is fully considered and rigorouslymodeled at the RVE scale in the DEM solver. As will be demonstrated,the proposed new framework presents three outstanding features whengranular media develop deformation en route to large deformation andflow regime: (1) it is able to model thermally induced stress due to grainexpansion/contraction; (2) it can capture mechanically induced heatdue to inter-particle friction dissipation; and (3) it can handle thermallyinduced melting at the contact scale. Consequently, TM-DEMPM offersa computational pathway for physics-based, cross-scale modeling andunderstanding of the thermo-mechanical responses of granular media.The rest of the paper is organized as follows. Section 2 providesthe macroscopic formulation of TM modeling by GIMP, followed by themesoscopic formulation of TM coupling in DEM in Section 3. Section 4introduces the hierarchical multiscale coupling and computing scheme.Numerical examples are showcased in Section 5, where the TM-MPMsolver is benchmarked against analytical and FEM solutions prior to thevalidation of TM-DEMPM, followed by three examples representativeof typical TM problems in granular media further presented to demonstrate the predictive capabilities and features of the proposed approach,including heat generation in biaxial compression, heat generation indischarge of a granular silo, and melting induced column collapse.Concluding remarks are summarized in Section 6. Tensorial indicialnotations and Einstein summation convention are followed in the study,and boldface letters for matrices are used.geostructures during large deformation and failure of granular media.In agricultural or powder industry, continuous discharging of grainsin a silo can accumulate heat to cause remarkable increase of temperature, posing a serious trigger for dangerous silo explosion (Russoet al., 2017). In chemical engineering, impregnation and calcinationperformance depends crucially on heat transfer and flow properties ofgranular media in rotary vessels (Saruwatari and Nakamura, 2022).For frozen granular media in nature, the melting process of interparticle bonds can significantly weaken the strength of granular matrix,triggering large deformation and flow of soils that may cause catastrophic geohazards and environmental disasters (Maslin et al., 2010).For example, the dissociation of gas hydrates in submarine settingsmay trigger potential geohazards during the course of exploitation,ranging from submarine landslides to earthquakes and tsunamis, threatening the operation and safety of offshore infrastructures and coastalcities (Maslin et al., 2010). Thaw-induced landslides in permafrost areasserve both as an awakening warning of global warming and an exacerbating factor by causing carbon release into the atmosphere (Froitzheimet al., 2021). There are evidently pressing needs from both industrial developments and environmental sustainability to advance ourunderstanding of thermo-mechanical response of granular media, inparticular when they reach the regime of large deformation and/orflow.Great efforts have been devoted to the study of thermo-mechanicalcoupling in granular media from diversified communities of granularphysics, thermal processing industry, and chemical and geotechnicalengineering. A prevailing body of these studies have been based oncontinuum mechanics based models and numerical approaches. Theytypically smear the discrete nature of a granular material and consider it as a continuum body with homogenized macroscopic responsesdescribed by assumed phenomenological constitutive models (Na andSun, 2017; Liu et al., 2018). To treat an engineering scale boundary value problem, these models are routinely implemented into acontinuum-based numerical approach such as Finite Element Method(FEM) and its alternative mesh-free ones