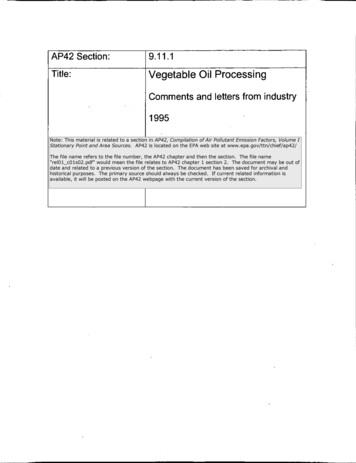
Transcription
AP42 Section:9.11.ITitle:Vegetable Oil ProcessingComments and letters from industry1995Note: This material is related to a section in AP42, Compilation of Air Pollutant Emission Factors, Volume IStationary Point and Area Sources. AP42 is located on the EPA web site at www.epa.gov/ttn/chief/ap42/The file name refers to the file number, the AP42 chapter and then the section. The file name"rel01 c01s02.pdf" would mean the file relates to AP42 chapter 1 section 2. The document may be out ofdate and related to a previous version of the section. The document has been saved for archival andhistorical purposes. The primary source should always be checked. If current related information isavailable, it will be posted on the AP42 webpage with the current version of the section.
MIDWEST RESEARCH INSTITUTESuite 350401 Harrison O a k BoulevardCery. North Carolina 27513-2412Telephone (919) 6774249FAX (919) 6774065Date:May 20, 1996Subject:Site Visit - - CargillEmission Factor Documentation for AP-42, Section 9.11.1EPA Contract No. 68-D2-0159;MRI Project No. 4602-03From:Tom LappTo:AP-42 Section 9.11.1 Project FileI.PurposeThe purpose of the visit was to briefly review commentsfrom the National Oilseed Processors Association (NOPA) and toconduct a walking tour of the soybean crush plant. Thisinformation will be incorporated into the revision of thebackground report and AP-42 Section 9.11.1, Vegetable OilProcessing.11.Place and DateCargill, IncorporatedRiver Road, Box 2309Fayetteville, North Carolina28302August 2, 1995111.AttendeesNationaPOilseed Processors AssociationDavid C. AilorDirector of Regulatory AffairsWashington, DCCarsill, Inc.Ron MoellerAssistant General SuperintendentOperations and EngineeringMinneapolis, MNTom RichardsonPlant SuperintendentFayetteville, NC
U. S. Environmental Protection AsencyDallas Safriet, EFIGRon Ryan, EFIGRoy Huntley, EFIGMidwest Research Institute (MRIITom LappIV.DiscussionThe visit as held primarily to conduct a walking tour ofthe facility in order to observe the actual processing steps inoperation. Prior to the tour, a brief meeting was held todiscuss general information on the soybean processing industryand to review suggested NOPA process diagrams for incorporationinto the final report. This discussion presents information onthe soybean processing industry and a description of the refiningof edible soybean oil. The review of NOPA diagrams consisted ofa discussion of process flow diagrams previously submitted to EPAby NOPA. Copies of the annotated diagrams are attached to thismemorandum.A.General InformationGenerally, the soybean industry annually processes 1.1. to1.3 billion bushels of soybeans. For 1995, most plants areoperating at about 70 percent of capacity. The Cargill plant atFayetteville is one of the larger plants in the U.S. and is inthe top 20 percent in terms of production capacity.For most plants, there have not been a lot changes overthe past 15 years and those changes that have occurred were theresult of EPA regulations or the increase in energy costs.During this 15 year period, there has been a move from the use ofdeep bed extractors towards shallow bed extractors. Also,changes have occurred in the desolventizing/toaster (DT) systems.Generally, plants do not change control devices without anincrease in capacity.In conventional soybean processing plants, there is noproduction of soybean meal for human consumption (white flakeproduction). Only about 8 plants in the U . S . have flashersystems for white flake production. These flasher systems usesuperheated hexane in the flake desolventizing step and do notuse meal dryers.B.Soybean Oil RefiningCrude soybean oil contains free fatty acids, phosphoruscompounds, protein fines, and triglycerides. The crude oil canbe either treated directly with caustic or undergo an optional
