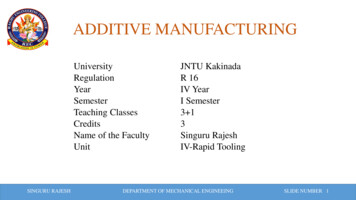
Transcription
ADDITIVE ing ClassesCreditsName of the FacultyUnitSINGURU RAJESHJNTU KakinadaR 16IV YearI Semester3 13Singuru RajeshIV-Rapid ToolingDEPARTMENT OF MECHANICAL ENGINEEINGSLIDE NUMBER 1
UNIT-4:Rapid ToolingSYLLABUS Introduction to rapid tooling (RT), conventional tooling Vs RT, Need for RT. Rapid tooling classification: indirect rapid tooling methods: spray metaldeposition, RTV epoxy tools, Ceramic tools, investment casting, spin casting, diecasting, sand casting, 3D Keltool process. Direct rapid tooling: direct AIM, LOM Tools, DTM Rapid Tool Process, EOSDirect Tool Process and Direct Metal Tooling using 3DP.SINGURU RAJESHDEPARTMENT OF MECHANICAL ENGINEEINGSLIDE NUMBER 2
Rapid Tooling: Applicationand ManufacturingSINGURU RAJESHDEPARTMENT OF MECHANICAL ENGINEEINGSLIDE NUMBER 3
Rapid Tooling Rapid Tooling (RT) describes a process that is the result of combining RapidPrototyping techniques with conventional tooling practices to produce a moldquickly or parts of a functional model from CAD data in less time and at alower cost relative to traditional machining methods. Rapid Tooling can act as a bridge to production injection molded parts. Rapid Tooling (RT) typically, either uses a Rapid Prototyping (RP) model as apattern or uses the Rapid Prototyping process directly to fabricate a tool for alimited volume of prototypes.SINGURU RAJESHDEPARTMENT OF MECHANICAL ENGINEEINGSLIDE NUMBER 4
Rapid ToolingSINGURU RAJESHDEPARTMENT OF MECHANICAL ENGINEEINGSLIDE NUMBER 5
Rapid Tooling In the advantages of Laminated Object Manufacturing we discussed thatLOM can be used in Rapid tooling application, since the material is solid andinexpensive, bulk complicated tools are cost effective to produce. Central to the theme of rapid tooling is the ability to produce multiple copies ofa prototype with functional material properties in short lead times. Apart from mechanical properties, the material can also include functionalitiessuch as colour dyes, transparency, flexibility etc.SINGURU RAJESHDEPARTMENT OF MECHANICAL ENGINEEINGSLIDE NUMBER 6
Need of Rapid Tooling Expensive tooling cost can be well justified just when the production quantity ismassive. Actually the way to produce tooling quicker and more economically,especially for small quantity manufacturing becomes a significant question. Additionally, in the product development cycle, requires always some intermediatetooling to produce a small quantity of prototypes or functional tests, samples formarketing, evaluation purpose, or production process design. The main advantages are tooling time is much shorter than for a conventional tool.Time to first articles can be less than one-fifth that of conventional tooling; toolingcost is much less than for a conventional tool. Cost can be below five percent ofconventional tooling cost.SINGURU RAJESHDEPARTMENT OF MECHANICAL ENGINEEINGSLIDE NUMBER 7
Benefits of Rapid ToolingThe following are benefits of RT: Prototypes in production material in littletime. Allows for full fit and function testing. Discover any design imperfection on earlystage. Low cost tooling allows for facilitate designrefinement and modification. Preceding production process- molds canproduce thousands of parts.SINGURU RAJESHNew stations rapid milling CNC - Charly Robotpresenting attractive costs can produce molds orprototypes in Fiberglass, aluminum and Compositesor fast production of products in extremely shorttime in dimensions:3100 mm x 2100 mm x 450 mmeven to fraction larger molds modeling.DEPARTMENT OF MECHANICAL ENGINEEINGSLIDE NUMBER 8
Rapid Tooling: issues Two issues are in this Rapid Tooling they are : Tooling proofs Process planning Tooling proofs refer to getting the tooling right so that there will not be aneed to do a tool change during production because of process problems. Process planning is meant for laying down the process plans for themanufacture as well as assembly of the product based on the prototypesproduced.SINGURU RAJESHDEPARTMENT OF MECHANICAL ENGINEEINGSLIDE NUMBER 9
