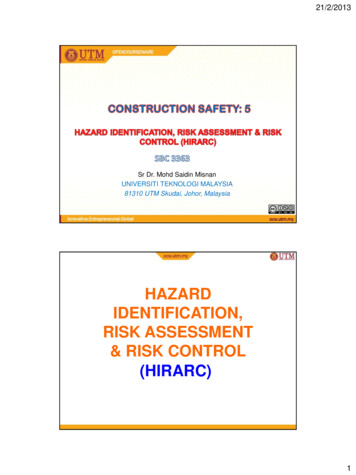
Transcription
21/2/2013Sr Dr. Mohd Saidin MisnanUNIVERSITI TEKNOLOGI MALAYSIA81310 UTM Skudai, Johor, MalaysiaHAZARDIDENTIFICATION,RISK ASSESSMENT& RISK CONTROL(HIRARC)1
21/2/2013OBJECTIVE The principles and practices of OSH HIRARCWhen to conduct HIRARC/Risk AssessmentsWhy HIRARC is importantHow to identify hazard and evaluate riskTo identify types of Hazard in work areaTo suggest Risk Controls to OrganizationTo implementing Risk ControlsTo review Risk ControlsContentSection 1Section 2Section 3Section 3.1Section 3.2Section 4Section 4.1Section 4.2Section 5: HIRARC – Definitions & Concepts: Process of HIRARC: Hazard Identification: Hazard Identification Tools: Types of Hazards: Risk Assessment: Analyzing Risk: Evaluation of Risk: Risk Control Approach2
21/2/2013OSH-MS (MS 1722:2003)Key Elements PolicyOrganizingPlanning And ImplementationMeasuring PerformanceAction for ImprovementWhy We Need OSH-MS Our Organization to be No. 1 Increase “Return of Investment”- employees, money , time . Safe work place3
21/2/2013How To Start Organization should have vision Commitment from management- right people- resource- timeHow To Start Should have internal auditManagement committee to review reportsExternal auditSpecific organization policy- hazard specificEmployee’s participation - meeting, trainingSafety as basic training4
21/2/2013Introduction to HIRARC Principles used in workplace to managesafety and health. Section 15 (2)(a) of OSHA 1994:which reads “ the provision andmaintenance of plants and systems of workthat are,so far as is practicable, safe andwithout risks to health”Overview Of HIRARC Definition of HazardsClassification of HazardsPotential sources of HazardsBasic components of Risk Management5
21/2/2013Purposes of HIRARC To identify all the factors that may cause harm toemployees and others (the hazards) To consider what the chances are of that harmactually befalling anyone in the circumstances of aparticular case and the possible consequences thatcould come from it (the risks) To enable employers to plan, introduce and monitorpreventive measures to ensure that the risks areadequately controlled at all times.SECTION 1HIRARCDefinitions and Concepts6
21/2/2013What is a Hazard?Source or situation with potential for harm in termof:i. Human injuryii. Ill healthiii. Damage to propertyiv. Damage to workplace environmentv. Or combination of theseWhat is a Risk?Combination of the likelihood andconsequence(s) of a specifiedhazardous event occurring.7
21/2/2013Risk – 2 Elements Likelihood that a hazard may occur(probability). Consequence(s) of the hazardousevent (severity).Definition HazardA source or a situation with a potential for harm tohumans, property and damage of environment or acombination of these. DangerRelative exposure to hazard. RiskA combination of likelihood of occurrence andseverity of injury or damage.8
21/2/2013What is risk assessment?Overall process of estimating themagnitude of risk and decidingwhether or not the risk is tolerable.Risk ControlMeasure taken to eliminate ormitigate the identified risks.9
21/2/2013Other Definitions Tolerable risk – risk that has been reduced to alevel that can be endured by the organizationhaving regard to its legal obligations and itsown OSH policy. Interested party – individual or groupconcerned with or affected by the OSHperformance of an organization.The Process of Risk ManagementClassify Activities(Work, Product, Services)Identify HazardAssess The RiskRisk ControlReview Risk Control10
21/2/2013Risk ManagementRisk Management describes the total procedureassociated with identifying a hazard, assessingthe risk, putting in place control measures, andreviewing the outcomes.Planning of HIRARC Ongoing HIRARC activities HIRARC Covers:- Routine and non-routine activities- Activities of all personnel including nonemployees (contractors, visitors)- Facilities at the workplace11
