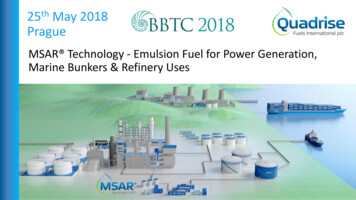
Transcription
25th May 2018PragueMSAR Technology - Emulsion Fuel for Power Generation,Marine Bunkers & Refinery Uses
Introduction to Quadrise Quadrise is the supplier of proprietary, proven MSAR technology.Industry participants: A low viscosity “synthetic HFO” is produced by blending heavyresidue streams without adding cutter, improving refinery margins. The technology and fuel are proven and verified at commercial scale. MSAR emulsion fuels are used as direct substitutes for HFO inpower and marine applications, and potentially refinery refuelling. Economic and environmental benefits for producer and consumer. IP is developed and protected jointly with Akzo Nobel and MSAR projects are being developed with major global companies. QFI plc is listed on the London Stock Exchange (AIM companies). Multiphase Superfine Atomised Residue2
OverviewQuadrise technology adds value to refineries and fuel oil consumersQuadrise licenses, operates & providesMSAR technology, additives & services toproduce a stable ‘Oil-in-Water’ emulsion fuelHow it works:Tiny droplets of extra-viscousheavy hydrocarbons are dispersedin water using proprietaryprocesses and additivesMSAR provides refiners withlow CAPEX, short cycle, upgradingsolutions for HFO poolKey benefits: Refinery yield improvement Water & chemicals replace cutters Blend ‘incompatible’ residue streams Simple, low risk implementationDelivers HFO consumerstangible cost savings &environmental benefitsKey benefits: Stable, lower cost fuelsynthetic HFO Enhanced combustion &lower emissions (NOx, PM)MSAR stands for Multiphase Superfine Atomised Residue3
MSAR Technology“Plug & Play” Refinery Technology“Semi-complex” RefineryAdditives 1%Premium fuelsCrudeResiduesBitumenSolid, viscous 70%residues Refinery residue streams fromVR to SDA pitch. Petchem reaction residues 1,000 – 100,000,000 cSt @ 100 CWater 29% Can be derivedfrom utility, wasteor stripped sourwater sourcesFuel OilWater &Additives12MSAR Unit3The blending hardware is based onproven asphalt emulsion systems.100 units worldwideFuel Oil Market1Oil residues are taken direct fromrefinery rundown lines and cooled toachieve the required viscosity ( 2001000cSt @ 100-200oC typically) forthe colloid mill.2Water, together withproprietary additives, isadded to the residue in ahigh-speed colloid millunder pressure.3The mixture is processed in the mill andcooled to provide a highly stable oil-inwater fuel oil equivalent ( 200cSt at50oC) that can be run down to existingfuel oil tanks.4
Project Timeline1-2 months3-4 months6-12 monthsScopingPilot TestingFEEDEPCOperationsRefinery residuestream identified.Pilot testing atQRF*, additiveformulationoptimized based onend-use applicationand product specs.Scope developedand a designprepared forimplementation.Quadrise provideclient training andexperience.Implementation/integration ofMSAR project inmodular, scalable,containerised units.Ongoing supportfrom Quadrise tomaintain optimumperformance.Conceptual designand feasibility study.A 6KBPD MSAR project costs 5m and isimplementedwithin 12 months.*QRF Quadrise Research FacilityMSAR installation at Cepsa San Roque Refinery5