Rapid Tooling: Classification Soft tooling, typically made ofsilicon rubber, epoxy resins, lowmelting point alloys and foundrysands, generally allows for onlysingle casts or for small batchproduction runs. Hard tooling, on the other hand,usually made from tool steels,generally allows for longerproduction runs.Classification of Rapid ToolingSINGURU RAJESHDEPARTMENT OF MECHANICAL ENGINEEINGSLIDE NUMBER 10
Rapid Tooling: Classification Direct tooling is referred to whenthe tool or die is created directly bythe RP process. As an example in the case ofinjection molding, the main cavityand cores, runner, gating andejection systems, can be produceddirectly using the RP process.Classification of Rapid ToolingSINGURU RAJESHDEPARTMENT OF MECHANICAL ENGINEEINGSLIDE NUMBER 11
Rapid Tooling: Classification Indirect tooling, on the other hand,only the master pattern is createdusing the RP process. A mold, made of silicon rubber,epoxy resin, low melting pointmetal, or ceramic, is then createdfrom the master pattern.Classification of Rapid ToolingSINGURU RAJESHDEPARTMENT OF MECHANICAL ENGINEEINGSLIDE NUMBER 12
Indirect Tooling Soft Tooling: Spray metaldeposition, Epoxy tools, Ceramictools, Investment casting, Spincasting, Die casting, Sand casting,3D Keltool process. Hard Tooling: 3D Keltool Direct Tooling Soft Tooling: Direct AIM, LOMTools Hard Tooling: DTM Rapid ToolProcess, EOS Direct Tool Processand Direct Metal Tooling using 3DP.process.SINGURU RAJESHDEPARTMENT OF MECHANICAL ENGINEEINGSLIDE NUMBER 13
Rapid Tooling processSINGURU RAJESHDEPARTMENT OF MECHANICAL ENGINEEINGSLIDE NUMBER 14
Direct Soft Tooling Rapid Tooling This is where the molding tool is produced directly by the RP systems. Such tooling can be used for liquid metal sand casting, in which the mold isdestroyed after a single cast. Other examples, such as composite molds, can be made directly usingstereolithography. These are generally used in the injection molding of plastic components and canwithstand up to between 100 to 1000 shots. As these molding tools can typically only support a single cast or small batchproduction run before breaking down, they are classified as soft tooling.SINGURU RAJESHDEPARTMENT OF MECHANICAL ENGINEEINGSLIDE NUMBER 15
Direct Soft Tooling Rapid Tooling Selective Laser Sintering of Sand Casting Molds: Sand casting molds can be produced directly using the selective laser sintering(SLS ) process. Individual sand grains are coated with a polymeric binder. Laser energy isapplied to melt this binder which coats the individual sand grains together, thereby bonding the grains of sand together in the shape of a mold. Accuracy and surface finish of the metal castings produced from such molds aresimilar to those produced by conventional sand casting methods. Functional prototypes can be produced this way, and should modifications benecessary, a new prototype can be produced within a few days.SINGURU RAJESHDEPARTMENT OF MECHANICAL ENGINEEINGSLIDE NUMBER 16
Direct Soft Tooling Rapid Tooling Direct AIM A rapid tooling method developed by 3D CAD/CAM systems uses the SLA toproduce resin molds that allow the direct injection of thermoplastic materialsKnown as the Direct AIM (ACES injection molding). This method is able to produce high levels of accuracy. However, build times using this method are relatively slow on the standard stereolithography (SLA) machine. Also, because the mechanical properties of these molds are very low, tool damagecan occur during ejection of the part. This is more evident when producinggeometrically more complex parts using these molds.SINGURU RAJESHDEPARTMENT OF MECHANICAL ENGINEEINGSLIDE NUMBER 17
