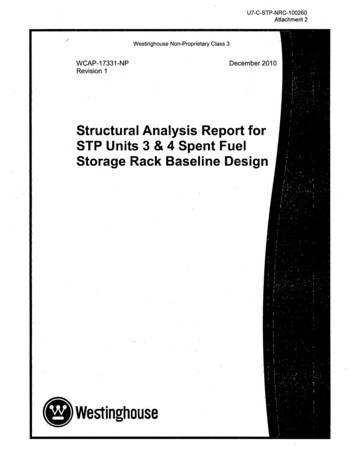
Transcription
U7-C-STP-NRC-100260Attachment 2Westinghouse Non-Proprietary Class 3WCAP-17331-NPRevision 1December 2010Structural Analysis Report forSTP Units 3 & 4 Spent FuelStorage Rack Baseline DesignWestinghouse
U7-C-STP-NRC-1 00260Attachment 2WESTINGHOUSE NON-PROPRIETARY CLASS 3WCAP-17331-NPRevision 1Structural Analysis Report for STP Units 3 & 4 Spent FuelStorage Rack Baseline DesignBrian Albert*Mechanical/Civil Design & Analysis IMatthew Coble*Major Reactor Component Design and Analysis-IDecember 2010Reviewer:Byounghoan Choi*Major Reactor Component Design and Analysis - ICharles A. Mance*Mechanical/Civil Design & Analysis IIApproved:Carl Gimbrone*, ManagerMajor Reactor Component Design and Analysis - I*Electronically approved records are authenticated in the electronic document management system.Westinghouse Electric Company LLC1000 Westinghouse DriveCranberry Township, PA 16066 2010 Westinghouse Electric Company LLCAll Rights ReservedWCAP-17331-NP.doc
U7-C-STP-NRC-1 00260Attachment 2WESTINGHOUSE NON-PROPRIETARY CLASS 3iiTABLE OF CONTENTSI2345678910IN TRO D UCTIO N .1-1TECHNICAL BACKGROUND . *. 2-1D E SIGN . !.3-1SEISMIC ANALYSIS METHODOLOGY .4-14.1TIM E H ISTO RY IN PUT .4-14.2MODELING METHODOLOGY .4-64.2.1Specific Modeling Details for a Single Rack .4-74.2.2Simulation and Solution Methodology .4-84.2.3Sim ulation D escription .4-84.2.4Conservatisms Inherent in Methodology .4-84.3KINEMATIC AND STRESS ACCEPTANCE CRITERIA . 4-124.3.1Introduction.4-124.3.2K inem atic Criteria .4-124.3.3Stress Limit Criteria .4-124.3.4Stress Limits for Various Conditions Per ASME Code . 4-134.4ASSUMPTIONS .4-14IN PU T DATA . 5-15.1RACK AND FUEL DATA .5-15.2STRUCTURAL DAMPING .5-15.3MATERIA L D ATA .5-1COMPUTER CODES .6-1AN ALYSE S . . 7-17.1ACCEPTANCE CRITERIA . .7-1RESULTS OF ANALYSES . 8-18.1SEISM IC IMPA CT LOAD S .8-18.1.1Fuel-to-R ack Im pact .8-18.1.2R ack-to-Floor Impact . . . 8-18.2RACK STRUCTURAL EVALUATION .8-18.2.1C ell Wall Stresses .8-18.2.2Level Screw Stress .8-38.2.3Weld Stresses . . . 8-78.2.4Baseplate Stress .8-88.2.5Support Plate Stress . 8-88.3DROPPED FUEL ASSEMBLY EVALUATION .8-98.3.1Drop O rientations .8-98.3.2Drop Locations .8-138.3.3Dropped Fuel Assembly Analysis Results . 8-138.4STUCK FUEL ASSEMBLY EVALUATION . . 8-14RESULTS AND CONCLUSIONS .9-1REFER EN C E S .I. 10-1WCAP-17331-NPDecember 2010Revision 1
U7-C-STP-NRC-1 00260Attachment 2WESTINGHOUSE NON-PROPRIETARY CLASS 311-1INTRODUCTIONThis report documents the structural analyses of the baseline spent fuel storage rack design for the SouthTexas Project Units 3 & 4 (STP 3&4). Revision 1 includes supplemental information added as a result ofthe U.S. Nuclear Regulatory Commission (NRC) Requests for Additional Information (RAIs). The racksare designed to store spent fuel assemblies in the spent fuel pool. The spent fuel pool is designed to hold31 stainless steel storage racks, which are made up of uniformly sized storage cells. The racks areconstructed in varying arrays of cells to maximize the number of storage cells available in the spent fuelpool. The total capacity of the spent fuel pool is 3,410 fuel assemblies. The basis for the analyses is thedesign requirements specified by the COLA in Part 2, Tier 2, Section 9.1, Revision 4 [1] and Tier 2,Appendix 3A, Revision 4 of the DCD [2]. As Revision lof this WCAP is a complete re-write, changebars have not been used.WCAP-17331-NPDecember 2010Revision I