such as Material Point Method(MPM) (Sulsky et al., 1995) and Smoothed Particle Hydrodynamics(SPH) (Gingold and Monaghan, 1977) which are specifically useful forlarge deformation problems (Bui et al., 2008; Lei et al., 2021). Despitetheir great success, continuum constitutive models may face difficultiesin capturing the physical behavior of granular media under complexloading conditions entangled with complicated coupling. When dealingwith problems involving large deformation and flow, even greaterchallenges are posed to both model developments and their implementations. Micromechanics-based approaches and tools, representedby Discrete Element Method (DEM) (Cundall and Strack, 1979), haverecently triggered growing interests by their capability of reproducingvarious complex mechanical characteristics of granular media from aparticulate perspective, such as anisotropy and liquefaction (Guo andZhao, 2013), strain localization and failure (Chen et al., 2011), noncoaxiality (Li and Yu, 2015) and the rich transitional behavior betweenfluid and solid (Herrmann et al., 2013). Micromechanics approachescan also facilitate the consideration of various coupling processes.Indeed, DEM may accommodate the thermo-mechanical coupling withproper network or pore-scale models (Nguyen et al., 2009; Gan et al.,2012; Choo et al., 2013; Moscardini et al., 2018; Caulk et al., 2020).It can further be coupled with other computational schemes such asComputational Fluid Dynamics (CFD) and Lattice Boltzmann Method(LBM) (Zhang et al., 2016) to simulate coupled hydro-mechanicalbehavior of granular media. However, computational cost may bean outstanding issue for DEM that limits its practical application forlarge-scale problems.Recent spotlights of modeling of granular media have more beenattracted by a class of hierarchical multiscale approaches that leveragethe strengths of both continuum- and discrete-based methods (Andradeet al., 2011; Chen et al., 2011; Guo and Zhao, 2014; Liu et al., 2016).They employ a hierarchical numerical coupling scheme where DEM is2. Thermo-mechanical modeling by GIMP2.1. Governing equations and weak form formulationThe macroscopic thermo-mechanical response of granular mediais modeled in a continuum-based manner, by solving the following2
Computers and Geotechnics 149 (2022) 104855S. Zhao et al.balance equations of energy and linear momentum in an updatedLagrangian framework:πππ,π‘ ππ,π ππ‘(1)πππ,π πππ πππ(2)physical field π (π₯π ) can be obtained by interpolating the correspondingvalues ππ carried on the material points in terms of the so-called particlecharacteristic function ππ (π₯π ) (Bardenhagen and Kober, 2004), i.e., ππ ππ (π₯π ),(7)π (π₯π ) πwhere π is the bulk mass density; π is the specific heat capacity; π isthe temperature; π‘ is the time; ππ is the heat flux; ππ‘ is a heat source orsink; πππ is the Cauchy stress tensor; ππ is the body force per unit of masspossibly performed on materials (e.g., gravitational acceleration), andππ is the acceleration term; π, π are sequential indices in {1, 2, 3} for 3Dor {1, 2} for 2D. Note that a latent heat term can be added in Eq. (1)to further consider the effect of phase transition on heat transfer. Toavoid unnecessary defocusing of the study, the detailed implementationis not presented in this paper. In future considerations, special attentionhas to be paid to the different thermal behaviors of coarse and finesoils during phase transition. Notably, the freezing point is widelyconsidered stationary for coarse soils during phase change, whilst it isregarded as a function of temperature for fine soils (Michalowski andZhu, 2006).According to the Fourierβs law for anisotropic heat conduction, theheat flux ππ can be written as (Onsager, 1931)such that the volume of a material particle is given byππ Note that ππ (π₯π ) satisfies