21/2/2013HIRARC -Planning & ImplementationFEEDBACK &ACCIDENT &COMPLAINNEAR ITTRANINGPOLICYSAFETYCOMMITTEEMANAGEMENT PROGRAMSECTION 2Process of HIRARC12
21/2/2013When to Conduct HIRARC For situation: Where hazard appear to pose significant threat Uncertain whether existing controls are adequate Before implementing corrective or preventivemeasures By organization intending to continuously improveOSHMS.HIRARC Process – 3 Basic Steps1. Identify Hazard2. Estimate risk from each hazard Probability of occurrence Severity of harm3. Decide if risk is tolerable.13
21/2/2013Why is HIRARC Important? Legal obligations (certain countries). To determine whether existing or plannedcontrols are adequate. “Risks should be controlled before harmcould occur”.Criteria for HIRARC ProcessClassify work RepresentativeIdentify HazardsPrepare Risk Control Action Plan (if necessary)ReviewRisk AssessmentImplement14
21/2/2013Classify work activitiesPossible ways. geographical or physical areas within/outsidepremises. Stages in production/service process Not too big. E.g. building a car Not too small. E.g. fixing a nut Defined task- e.g. loading, packing, mixing, fixing the doorWork activities Information Requirement Tasks carries out- duration & frequency- Site/location- Who involved/affected- Written system of work Services used- Compressed air, steam Type of material handled Plant/machinery used Distances/heights materialto be moved Tolls/equipment used Acts/Regulations/COP MSDS/CSDS Reactive monitoring data Advice from specialist15
21/2/2013Risk AssessmentDetermine riskMake a subjective assessment of risk associatedwith each hazard assuming that planned orexisting controls are in place.Decide if risk is tolerableJudge whether planned or existing OSHprecautions (if any) are sufficient to keep thehazard under control and meet legal requirements.Prepare risk control action plan (if necessary)Prepare a plan to deal with any issues found by theassessment to require attention.Organizations should ensure that new and existingcontrols remain in place and are effective.16
21/2/2013ImplementExecute the risk control plan.Monitor the effectiveness of the plan.ReviewRe-assess risks on the basis of the revisedcontrols.Check that risks will be tolerable.17
21/2/2013SECTION 3HAZARDIDENTIFICATIONHazard Identification To keep workplace safe and healthy.-employers should make sure there are nohazards to which employees could be exposed. Employers should look for hazards in advanceas part of their risk management plan toprevent potential hazards.18
21/2/2013Classify Work ActivitiesIdentify HazardsIdentify HazardsIdentify all significant hazards relating toeach work activity.Consider who might be harmed and how.19
21/2/2013Hazards Identification1. Is there a source of harm?2. Who could be harmed?3. How harm could occur?Identify HazardsGeneral (Qualitative) methods1. Previewing legislation and COP2. Using hazard checklist3. Conducting survey (audit), observation4. Assessing competency of personnel5. Analyzing reactive data (previous incidents data)6. Analyzing work process7. Through consultation with employees8. MSDS/CSDS9. Seeking advice from specialist10. OSH Journal / publications20
21/2/2013SECTION 3.1HAZARDIDENTIFICATIONTOOLSQuantitative Methods Hazard and Operability Study (HAZOP) Failure Mode and Effects Analysis(FMEA) Job Safety Analysis (JSA) Fault Tree Analysis (FTA)21
21/2/2013HAZOP To identify hazard in process and operabilityproblems. To study effects of deviation from processdesign condition. It takes a representation of a system andanalyses how its operation may lead to anunsafe deviation from the intent of the system.HAZOP22
21/2/2013HAZOPGuide Words None of . More of . Less of . Part of . As well as . Reverse . Other than .FMEAFMEA is a systematic approach to; Recognize and evaluate the potential failure of aproduct/process and the effects of that failure. Identify actions that could eliminate or reducethe chance of potential failure occurring. Document the entire process.23