step to degum the oil, which removes the lecithin. Aftertreatment with caustic, the o i l i s centrifuged to separate theaqueous refining by-product lipid from the o i l . This lipidsolution contains protein fines, phosphorus compounds, somesaponified triglycerides, and sodium salts of the fatty acids.Following separation of the lipid, the oil is washed with waterand centrifuged to remove some of the remaining saponifiedtriglycerides.The refined oil is then bleached and deodorized. In thebleaching step, the refined oil is treated with bleach clay andthen transferred to a vacuum bleaching tank. Following thebleaching step, the spent clay is filtered from the oil and therefined, bleached oil is ready for the deodorizing step. Priorto the deodorizing step, the bleached oil may be hydrogenatedusing a nickel catalyst and the resultant liquid supercooled tofilter out the saturated oil. The refined, bleached oil isdeodorized by stripping in a still with steam ejectors. In thestripping process, any triglycerides and fatty acids remaining inthe refined, bleached oil are removed and the refined-bleacheddeodorized (RBD) oil is ready for processing into commercialproducts. A process flow diagram for the edible oil processingoperation is attached to this memorandum.
. ',Crude orRefiningDegummed OilICaustic.IIIIIWaterBleach ClayStrippingand VacuumEjector SteamRefi,ning(Centrifuge).I.Water Washin'g(Centrifuge) w1I- IBleaching(EnclosedPlate Filter)Deodorizer(Still withSteam Ejectors).I.Refined-Bleac hed-Deodorized(RBD) OilEdible Oil ProcessingRefiningBy-productLipidIISoapy WaterSpentBleach Clay(Oil)ContactCooling Waterwith Triglycerides
97/28/9518:47S 2 0 2 833 3638Q."SamplingRaw SoybeanWeigh and Dump@010/013EAUCK & ASSOC.3,, Particulate Emissions(SCC 3-02-007-81)cStoragei!Soybeans To Preparation(Figure 9.11.1-2)Figure 9.1 1.1-1. Flow diagram of typical soybean handling/elevator operations.(Source Classification Codes in parentheses.)
?7/28/05BAUCK El ASSOC.B 2 0 2 833 383618:47a011/013ATTACHMENT 2Soybeans fromHandling/Elevator Operations(Figure 9.11.1.1)I- -- --- IIJCracking. .1':. .1. . Emissions- .I. - .' ,. -Particulate::I;!.-I1. .Flaking :i i. .(SCC 3.02407-88). .!I j; .:a, 4 I.I. . . . ! q.d o . g . l o -b, v z'.!!.,.I. . -j&"JWJJflakes to Solvent Extractjon(Figure 9.11.1-3)Figure 9.11.1-2. Flow diagram of the typical process for preparing soybeansfor solvent extraction. (Source Classification Codes in parentheses.)
.9U7/28/9516:47B 2 0 2 833 3836 012/013U U C R & ASSOC.ATTACHMENT 3Hexane and Sream VaporsIIFigure 9.1 1.1-3. Flow diagram of the "conventiod"soybean solvent exmaion process.(Source Classification Codes in parentheses.)
- -:07/28/B5E202 833 3 8 3 010:47@013/013U U C K & ASSOC.ATTACHMENT 4Cool Dried Meal fromSolvent ExtractionParticulateEmissions-Hulls fromPreparatlon(Fgurs 9.11.1-3)(Figure 9.11.1-2)11Meal Grindingand Sizing(SCC 342407#tr)Hull Grindingand Sizing(SCC302-00786)-ParticulateEmissions1Hull Toasting 4.-T l19eloMealStorage(High Protein)IToasted Hull(Millfeed)StorageI\IMeal-MillfeedBlending1Meal Storage(Low Protein)(Rail, Truck, Barge)ParticulateEmissions,.Figure 9.1 1.1-4. Flow diagram of the "convenuonal" process fordry material sizing, grinding, and loadout. (Source Classification Codes in parenrheses.)