the partition of unity property in the undeformed configuration (Bardenhagen and Kober, 2004) and a ββtop-hatββfunction is employed here. For the background grid, a physical fieldπ(π₯π ) can be also interpolated based on the corresponding value ππΌ atthe grid node πΌ, i.e., π(π₯π ) ππΌ ππΌ (π₯π )(9)πΌwhere ππΌ (π₯π ) is the grid shape function at node πΌ. Note that thesubscripts π or πΌ denote properties or functions associated with particleπ or node πΌ hereafter.The weak forms in Eqs. (5) and (6) can be rewritten into thefollowing integration forms over all particles] (π ) [ (π ) ππΌππ ππΌπ ππ‘π πΜπ β 1 ππΌπππΌππ ππ ππΌπ ππ½ π ππ½ ,π‘ (3)ππ πππ π,πwhere πππ is the thermal conductivity tensor.The following general boundary and initial conditions are considered for a typical heat conduction and mechanical problem:π (π‘) πΜon π€π(4a)π(π‘)π πΜπon(4b)π€ππ’π π’Μ ππππ ππ π‘Μππ€π’(4d)on π€π‘on(4e))π(π,π πππ π,π dπΊ πΊ πΊπ(π’)π,π πππ dπΊ π(π ) πππ,π‘ dπΊ πΊπ(π’)π πππ dπΊ πΊ πΊπ(π ) ππ‘ dπΊ π(π’)π πππ dπΊ π€π π€π‘π(π ) πdπ€Μ(5)Μπ(π’)π π‘π dπ€(6)πΌ πΌπ)π(ππΌ πππ ππΌπ,π ππππ ππ,ππ(10) π(π’)πΌπΌ π½ππ ππΌπ ππ½ πππ½ π πΌ π(π’)πΌ ππ(π’)πΌππ ππΌπ πππ πΌ π(π’)πΌ ππ ππΌπ π‘Μππ β 1ππΌππ ππΌπ,π πππππ(11)where π€π and π€π are the prescribed temperature and heat flux boundaries of the problem domain πΊ, respectively; πΜ and πΜπ are the prescribedboundary temperature on π€π and boundary heat flux on π€π , respectively; ππππ is the ambient or reference temperature; Eqs. (4a) and(4b) are Dirichlet (fixed temperature) and Neumann (fixed heat flux)boundary conditions, respectively, while Eq. (4c) is the initial conditionfor temperature distribution at the initial state. ππ is the boundaryoutward normal of the domain πΊ; π’Μ π and π‘Μπ are the prescribed materialdisplacement on π€π’ and boundary traction on π€π‘ , respectively; Eqs. (4d)and (4e) are Dirichlet and Neumann boundary conditions, respectively.Multiplying Eqs. (1) and (2) by a corresponding test function π(π )(with zeros on π€π ) and π(π’)(with zeros on π€π’ ), respectively, andπintegrating over the entire domain πΊ by application of integration byparts and Greenβs formula, the weak form formulations of the governingequations can be obtained as follows πΊππ½πΌ(4c)π (0) ππππ(8)ππ dπΊ. πΊπwhere β is the virtual boundary layer thickness serving for the boundary integration (Zhang et al., 2011); ππ is the mass of particle π; ππΌπ andππΌπ,π are the weighting and gradient weighting functions, respectively,defined asππΌπ 1π π dπΊππ πΊπ π πΌ(12)ππΌπ,π 1π π dπΊππ πΊπ π πΌ,π(13)Although several other GIMP variations have been proposed in theliterature for better accuracy, e.g., CPDI (Sadeghirad et al., 2011) andCPDI2 (Sadeghirad et al., 2013), the undeformed GIMP (uGIMP) (Bardenhagen and Kober, 2004) is adopted here as the macroscopic solverof the proposed multiscale framework for simplicity in implementationwithout losing generality.Due to the arbitrariness of the test functions, the weak forms givenby Eqs. (10) and (11) can be simplified into the following semi-discreteequations at node πΌ: πππ‘πΆπΌπ½ ππ½ ,π‘ πππ₯π‘(14)πΌ ππΌ2.2. Spatial discretization in GIMPπ½ Lagrangian material points and Eulerian background grid are twokey ingredients for MPM discretization of a continuum domain. TheGIMP formulation was proposed by Bardenhagen and Kober (2004) toovercome the potential cell-crossing issue in the conventional MPM.In the GIMP discretization, the continuum is spatially discretized intoa finite set of subdomains occupied by material points with a certaindomain for each. The integration over the entire domain πΊ governedby the weak forms in Eqs. (5) and (6) can be converted into thesummation of integration over each subdomain πΊπ of particles. AππΌπ½ πππ½ πππΌππ₯π‘ πππΌπππ‘(15)π½withπΆπΌπ½ ππππ₯π‘πΌ ππ ππΌπ ππ‘π ππππΌππ₯π‘ π3ππΌπ½ ππ ππ ππΌπ ππ½ π ππ ππΌπ πππ πππ ππΌπ ππ½ π(16)ππ ππΌπ,π ππππ ππ,π(17)ππΜπ β 1 ππΌππ ππππ‘πΌ πππ ππΌπ π‘Μππ β 1πππΌπππ‘ πππ ππΌπ,π ππππ(18)
