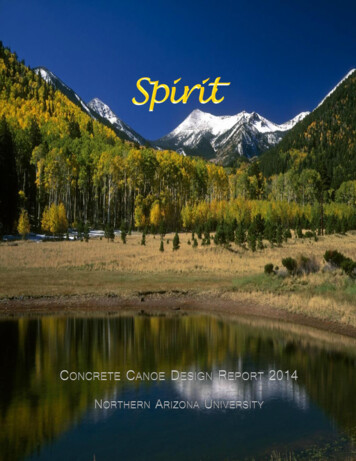
Transcription
Night furyNight fury-
SpiritNORTHERN ARIZONA UNIVERSITYTable of ContentsExecutive Summary .iiProject Management .1Organization Chart .2Hull Design and Structural Analysis.3Development and Testing .5Construction .7Project Schedule.9Design Drawing . 10List of TablesTable 1: Spirit Specifications .iiTable 2: Concrete Properties .iiTable 3: Project Milestones .1Table 4: Concrete Mix Designs .3Table 5: Fiber Reasoning .6List of FiguresFigure 1: Estimated Man-hour Distribution .1Figure 2: Allocation of Expenses .1Figure 3: Load Locations and Distributed Loads.3Figure 4: Example of Rib Design Analysis .4Figure 5: Concrete lead making cylinders and a sample sheet .5Figure 6: Restrained Shrinkage Ring Test and Sample Sheet Test .5Figure 7: Reinforcement Testing Setup .6Figure 8: Application of first 1/8 inch layer .7Figure 9: Reinforcement with 6 inch overlap .8List of AppendicesAppendix A—References . .A-1Appendix B—Mixture Proportions. .B-1Appendix C—Bill of Materials . .C-1i
SpiritNORTHERN ARIZONA UNIVERSITYExecutive SummaryNORTHERN ARIZONA UNIVERSITYSpirit is one of the major components thatwe wanted to improve upon at our university,as well as within ourselves. Spirit is theessenceofcourage,energy,anddetermination. The design and constructionof Spirit encompassed all three traits andtruly became more than just a project, butsomething that taught the team the truemeaning of spirit and pride.NAU is located over 7,000 feet above sealevelinthemountainousterrainencompassing Mount Elden and the SanFrancisco Peaks in Flagstaff, Arizona. Sinceits founding in 1899 with 23 students and 1instructor, NAU has expanded to comprise 6colleges, including the College ofEngineering, Forestry, and Natural Sciences.There are approximately 25,000 studentscurrently enrolled, with 490 undergraduatesin the Civil and Environmental EngineeringDepartment.After the establishment of the first NAUconcrete canoe team in 1977, they qualifiedfor the National Concrete Canoe Competition(NCCC) from 1989 to 1993. Though theyhad a great run of success and nationalappearances, NAU has failed to advance tonationals since. In 2011, Ponderosa took 7thoverall at the Pacific Southwest Conference(PSWC) and in 2012, Betula was placed evenlower. However, in 2013 Night Fury placedin the top six in the overall team scoringbracket at PSWC. NAU is one of 18 schoolsthat compete at the regional PSWC alongsideuniversities from Southern Nevada, Arizona,Hawaii, and Southern California.The hull design used for Spirit was alsoutilized by last year’s team, Night Fury. Thisparticular hull shape features a mediumrocker v-shape that increased the speed andmaneuverability in comparison to thestandard hull shape provided by the CNCCC.Additional information on the canoe’sspecifications can be found in Table 1.Table 1: Spirit SpecificationsCanoe NameSpiritSpirit206.7 lbsEstimated WeightLength228 inMaximum Width27 inMaximum Depth14.3 inAverage Thickness0.5 inMedium GreyConcrete ColorBlue, Gold, GreenStain ColorsReinforcementStucco Fiberglass MeshSince Spirit’s hull design matches NightFury, we were able to use Night Fury’scalculations as a baseline. The overall goalfor Spirit was to increase the workability andcompressive strength of the concrete mixes toeliminate the use of post tensioning (PT)strands. The concrete designed for Spirit isthe first of its kind to include fine fibers toreduce cracking. Three load ent was also completed using alinear analysis of the tensile strain. Table 2contains the final concrete mix designproperties.Table 2: Concrete PropertiesWet (Plastic) Unit Weight98.1 lb/ft3Dry Unit Weight81.1 lb/ft3Compressive Strength4,536.0 psiSpirit entails the ambition of the team toovercome all odds. Spirit encompasses theteam’s dynamic personality, determination,energy, and courage to break down fromtraditions and explore new ways that will setus apart from the rest. Spirit is anotherstepping stone for future canoe teams thatwill bring NAU back into rightful place atconference.ii
