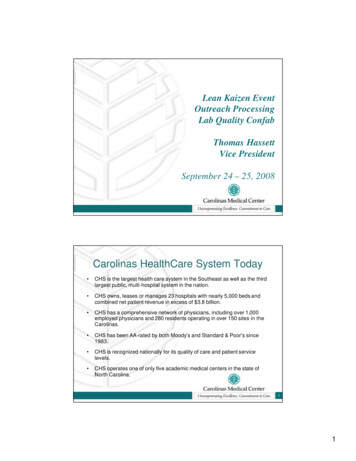
Transcription
Lean Kaizen EventOutreach ProcessingLab Quality ConfabThomas HassettVice PresidentSeptember 24 – 25, 2008Carolinas HealthCare System Today CHS is the largest health care system in the Southeast as well as the thirdlargest public, multi-hospital system in the nation. CHS owns, leases or manages 23 hospitals with nearly 5,000 beds andcombined net patient revenue in excess of 3.8 billion. CHS has a comprehensive network of physicians, including over 1,000employed physicians and 280 residents operating in over 150 sites in theCarolinas. CHS has been AA-rated by both Moody’s and Standard & Poor's since1983. CHS is recognized nationally for its quality of care and patient servicelevels. CHS operates one of only five academic medical centers in the state ofNorth Carolina.11
Carolinas HealthCare SystemExperience in the CarolinasCarolinasCarolinas HealthCareHealthCare SystemSystem owns,owns, leasesleases oror managesmanages 2323 hospitalshospitals throughoutthroughout thethe Carolinas.Carolinas.ManagingManaging thisthis diversediverse groupgroup ofof hospitalshospitals providesprovides CarolinasCarolinas HealHealthCarethCare SystemSystem anan talsininthetheregion.region.AsheWataugaMitchell eeMaconClay16SurryStokesRockingham CaswellForsythGuilford21WilkesAlexander asquotankPerquimansChowanBertieNashEdgecombe rdHospitals1. Carolinas Medical CenterAndersonLaurensFairfieldDillonKershaw2. arion3. ickSumterHorry4. CMC-UniversityLexingtonEdgefield5. CMC-LincolnCalhounAikenClarendonWilliamsburg6. CMC-NorthEastOrangeburgGeorgetownSpecialty HospitalsBarnwell BambergDorchesterBerkeley7. Levine Children’s HospitalAllendaleColleton8. Carolinas RehabilitationHampton1 8 Charleston199. Carolinas Rehabilitation – Mt. HollyJasperBeaufort10. Behavioral Health Center CMC -RandolphLeased FacilitiesHospitals11. Cleveland Regional Medical Center12. Kings Mountain Hospital13. Crawley Memorial Hospital14. CMC -Union15. Anson Community HospitalGatesHertford6411Cabarrus 2 5Harnett613 12Gaston9StanlyMoore8 71 nSpartanburgYorkUn i o nAnson26Pickens21 09ScotlandOconeeUn i o Henderson 2 wellPerson GranvilleVanceHalifaxYadkinLincoln5JacksonOwned FacilitiesBuncombeAlleghanyCounties CHS linOnslowPenderNewHanoverBrunswickManaged FacilitiesHospitals16. Grace Hospital17. Valdese Hospital18. Roper Hospital19. Bon Secours /St. Francis Hospital20. Wallace Thomson Hospital21. Wilkes Regional Medical Center22. Columbus Regional Healthcare System23. St. Luke ’s HospitalJoint Ventures/DevelopmentContracts24. Iredell Surgery Center25. Stanly Memorial Hospital26. Piedmont/Carolinas Radiation TherapyCounties with Joint OperationsWest Care and Haywood Regional2Carolinas Medical Center: ACenter of DistinctionLevel I Trauma CenterAcademic Medical CenterAdvanced technologyPreferred by consumers32
Serving Charlotte formore than a centurySt. Peters Hospital (1878)Carolinas Medical Center (2004)4Children’s HospitalBusiest pediatric acutecare center in the state53
Mecklenburg County’sHealthcare NeedsFour acute care hospitalsNetwork of physician offices6Carolinas Laboratory Network Overview? The mission of Carolinas Laboratory Network is to maintain highquality, cost efficient and timely testing for the CMC-Charlottefacilities, as well as to provide comprehensive, quality services tosupport the outpatient and physician office needs.? Carolinas Laboratory Network provides a broad range of testing toa variety of clients. CMC-Charlotte hospitals; inpatient and outpatient testing CMC-Charlotte related business (e.g. Carolinas Rehab, HealthDepartment, Behavioral Health, etc.) Carolinas HealthCare System owned and controlled entities, (e.g.Sardis and Huntersville Oaks Nursing homes, transplant services) Some regional facilities (CCHS, Anson, CMC-Union, CMC-Lincoln) Carolinas Physician Network Unaffiliated physician practices74
Carolinas Laboratory Network Overview (con’t.)? Carolinas Laboratory Network’s core laboratoryperforms approximately four million tests annually.? The outreach laboratory accounts for approximately1.7 million tests which ranks in the upper quartile 1 ofnational hospital-based outreach businesses? Core lab testing is performed at both the CMC-Mercy(anatomic pathology, molecular, and transplant) andCMC (all other areas). CMC-Pineville and CMCUniversity operate scaled down “acute care”laboratories.Source: Chi Solutions National Survey.8Carolinas Laboratory Network Volume?Outreach Volume:?2200 reqs/day?528 Client?1.8 M tests in 2007?Projected volume for 2008 is 1.9 M tests95