Computers and Geotechnics 149 (2022) 104855S. Zhao et al.where πΆ and π are the consistent heat capacity matrix and mass matrix, respectively; π and ππ are heat and mechanical loads, respectively(the superscripts ββintββ and ββextββ denote internal and external loads,respectively). To facilitate the computation, the scheme of lumpedmatrix is employed, i.e., ππ ππΌπ(19)ππ ππ ππΌπππΌ πΆπΌ temperature given by Eq. (29) is the so-called remapped temperature,which is smoother than that given by Eq. (28) (Tao et al., 2016). Inthis work, the fluctuating particle temperature is tracked to update thenodal temperature, while the smooth particle temperature is taken asan input for the representative volume elements (RVEs). Detail will beintroduced in Section 4.In addition, the timestep should be chosen sufficiently small tomaintain numerical stability and convergence in the coupled thermomechanical system. In the proposed staggered coupling algorithm, boththe mechanical and thermal solvers adopt the same timestep satisfyingthe following constrains (Tao et al., 2016; Lei et al., 2021):ππsuch that,πππ‘πΆπΌ ππΌ,π‘ πππ₯π‘πΌ ππΌππΌ πππΌ πππΌππ₯π‘ πππΌπππ‘(20)ππ₯π‘ ππΈ π2.3. Temporal discretizationWe employ the Euler forward method to discretize the thermomechanical coupled system (i.e., the semi-discrete equations inEqs. (20)) in time such that the MPM solver works in an explicitmanner. Indeed, this explicit MPM in conjunction with the schemeof lumped matrix has been prevailingly adopted in the literature forits straightforward numerical implementation (de Vaucorbeil et al.,2020). In this scheme, the discrete equations for nodal temperature andvelocity are written as:(π‘)π₯π‘ππΌ(π‘ π₯π‘) ππΌ(π‘) ππΌ,π‘(21)(π‘)(π‘)π£(π‘ π₯π‘) π£ππΌ πππΌπ₯π‘ππΌ(22) πΌ(π‘) (π‘)ππΌπ π£ππΌ π(π‘) π₯π‘π(π‘)ππΌ πΌπfor PIC3. Thermo-mechanical coupling in DEM3.1. Thermal response of an RVE assembly3.1.1. Heat generated by frictionHeat can be generated due to friction dissipation at inter-particlecontacts during various granular flow processes. Note that heat canbe generated through different dissipation processes and mechanisms.Only sliding friction is considered here for simplicity as it has been reported experimentally to dominate the friction dissipation (Zhai et al.,2019). For a single timestep π₯π‘, the total amount of heat within anassembly due to friction dissipation is quantified by (π) (π)πΈπ ππ‘ π£π‘ π₯π‘(32)(24)πOne major difference between the FLIP and PIC methods is that theFLIP method uses the grid accelerations only while the PIC methoduses the updated grid velocities. Stomakhin et al. (2013) suggesteda combination of the FLIP and PIC methods by regrading PIC as adamping term as follows: (π‘) (π‘) ) (π‘) (π‘)((π‘)(25)π£ππΌ ππΌππππΌ ππΌπ π₯π‘ πΌπ πΌπΆ π£(π‘)π£(π‘ π₯π‘) π£ππ ππ πππΌwhere ππ‘(π) and π£(π)π‘ are friction (tangential force) and relative tangentialvelocity at contact π during the present timestep. Therefore, the heatsource is given by π (π)π 1 πΈπ(33)π π ππ₯π‘where π is the DEM iteration number for a given strain loading; π isthe volume of the assembly.πΌwhere πΌπ πΌπΆ [0, 1] is the PIC fraction. With grid damping πΌπ andparticle damping πΌπ , the damped particle velocity reads (π‘) (π‘) (π‘) (π‘)(π‘)π£(π‘ π₯π‘) π£ππ πππΌ ππΌπ π₯π‘ (πΌπ πΌπΆ πΌπ )π£(π‘)π£ππΌ ππΌπ (26)ππππ (πΌπ πΌπΆ πΌπ )πΌ3.1.2. Thermal conductivity tensorWe follow our previous study (Zhao et al., 2020) to constructthe fabric-based conductivity tensor for an assembly of non-sphericalparticles. The derivation is based on such a fundamental assumptionthat heat flows through an imaginary heat pipe joining the center ofeach contacted particle (heat reservoir) through the contact (anotherheat reservoir) as schematically illustrated in Fig. 1(a). Accordingly, athermal conductivity tensor πππ can be given asπΌand the particle position is updated with a general second-order FLIPformulation (Nairn, 2015) (π‘ π₯π‘) (π‘)π₯(π‘ π₯π‘) π₯(π‘)π£ππΌ ππΌπ π₯π‘ππππ πΌ ( (π‘) (π‘) )π₯π‘ (π‘) (π‘)πππΌ ππΌπ π₯π‘ (πΌπ πΌπΆ πΌπ )π£(π‘) (πΌπ πΌπΆ πΌπ )π£ππΌ ππΌπππ2 πΌπΌ(27)πππ Similarly to the FLIP and PIC methods on velocity update in themechanical part, two possible schemes can be formulated to update theparticle temperature, i.e., (π‘) (π‘)ππ(π‘ π₯π‘) ππ(π‘) ππΌπ ππΌ,π‘ π₯π‘(28)ππ(π‘ π₯π‘) ππ2 πππΌπΌπΌ(π‘) (π‘ π₯π‘)ππΌπ ππΌ(30)for thermal(31)ππwhere πΈ is Youngβs modulus, which can be estimated from odometertests for an RVE packing (see Section 5.2.2 for detail); π is an adjustablefactor, with a default value of 1; ππ is the minimum element size of amesh; π is the mean thermal conductivity, i.e., average of the diagonalterms of the thermal conductivity tensor πππ .π₯π‘ where the superscripts π‘ and π‘ π₯π‘ indicate the variables at the startand end of the processing timestep hereafter, respectively. For themechanical part, the movement of material points can be solved according to the kinematic fields of the background grid. Two directcandidate methods are considered here, i.e., the so-called FLIP (FLuidImplicit Particle Brackbill and Ruppel, 1986) method and PIC (ParticleIn Cell Harlow, 1964) method, where particle velocity is updated as (π‘) (π‘)(π‘)π£(π‘ π₯π‘) π£ππ πππΌ ππΌπ π₯π‘ for FLIP(23)ππ π£(π‘ π₯π‘)ππfor mechanicalπ (π) (π)1 ππ πππ π 1 πΌ (π) π(π)(34)where π is the volume of the assembly; ππ is the vector along the πthheat pipe; π is the branch vector joining the two adjacent particles atthe contact of the heat pipe, and πΌ is the thermal resistance per lengthof the heat pipe.We note that it is non-trivial to derive an elegant theoretical solutionfor the thermal conductivity tensor πππ of granular media (Choo et al.,2013). Porosity has been regarded as one of the key factors influencingπππ . The effective thermal conductivity has been frequently assumed to(29)πΌwhere the former uses only the incremental temperature of nodes,whereas the latter is a direct remapping of nodal temperatures. The4
Computers and Geotechnics 149 (2022) 104855S. Zhao et al.Fig. 1. (a) Heat conduction through an inter-particle contact; (b) thermally induced contact force due to particle expansion.where π (0)π is the initial principal length of a particle at the referencetemperature; π π is the current principal length of a particle at a temperature change π₯π with respect to the reference temperature; π½ is thelinear thermal expansion coefficient. As a consequence, the thermallyinduced change in particle profile yields an additional penetration πΏππ ,referring to Fig. 1(b).follow an empirical relation with porosity (Zhang and Wang, 2017),without consideration of the anisotropic nature of materials in anengineering setting, e.g., in geotechnical engineering. Further appraisalis needed to rigorously consider the various physical attributes in deriving a robust expression for effective thermal conductivity of granularmedia.Remarks: In the conventional TM modeling with pure DEM, e.g., (Nguyenet al., 2009; Choo et al., 2013), the inter-particle heat transfer has to bemodeled at the particle scale for heat flows with remarkable increase in computational cost. By contrast, in the present proposed TM coupling scheme,heat transfer is captured at the mesoscopic/RVE scale (the effect of fabricchange can be considered, e.g., on thermal conductivity tensor) and solved inMPM at the continuum scale, which helps to develop the homogenized modelwith TM coupling and significantly boost the computational efficiency.3.2.3. Thermally sensitive bond contact modelFor cemented granular media such as