vs. HFO (RMG)Water MSAR contains 30% water, resulting in areduced calorific value compared to HFO. Typically 50% more fuel required (factoredinto economics). Water along with micro droplet sizeenhances the combustion process.Density MSAR density is higher as residue based.Viscosity MSAR Viscosity is lower as it is a functionof the water in the bulk phase.Sulphur Like HFO, MSAR contains sulphur as afunction of the residue.Comparison of ISO8217:2010 marine residual fuel (RMG) versus MSAR CharacteristicDensity at 15 c, kg/m³Kinematic Vicosity at 50 c, mm²Flash Point cPour Point (upper)Winter Quality cSummer Quality cCarbon Residue, % (m/m)Ash, % (m/m)Water, % (v/v)Sulfur, % (m/m)Acid number, mg KOH/gHydrogen Sulfide, mg/kgVanadium, mg/kgSodium, mg/kgTotal Sediment Potential, % (m/m)Aluminium plus Silicon, mg/kgUsed lubricating oil (ULO)Zinc, mg/kgPhosphorus, mg/kgCalcium, max.max.max.max.max.max*CategoryISO-F-ISO Test MethodRMG 380991,0380,060ReferenceISO 3675 / ISO 12185ISO 3104ISO 2719Marine 080ISO 3016ISO 3016ISO 10370ISO 6245ISO 3733ISO 14597 / 8754IP 570 Part AISO 14597 / IP 501ISO 14597 / IP 501ISO 10307-2ISO 10478N/AN/A200,333,03,52,52,0350100N/A15151530IP 501/IP 470IP 501/IP 470IP 501/IP 470N/AN/AN/A* The fuel shall be considered free of ULO if one or moreelements Zn, P and Ca are below or at the specified limits.All three elements shall exceed the same limits before afuel shall be deemed to contain ULO.* at 100s -1N/A Notrelevant foremulsion fuel6
Economic drivers for MSAR Value is created via a significant refinery yield shift due toupgrading cutter from the fuel oil pool to the distillate pool.Traditional refinery process50%An MSAR refinery70%30%RefineryoutputHFOHFO example60% residue40% diluent30%RefineryoutputMSAR 70% residue30% water &chemicals20%Water & 1% chemicalsEvery barrel of high value premium fuel usedto create HFO is lost margin to the refineryHigh valuetransport fuelsHigh value fuels usedto dilute HFOResidualfuelsAn additional 20% of higher value fuel can be soldby the refinery at the market rate vs HFO value* Price of MSAR HFO on a per unit of energy basis7
Refinery economics (2H 18 example)MSAR vs HFO [ HFO value – distillate savings additive costs ] x Net Calorific Value AdjustmentGeneric Refinery Economics; Vacuum residue cut with LCO for 380cSt HFO vs Quadrise MSAR MSAR production per MSAR Unit 1000 mt/d350,000mt/yr MSAR % Resid in MSAR 70% 245,000mt/yr Residue feedMarket Prices (USD/MT)Gasoil, 0.1wt% S 632HFO 3.5%S 262at refinery gate Gasoil / Fuel Oil spread 370/mtRefinery Fuel Oil Blend Assumed /mtViscosity, cSt@50 Cwt %mt/yrShell V50CommentsHeavy Fuel Oil, 3.5wt% S262380100%410,62033.0Mitsui futures. MED FOB. 2020made from Cutter Stock (LCO)5376.540%165,62017.185% Market gasoil value assumedand Refinery Residue77250,00060%245,00043.7Netback value (HFO & LCO /t and blend ratio)Step 1 Derive the value of the residue per ton on a netback Basis, i.e. value of HFO less the cost of distillates (LCO)MSAR Blend Economics /mtRatio (wt%) /mt of MSAR Step 2 Calculate the cost of MSAR /t (ResidueRefinery Residue77x70% 54 water additives)OPEX (Water 29%, Additives 1%, etc)35x30% 35- typical range 25/mt (Power) - 35/mtMSAR Cost of Production (variable cost basis) 89(Marine)Step 3 Adjust MSAR value for lower NCV and compare HFO fuel savings on a “like for like” energy basisAssumptions: HFO NCV 40.8 GJ/mtResid NCV (GJ/mt) 39.5 GJ/mttherefore MSAR NCV 27.11 GJ/mtCost of MSAR on HFO basis 40.8 / 27.1x 89/mt 133/mt HFOMSAR cost normalised for NCV (HFO equiv.)Margin for MSAR vs HFO (normalised for NCV) 262 - 133 129/mt HFOStep 4 Calculate MSAR Margin (to be shared)( 129/mt HFO x 27.1 / 40.8) 86/mt MSAR x 350,000mt/yr MSAR 30 million/yr49% Discount vs HFO. ( /mt to be shared)Step 1 Derive the value of the residue per ton, based on value of HFO less the cost of distillates (LCO)Step 2 Calculate the cost of MSAR (residue water additives)Step 3 Adjust for lower calorific value and compare savings “like for like” vs HFO.Step 4 MSAR value to be shared, (assumed 50% to refinery) 8