U7-C-STP-NRC-100260Attachment 2WESTINGHOUSE NON-PROPRIETARY CLASS 322-1TECHNICAL BACKGROUNDThis report demonstrates the structural adequacy of the proposed STP 3&4 spent fuel storage racks underpostulated loading conditions. Analyses and evaluations follow the NRC Standard Review Plan 3.8.4,Revision 2 [5]. The analysis uses a finite element modeling code used in previous fuel rack licensingefforts. This report provides a discussion of the method of analyses, modeling assumptions, keyevaluations, and results obtained to establish that the spent fuel rack meets all structural integrityrequirements.WCAP-17331-NPDecember 2010Revision 1
U7-C-STP-NRC-1 00260Attachment 2WESTINGHOUSE NON-PROPRIETARY CLASS 333-1DESIGNThe layout of the spent fuel storage racks in the spent fuel pool is shown in Figure 3-1 and summarized inTable 3-1. The pool is populated with 31 spent fuel racks with a total capacity of 3,410 fuel assemblies.The storage racks are composed of individual storage cells made of []a.c thick austenitic stainlesssteel sheet. For this analysis, the cells have a center-to-center cell pitch of []a'C and an insidedimension of[]". - The storage cells are 190 inches tall and are welded to a base supportassembly as well as one another to form an integral structure.The base support assembly consists of a 1.5 inch thick stainless steel baseplate supported by levelingblock assemblies. The stainless steel leveling block assemblies allow the height of the support feet to beadjusted to level the rack during installation. The top of the baseplate is located 8.1 inches above the spentfuel pool floor. The spent fuel racks are free standing racks and are not anchored to the floor or walls ofthe spent fuel pool. Each spent fuel rack is attached to the neighboring spent fuel rack with tie-bars at thetop of the racks. Each side of a rack has a tie-bar; therefore, an internally located rack will have four tiebar assemblies. The tie-bars are included in the seismic analysis, but the detailed design and qualificationwill be completed as part of the final design. During seismic events, the racks may slide along the floorof the spent fuel pool.The neutron absorbing material, Boral 1, is attached along the length of the cell walls through the use ofthin gauge stainless steel wrapper plates. The wrapper plates are formed to create a small cavity and thenwelded to the cell walls. The Boral plates are then inserted into the cavity formed between the wrapperplates and the cell walls. The Boral plates are []a.c thick and completely cover the active fuelregion of the fuel. The top of the Boral plates are located []a*c below the top of the cells.Geometric details of the racks are shown in Figures 3-2 through 3-4. An overview of the construction andmaterials used in the STP 3&4 spent fuel storage rack is presented in Table 3-2 through Table 3-3. Thefuel assembly details are summarized in Table 3-4.Table 3-1: Spent Fuel Rack Summarya,c1.Boral is aregistered trademark of Ceradyne Inc. in the United States or other countries. All other brand, product,service and feature names or trademarks are the property of their respective owners.WCAP-17331-NPDecember 2010Revision 1
U7-C-STP-NRC-1 00260Attachment 2WESTINGHOUSE NON-PROPRIETARY CLASS 33-2Note: Dimensions in brackets are in meters.Figure 3-1: Spent Fuel Pool LayoutWCAP-17331-NPDecember 2010Revision I--. C
U7-C-STP-NRC-100260Attachment 23-3WESTINGHOUSE NON-PROPRIETARY CLASS 3a.cFigure 3-2: STP Spent Fuel Storage Rack Arrangement, 11 x 11 Fuel Storage Rack IsometricWCAP-17331-NPDecember 2010Revision 1
U7-C-STP-NRC-1 00260Attachment 2WESTINGHOUSE NON-PROPRIETARY CLASS 33-4I a.cFigure 3-3: Rack GeometryWCAP-17331-NPDecember 2010Revision 1
U7-C-STP-NRC-1 00260Attachment 2WESTINGHOUSE NON-PROPRIETARY CLASS 33-5-laxFigure 3-4: Rack GeometryWCAP-17331-NPDecember 2010Revision I
U7-C-STP-NRC-100260Attachment 2WESTINGHOUSE NON-PROPRIETARY CLASS 33-6Table 3-2: STP Spent Fuel Storage Rack Storage Cell Descriptiona.c1I4IiTable 3-3: STP 3&4 Spent Fuel Storage Rack Modulea,cTable 3-4: STP Spent Fuel Storage Rack Fuel Data-II-.14-WCAP-17331-NPDecember 2010Revision 1a,c