Crude orCausticIIIRefiningI ) ge)WashingLipidI- Bleaching(Enclosed Plate Filter)Bleach ClayStrippingand VacuumEjector SteamRefiningwDeodorizer(Still withSteam Ejectors) Refined-Bleached-Deodorized(RBD) OilEdible Oil ProcessingISoapy Water SpentBleach Clay(Oil)ContactCooling Waterwith Triglyceridesand Fatty Acid
!l. -0 7 / 2 8 / 8 516:44B 2 0 2 8 3 3 3656HAWK& ASSOC.a001/013IINATIONAL OILSEED PROCESSORS ASSOCIATION1255 TWENTY-THIRD STREET, N.W.WASHINGTON, DC 20037Phone: (202)452-8040Fax:(202) 466-4949-FACSIMILE-TRANSMITTAL FORM-# OF PAGES IN THIS FAX (including cover page):If transmittal is incomplete or unclear, please call (202) 452-8040 forassistance.FROM:David C. Ailor,NOPA Director of Regulatory Affairs
July 28, 1174PHONE:(202) 452-8040FAX:(202) 835-0400U.S. Environmental Protection AgencyOflice of Air Quality Planning and Standards (MD-15)Research Triangle Park, NC 2771 1Attn.: Mr. Dallas W. Safriet, Emission Inventory BranchEmission Standards DivisionRe.: EPAs Revised Draft Emission Factor Documentation for AP42 Sectlon 9.1 1.1, Vegetable Oil Processing (June 1995)Dear Mr. Safriet:On June 9, 1995, Mr. Tom Lapp (Midwest Research Institute),acting on your behalf, sent our organization, the National OilseedProcessors Association (NOPA), the EPAs Revised Draft EmissionFactor Documentation for AP-42 Section 9.1 1.1, Vegetable OilProcessing, that the EPA intends to publish in an upcomlngsupplement to AP-42, Compilation of Air Pollutant EmissionFactors. You asked that we review and provide you with ourcomments on the revised draft document towards the Agencypublishing this sectlon as a new section In AP-42.NOPA is a national trade association comprised of 13 regular and27 associate member companies wlth plants engaged in theprocessing of vegetable meals and oils from oilseeds. NOPAs 13regular member firms process an estimated 1.1 billion bushels ofoilseeds annually at 72 plants in 22 states, employing anestimated 4.700 workers. We very much appreciate the invitationto share our views with you on a topic of such relevance to ourindustry.Generally speaking, the dowment is much improved over theDraft Emission Factor Documentation for AP-42 Section 6.1 1.1that you provided us for review/comment in August 1993.However, it is still incorrect or lacking in a few areas, and shouldbe revised accordingly. Our detailed commentshecommendedrevisions are presented in the enclosure to this letter.As you know, on Wednesday, August 2, you and several otherrepresentatives of EPA-OAQPS will be joining Ron Moeller(Cargill) and me in Fayetteville, NC. for a tour of Cargill’sFayetteville Crush PlanVOil Refinery. Ron and I would like toutilize that meeting as an opportunity to briefly review ourcomments with you and answer any questions you may have.Please advise me should that present a problem.-(1929-19B9) NATIONAL SOYBEAN PROCESSORS ASSOCIAllON
.07/28/0518:45e 2 0 2 833 3636IIAUCK & ASSOC.'t)Dallas W. SafrietEPAs Revised Draft Emission Factor Documentation for AP-42Section 9.1 1.1July 28, 1995Page 2Thank you again for the opportunity to comment on the RevisedDraft Emission Factor Documentation for AP-42 Section 9.1 1 .l,Vegetable Oil Processing. Please call me if you have anyquestions. I look forward to seeing you next week.Director of Regulatory AffairsEnclosurecc: Thomas W.Lapp (MRI. 401 Harrison Oaks Boulevard, Suite350, Cary. NC 2751 3-241 2)
