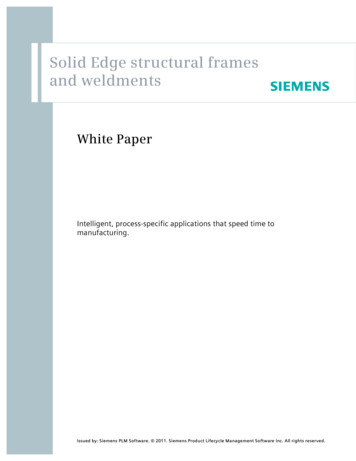
Transcription
Solid Edge structural framesand weldmentsWhite PaperIntelligent, process-specific applications that speed time tomanufacturing.Issued by: Siemens PLM Software. 2011. Siemens Product Lifecycle Ma nagement Software Inc. All rights reser ved.
W hite Paper Solid Edge structural frames a nd weldmentsContentsSolid Edge structural frames and weldments . 3 Solid Edge structural frames . 4 Creating the frame skeleton . 4 Building the 3D frame . 4 Create drawings with cut lists . 5 Solid Edge weldments . 6 Creation and selection of the weldment . 6 Surface preparation . 6 Weld bead creation . 7 Machining . 8 Drawings and documentation . 9 The Solid Edge advantage . 10 Conclusion . 11 Issued by: Siemens PLM Softwa re. 2011. Siemens Product Lifecycle Ma nagement Software Inc. All rights reserved.2
W hite Paper Solid Edge structural frames a nd weldments3Solid Edge structural frames and weldmentsSolid Edge software includes two process-specificapplications designed specifically to speed thecreation of rigid frame structures and weldments,both of which are commonly required for processequipment and mechanical machinery. Solid EdgeStructural Frames and Solid Edge Weldments are partof the core design capabilities of Solid Edge andfeature the same user-friendly process-orientedworkflows that have made Solid Edge the mostintuitive and productive solid modeling programavailable.Solid Edge Structural Frames and Solid Edge Weldments incorporate industry intelligence and use theterminology common to their disciplines. Embeddedengineering process knowledge, along with structured workflows, help you design frames andweldments much faster than with general-purposeCAD modeling tools. Streamlined modeling commands are tailored to the unique needs of the tasksfor maximum modeling speed.Solid Edge Structural Frames and Solid Edge Weldments are fully associative with Solid Edge assembly,part modeling and drafting capabilities. Becausethese applications are core capabilities of Solid Edge,users can leverage the exclusive Solid Edge cPDM anddesign management capabilities integrated directlyinto the CAD system to enhance collaboration, speeddecisions and ensure that users are always workingwith the most current version of a design.Solid Edge Structural Frames and Solid Edge Weldments act together to provide a workflow that speedsthe design, validation and documentation of weldedframes, making Solid Edge the best choice formachinery and process equipment design. This paperexplores how these applications are used and howmuch time they save compared to traditional designmethods for welded frames.Issued by: Siemens PLM Softwa re. 2011. Siemens Product Lifecycle Ma nagement Software Inc. All rights reser ved.