In-Direct Soft Tooling Rapid Tooling In this rapid tooling method, a master pattern is first produced using RP. From the master pattern, a mold tooling can be built out of an array of materialssuch as silicon rubber, epoxy resin, low melting point metals, and ceramics. Arc Spray Metal Tooling Silicon Rubber Molds Spin Casting with Vulcanized Rubber Molds Castable Resin Molds Castable Ceramic Molds Plaster Molds Investment castingSINGURU RAJESHDEPARTMENT OF MECHANICAL ENGINEEINGSLIDE NUMBER 18
Arc Spray Metal Tooling1234SINGURU RAJESH5DEPARTMENT OF MECHANICAL ENGINEEING6SLIDE NUMBER 19
Arc Spray Metal Tooling It is possible to create very quickly an injection mold thatcan be used to mold a limited number of prototype parts. The metal spraying process is operated manually, with ahand-held gun. An electric arc is introduced between two wires, which meltsthe wires into tiny droplets. Compressed air blows out the droplets in small layers ofapproximately 0.5 mm of metal.SINGURU RAJESHDEPARTMENT OF MECHANICAL ENGINEEINGSLIDE NUMBER 20
Silicon Rubber Molds/MouldsSINGURU RAJESHDEPARTMENT OF MECHANICAL ENGINEEINGSLIDE NUMBER 21
Silicon Rubber Molds/MouldsSINGURU RAJESHDEPARTMENT OF MECHANICAL ENGINEEINGSLIDE NUMBER 22
Silicon Rubber Molds/Moulds In manufacturing functional plastic, metal and ceramic components, vacuumcasting with the silicon rubber mold has been the most flexible rapid toolingprocess and the most used to date.They have the following advantages: Extremely high resolution of master model details can be easily copied to thesilicon cavity mold. Gross reduction of backdraft problems (i.e., die lock, or the inability to releasethe part from the mold cavity because some of the geometry is not within thesame draw direction as for the rest of the part)SINGURU RAJESHDEPARTMENT OF MECHANICAL ENGINEEINGSLIDE NUMBER 23
Spin Casting with Vulcanized RubberMolds Spin casting, as its name implies, applies spinning techniques to producesufficient centrifugal forces in order to assist in filling the cavities. Circular tooling molds made from vulcanized rubber are produced in much thesame way as in silicon rubber molding. The tooling cavities are formed closer to the outer parameter of the circular moldto increase centrifugal forces. Polyurethane or zinc-based alloys can be cast using this method. This process is particularly suitable for producing low volumes of small zincprototypes that will ultimately be mass-produced by die-casting.SINGURU RAJESHDEPARTMENT OF MECHANICAL ENGINEEINGSLIDE NUMBER 24
Cast-able Resin Molds Similar to the silicon rubber molds, the master pattern is placed in a mold boxwith the parting, line marked out in plasticine. The resin is painted or poured over the master pattern until there is sufficientmaterial for one half of the mold. Different tooling resins may be blended with aluminum powder or pellets so asto provide different mechanical and thermal properties. Such tools are able to withstand up to between 100 to 200 injection moldingshots.SINGURU RAJESHDEPARTMENT OF MECHANICAL ENGINEEINGSLIDE NUMBER 25
Casting Although there are numerous casting techniques available, three main processesare discussed here: the conventional sand casting, investment casting, andevaporative casting processes. RP models render themselves well to be the master patterns for the creation ofthese metal dies. Sand casting is the cheapest and most practical method for the casting of largeparts.SINGURU RAJESHDEPARTMENT OF MECHANICAL ENGINEEINGSLIDE NUMBER 26
Investment CastingSchematic diagram of the shell investment casting processSINGURU RAJESHDEPARTMENT OF MECHANICAL ENGINEEINGSLIDE NUMBER 27
Evaporation pattern castingSINGURU RAJESHDEPARTMENT OF MECHANICAL ENGINEEINGSLIDE NUMBER 28