Impact of MEPC 2020 on MSAR EconomicsCourtesy ofS&P Global Platts Positive for QFI and the MSAR fuel solution: Wider distillate – fuel oil ‘spreads’ create even stronger economics. High margins combined with low CAPEX, 5million for 6KBPD MSAR , and quick implementation, 12mths, result in 2 year payback providing low risk, short cycle projects. MSAR is compatible with ECGS (“scrubber”) so positive for End Users with EGCS as it enablesaffordable compliance with environmental standards. MSAR can be both a permanent or interim solution based on other upgrading projects.9
Economic & Environmental BenefitsBURNING HFO:1. Energy Savings MSAR is stored & transported at ambienttemperatures ( 25oC)2. Efficient CombustionWith MSAR :Tiny droplets ofresidue aredispersed inwaterMSAR : Complete Carbon burnout lower dust emissions less Black Carbon5-10 microndroplets3. Lower NOx Emissions Water reduces the combustion temperature 20% lower NOx emitted4. Lower CO2 Impact Considerable CO₂ emission savings of 6%CO₂ using EGCS vs. 0.5%S fuel.Source: Concawe Report 1/13R (EU Refineries) 201310
Cepsa MSAR Installation 6 KBPD MSAR system installed at the CEPSA 240 KBPD Gibraltar San Roque Refinery for Marine & PowerQuadrise responsible for MSAR system installation, commissioning, operations & quality controlMSAR system designed to supply Marine or Power end users, installed in 9 months for 5mProcessing visbreaker residue from a wide range of sweet and sour opportunity crudesProven, reliable, 24/7, continuous operation11
Our Focus on HFO ApplicationsSteam Boilers (Power & Utilities)Diesel Engines (Marine & Power) Significant worldwide emulsion fuel boiler experience. MSAR is proven in Wärtsilä 4-stroke diesel engines. Experience applied to MSAR improvements. JDA with Maersk commenced in 2008 to demonstrate MSAR use inlarge 2-stoke diesel propulsion engines. 60 million tons emulsion fuel fired: 50MWth to 770MWe Successful laboratory and land-based tests (2009-2013) leading tosea-borne 2014 “Proof of Concept” vessel tests. “Operational LONO Trial” with Cepsa & Maersk 2016/17. Interim LONO received from Wärtsilä for Flex Engine Types.Plus Cement Kilns,Fired Heaters etc 12
Global Applications SummaryPower Opportunities for KSA PowerGensupply 400-500KBPD HFO.Complementary Solutions Refinery heaters and boilers. National Oil Companysynergies to provide MSAR forMarine & Power. Selected upstream &petrochemical residueopportunities. MoA signed with JGCCorporation to develop MSAR projects in Japan and elsewhere. Supply into Middle East, Asia etc. Potential funding of emissionscontrol equipment.Marine Term supply options with bunkerbuyers to further improve scrubbereconomics. OEM (MAN & Wärtsilä) approvalsfor MSAR use alongside scrubbers.13
25th May 2018PragueMSAR - Emulsion Fuel for Power Generation,Marine Bunkers & Refinery UsesThank you / Děkuji- questions welcome!Further info available:www.quadrisefuels.com or info@quadrisefuels.com
Fuel Oil Fuel Oil Market Water & Additives 2 3 1 MSAR Unit Plug & Play Refinery Technology 70% Water 29% Additives 1% Can be derived from utility, waste or stripped sour water sources Oil residues are taken direct from refinery rundown lines and cooled to achieve the required viscosity ( 200-1000cSt @ 100-200oC typically) for the colloid mill.