07/28/0516:45"202MUCK & ASSOC.833 3636a004/013,I'ENCLOSURENOPA Comments1on EPA's Revised Draft Emission Factor Documentationfor AP-42 Sect ion 9.11 .l.Veaetable Oil Processina fJu ne 1995)d1.Paae 9.11.1-1 S e c t i o n 9.11.1.21The last sentence in the first paragraph of this section is slightly incorrect as drafted.It should be revised to read as follows:T h e process consists of five steps: oilseed handlinglelevator operations,preparation of soybeans for solvent extraction, solvent extraction and oildesolventizing, desolventizing flakes, and oil refining."1 2. -P-1This figure contains several inaccuracieslomissions as drafted. It should be revisedin several ways, as discussed below:-a. References to "Moisture, "Foreign Materlal", and "Damaged and Treated Beans"are included in the figure, adjacent to the first box ("Sampllng'). Suchinformation is extraneous to the flowchart and should be deleted.Yb. *The Source Classification Code (SCC) associated with the process addressed inthe second box in the figure ('Raw Soybean Weigh and Dump") should be'included in the box. The correct SCC number (SCC 3-02-007-81)correspondsto that for 'Receiving" in Table 9.11.1-2 on page 9.11.1-1 1.Jc.The notations for the two exit streams leaving the "Grain Cleaning" box (Le.,"Trash and Hulls" and "Particulate Emissions") should be reversed, with the topexit stream being denoted as a horizontal arrow labeled "Particulate Emissions".The bottom exit dream. denoted by a downward sloped arrow, should be labeled"Trash and Hulls".4.The exit stream from the box labeled "Process Bins" at the bottom of the figure Iscurrently labeled "To Milling". To better and more accurately illustrate therelationship between the various processedfigures in this section, this exitstream should be relabeled "Soybeans to Preparation (Figure 9.1 1.1-2)".J Attachment 1 is a revised Figure 9.1.1-1 in which the suggested revisions havebeen incorporated.13.-9.11.1 3 ISection 9.11.mThe title of the last full paragraph on this page is slightly incorrect as drafted. Itshould be revised to read as follows:"Solvent Extraction and Oil Desolventizing"1 ' '
p7/28/0516:45a 2 0 2 833 3636EAUCK & ASSOC.@l005/0131d4. Paae 9-11-1-3(Section 9.11.1.2)2The last sentence of the last full paragraph on this page is slightly incorrect asdrafted. It should be revised to read as follows:"The desolventized oil. called "crude" soybean oil, is stored for furtherprocessing or loadout.'d5.Ease 9.11.1-3 (Section 9. 11.1.2JThe discussion entitled "Desolventizing Flakes', which begins at the bottom ofthlspage and continues on to page 9.1 1.l-6. is incorrect as drafted. It should bereordered/revised to read as follows:"Desolventizing Flakes - The flakes leaving the extractor contain up to 35to 40 percent solvent and must be desolventized before use. Flakes aredesolventized in one of two ways: either "conventional" desolventizing orspecialty or 'flash" desolventizing. The method used depends upon theend use of the material. Flakes that are flash desolventized are typicallyused for human foods, while conventionally desolventized flakes are usedprimarily in animal feeds.Conventional desolventizing takes place in a desolventizer-toaster whereboth contact and nonmntact steam is used to evaporate the hexane. Inaddition, the contact steam "toasts" the flakes, making them more Usablefor animal feeds. The desolventized and toasted flakes then pass to adryer, where excess moisture is removed by heat, and then finally to acooler where ambient air is used to reduce the temperature of the driedflakes. The desolventized, defatted flakes are dried, cooled, and groundfor use as soybean meal (see Figure 9.1 1.1-4).) flk q-Specialty or "flash" desolventizing utilizes different equipment and is farless efficient than conventional desolventizing in terms of energyconsumption and solvent removal. Given these factors, solvent emissionfactors would be considerably higher for a specialty desolventizingprocess than for a similar-sized conventional desolventizing process."6.Paae 9.11.1-4(Fiaure 9.11.1-22This figure contains several inaccuracieslomissions as drafted. It should besignificantly revised, as discussed below:/a. This figure is currently entitled "Flow diagram of the process for preparingsoybeans for solvent extraction". The figure should be retitled "Flow diagram ofthe typical process for preparing soybeans for solvent extraction" because itpresents the process used by most, but not necessarily all, of the industry.