SpiritNORTHERN ARIZONA UNIVERSITYProject ManagementThis year’s concrete canoe team iscomprised of four members, which mademanagement a critical task. In order tocomplete this design in an effective andtimely manner, the project was broken intothree categories; reinforcement design,concrete development, and structuralanalysis. Each category had a lead designer.Active involvement from each captain inother aspects of the canoe proved to be morevital than expected. Having multipleindividuals engaged in the different designprocesses worked in the team’s favor tocomplete a noteworthy final product.In late September, the team drafted aproject schedule consisting of all majormilestone activities. Based on previous NAUconcrete canoe schedules, the team identifiedfour critical path activities that weredetermined based on the most impact oncompleting the project on time. These taskswere fundraising and acquiring a facility, mixdesign and testing, structural andreinforcement analyses and design, andcanoe construction. Project milestones can beseen in Table 3.Table 3: Project MilestonesMilestoneVarianceFinal MixDesignPour DayFinal ReportConferenceAttendance 18 days 32 days 3NoneSpirit. The estimated amount of man-hoursneeded to complete Spirit is 1,680.Analysis3% 8%Mix DesignFigure 1: Estimated Man-hour DistributionSpirit had an estimated budget for designand construction of 3,000. Throughextensive fundraising efforts, Spirit receiveda generous monetary donation of 2,000 aswell as 1,000 from the civil engineeringdepartment. The conference segmentpresented in Figure 2 is not included withinthe team’s budget. These expenses will besolely covered by the civil engineeringdepartment.2%Mix Design16%2%62%18%N/ATo ensure that the team stayed on task,meetings were scheduled accordingly.Certain tasks within the schedule were overestimated to account for any unforeseencircumstances that might hinder the task frombeing completed.Figure 1 gives the percentage estimate foreach category involved with the creation ofFinishingProjectManagementConferenceReasonFine TuningThe Final ructionFigure 2: Allocation of ExpensesOne of the structural analysis leadsserved as the primary quality control, qualityassurance, and safety officer. Before anymaterials were handled, MSDS sheets werereviewed. The safety program requiredeveryone to wear long pants, long sleeves,and closed toe shoes during construction ortesting of the materials. Furthermore, dustmasks and goggles were required whilemixing concrete batches. Gloves and safetyglasses were required during casting. Allvolunteers were required to sign a safety planwritten by the project manager.1
SpiritNORTHERN ARIZONA UNIVERSITYOrganization ChartProject Management & Reinforcement DesignHannah Williams Oversee schedule, finances,quality control/safety, taskdelegation, materialprocurement, and documentproduction Research reinforcement anddevelop reinforcementscheme Developed safety plan Assisted with concrete mixdesigns Research materials anddevelop mix designs Test concrete mixes andreinforcement Document production Quality Control Assisted with reinforcementanalysisStainingAriel SuarezHannah WilliamsStructural Analysis Ariel Suarez Shuo ZhangPresentationHannah WilliamsShuo ZhangDisplayRamon AguilarCynthia AlvarezJeremey DeGeyterBrent AllmanPerformed handcalculations andcomputersoftware ty controland safetyCanoe FabricationAll Captains 15 volunteersPaddlersBrent AllmanTodd BrewerNoёl CruzJeremy DeGeyterBrent LiparAlejandra QuesadaAriel SuarezKristin Van SciverHannah WilliamsShuo ZhangConcrete Design Mold FabricationNight Fury TeamPerformed handcalculations andcomputersoftware analysisDocumentproductionAssisted withconcrete mixdesignsCross SectionBrent AllmanShuo ZhangAdvisorsMark LamerThomas NelsonDr. Robin Tuchscherer2
SpiritNORTHERN ARIZONA UNIVERSITYHull Design and StructuralAnalysisAfter last year’s success with Night Fury,the general hull design was incorporated intoSpirit. The hull design goals set out by teamNight Fury included four design criteria:tracking, ease of construction, speed, andmaneuverability. These goals helped NightFury to produce an asymmetrical canoe witha moderate rocker shape that allowed for easytracking as well as maneuverability. The hulldesign includes a wetted surface area of 33.6square feet, a beam width of 27.4 inches, maxdrag coefficient of 11, and a displacement tolength ratio of 53.8. The team completed acost-benefit analysis that reinforced thedecision to reuse Night Fury’s mold andfound that to build an entirely new moldwould cost almost 1,000 dollars inmaterials.Using the same hull, the waterlines wererecalculated along the entire length of thecanoe in increments of 14 inches. The teambegan by establishing waterlines at 8, 10, and12 inches. The areas for each of the sectionsthat were below the waterline were summed,averaged and multiplied by the density ofwater to find the total buoyant force. Thesevalues were compared to the total force on thecanoe under different load cases. The fourperson condition produced a total load of 897pounds which includes an overestimated selfweight of 300 