Indirect Tooling Soft Tooling: Spray metaldeposition, Epoxy tools, Ceramictools, Investment casting, Spincasting, Die casting, Sand casting. Hard Tooling: 3D Keltool Direct Tooling Soft Tooling: Direct AIM, LOMTools Hard Tooling: DTM Rapid ToolProcess, EOS Direct Tool Processand Direct Metal Tooling using 3DP.process.SINGURU RAJESHDEPARTMENT OF MECHANICAL ENGINEEINGSLIDE NUMBER 29
Direct Hard Tooling Hard tooling produced by RP systems has been a majortopic for research in recent years. Although severalmethods have been demonstrated, much research is stillbeing carried out in this area. The advantages of hard tooling produced by RP methodsare fast turn around times to create highly complexshaped mold tooling for high volume production. The fast response to modifications in generic designs canbe almost immediate.SINGURU RAJESHDEPARTMENT OF MECHANICAL ENGINEEINGSLIDE NUMBER 30
Direct Hard Tooling: DTM Rapid Tool TM Rapid Tool TM is a technology invented by DTM Corporation to produce metalmoulds for plastic injection moulding directly from the SLS SinterstationTM . The moulds are capable of being used in conventional injection moldingmachines to mould the final product with the functional material. The CAD data is fed into the SinterstationTM which bonds polymeric bindercoated metal beads together using the Selective Laser Sintering (SLS) process. Next, de-binding takes place and the green part is cured and infiltrated withcopper to make it solid. The furnace cycle is about 40 hours with the finished part having similarproperties equivalent to aluminum. The finished mould can be easily machined.SINGURU RAJESHDEPARTMENT OF MECHANICAL ENGINEEINGSLIDE NUMBER 31
Direct Hard Tooling: Rapid Tool TM Shrinkage is reported to be no more than 2%, which is compensated for in thesoftware. Typical time frames allow relatively complex molds to be produced in two weeks ascompared to 6 to 12 weeks using conventional techniques. The finished mold is capable of producing up to tens of thousands injection-moldedparts before breaking down.SINGURU RAJESHDEPARTMENT OF MECHANICAL ENGINEEINGSLIDE NUMBER 32
Direct Hard Tooling:Laminated Metal Tooling This is another method that may prove promising for RT applications. The process applies metal laminated sheets with the Laminated ObjectManufacturing (LOM) method. The sheets can be made of steel or any other material which can be cut by theappropriate means, for example by CO2 laser, water jet, or milling, based on theLOM principle. The CAD-3D data provides the sliced 2D information for cutting the sheets layer bylayer. However, instead of bonding each layer as it is cut, the layers are all assembled aftercutting and either bolted or bonded together.SINGURU RAJESHDEPARTMENT OF MECHANICAL ENGINEEINGSLIDE NUMBER 33
Direct Hard Tooling:Direct Metal Laser Sintering (DMLS) Tooling The Direct Metal Laser Sintering (DMLS) technology was developed by EOS. The process uses a very high-powered laser to sinter metal powders directly. The powders available for use by this technology are the bronze-based and steelbased materials. Bronze is used for applications where strength requirements are not crucial. Uponsintering of the bronze powder, an organic resin, such as epoxy, is used to infiltrate(pass through, penetrate) the part. For steel powders, the process is capable of producing direct steel parts of up to95% density so that further infiltration is not required. Several direct applications produced with this technology including mould insertsand other metal partsSINGURU RAJESHDEPARTMENT OF MECHANICAL ENGINEEINGSLIDE NUMBER 34