07/28/95J16:45e 2 0 2 8 3 3 3636EAUCK&ASSOC.@008/013b. To better illustrate the relationship between the various processes/figures in this 3section, a new entrance stream labeled "Soybeans from Handling/ElevatorOperations (Figure 9.11.l-l). should be added to the first box in this figure("Cracking").Jc. The figure as drafted indicates that the "Cracking" operation is a point source ofparticulate emissions. This is generally not the case in the typical process forpreparing soybeans for solvent extraction. Instead, particulate matter generatedki/;in the cracking operation is typically routed to the discharge for the "DehullingAspiration" operation, where it is combined with particulate matter generatedduring that operation and routed to a control device. The figure should berevised according Iy .Jd.JJf.The SCC's associated with the boxes labeled "Dehulling Aspiration", "CrackedBean Conditioning", and "Flaking" should be included in the boxes. The correctSCCs are SCC 3-02-007-85. SCC 3-02-007-87, and SCC 3-02-007-88,respectively. These SCC's correspond to the SCC's in Table 9.11 .l-2 (page9.11.1-1 1) for "Primary/secondary dehulling". "Bean conditioning", and "Flakingrolls", respectively.e. The box labeled "HulVBean Separation Aspiration" should be relabeled"Dehulling Aspiration" as a more accurate description of the operation. The SCCfor this operation, which corresponds to that for "Prirnary/secondary dehulling"(SCC3-02-007-85) In Table 9.1 1 . l - 2 (page 9.11 .l-1 l),should be included in thebox.The exit stream from the box labeled "Flaking' is currently labeled "ToExtraction".To better and more accurately illustrate the relationship between the variousprocessesrtigures in this section, this exit stream should be relabeled "Flakes toSolvent Extraction (Figure 9.1 1 .l-3)".J g. As currently drafted, this figure includes many steps which are not intrinsic to thetypical process for preparing soybeans for solvent extraction. These steps, whichinclude 'Hull Grinding', "Meal Loadout", "Mllifeed Loadout', and all theintermediate steps shown, should be removed from the figure and incorporated,with some modifications, in Figure 9.11.1-4(page 9.1 1.1-7)./Attachment 2 is a revised Figure 9.1.1-2in which the suggested revisions have beenincorporated./ 7 .paae9-11.1-5 (Fiaure 9.11.1 -3)This figure contains several inaccuracieslomissions as drafted. It should be revisedin several ways, as discussed below:Ja. This figure is currently entitled "Flow diagram of the solvent extraction process".The figure should be retitled "Flow diagram of the 'conventional' solventextraction process" as a more accurate description of the process.