W hite Paper Solid Edge structural frames a nd weldments4Solid Edge structural framesSolid Edge Structural Frames is a process-specificworkflow that helps users develop rigid framestructures. An intuitive interface guides a userthrough the process of creating a 3D sketch of theframe skeleton, modifying default features, applyingstandard structural cross-sections and then automatically generating a 3D solid model of the frame.In addition to creating path segments from 2Dsketches, you can also use edges and other geometryfrom 3D parts in the assembly. You also can buildframes that have more than two frame membersjoined at a single vertex, choosing which of severalpossible solutions you want to use for mitering orcutting each of the frame members.Creating the frame skeletonBuilding the 3D frameThe Structural Frames workflow is initiated from theassembly environment. During this step, you createthe skeleton, which delivers a fully associative pathfor the frame section to follow. This step uses thesame tools that have been developed for the SolidEdge XpresRoute application, which let you specifythese paths quickly by defining 3D variationalsketches using specialized modeling aids, such asOrientXpres.Once a full or partial frame skeleton has beencreated, click the frames button. This command letsyou build the frame unit by choosing segments of theframe skeleton and selecting specific cross-sections toapply to those segments.OrientXpres is an interactive design aid that assists indrawing the 3D lines and arcs that the frame members will follow. Both straight and curved frame pathsare supported, so you can define frame componentsto be linear, curved or bent. As you draw line orarc segments, you can use OrientXpres to lockthe orientation of the segment parallel to an axisor plane.You can alsoassociate pathsegments toexisting assemblygeometry usingstandard SolidEdge relationships,such as parallel,perpendicular and colinear. As with 2D sketches, youcan define the size of the segments using dimensions, variables or other constraints to setrelationships, such as making two frame membersequal in length.After clicking on the desired path geometry, you caneither select a cross-section from the recently usedpulldown list in the SmartStep ribbon bar, or browsethe standard library components to specify the framecomponent type and size. Solid Edge is delivered witha complement of frame sizes in its Standard Partsapplication, with many more available in the optionalSolid Edge Machinery Library. Solid Edge supports themost common cross-sectional shapes, as well as manyothers such as T, hexagonal, Z and flats. Most of themajor standards (for example, ANSI, DIN, ISO, GB, JIS)for frame components are supported. You also canadd your own custom components to the library (seeSolid Edge Help for details on how to do this), anduse them in exactly the same manner.After selecting the relevant cross-sections, Solid Edgeautomatically creates the 3D model of the frame byapplying those sections to the chosen path segmentsand using the end treatment options specified in theinitial frame dialog. You have a number of differentend conditions to choose from – miter, butt1, butt2or none. The miter and none options are self explanatory. With a butt1 condition, the longest member willbe trimmed against (the shortest member will havematerial removed to suit). A butt2 condition is theIssued by: Siemens PLM Softwa re. 2011. Siemens Product Lifecycle Ma nagement Software Inc. All rights reser ved.
W hite Paper Solid Edge structural frames a nd weldmentsopposite, with the shortest member being trimmedagainst. You can mix and match frame componentsizes and shapes and their end condition treatments;any combination is possible.At this point, you can either click the finish button onSmartStep, or make any necessary edits to the pathstep, frame cross-sections or frame end conditions forthe set of components you have just created. If youfinish, you can then continue to add more framemembers to the path geometry. Subsequent frameswill be trimmed against existing frame components,giving you the ability to mix and match sizes andshapes of frame components in any combination.A nice feature of this workflow is the built-in supportfor automatic positioning. As you continue to addcomponents to the overall frame, those individualcomponents will analyze any existing, adjacent framecomponents to determine their correct location andorientation. If the automatically chosen position isincorrect, you can quickly shift the component usingthe n key to rotate in 90º increments, or the arrowkeys to shift upward, downward, left or right.5Create drawings with cut listsAs with all process-specific functionality in SolidEdge, full support is provided for creating drawings of3D frames. You can automatically create a parts listthat includes cut lengths for each component andchoose how you want to organize the list for downstream viewers in manufacturing or purchasing. SolidEdge also supports the concept of “rough cut” sizing,allowing you to specify an amount that will be addedto the exact length of frame. For example, the exactlength of a frame may be 36 inches, but you need theparts list to display 36 inches or the “rough cut”length. In this case, you simply specify a rough cutvalue of a half inch to be added to the exact length ofeach frame component.You can also select frame components and usestandard SmartStep methodology to click backthrough any of the creation steps to edit a frame thatyou have already created. In this way, you can add orremove path segments, select new frame crosssection types or sizes, or change end treatmentsglobally (for the whole frame) or locally (for a singlevertex). After making edits, the frame will immediately be recomputed to show the changes.Issued by: Siemens PLM Softwa re. 2011. Siemens Product Lifecycle Ma nagement Software Inc. All rights reser ved.