pounds. Through basicinterpolation between the waterlines of 8, 10,and 12 inches, the waterline for each of theload scenarios was calculated until thebuoyant forces equaled the applied load. Thewaterline for the four person conditionequated to 11.09 inches, giving a minimumfreeboard of 3.21 inches. The waterline forthe 2 female and 2 male were determined tobe 8.60 and 9.11 inches, respectively.The forces and stresses within the canoeimposed by both the water and the differentload scenarios were analyzed to determinewhere the highest stresses occur within thecanoe. Using RISA 2D, a simple beam wasanalyzed for each of the load scenarios withprimary focus on the four person load. Fourdifferent conservative loads were applied tothe beam located at the lengths approximatedin the waterlines to ensure equilibrium. Pointloads of 127, 160, 170, and 140 pounds wereplaced approximately 78, 126, 147, and 175inches from the bow along the beam. Figure3 illustrates the locations of the point loadsalong with the distributed load from thebuoyant forces and self-weight of the canoe.Figure 3: Load Locations and Distributed Loads(Note: full length of the canoe is not depicted in thefigure.)From the waterline calculations, thedistributed load imposed by the change inbuoyant force was divided into 14 inchincrements along the length of the canoe. Theresulting distributed loads were applied to thebottom of the beam. For the next step, theself-weight of the canoe was divided intoappropriate increments to represent thedistribution of the weight. To accomplish thispart of the calculations, the volume of thecanoe was found by multiplying the volumefor each section by the density of concrete.The approximate weight of each section wasthen divided by its length to yield thedistributed load per section. These distributedloads were applied to the canoe in 14 inchincrements as described above. Based on thisanalysis, the maximum moment for the fourperson condition was determined to be 237.5lb-ft. Three other moments were also3
SpiritNORTHERN ARIZONA UNIVERSITYobserved, which included 151.1, 235.2, and140.3 lb-ft. Knowing the locations of themaximum moments was essential in the nextstep of the analysis which was to determinethe amount of reinforcement.To compensate for the elimination of PTstrands, the final concrete mix design had ahigher tensile strength and incorporated finefibers to aid in crack control. To accomplishthis goal, the team set out to make theconcrete mix as strong as possible. In doingso, the density was increased yet the slumpwas maintained below 2 inches. The resultingcompressive strength reached a maximum of4.5 ksi. Spirit’s goal was to indirectlyincrease the tensile strength by increasing thecompressive strength, maintain a workableyet playdough-like consistency of theconcrete mix, and conduct an accurateprimary reinforcement analysis. Since thecompressive strength of the concrete wassubstantial, the team determined to utilizefiberglass mesh to provide tensile capacityand ribs to stiffen the hull.After determining the locations of themax longitudinal and transverse moments,the team took cross sections at thesedesignated rib locations. Then the rib crosssections were analyzed similar to how areinforced concrete beam is flexurallyanalyzed. Figure 4 is an example of how thecross sections were analyzed.Figure 4: Example of Rib Design AnalysisTo perform this calculation, the tensilestrength, modulus of elasticity, and yieldstrain of the fiberglass mesh needed to bedefined. The ultimate tensile stress per strandwas tested to be 6.19 ksi. Usingengineeringtoolbox.com (2014), the modulusof elasticity was assumed to be 2400 ksi.Applying Hooke’s law, σ Eε, the yieldstrain per strand was calculated to be 0.0026in/in. The team was able to flexurally analyzethe ribs and ensure that their capacity wasgreater than the maximum transversemoment demand. As a result, in the fourlocations with the highest transversemoments, 12 in x 2 in x 0.5 in ribs wereplaced to provide a higher moment capacityto resist the moment demand imposed by thewater.The dry unit weight of concrete wasdetermined to be 81.1 pcf. Since the densityof the concrete is heavier than the density ofwater, the team had to include foam in thehull. The team used a combination of sprayfoam and foam board as the buoyant material.This was crucial to ensure that the canoewould be able to pass the swamp test. Thevolume of the canoe was calculated using thecross section drawings created for NightFury. Using the desired thickness of 0.5inches, the overall volume of concrete wasestimated to be 2.55 cubic feet. Afterconsidering the buoyancy of water, theremaining density was used to determine thebuoyant weight of the canoe. The result wasthat the canoe weighed 206.7 pounds inwater. After extensive research, a factor ofsafety (FS) of 1.33 was determined to be thebest option (Darla). This FS was multipliedby the difference in the buoyant force andcanoe weight. The volume of foam neededwas determined by dividing the excessweight by the difference between the densityof water and the density of foam used.Finally, an analysis of shipping stresseswas eliminated due to the fact that a “coffin”composed of 15 individual supports wasutilized to transport the canoe.4
