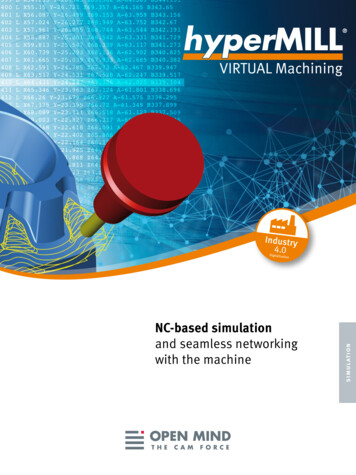
Transcription
LLLLLLLLLLLLLLLLLLLLLLLLLLLLLLLLLLLLLX54.213 Y-26.943 Z69.562 A-64.369 B344.151X55.15 Y-26.721 Z69.357 A-64.165 B343.65X56.087 Y-26.499 Z69.153 A-63.959 B343.156X57.024 Y-26.277 Z68.949 A-63.752 B342.67X57.961 Y-26.055 Z68.744 A-63.544 B342.191X58.887 Y-25.801 Z68.542 A-63.331 B341.729X59.813 Y-25.547 Z68.339 A-63.117 B341.273X60.739 Y-25.293 Z68.136 A-62.902 B340.825X61.665 Y-25.039 Z67.933 A-62.685 B340.382X62.591 Y-24.785 Z67.73 A-62.467 B339.947X63.517 Y-24.531 Z67.528 A-62.247 B339.517X64.431 Y-24.247 Z67.326 A-62.025 B339.104X65.346 Y-23.963 Z67.124 A-61.801 B338.696X66.26 Y-23.679 Z66.922 A-61.575 B338.295X67.175 Y-23.395 Z66.72 A-61.349 B337.899X68.089 Y-23.111 Z66.518 A-61.122 B337.509X69.003 Y-22.827 Z66.317 A-60.893 B337.125X69.868 Y-22.618 Z66.091 A-60.677 B336.775X70.732 Y-22.402 Z65.866 A-60.46 B336.432X70.444 Y-22.164 Z65.136 A-60.091 B336.944 F6X70.155 Y-21.925 Z64.405 A-59.719 B337.445X70.067 Y-21.868 Z64.222 A-59.627 B337.577 F3X69.979 Y-21.811 Z64.039 A-59.536 B337.708X69.75 Y-21.723 Z63.698 A-59.374 B337.982X69.473 Y-21.658 Z63.394 A-59.237 B338.26X69.157 Y-21.624 Z63.133 A-59.129 B338.535X68.81 Y-21.622 Z62.919 A-59.053 B338.803X68.268 Y-21.606 Z62.685 A-58.974 B339.18 F2.4X67.725 Y-21.59 Z62.45 A-58.894 B339.556X67.171 Y-21.59 Z62.247 A-58.833 B339.92X66.618 Y-21.589 Z62.044 A-58.77 B340.284X66.057 Y-21.605 Z61.874 A-58.727 B340.636X65.495 Y-21.621 Z61.703 A-58.682 B340.987X64.927 Y-21.652 Z61.566 A-58.657 B341.326X64.36 Y-21.684 Z61.428 A-58.63 B341.665X63.784 Y-21.733 Z61.323 A-58.623 B341.994 F4.8X63.209 Y-21.782 Z61.218 A-58.615 B342.323NC-based simulationand seamless networkingwith the 432143314341435
Perfect synthesis of the virtual and real worldsOPEN MIND has developed hyperMILL VIRTUAL Machining* to evaluate, control and optimise machining pro cesses more reliably. This highly efficient simulation solution consists of three modules: Center, Optimizer and CONNECTED Machining.Increased safety in simulationsActual machining situations, that is, the machine including controller and PLC, are mapped virtually and simu lated based on the NC code in the hyperMILL VIRTUAL Machining Center. All processes are transparent to the user, and can be analysed in detail. Real-world machine collisions, causing costly machine damage, productiondowntime and thereby critical delays, are avoided.More than just simulationPowerful optimisation algorithms ensure efficient multi-axis machining design. The hyperMILL VIRTUAL Machining Optimizer automatically finds the best tilt angle, thereby ensuring seamless machining. In addition, hyperMILL CONNECTED Machining enables in-depth networking and synchronisation with the machine.Greater efficiency thanks to a new generation of postprocessorsPostprocessor technology* has also been significantly further developed with the hyperMILL VIRTUAL Machining simulation solution, and supplemented with many innovative functionalities. For instance, bidirectional linking isnow possible between the NC program and the machining information from hyperMILL . By means of this connec tion the respective hyperMILL job can be assigned to the NC Code. *Note: hyperMILL VIRTUAL Machining requires a hyperMILL VIRTUAL Machining postprocessor. CenterOptimizer
Application areasn Checking,n Matchingn Easilya job to available machinesshifting job tasks between available machinesn Supportn Moreevaluating and optimising the machining processfor the acquisition of new machinesaccurate estimation of costs for bid proposalsNetworking withthe machineRemote control forstarting and stoppingMachine andremoval simulationEach line of codeis simulatedNC code displayIntuitive operation“The hyperMILL VIRTUAL Machining Centeris key to designing prove-out processes in afar more safe and efficient way.”Dr Josef Koch, CTO, OPEN MIND Technologies AG