J b. The entrance stream to the box labeled "Oil Extraction" at the top of the figureis 4curiently labeled 'Flakes from Milling". To better and more accurately illustratethe relationship between the various processes/figuresin this section, thisentrance stream should be relabeled 'Flakes from Preparation (Figure 9.11.1-2r.Jc.In the "conventional" soybean solvent extraction process, "Hexane-WaterSeparation" typically discharges a hexane and water stream to a reboiier.Accordingly, a new box labeled "Reboiler should be added to the figureimmediately downstream of 'Hexane-Water Separation". The new box should bedrawn with one entrance stream from "Hexane-Water Separation" labeled"Hexane and Wate?; and, two exit streams, including "Hexane and steamvapors" (which should be drawn as exiting to "Hexane-Steam Condensing') andwater.1 d.The exit stream from the "Hexane-Steam Condensing" boxes Is currently labeled"Exhaust to Mineral Oil Scrubber. This exit stream should be relabeled "HexaneVapor to Mineral Oil Scrubber" as a more accurate description of the stream.I/e. The box labeled "Further Processing" at the bottom of the figure should berelabeled "Further Processing or Loadout" as a more accurate description of theoperation.L/ f,The exit stream from the box labeled "Meal Cooler" is currently labeled "CooledMeal to Sizing and Grinding". To better and more accurately illustrate therelationship between the various pmcesseslfigures in this section. this exitstream should be relabeled "Cooled Dried Meal to Sizing, Grinding, and Loadout(Figure 9.11.l-4)"./Attachment 3 is a revised Figure 9.1.1-3in which the suggested revisions have beenincorporated./8 . Paae 9.11.1-7 [Fiaure 9.11.1-4)This figure contains several inaccuraciedomissions as drafted. It should besignificantly revised, as discussed below:/a.This figure is currently entitled 'Flow diagram of final processing stages'. Thefigure should be retitled "Flow diagram of the 'conventional' process for drymaterial sizing, grinding, and loadout" as a more accurate description of theprocess.Ab. The figure is currently incomplete/inaccurate In several areas. For example, asnoted earlier, several process steps included In Figure 9.11.1-2(page 9.11.1-4)are more accurately included (with some modifications) in Figure 9.1 1.1-4.These steps include "Hull Grinding and Sizing", "Meal Loadout", "MillfeedLoadout', and certaln Intermediate steps.J Attachment 4 is a revised Figure 9.1.l-4in which the suggested revisions have beenincorporated.
p7/28/9516:46B 2 0 2 8 3 3 3636HAUCR & ASSOC.@lOOS/Ol391 9 . Peae 9.11.1-9 (Table 9.11.1-115Among the various hexane emission factors included in the table, that for "Fugitiveemissions from meal" is by far the largest in terms of mass of hexane emitted permass of soybeans processed. Additionally, it is given the highest emission factorrating among the factors included in the table (i.e., a rating of "C).The approachthat was used to estimate fugitive emissions from meal at solvent extraction facilitiesassumesthat all of the solvent in the meal at the exit point of the desolventizertoaster is released onsite, either through the dryer or cooler vents, or as fugitiveemisslons (see page 4-16 of Revised Draft Report). However, thls concluslon Isinconsistent with the dataPage 2-17 of the Revised Draft Report provides as follows on this issue:'These results suggest that volatilization of hexane may occur from thesoybean meal as it is processed into feedstuffs and marketed. Hexane inmeal that is processed into flour for cooking or cooked feeds (many animalfeeds like dog and cat food are often overcooked) will probably bevolatilized during cooking. Processing that does not require cooking mayresult in hexane remaining in the meal until consumption."Similar conclusions are included on page 9.1 1.1-8.All of the conclusions presented above pertain to activities that occur downstream Ofsolvent extraction facilities. Consequently, the data relied upon by EPA do notpermit quantification of the fugitive emissions that may be occurring onsite at asolvent extraction facility or at later stages in the production stream (e.g.,transportation, preparation of feedstuffs, use). The line item "Fugitive emissions frommeal" should