frozen soils in permafrostareas and gas hydrate-bearing soils in submarine settings, particlesare bonded together through the ice or ice-like cementation. Such icybonds are sensitive to temperature change which may cause phasetransformation. Such process of inter-particle bonds can be readilyconsidered via proper modification of the contact models (Brown et al.,2014; Shen et al., 2016). For simplicity yet without losing generality,we introduce the following thermally sensitive bond contact model thatgoverns the bond breakage upon heating:3.2. Mechanical response of an RVE assembly3.2.1. Basic contact modelDEM modeling of granular media commonly postulates a forceβdisplacement law in conjunction with Coulombβs friction conditiongoverning inter-particle contacts (Cundall and Strack, 1979). A simplelinear spring contact model is employed here to establish the relation between contact force and relative displacement for each pair ofcontacting grains as followsππ π ππ π’πππ₯ππ ππ‘ πΏπ’π‘ππ(35b)π‘where ππ and ππ are normal and tangential contact forces along thenormal πππ and the tangential π‘ππ directions at contact π, respectively,referring to Fig. 1(b); π₯ππ π‘ is the incremental tangential contact forceat the current timestep; ππ and ππ‘ are the normal and tangent contactstiffness, respectively; π’ππ is the penetration depth along contact normal, πΏπ’π‘π is the relative tangential displacement of the two contactingparticles at the current timestep. The Coulomb condition of friction isapplied to constraining the tangential contact force according to, π π‘ π π π (38) πΉπ‘ πΉπ‘π ,πΉπ‘π ππ πΉππ(39)where π½π is a tuned parameter, and ππ is a threshold for temperaturechange. Both π½π and ππ are assumed to be constant in the numericalexamples in this work. More elegant models will be investigated in ourfuture work.(36)where π is the coefficient of friction.3.2.2. Thermal expansion contact modelFor a dry cohesionless granular assembly, the thermally inducedstress within an assembly depends on expansion or contraction ofparticles caused by temperature change. For simplicity, the change ofparticle size is assumed to be governed by the following relation (Vargas and McCarthy, 2007; Zhao et al., 2017; Zhao and Feng, 2019):π π π (0)π (1 π½π₯π )πΉππ π½π ππ π where π½π is defined as the breakage strength coefficient with respectto normal contact stiffness ππ ; π is the average radius of the twocontacting particles; ππ is a threshold coefficient of the maximum shearforce at breakage with respect to the normal breakage force, whichis assumed independent of temperature. Once either condition of theabove inequalities is met, the bond breaks and can no longer sustaintension. Note that herein we only consider bond breakage subjectedto tension and shear, while neglecting bond failure caused by twistingand/or compression. The breakage strength coefficient is a function oftemperature π , which can be simply defined as{ π½ (π π )π π , if π ππ ,ππ π½π (40)0,otherwise(35a)π‘πΉπ πΉππ ,3.2.4. Periodic cell, deformation and stressAn RVE assembly is assumed to be sufficiently small to capturethe response of a material point from the macroscopic perspective andmeanwhile sufficiently large to yield a representative response withrespect to discrete grains. To reduce the boundary effect from rigidboundaries (e.g., rigid confining walls), periodic boundary conditionsare employed in the DEM simulations (Thornton, 2000; Yang et al.,2014; Radjai, 2018). Typically,
chemical and mining engineering (Nguyen et al.,2009). A better under-standing of the interplay between thermal and mechanical behaviors of granular media could provide crucial theoretical bases for the design, operation, and risk assessment of relevant applications and practices. The thermo-mechanical coupling not only manifests by direct be-