U7-C-STP-NRC-100260Attachment 2WESTINGHOUSE NON-PROPRIETARY CLASS 34SEISMIC ANALYSIS METHODOLOGY4.1TIME HISTORY INPUT4-1The safe shutdown earthquake (SSE) time histories are provided in the Westinghouse calculation note forthe generation of artificial seismic time histories [6]. The spent fuel layout drawing in Figure 4-1 detailsthe coordinate system for the seismic inputs from [6]. The x-axis is oriented along plane north, the y-axisis oriented along plane west, and the z-axis is oriented in the vertical direction according to the right-handrule. The response spectra used for creating the artificial time history are taken from node 100 in theDCD Tier 2, Appendix 3A, Revision 4 [2]. This node corresponds to the reactor building at elevation77.10 feet (23.5 meters). The base of the spent fuel pool is at 64.96 feet (19.8 meters), and the top of theracks is at 81.36 feet (24.8 meters). Therefore, the developed time history accounts for the wallamplification very near the top of the spent fuel racks.The acceleration versus time data for the x, y, and z directions are shown in Figure 4-2 through Figure4-4. Baseline corrected displacement time histories are developed using these accelerations. Thedisplacement versus time data for the x, y, and z directions are shown in Figure 4-5.Figure 4-1: Seismic Input Coordinate DirectionsWCAP-17331-NPDecember 2010Revision I
U7-C-STP-NRC-100260Attachment 2WESTINGHOUSE NON-PROPRIETARY CLASS 34-2a,cFigure 4-2: Artificial Acceleration Time History - Horizontal (X)WCAP-1733 1-NPDecember 2010Revision 1
U7-C-STP-NRC-1 00260Attachment 2WESTINGHOUSE NON-PROPRIETARY CLASS 34-3a,cFigure 4-3: Artificial Acceleration Time History - Horizontal (Y)WCAP-17331-NPDecember 2010Revision I
U7-C-STP-NRC-1 00260Attachment 2WESTINGHOUSE NON-PROPRIETARY CLASS 34-4a,cFigure 4-4: Artificial Acceleration Time History - Vertical (Z)WCAP-17331-NPDecember 2010Revision 1
U7-C-STP-NRC-1 00260Attachment 2WESTINGHOUSE NON-PROPRIETARY CLASS 34-5a,cFigure 4-5: Baseline Corrected Artificial Displacement Time HistoryWCAP-17331-NPDecember 2010Revision 1
U7-C-STP-NRC-100260Attachment 2WESTINGHOUSE NON-PROPRIETARY CLASS 34.24-6MODELING METHODOLOGYOnce a set of input excitations is obtained, a dynamic representation is developed. Reliable assessment ofthe stress field and kinematic behavior of the rack modules calls for a conservative dynamic modelincorporating all key attributes of the actual structure. This means that the dynamic model must have theability to execute concurrent sliding, rocking, bending, twisting, and other motion forms compatible withthe freestanding installation of the modules. Additionally, the model must possess the capability to affectmomentum transfers that occur due to rattling of fuel assemblies inside storage cells and the capability tosimulate lift-off and subsequent impact of support pedestals with the rack bearing pad or pool liner. Thecontribution of the water mass in the interstitial spaces around the rack modules and within the storagecells must be modeled in an accurate manner. The Coulomb friction coefficient at the pedestal-to-bearingpad and pool liner interfaces may lie in a rather wide range, depending on the design of those interfaces;and the model must be able to reflect their effect. In short, there are a l
pool. The total capacity of the spent fuel pool is 3,410 fuel assemblies. The basis for the analyses is the design requirements specified by the COLA in Part 2, Tier 2, Section 9.1, Revision 4 [1] and Tier 2, Appendix 3A, Revision 4 of the DCD [2]. As Revision lof this WCAP is a complete re-write, change bars have not been used.