Everything for efficient simulationThe hyperMILL VIRTUAL Machining Center represents the core of the new solution. This offers all the classic options for simulation, embedded in a highly intuitive user interface. Here, machine simulation is carried outwith a defined machine model, taking into account the workpiece and tool as well as the tool holder, fixturesand clamps. Axes can be moved and simulated manually, and possible collisions and limit switch traversals aredetected automatically.Highly efficient and reliable Simulation based on NC codeMachine movements are often simulated before the postprocessor run. In these cases, there is no connectionbetween the postprocessor and the simulation and the actual machining situation cannot be fully simulated. Forthis reason, OPEN MIND has decided to go one major step further with its hyperMILL VIRTUAL Machining Center. The simulation is based on the NC code after the postprocessor run is completed. The code is simulated line forline, including the transition movements. This ensures that the virtual machine movements fully correspond to theactual machine movements. As such, the NC-based machine simulation assures reliable collision detection andsafer and more efficient prove-out processes.Center
Featuresn Simulationbased on NC coden Bidirectionallinking of NC block andhyperMILL job enables quick comparisonof the respective machining job n Fullsimulation of all movements, includingtransition movementsactualpositionn Quickcollision check that can be carried out independently of the simulationn Interactiven Manualplacement of workpiece and fixturesmovement of the virtual machinen Approachof target points with and withoutRotating Tool Center Point (RTCP)n Displayof axis limitsn Comprehensiveanalysis functionsn Fastcomparison of the programmed datum pointsand tools with the actual machine configurationClear program managementAll main and sub programs are mapped in a clearstructure. Individual operations can be simulatedseparately, or used as a starting point for thesimulation.I ntuitive user interfaceThe design of the user interface is based on an actualcontroller. Machine operators, CAM programmers andmanufacturing planners benefit from the intuitiveoperation. This reduces the learning curve for thesimulation technology to a minimum.userdefinedbreakpoint
Everything for illuminating analysesAlongside efficient simulation, the hyperMILL VIRTUAL Machining Center contains comprehensive analysis func tions that enable detailed observation of the individual machining situations. This means that a precise checkis carried out before the machine is run. This prevents errors and inefficient operations, as individual machinecomponents are analysed to ensure that there is sufficient safety. Various technical charts provide valuable infor mation about the quality of the machining programs. Movements, feedrates and the spindle speed are all shown.Conspicuous axis movements and accelerations can be quickly recorded and corrected before the program is runat the machine.‘Best Fit’ functionCalculates the optimalworkholding positionfor the availableworkspaceSlider (limited)Slider (all)Limit areasRestrict thesimulation area fora detailed viewMaterial removalThe milling processshown in detail basedon the stock modelCenter.