NORTHERN ARIZONA UNIVERSITYDevelopment and TestingThe goals set forth by the team for theconcrete mix design this year were to have aplaydough-likeconsistency,sufficientworkability, a slump of less than one inch, aminimum compressive strength of 3,000 psiand increase the tensile strength to eliminatethe use of PT strands.Night Fury’s mix design was used as abaseline since one of our overall goals thisyear was to improve upon their design. Themechanical properties of their mix had acompressive strength of 1,570 psi and a unitweight of 61.5 pcf. Night Fury’s mix designconsisted of Type I white Portland cement,Class F Fly Ash, 3M K1 glass bubbles, 0.52mm Poraver recycled glass beads,cenospheres, Glenium 3030, and MB-AE 90.The adjustments implemented to improveNight Fury’s mix included researching andtesting fine fibers, admixtures, aggregates,and modifying mix ratios. Figure 5 belowdepicts one of the many creations of the finalmix design and as well as a sample sheet.Figure 5: Concretelead makingcylinders and asample sheetThe effect of admixtures from last year’smix design were compared and tested againstmixes without these admixtures, and with theaddition of lime. This new cementitiousmaterial was selected due its ability to ty. Although the lime reduced thecompressive strength, the difference was sosmall that it did not warrant a disqualificationof this material.Aggregates were selected in order toincrease strength and maintain properconsistency. Although this year’s team wassatisfied with the sustainability andperformance of the Poraver aggregate, thedesired slump and compressive strength werenot fulfilled. Therefore, Mortar sand wasused as a secondary aggregate to adjust thesemechanical properties.Testing of the concrete mixes was inaccordance with the following standard testmethods; compressive strength (ASTM 39/C39M), slump (ASTM C143 / C143M), and aircontent (ASTM 138/C 138 M). Other testmethods utilized by the team were therestrained ring test and a sample sheet test. Asthe restrained ring test assesses resistance torestrained shrinkage cracking, this methodwas used to compare the difference betweenNight Fury’s mix design and Spirit’s. Thesample sheet test is a 1 ft by 1 ft section inwhich the workability or ease of applicationof the mix design was tested. Figure 6 belowshows the two mixes side by side during theshrinkage ring test and a freshly made samplesheet.Figure 6: Top:RestrainedShrinkage Ring Test– Night Fury mixdesign (left), Spiritmix design (right).Bottom: SamplesheetAfter analyzing all 12 mix designs, mixes#5 and #11 were the only two that met the set5
SpiritNORTHERN ARIZONA UNIVERSITYcriteria. After further review, mix #11provided slightly better results. Table 4compares the results of these two mixes withthe set criteria.Table 4: Concrete Mix DesignsCharacteristicsSet CriteriaMix#54,436Mix#114,536Strength (psi) 3,000Unit Weight(lb/ft3)Workability –"Slump" (in) 2/3 normalconcrete10481.1 2”11After an extensive literature review, thereinforcement used last year, HexForceFiberglass Mesh, was compared to white andgreen stucco fiberglass mesh, welded wiremesh, and geogrid. The flexibility/workability/molding with the shape of thecanoe, percent open area (POA), and qualityof bond with the concrete were parameterscompared on the primary reinforcement. Thewhite and green stucco fiberglass mesh metthese requirements.As a secondary reinforcement measure,the team investigated internal fibers becausethe use of this reinforcement would aid in thecontrol and distribution of cracking. To selecta fiber, a test method was utilized based onASTM C1581 / C1581M - 09a Standard TestMethod for Determining Age at Cracking andInduced Tensile Stress Characteristics ofMortar and Concrete under RestrainedShrinkage. Fibers were researched and testedbased upon the following factors: aesthetics,ability to control/reduce overall cracking, andbonding