21/2/2013Types of FMEAAll FMEAs focus on the design, be it product orprocess: Design of FMEA (of product) Process FMEA (of process)FMEASystemComponentFailure ModeFailure EffectScrubberWater pumpInadequatewater flowIncreasedenvironmentalpollution24
21/2/2013Where are FMEA’s currently used? Aerospace- Complex systems, processesand productsLow volume manufacturer Automotive - Complex systems, processesand productsHigh volume manufacturerWhen are FMEA applied? During the Advanced Product Quality PlanningProcess (APQP). Design FMEA applied during the product designand development. Process FMEA applied during process designand development.25
21/2/2013JSA Ideally, all jobs should be subjected to JSA. Usually useful for non routine activities.JSA basic procedure Select job to be analyzed Define the scope of the job Organize the job into sequential logical steps Observe each job step to determine the hazards Develop preventive measure to eliminate the hazards26
21/2/2013JSAFTA Shows the relation between system failure- a specific undesirable event in the system, andfailures of the components of the system Technique based on deductive logic, using“AND” and “OR” gates An undesirable event is first defined and casualrelationships of the failures leading to thateventare then identified Based on factual approach27
21/2/2013FTASECTION 3.2HAZARDTYPES28
21/2/2013Safety LevelsPreventionControlProtectionMitigation Mechanical Integrity Predictive/preventivemaintenance Operator training Human factors Impact barriers Adequate procedure AutomaticProcess controlsystem Manual controls On-line spares Backup systems Alarms Operator intervention Interlocks, trips Emergency shutdown Last resort controls Emergency relief Ignition source control Emergencyresponse Sprinkler, deluge Dike, trench Blast wall, barricade Water curtain Personal ProtectiveEquipmentHazardMaterial/energycontained andcontrolled duringnormal operation Toxicity Flammability Reactivity Elevated pressureetc.CauseInitiating event ofprocess upset;start of accidentevent sequence Mechanical failure Procedural error External force Fouling etc.DeviationExcursion beyonddesign/operatinglimits No flow High temperature Low level Impurities Wrong material Step omitted etc.AccidentalEventLoss ofcontainment ofprocessmaterial/energy Fire Explosion Hazardous material Release etc. Other energyreleaseImpactSeverity ofconsequences;losses Illnesses/Injuries death Propertydamage businessinterruption Environmentaldamage etc.Classification & Potential Sources of HazardsClassificationExample of HazardsMechanical - Sharp points & edges, overload.Electrical- Insulation damaged or cover brokenBiological- Exposed, airborne/blood bornemicroorganism.Chemical- Expose to carcinogens chemicalErgonomics- Expose to unnatural posturesPsychological - Stress or violent at workplace.29
21/2/2013Classification of Hazards inconstruction ChemicalErgonomicsSOURCES OF HAZARDSManMachineryMaterialsMethodMediaUnsafe actsInstallation, layout and design of equipmentSubstances such as chemicals and gases usein the workplaceThe way people carry out their workWorkplace condition i.e. air quality,ventilation, lighting, noise, vibration etc.30
21/2/2013Broad Categories of Hazards To facilitate hazards identification, useful tocategorizes hazards in different ways, e.g. bytopic; Chemical Physical Biological Ergonomics Psychosocial Mechanical Electrical MachineryPhysical HazardsPHYSICAL Noise/Vibration Electrical Extreme Temperature(Heat/Cold) Fire/Explosion Radiation Machinery/Equipment Height/Gravitational Confined Space Slip/Trip/Fall Vehicles Water31