Featuresn orkspace monitoringWWith the help of a stored machine model, theworkspace monitoring checks whether any limitswitches are traversed by the 2.5D, 3D, 3 2 or5axis simultaneous machining movements. Themovements of both the linear axes (X, Y and Z)and the rotary axes (A, B and C) are checked, asare the clamps and fixturing systems.n etting breakpointsSThe simulation can be controlled to stop atcertain locations in order to reliably check criticalpoints and estimate the subsequent processesmore precisely. The breakpoints are createdautomatically under certain conditions, such as atool change or a change from rapid to cutmovements. Moreover, breakpoints can also beselected manually through an NC block line, orpicked up from any point on the toolpath.n Adjusting visibilityThe visibility of the individual machine compo nents can be adjusted in order to enable optimalvisualisation of the simulation. Preset machineviews, such as ‘Head and Table’, can be calledup at the push of a button.n ‘BestFit’ function for optimal placementof the component in the workspacen Detailedn Settingn Safeanalysis of the traverse pathsof user-defined breakpointsworkspace monitoringDistance controlEasy measurementof distances betweentwo componentsAxis diagramDetailed analysisof machine axismovementsn Safe working space analysis.Flexible manufacturing planningTools, fixtures and stock as well asclamps can be managed manually. Theuser can make changes directly in thesimulation environment. The changescan be previewed and stored, or notaccepted as a process change.The unique Best Fit function automaticallyoptimises the machining operation to match theavailable workspace. Workspace monitoring isable to indicate instances where the limitswitches have been traversed but the actualworkspace is still sufficient for machining. In thiscase, the Best Fit function automatically deter mines the optimal setup location for the respec tive workspace. This does away with the need forunnecessary set-up changes and resultingdowntimes.
Always the best possible NC codeMore axes, more solutionsThere are several solutions for tool orientation in multi-axis machining. The selected solution plays a crucial rolein determining machining quality and efficiency. If the user sets the axis position at certain points manually, it isoften not possible to determine the best possible tool orientation due to the complexity of the decision.Automatic solution selection optimises multi-axis positionsDuring the postprocessor run, the Optimizer automatically selects the best solution for collision-free orienta tion. Special kinematic properties and user-specific properties are taken into account for collision avoidance.Programming errors or subsequent editing of the machining program are avoided, and optimal, collision-freemachining on the machine is assured.Without Optimizer633 L X-303.616 Y733.364 Z248.535 A-35 C35.924Avoiding repositioningIn order to avoid time-consuming repositioningand retractions, the Optimizer ana lyses not justindividual operations but entire machiningsequences. Based on this analysis, the Optimizerselects the ideal solution for machining the entiresequence together, within the given machinelimits.Optimizer
Featuresn Automaticnsolution selection for multi-axispositionsn Optimisedmovementsn Individualconfiguration optionsn Processreliability ovement optimisationMIf a 3axis movement is not possible due todetected collisions, the Optimizer changesthe movement with the aid of a fourth orfifth axis. In this example, the fourthposition would lead to a collision with thespindle’s attaching parts. For this reason,the C axis rotates so that the machining canbe carried out in a collision-free manner.Without Optimizer: Collision detectedWith Optimizer633 L X-36.390 Y926.973 Z248.535 A35 C-144.076With Optimizer: Collision freen recise machiningPIndependent of the kinematic properties ofthe machine, the Optimizer automaticallycreates additional intermediate positionsin the toolpaths. This means that softmachine movements for precise machiningare also ensured near the pole.n ptimised movementsOThe movements between the individualoperations are perfectly aligned with thekinematic properties of the respectivemachine. The Optimizer analyses thesemovements to avoid large compensationmovements during repositioning. Mean while, the rotary axes are moved along theshortest path, and the movements of thelinear axes are minimised. This allowsgreater speeds to be achieved during themovements.