therefore either be deleted from the table altogether or, at a minimum,denoted by a "NA" in the table.10. paae 9.11.1 -11 (Table 9.11.1-aThis table contains several inaccuracieslornissions as drafted. It should be revisedin several ways, as discussed below:/a.The emission factors in this table are all given an emission factor rating of "E".However, no explanation is ever provided for this rating. To help reade'rs betterunderstand the basis for this rating, explanatory text from page 4-1 8 of theRevised Draft Report should be incorporated in the table as a footnote. Thefootnote should reads as follows:"These data were obtained from unpublished emission test data andfrom industry questionnaires. Because all data were secondary data,the test data and questionnaire data were weighted equally incalculating emlssion factors, and the factors were calculated asarithmetic means of the associated data. Because the data aresecondary. all emission factors are rated E.",.I
.07/28/9516:46MUCK & ASSOC.a 2 0 2 8 3 3 3636@009/0137-J b. One process included in the table - "Hull screens" - is no longer a typical6component of the "conventional' process for dry material sizing, grinding, andloadout. Consequently, this process should be deleted from the table.--J c . One process included in Table 9.11.1-2 "White flake cooling" should bedeleted from the table because it is associated with a specialty process that is notaddressed in the related figures. White flake cooling is not a component of the"conventional' solvent extraction process, the principal focus of both the text andthe four figures in the section. Rather, it is associated with the specialty or "flash"desolventizing process discussed on page 9.1 1. I - 6 of the text. Omission ordeletion of its related processes from the figures and the table is entirelyappropriate because it is a specialty process./d.1/11.-One process included in Table 9.11.1-2 - "Meal grinder should be reterrned'Meal grinderlsizing" to be consistent with the suggested revisions offered onFigure 9.1 1.1-4 (see comment no. 8).Peae.9.11.1-13 I R e t e r w No 20 f0 r Secti o n 9.lmINo publication date is provided for Reference no. 20. The date should be inclidedfor this reference along with the other pertinent information already provided.TO1 lkM7-2a85
p7/28/9516:47"2028 3 3 3636Raw SoybeanWeigh and Dump(SCC 302-007-81)EAUCKkASSOC. Particulate EmissionsProcess BinsSoybeans To Preparation(Figure 9.11.1-2)Figure 9.11.1-1. Flow diagram oftypical soybean handling/elevaror operations.(Source Classification Codes in parentheses.)@010/013
ATTACHMENT 2Soybeans fromHandling/Elevator Operations(figurer . y --8-I-J-- - -CrackingIDehulling --Bean ReturnvCracked BeanConditloning(SCC 30240737)(SCC 3-02-00735)-ParticulateEmissionsHullsHulls to,Flaking(SCC 302.007-88)& 0,HIOFigure 9.11.1-2. Flow diagram of the typical process for preparing soybeansfor solvent extraction. (Source Classification Codes in parentheses.)
,07/28/B58 2 0 2 8 3 3 363010:47@012/013HAUCK & ASSOC.ATTACHMENT 3Hexane and Steam VaporsFlakes fromPreparation(Flgure 9.11.1-2)HexaneHexaneWaterSeparation1\Hexaneand WaterReboiierIHexane and Steam VaporsIHexane-WaterCondensateHexane Vapor toMlneral Oil ScrubberMineral Oil I".-HexaneHexane and Oil*II1-Oil/HexaneDIRillsLionHexane EmissionsHexane andSteam VaporsCrude OilDesolvendzed and "7Toasted Meal -4.HexmeandParticulateEmlsslons-& &"Meal Dryer(SCC 3-32-00789)/FurVler Processlngor LoadoutDned MealHexane andpanlculareEmissionsCooled Dried Meal toSizing, Grlndlng, and Loadout1(Rgure 9.11.14)Figure 9.1 1.1-3. Flow diagram of the "convendond"soybean solvent exuaccion process.(Source Classifation Codes in parentheses.)
. .,07/28/95/I18:47Cool Dried Meal fromSolvent ExtractionI/@013/013BAUCK & ASSOC.ATTACHMENT 4B202 8 3 3 3838Hulls fromPreparation(Figure 9.11.1-3)(Figure 9.11.1-2)IParticulateEmissionsMeal Grindingand SizingHull Grinding(SCC 3-02-007##)(SCC 3-02-00786)Storage(High Protein)Toasted Hull(Millfeed)Storageand Sizingt-ParticulateEmissions d - l qBlendingq (Rail, Truck, Barge)ParticulateEmissionsFigure 9.1 1.1-4. Flow diagram of the "conventional"process fordry material sizing, grinding, and loadour (Source Classification Codes in parentheses.)
.1.*.