W hite Paper Solid Edge structural frames a nd weldments6Solid Edge weldmentsThrough close cooperative work with our customersand talking to welding engineers, we have developedSolid Edge Weldments to provide process-driven toolsto speed up time-to-manufacture. Solid Edge Weldments complements (but is not limited to) Solid EdgeStructural Frames by providing a process-specificworkflow for the efficient construction of weldments,using a frame assembly document as input. Aweldment is started directly within a Solid Edgeassembly where process-specific tools are used to addtrue weldment information, adding surface preparation features, defining weld bead features and weldcharacteristics, and specifying final post-weldfeatures. Weld bead and machining operations andweldment operations are organized in the nativeassembly tree within EdgeBar.companies estimate the cost of welding based onweld bead mass). As soon as the assembly is markedas a weldment, a process-specific toolbar is presented, for weld preparation, adding weld material andpost-weld machining operations.Surface preparationCreation and selection of the weldmentMany welded joints use weld preparation to strengthen them. On thin gauged materials such as sheetmetal, up to about 3mm thick, a simple gap of aboutthe material thickness is usually all that is required.On thicker materials different types of weld preparation are normal; ‘V’, ‘J’ and ‘U’ preps are useddepending on the material and the joint type. SolidEdge provides assembly feature tools, such aschamfer, cutout and swept cutout to create weldpreparation details on the edges where parts are tobe welded together. These do not affect the parts inthe original frame assembly document.The process begins by marking a Solid Edge assemblyas a weldment using the Weldment Assemblycommand. Because you remain in the assembly, youmaintain all the advantages such as color, styles,configurations, product structure and managed datain a single file. The weldment is assigned propertiesfor bead material, style and density. These propertiesare applied to the weld as they are created. Byassigning a material density, weight is automaticallyadded to the assembly, providing accurate masscalculations. Companies are able to use the weldbead mass calculations to help estimate costs (manyIssued by: Siemens PLM Softwa re. 2011. Siemens Product Lifecycle Ma nagement Software Inc. All rights reser ved.
W hite Paper Solid Edge structural fram es and weldmentsWeld bead creationSolid Edge provides many tools to easily create theweld bead material depending on the weld typerequired and joint preparation.Fillet welds The most common type of weld is thefillet weld. Following a simple process, all you have todo is choose the two faces that are going to bewelded together. Solid Edgeautomatically creates the familiartriangular shaped weld beadassociated with this weld type;predefined parameters for eachleg length and offset, size andstyle are used.Customized welds Not all welds are simply triangularin shape; some beads need to represent a specificcross-section, either because of the weld specificationor preparation type. Assembly feature tools –protrusion, revolved and sweep protrusions – areavailable so that users can define their required weldbead cross-section.Groove weld For joint types withshaped weld preparations, thegroove weld bead provides greatflexibility whereas other methodsdo not support such a bridging gap.You can quickly add weld beads tocomponents with complex boundaries or weldpreparation on both sides of the joint. The process forcreating a groove weld is simple – choose the faces toapply the weld, select the boundary where the weldpreparation is to be contained and the groove weld iscomplete. Additional extent options allow you tocontrol how the groove weld extends along the weld,or cross-sectional profile.7Compound weld Many welded joints consist ofmultiple weld beads or runs as they are sometimesknown, which overlay each other to strengthen ajoint. The compound weld bead command allowsdesigners to add welds on top of other weld beads,and then label them. When a compound weld islabeled, it canthen be extracted on thedrawing toprovide detailedannotations ondrawings.Stitch weld Where strength or gas tightness is not apriority, stitch welds are used to save time andmaterials. The Stitch Weld command provides adedicated tool to applystitch welds to joincomponents. Optionsallow you
with the most current version of a design. Solid Edge Structural Frames and Solid Edge Weld-ments act together to provide a workflow that speeds the design, validation and documentation of welded frames, making Solid Edge the best choice for machinery and process equipment design. This paper explores how these applications are used and howFile Size: 559KBPage Count: 12