21/2/2013Chemical HazardsCHEMICAL Very ToxicToxicCorrosiveHarmfulIrritant ExplosiveOxidizingExtremely FlammableHighly FlammableFlammableBiological HazardsBIOLOGICAL Animals– Wild Dogs , Snakes, Scorpions Plants- Poisons, irritants, Rashes Bacteria– Legionella Viruses– Influenza, HIV, Hepatitis Yeast– Cryptococcus Fungi– Tineas Parasites – Ticks, Gardia,32
21/2/2013Ergonomics HazardsERGONOMIC Repetitive Work - Prolonged Similar Task Manual Handling - Lifting, Pulling, Pushing, Twisting Computer Works - Sitting Posture, Eyes Strain Lighting- Adequacy of Light Ventilation- Indoor Air QualityPsychosocial HazardsPSYCHOSOCIAL Shift work- Prolonged night duty Stress- Multifactor Violence- Individual, Group Harassment- Sexual, Bullying33
21/2/2013HazardsClassification andPotential Sources of HazardsClassification ofHazardsExample of Potential Sources of HazardsMechanicalPinch points, sharp points and edges, overloador force a tool beyond its capabilities and grindingwheel without guardElectricalElectrical cord insulation damaged, electrical faceplate or cover broken or missing and fan cordinsulation pulled looseBiologicalExposed to airborne and blood borne viruses,bacteria and fungus34
21/2/2013Classification andPotential Sources of HazardsClassificationof HazardsExample of Potential Sources ofHazardsChemicalExposed to carcinogens chemicals,sensitizers and corrosive chemicals.ErgonomicsRepeated exposure to unnaturalpostures and unnatural movement,wrong design of workstation, tools andtask.Stress, sexual harassment and violent atwork.PsychologicalSECTION 4RISKASSESSMENT35
21/2/2013Classify Work ActivitiesIdentify HazardsRisk AssessmentDetermine RiskRisk Likelihood X SeverityLikelihood : likelihood the specified hazardous eventoccurringSeverity : consequence(s) of specified hazardous eventoccurring36
21/2/2013SECTION 4.1ANALYZING RISKLikelihood of Occurrence Consider-The availability of control measures- The existing control measures- Likelihood of failure of the control measures- Legal requirements and Code of Practicecovering controls of specific hazards37
21/2/2013Likelihood of Occurrence Consider:- No. of personnel exposed- Frequency & duration of exposure to hazard- Failure of services (electricity, water)- Failure of machinery & safety devices- Protection afforded by PPELikelihood of Occurrence Consider unsafe acts by personnel who- unaware of hazards- do not have knowledge or skills to do the task- underestimate risks- overlook safety procedures Establish the ranking. Example;- Very unlikely- Unlikely- Likely- Most likely- Certain38
21/2/2013TIPS .Factors for consideration in a workplace risk assessment. Maintenance: Maintenance of structure, equipment,systems, 5S etc. Environmental Factors: Ventilation, Temperaturecontrol, Lighting, 5S, Room dimensions and space,workstations, seating etc. Structural Features: Floor & traffic routes, transparentwindows & doors, gates, escalator etc.TIPS . Fire Protection Emergency Procedure Vehicle Movements Electrical Installations and Appliances Information, Instruction, Training and Supervision39
21/2/2013TIPS .Factors for consideration in a work equipment riskassessment. Suitability Maintenance Specific Risk- Only be used by designated and trained user. Information,Instructions and Training High or very low temperatureTIPS . Controls- Stop controls, emergency stop controls, controlsetc. Stability Lighting Markingsand Warnings Sign40
21/2/2013TIPS .Factors for consideration in a health risk assessment. Substances or type of substances Effects of the substances Location and form (gas, fumes, mist etc.) ExposureDuration (including OSHA requirements) Storage Requirements Air Monitoring & Health Surveillance Requirements Information, Instruction and TrainingTIPS .Factors for consideration in a noise riskassessment. Noise exposure records- Noise mapping, Audiometric Test etc. Action taken Noise control programmes Information, Instruction and Training41