MIDWEST RESEARCH INSTITUTECROIECT D E Y E l O C M E N l SKEICWPROJECT NO.DRAWNAPPR.DATE-
June 1, 1 174U.S. Environmental Protection AgencyOffice of Air Quality Planning and Standards (MD-15)Research Triangle Park, NC 2771 1 Attn.: Mr. Dallas W. Safriet, Emission Inventory BranchEmission Standards DivisionPHONE:(202) 452-8040Re.: Comments on EPAs May 12 Draft AP-42 IntroductionFAX:(202) 835-0400Dear Dallas:As you will recall, on Monday, March 21, I and several otherrepresentatives of the oilseed crushing industry met withOAQPS Director John Seitz and other OAQPS representatives,including yourself, to discuss possible solutions to issuessurrounding the development and use of AP-42 emissionfactors. Since then we have exchanged thoughts on using theAP-42 Introduction to address these issues, with the mostrecent communication coming from you on May 17, when youfaxed me the Agency‘s May 12 draft version of the Introductionfor our reviewkomment. This memorandum is to provide youwith our comments on the May 12 draft Introduction.JOHN MARCHChairinanCHARLESBAYLESSIs1 Vice ChairmanC. LOCKWOOD MARINE2nd V8cs ChaNrmanM E R R I T E PETERSEN1st Vice PresidsnlPATRICK E WRIGHT2nd Vice PreridenlRICHARD GALLOWAYSesrelar”J.JOHN BURR177TrearurmrJAMES W. LINDSRYlmmsdlafe Per, ChslrmanIn general, we think that this version of the draft Introductionresolves our major concerns about the potential misuse of AP42 emission factors. Our only comments, which are of arelatively minor nature, are discussed in the Attachment to thismemorandum. We compliment the Agency on itsresponsiveness to our concerns, and look forward to seeingthe final version of the Introduction in print. As stated inprevious correspondence and a! the meeting, we urge you toprint the Introduction at the beginning of each chapter tominimize the likelihood that an AP-42 user will overlook thepertinent information.On behalf of the Corn Refiners Association, the National CottonCouncil, and NOPA, I want to thank you once again for workingwith us to resolve our concerns on the development and use ofAP-42 emission factors. We have found our meetings anddiscussions most productive, and look forward to our continueddealings.SHELDON J. HAUCKPrsddsnl(1929-1989) -NATIONAL SOYBEAN PROCESSORS ASSOCIATION
Mr. Dallas W. SafrietComments on EPAs May 12 Drafl AP-42 IntroductionJune 1, 1994Page 2Thank you for your consideration of our concerns and yourcooperation in addressing them. Please call me if you haveany questions or wish to discuss our comments further.avid C. Ailor. P.E.Director of Regulatory AffairsAttachmentcc: Dallas Safriet (via facsimile)John Seitz (via Regular Mail)TW2
ONE:(202) 452-8040FAX:(202) 835-0400January 10, 1994U S . Environmental Protection AgencyOffice of Air Quality Planning and Standards (MD-15)Research Triangle Park, NC 2771 1Attn.: Mr. Dallas W. Safriet, Emission Inventory BranchEmission Standards DivisionRe.: Draft Emission Factor Documentation for AP-42 Section6.1 1.1, Vegetable Oil Processing (August 10, 1993)Dear Mr. Safriet:In August 1993 you sent our organization, the National OilseedProcessors Association (NOPA), a new draft Section 6.1 1.1,Vegetable Oil Processing, that the EPA intends to publish in asupplement to AP-42, Compilation of Air Pollutant EmissionFactors. You asked that we provide you with our comments on thenew draft document towards the Agency publishing this newsection.NOPA is a national trade association comprised of 14 reg
The refined, bleached oil is deodorized by stripping in a still with steam ejectors. In . the stripping process, any triglycerides and fatty acids remaining in the refined, bleached oil are removed and the refined-bleached- deodorized (RBD) oil is ready . for . processing into commercial products. A . process flow diagram for the edible oil .