with concrete. The use of therestrained shrinkage ring and sample sheettests as well as a decision matrix was utilizedto determine the best fiber. The fiber that metthis criteria was the Fibermesh 150. Thereasoning behind the categories analyzed forthe fibers are shown in Table 5.Table 5: Fiber ReasoningBased on how the fibers look inAestheticsthe concrete when placedBased on restrained ring testAbility towhich observes the sizes ofcontrol/ reducecracks occurring during curingoverallprocesscrackingBased on the fibers ability toBonding withmerge with the mix designconcretewithout causing laminationThe green stucco fiberglass mesh wastested in direct tension by hanging weightsfrom two strands until failure occurred.Figure 7 demonstrates this setup.Figure 7: Reinforcement Testing SetupThe final mix exceeded the team’s goalsof creating a strong and innovative mix. Thecombined strength of Spirit’s stuccofiberglass, Fibermesh 150 reinforcementsand concrete mix has created a unique,competition-ready product.6
SpiritNORTHERN ARIZONA UNIVERSITYConstructionThe main goals that the team wanted toimplement during the construction of Spiritincluded efficient quality control, enforcedsafetyprocedures,andaccuratereinforcement placement.The mold that was utilized for the castingof Spirit was completed by last year’s team.The mold was initially modeled inAutoCAD by splitting the hull into 15sections each at 3/4 of an inch thick. After themodeling was completed, the 15 male crosssections were cut into 3/4 inch thick pieces ofplywood which were then placed in a strongback. Next, pinewood strips were nailed intoeach cross-section and then glued to thesurrounding wood strips. Once the glue dried,the nails were removed and the mold waspatched, sanded, and waterproofed with afiberglass resin. The mold was removed fromthe strong back after the resin cured. Themold was placed in female cross-sections.The inside of the mold was sanded andapplied with the fiberglass resin while in thefemale cross-sections. It was concluded thatthe strong back could be used for futuretransportation of the canoe to conferences.Since the team decided to reuse lastyear’s mold, the primary focus was on qualitycontrol. The team explored several ideas onhow to properly control the thickness desiredper layer. After careful deliberation, twomethods were decided upon. One methodincluded cutting down pins to the lengths thatwould reflect the desired thickness per layer.The pins were cut down to 1/8 of an inch, 1/4of an inch, and 1/2 of an inch long. Four ofeach sized pins were made so that on pourday, others could assist in checking thethickness periodically. The second methodincluded calculating how much concretewould be needed per layer. It was measuredthat approximately 49 pounds of concretewas needed for the first layer as well as thesecond layer and 98 pounds was needed forthe final layer. These estimated batch weightsdid not include the material needed for thebulkheads and ribs.Pour day was set for February 8th andwith the help of volunteers from NAU’s ownASCE chapter and the Rocky MountainResearch employees lending the team itsfacility, it was a success.Pre-construction tasks began the daybefore casting day. The tasks includedmeasuring out the quantities of concreteneeded per layer and separating them intobuckets, purchasing the necessary personalprotective equipment, and preparing all toolsfor transport from the school to the facility.On casting day, a form release chemicalwas applied to the inside of the mold in a thinlayer. During this process, all volunteers hadto read and sign a safety sheet that waswritten by the team. The volunteers were thentold the desired depth for the first layer ofconcrete that was to be applied and thenbroken down into teams. Three othervolunteers assisted in thickness checks usingthe pins, two volunteers helped the concretelead in mixing and distributing the concrete,all others assisted in the application of theconcrete.The first layer was applied by hand whileconstantly being checked with the pins. Thelayer was smoothed using trowels. Figure 8depicts the careful application of concrete.Figure 8: Application of first 1/8 inch layer7