21/2/2013Likelihood of OccurrenceVery unlikely(1)Unlikely(2)Likely(3)Most Likely(4)The probability tohappen isextremely small( 1% )Could happen,however very rare( 1 – 9% )Chances tohappen isrelatively high( 10 – 59% )Can happenfrequently( 60 – 100% )Severity of Harm To establish potential severity of harm, consider- part(s) of the body likely to be affected- nature of harm- nature of property damage- establish the ranking. Example;- Negligible- Minor- Major- Critical- Catastrophe42
21/2/2013Severity of HarmRisk LevelNegligible(1)Nature of InjuryNature of PropertyDamageFirst aid onlyUnnoticeable damageMinor(2)Medical treatment,OutpatientDamage with repair cost RM1KMajor(3)Hospitalized, disablinginjury, recoverableSignificant damage withrepair cost RM1K but RM50,000Critical(4)Permanent Disability,Single casualty, MultiplecasualtyHeavy damage with repaircost RM50K but RM0.5M; or more Damagecost RM0.5MSECTION 4.2EVALUATIONOF RISK43
21/2/2013RISK RATINGRisk Rating Existing Control Measure (ECM) XFrequency (F) X Likelihood (L) XSeverity (S)Likelihood : likelihood or probability that an accident orincident could occurSeverity : consequence(s) that an accident or incidentcould occur (in terms of injury, damage or loss)Jadual : Ukurtara kemungkinan (kualitatif)TAHAPKEMUNGKINANKETERANGAN4Sangat mungkinKejadian boleh berlaku dengan kerap(setiap hari)3MungkinKejadian boleh berlaku sekali-sekala(setiap minggu)2Tidak mungkinKejadian boleh berlaku tetapi jarang(setiap bulan)1Sangat tidak mungkinKejadian boleh berlaku tetapi kemungkinan tidak(setiap tahun)44
21/2/2013Jadual : Ukurtara keterukan (kualitatif)TAHAPAKIBATKETERANGAN1Kecederaan yangboleh diabaikanKecederaan hanya memerlukan pertolongancemas di tempat kerja/saja kemalanganhampir2Kecederaan ringanCedera atau sakit yang memerlukan cutidaripada kerja (maksimum 4 hari)3Kecederaan terukHilang upaya sementara atau cuti sakitmelebihi 4 hari4KematianKematian atau hilang upaya kekalJadual : Jadual Risiko ggiTinggiSederhanaKecederaan Teruk3TinggiTinggiSederhanaRendahKecederaan Ringan2TinggiSederhanaSederhanaRendahKecederaan yangBoleh Diabaikan1SederhanaRendahRendahRendahFormula Penaksiran Risiko:Risiko Akibat x Kemungkinan45
21/2/2013RISK jor injuriesHIGHHIGHMEDIUMMEDIUMMinor gible injuriesNomogramNomogram for analyzing risk and cost justification (from G. F.Kinney andA. D. Wiruth, Practical Risk Analysis for Safety Management).46
21/2/2013Risk AssessmentGather information abouteach hazard identifiedHow many people are exposedto each hazard and for howlongUse the information toassess the LIKELIHOOD andCONSEQUENCESof each hazardsUse a risk table to work out theRISK associated with eachhazardsHow LIKELY is it that a hazardous event or situationwill occur ? Very likely- frequently Likely- Occasionally Unlikely- happen but only rarely Highly unlikely - happen but probablynever willWhat might be the CONSEQUENCES of a hazardousevent or situations Fatality Major injuries (normally irreversible) Minor injuries ( normally reversiblerequiring several days off work ) Negligible injuries ( First Aid )Is the RISK tolerable ? IF YES ! Leave them alone, But need MONITORING . IF NO !– Need CORRECTIVE /PREVENTIVE MEASURES.47
21/2/2013Actions & Recommendations All related statements should be madeWith no cost restrainsShould be reviewed every 4 monthsNeed management supportRisk Assessment Is the process of evaluating the risk tosafety & health from hazards at workTypes- Qualitative- Semi-quantitative- Quantitative48
21/2/2013How To Assess Risk1) Look for the Hazards2) Decide who might be harmed & how3) Evaluate the risk and check what isdone to prevent it from happening 4) Record finding 5) Review assessment and revise it ifnecessaryTypes of Risk Assessment Qualitative - (Use Risk Matrix)-table scales for likelihood and severityFatalityMajor injuriesMinor injuriesFirst aid or near misses49
21/2/2013Types of Risk Assessment Based on statisticLikelihood Very likely Likely Unlikely Highly UnlikelyQualitative Risk umMediumLowLowFirst Aid/N/misses50