Seamless networking with the machineClosely connectedSeeing the actual machining situation in the simulation environment in real time, perfectly synchronising themachine and simulation and easily controlling machining from your laptop: Wouldn’t that be incredibly efficient?This is all possible with the new hyperMILL CONNECTED Machining module. The module provides bidirectional data exchanging with the machine controller, which means it can send data to the machine and execute it there,as well as receive data from the machine.Increased safetyIn-depth networking – fully in the spirit of Smart Factory – also enhances safety in the machine set-up and inmachining. Should any datum points, tools or machine setting parameters not correspond to the programmedvalues in hyperMILL , the reliable hyperMILL CONNECTED Machining safety mechanism kicks in, which prevents NC program transfer to the machine and keeps the machine from starting.NC block s ynchronisationThe NC block of the machinecan be synchronised with thehyperMILL VIRTUAL MachiningCenter so that the machiningposition of the machine simu lation corresponds exactly tothe actual machine position.Datum point alignmentwith the real machineThe machine datum pointsare aligned with those ofthe NC program. Fixturingerrors or incorrect positionsare avoided.Bidirectional connection
Featuresn n Readoutof datum point definitions, tool data and criticalmachine parameters from the controller, including comparisonwith the data stored in hyperMILL n QuickNC program transfern Remotecontrol of CNC machinesn Synchronisationn Reliable Quicknetworking with the machinehyperMILL CONNECTED Machining seam lessly integrates into the existing user inter face of the hyperMILL VIRTUAL MachiningCenter. The connection to the CNC machinecan be easily created with the clickof a mouse.of the simulation with the machine’s NC blocksafety mechanismsn emote controlRSeamless interaction with the machine viaremote computer. This means that the programcan be easily started or stopped from a PC.n onvenient retract movementsCThanks to hyperMILL CONNECTEDMachining, even difficult retract movementscan be carried out. nAutomatic tool comparisonTool data from the NC programis automatically compared withthe tool data of the machine.If this data does not match, anerror message is output andthe program run is halted.NC program transferThe NC program is loadeddirectly into the memory of themachine controller. There is nochance of program mix-ups. eliable safety mechanismsR– Safe collision checking– Protection from unauthorised access– Comparison of machining parameters– Comparison of machine parameters– Machine does not start until after all safetymechanisms have been checked
OPEN MIND Technologies AGArgelsrieder Feld 5 82234 Wessling GermanyPhone: 49 8153 933-500E-mail: nd-tech.comUKOPEN MIND Technologies UK Ltd.Units 3 Bicester Business CentreTelford Road Bicester Oxfordshire OX26 4LD UKPhone: 44 1869 290003E-mail: Info.UK@openmind-tech.comUSAOPEN MIND Technologies USA, Inc.1492 Highland Avenue, Unit 3 Needham MA 02492 USAPhone: 1 888 516-1232E-mail: Info.Americas@openmind-tech.comBrazilOPEN MIND Tecnologia Brasil LTDAAv. Andromeda, 885 SL202106473-000 Alphaville EmpresarialBarueri Sao Paulo BrasilPhone: 55 11 2424 8580E-mail: Info.Brazil@openmind-tech.comAsia PacificOPEN MIND Technologies Asia Pacific Pte. Ltd.3791, Jalan Bukit Merah #04-08Singapore 159471 SingaporePhone: 65 6742 95-56E-mail: Info.Asia@openmind-tech.comChinaOPEN MIND Technologies China Co. Ltd.Suite 1608 Zhong Rong International PlazaNo. 1088 South Pudong RoadShanghai 200120 ChinaPhone: 86 21 588765-72E-mail: Info.China@openmind-tech.comIndiaOPEN MIND CADCAM Technologies India Pvt. Ltd.No. 610 and 611 · 6th Floor · ‘B’ WingNo. 6, Mittal Tower, M.G. RoadBengaluru 560001 · Karnataka · IndiaPhone: 91 80 2676 6999E-mail: Info.India@openmind-tech.comJapanOPEN MIND Technologies Japan K.K.Albergo Musashino B101, 3-2-1 NishikuboMusashino-shi Tokyo 180-0013 JapanTelefone: 81-50-5370-1018E-mail: info.jp@openmind-tech.co.jpTaiwanOPEN MIND Technologies Taiwan Inc.Rm. F, 4F., No.1, Yuandong Rd., Banqiao Dist.New Taipei City 22063 TaiwanPhone: 886 2 2957-6898E-mail: I nfo.Taiwan@openmind-tech.comOPEN MIND Technologies AG is represented worldwide with ownsubsidiaries and through competent partners and is a member ofthe Mensch und Maschine technology group, www.mum.dewww.openmind-tech.com All rights reserved, OPEN MIND Technologies AG, Wessling, Germany. Last updated April 2021. Subject to modifications. No reproduction allowed without the consent of the publisher.Headquarters
More than just simulation Powerful optimisation algorithms ensure efficient multi axis machining design. The hyperMILL VIRTUAL Machining Optimizer automatically finds the best tilt angle, thereby ensuring seamless machining. In addition, hyperMILL CONNECTED Machining enables in depth networking and synchronisation with the machine.