NORTHERN ARIZONA UNIVERSITYThe first layer achieved the desired thicknessof 1/8-inch. After this first layer was applied,the first layer of fiberglass mesh was placedon top of that concrete. The reinforcementlead cut down the stucco fiberglass mesh tofit the shape of the canoe. Spliced meshpieces were strategically placed within thecanoe so as to ensure that lateral crackingwould not occur due to poor placement. Toachieve this, spliced reinforcement were notplaced in areas where the max stresses werepredicted to occur. Furthermore, a 6 inchoverlap between reinforcement layers wasrecommended to help reduce any risk ofcracking due to inadequate placement ofreinforcement. Figure 9 shows a 6 inchoverlap installed into the canoe.Figure 9: Reinforcement with 6 inch overlapThe open areas within those overlappedsections were lined up to allow for the secondlayer of concrete to bond with the first layer.The team worked quickly when applyingthe fiberglass mesh in order for bond betweenthe layers to be successful. The second layerof concrete was then applied and worked byhand to bond with the first layer of concrete.After completion of the second layer, thesecond layer of reinforcement was added in asimilar fashion. The second layer was alsoSpiritspliced but placed away from the first spliceoverlaps and maximum stress locations.Finally, 1/4 inch layer was applied to reachour goal thickness of 1/2 an inch. The layerwas worked by hand to ensure bondingbetween layers. After completion, the toplayer was smoothed with trowels with anyexcess amounts of concrete removed. Duringthis process, ribs were placed and shaped inthe appropriate locations. The gunwales werekept at 1/2 inch thickness.The bulkheads were completed using aunique process. The bulkheads were formedusing two solid pieces of foam, one to formthe inside face of the bulkhead and the othertwo form the top of the bulkhead. Onceconcrete was applied to the form and allowedto cure for 7 days, a hole was drilled andspray foam was used to fill the cavity formedby the foam boards. With the foam boardsand concrete in place, the expansion of thefoam spray was controlled and excessexpansion material was allowed to dischargefrom the drilled hole.Once all concrete was placed, a black tarpwas used to create a curing tent. A cold-airhumidifier was placed inside the tent to allowthe canoe to wet cure. Additionally, the teamsprayed down the canoe with water every dayduring the wet curing process. Spirit wasallowed to wet cure for 21 days and dry curefor 7 days.After the canoe cured for the projectedamount of time, the canoe was removed fromthe mold. Any holes found within the canoewere then patched. The canoe was thensanded until the surface was smooth. Waterbased stains were applied to create a blue togold gradient on Spirit with the help of aFlagstaff local artist as well as the NAU artdepartment. A lumberjack representing thecourageous spirit of the team was painted onthe inside of the canoe. Finally, two evencoats of sealant were applied to Spirit’ssurface.8
NORTHERN ARIZONA UNIVERSITYThis page was intentionally left blank.Spirit
NORTHERN ARIZONA UNIVERSITYPROJECT SCHEDULESpirit9
NORTHERN ARIZONA UNIVERSITYDESIGNDRAWINGSpiritSpirit
SpiritNORTHERN ARIZONA UNIVERSITYAppendix A - ReferencesASCE/NCCC. (2012). “2014 American Society of Civil Engineers National Concrete CanoeCompetition: Rules and Regulations.” http://www.asce.org/uploadedFiles/Concrete Canoe/Rules and ulations.pdf September 6, 2014.ASTM (2011). “Standard Performance Specification for Hydraulic Cement.” C1157/C1157M11, West Conshohocken, PA.ASTM (2010). “Standard Specification for Air-Entraining Admixtures for Concrete.”C260/260M-10a, West Conshohocken, PA.ASTM (2011). “Standard Specification for Blended Hydraulic Cements.” C595/C595M-11,West Conshohocken, PA.ASTM (2011). “Standard Specification for Chemical Admixtures for Concrete.” C494/C494M11, West Conshohocken, PA.ASTM (2008). “Standard Specification for Coal Fly Ash and Raw or Calcined Natural Pozzolanfor Use in Concrete.” C618-08a, West Conshohocken, PA.ASTM (2011). “Standard Specification for Concrete Aggregates.” C33/33M-11a, WestConshohocken, PA.ASTM (2010). “Standard Specification for Fiber-Reinforced Concrete.” C1116/C1116M-10a,West Conshohocken, PA.ASTM (2011). “Standard Specification for Latex and Powder Modifiers for Hydraulic CementConcrete and Mortar.” C1438-11a, West Conshohocken, PA.ASTM (2011). “Standard Specification for Liquid Membrane-Forming Compounds HavingSpecial Properties for Curing and Sealing Concrete.” C1315-11, West Conshohocken, PA.ASTM (2011). “Standard Specification for Portland
After the establishment of the first NAU concrete canoe team in 1977, they qualified for the National Concrete Canoe Competition (NCCC) from 1989 to 1993. Though they had a great run of success and national appearances, NAU has failed to advance to nationals since. In 2011, Ponderosa took 7th overall at the Pacific Southwest Conference