21/2/2013Semi-Quantitative Risk AssessmentSeverity Categories1. First Aid2. Less than 4 days M/C3. More than 4 days M/C4. Fatality & Permanent DisabilitySemi-Quantitative Risk AssessmentLikelihood Occurrence1. Yearly2. Monthly3. Weekly4. Daily51
21/2/2013Semi-Quantitative Risk 4First Aid11234 4 Days MC22468 4 Days MC336912Fatality &PermanentDisability4481216Quantitative Risk Assessment In cases where hazards are numerous and complexeg; Chemical process plant Should have Job Safety Analysis (JSA)- describe job in less than 10 steps- List things that can go wrong- eg; Changing a Car Wheel52
21/2/2013SECTION 5RISK CONTROLAPPROACHClassify Work ActivitiesIdentify HazardsRisk AssessmentPrepare risk control action plan53
21/2/2013Selection of Risk Controls Eliminate hazards Substitution- Using less hazardous chemicals Engineering Control- Isolation- Safety switch- Adapt work to individual- Local exhaust ventilation (LEV)- Water spray- Machine Guarding- Detection system- Enclosure / closed systemSelection of Risk Controls Administration Control- Planned maintenance- Emergency preparedness and Response (ERP)- Training – on work instruction, PPE, ERP, safehandling etc.- Competency requirement- Signage- Procedure, work instruction- Medical Surveillance- Supervision- Hygiene practice54
21/2/2013Selection of Risk Controls PPE as last resort- Safety helmet- Safety shoes- Body harness- Protective clothing- Goggle- Face shield- Mask/Respirator – dust, vapor, fume, gas- Glove- Ear plugSelection of Risk Controls55
21/2/2013Classify Work ActivitiesIdentify HazardsRisk AssessmentPrepare risk control action planReview adequacy of action planReview adequacy of action plan Tolerable risk achieved? New hazard created? Is it cost effective? Control practical?56
21/2/2013When to Review HIRARCThe HIRARC will be reviewed and maintained as follows: As part of the annual management review process As a consequence of any significant changes to theorganization’s activities, products or services As a consequence of any relevant changes to theregister of applicable legislation As a consequence of feedback from nonconformances identified during internal or externalaudit processManaging HIRARC Incorporate into OSH objectives Continuing process- Feedback loop from subsequent experience toamend HIRARC, if necessary Proactive measure, not reactive. Review at a pre-determined time or period57
21/2/2013Actions & Recommendations EL- EliminateSL- SubstituteISIsolationEC- Engineering ControlAC Administration ControlPPEPersonal Protection EquipmentActions & RecommendationsEg;EL - stop work, cover hazard SL - use other route, other material.IS - put up temporary barrier, EC - construct permanent wall,.AC - put up notice, job rotation, PPE - gloves, respirator, 58
21/2/2013The Process of Safety RiskManagementStartClassify Activities(Work, Product, Services, Activities)Identify HazardsDetermine Risk*/Impact*Risk Harm X LikelihoodDecide if Risk is TolerableDecide if Impact is SignificantPrepare Risk Control Action PlanReview Adequacy of Action PlanConclusionHazard identification, risk assessment, control andreview is not a task that is completed and then forgottenabout.Hazard identification should be properly documentedeven in the simplest of situationsRisk assessment should include a careful assessment ofboth likelihood and consequence. Control measuresshould conform to the recommendations of the hierarchyof control.The risk management process is an on going one.59
21/2/2013Terima KasihBe Safety Minded Be Safety Smart,Think of Safety Before You Start.60
Defined task - e.g. loading, packing, mixing, fixing the door Classify work activities Tasks carries out - duration & frequency - Site/location - Who involved/affected - Written system of work Plant/machinery used Tolls/equipment used MSDS/CSDS Services used - Compressed air, steam Type of material handled