Direct Hard Tooling:Pro Metal TM Rapid Tooling Based on MIT’s Three Dimensional Printing (3DP) process, the Pro MetalTM RapidTooling System is capable of creating steel parts for tooling of plastic injectionmoulding parts, lost foam patterns and vacuum forming. This technology uses an electrostatic ink jet print head to eject liquid binders ontothe powder, selectively hardening slices of an object a layer at a time. A fresh coat of metal powder is spread on top and the process repeats until the part iscompleted. The loose powder act as supports for the object to be built. The RP part is then infiltrated at furnace temperatures with a secondary metal toachieve full density. Tooling produced by this technology for use in injection moulding have reportedwithstanding pressures up to 30000 psi (200 MPa) and surviving 100000 shots ofglass-filled nylon.SINGURU RAJESHDEPARTMENT OF MECHANICAL ENGINEEINGSLIDE NUMBER 35
Indirect Hard Tooling There are numerous indirect RP tooling methods that fall under this category and thisnumber continues to grow. However, many of these processes remain largely similar in nature except for smalldifferences, e.g., binder system formulations or type of system used. Processes include the Rapid Solidification Process (RSP), Ford’s (UK) Sprayform,Cast Kirksite Tooling, CEMCOM’s Chemically Bonded Ceramics (CBC) and SwiftTechnologies Ltd. “SwiftTool”, just to name a few. In general, indirect methods for producing hard tools for plastic injection moldinggenerally make use of casting of liquid metals or steel powders in a bindersystem. For the latter, debinding, sintering and infiltration with a secondary material areusually carried out as post-processes.SINGURU RAJESHDEPARTMENT OF MECHANICAL ENGINEEINGSLIDE NUMBER 36
Indirect Hard Tooling: 3D Keltool 3D Keltool is process has been developed by 3D Systems to produce a mould infused powdered steel. The process uses a SLA model of the tool for the final part that is finished to a highquality by sanding and polishing. The model is placed in a container where silicon rubber is poured around it to makea soft silicon rubber mould that replicates the female cavity of the SLA model. This is then placed in a box and then silicon rubber is poured around it to produce areplica copy of the SLA model in silicon rubber. This silicon rubber is then placed in a box and a proprietary mixture of metalparticles, such as tool steel, and a binder material is poured around it, cured andseparated from the silicon rubber model.SINGURU RAJESHDEPARTMENT OF MECHANICAL ENGINEEINGSLIDE NUMBER 37
Indirect Hard Tooling: 3D KeltoolSINGURU RAJESHDEPARTMENT OF MECHANICAL ENGINEEINGSLIDE NUMBER 38
Indirect Hard Tooling: 3D KeltoolSINGURU RAJESHDEPARTMENT OF MECHANICAL ENGINEEINGSLIDE NUMBER 39
Indirect Hard Tooling: 3D Keltool This is then fired to eliminate the binder and sinter the green metal particles together. The sintered part which is about 70% steel and 30% void is then infiltrated withcopper to give a solid mold, which can be used in injection molding. An alternative to this process is described as the reverse generation process. This uses a positive SLA master pattern of the mold and requires one step less. This process claims that the CAD solid model to injection-molded production partcan be completed in four to six weeks. Cost savings of around 25% to 40% can be achieved when compared to that ofconventional machined steel tools.SINGURU RAJESHDEPARTMENT OF MECHANICAL ENGINEEINGSLIDE NUMBER 40
Indirect Hard Tooling: 3D KeltoolSINGURU RAJESHDEPARTMENT OF MECHANICAL ENGINEEINGSLIDE NUMBER 41
Thank youSINGURU RAJESHM.Tech (MD), PGDEEM, B.Tech (ME)Assistant ProfessorRaghu Engineering College(Autonomous)Dakamarri, Bhimunipatnam Mandal,Visakapatnam Dist, Andhra PradeshSINGURU RAJESHDEPARTMENT OF MECHANICAL ENGINEEINGSLIDE NUMBER 42
Rapid tooling classification: indirect rapid tooling methods: spray metal deposition, RTV epoxy tools, Ceramic tools, investment casting, spin casting, die casting, sand casting, 3D Keltool process. Direct rapid tooling: direct AIM, LOM Tools, DTM Rapid Tool Process, EOS Direct Tool Process and Direct Metal Tooling using 3DP.