Why Lean Principle?Kaizen event offered a “quick hit” process change that we feltwould positively impact our overall turn around times, how early ouroutreach processing finished each night, our overtime utilization,and improve employee satisfaction?Lean principles gaining notoriety among hospitals and laboratoriesas an effective method to reduce waste?We always knew we had waste in our process but we felt lost inunderstanding how to tackle and eliminate the waste?The timing was perfect for our institution as we prepared to investcapital into space for the department. Lean could offer a chance toevaluate and maximize workflow so that we could design the spaceto fit our new processes?We realized we could no longer work harder and achieve our goals .We had to figure out how to work smarter if we were going tocontinue to have success in our outreach program10Engagement Objectives? Assess, analyze and implement streamlinedprocesses for the outreach specimen receiving andregistration area.? Use lean methods to perform a rapid design (kaizenevent) of the outreach specimen receiving area fromthe point that the couriers drop off specimens untilthey are delivered to the laboratory testingdepartments.? Determine optimal layout and work cell configuration,options to standardize work and balance staffworkload such that workflow is significantly improved.116
Kaizen Event Structure?Phase 1: Planning and Preparation1. Select an Area2.3.Select a Problem for ImprovementSelect the Team Leader4.5.Select the Team MembersPrepare the Area?Phase 2: Implementation1. Understand the Current Situation?Phase 3: Presentation, Celebration &Follow Up2.Make the Improvements12Understanding the Current Situation1.2.3.4.Observe the area and gather data? Learn to see wasteful work and identify the type of wasteMap the process? Videotape and draw spaghetti diagrams of worker movementor draw a tube travel diagramDo time studies of all operations? Time work at each stage of the process and identify wastefulwaiting? Time individual work elements and identify as value-added ornon value-addedCount work in progress? Evaluate where work is “resting” in between stages and why137
Current State Assessment: Staffing and Work Areas? Monday-Friday, budgeted staff of 16.5 FTEs are deployed to three work areas.? Working 19 employees (some part-timers); peak period from 4 PM – 12AM? Couriers finish specimen deliver around 9 PM; staffed until work is complete? Average leave time is 3:56 AM for the past 6 months; goal is 12:00 AM? Overtime is averaging 9.96% in FY 07; goal is less than 4.44%SendoutsRoomRegistrationRoomProcessing RoomCurrent State Assessment: Tube Travel Diagram How do samples move through the work area and how many stepsdoes it take to transport them from one stage to another?Total Steps 366 stepsAll the staff was walking some or all of the route often: chaotic flow,lots of people walking about, difficult to see if work was getting done?Stage 4:To Lab?Stage 2:RegistrationStage 3:Order Entry?Stage 1:Sorting Holding (storage)8
Current State Assessment:What Are the Value-Added Jobs?1.2.3.4.5.StageSortingRegistrationOrder EntryQuality ControlTransport to LabTime per Batch2:30 minutes15:00 minutes35:00 minutes5:00 minutes2:00 minutesBatch 15 patientsTotal Value-Added Activities 59:30 minutesThis is the time it should take to register a batch of 15patients with no waste in the process!16Current State Assessment:What Are the Non Value-Added Jobs?StageTime per Batch1.2.3.SortingHolding (Storage)Registration2:30 minutes45 minutes15 minutes4.5.6.Holding (Storage)Order EntryHolding (Storage)1:05 hours35 minutes1:13 hours7.8.Transport to LabQuality Control2:00 minutes5:00 minutesBatch 15 patients Inventory (waste)Total Non-Value Added Activities 3:03 hoursThese are activities that bring no value to your customers, likewaiting, human motion, overproduction, defects, inventory.179
Current State Assessment:What Is the Current Turnaround Time? Defined as the average time it takes to complete all steps in adefined process; includes both value-added and non-valueadded activities Total Value-Added Activities 59:30 minutes Total Non-Value Added Activities 3:03 hours? Seventy-five percent of the Outreach Registration cycle time isclassified as waste Most service organizations have 50-80% waste without evenknowing it Learning to see waste raises awareness and Lean tools worktogether to eliminate it from the value-added (important) workCurrent Turnaround Time 4:02:30 hours(of which 75% brings no value to your customers!)18Current State Assessment:Current Wastes? Waste of Processing?No FIFO system?Separate rooms for Sorting, Registration & OrderEntry?Separate job duties for Registration & Order Entry?Pulling reqs to sort specimens from couriers?Stopping to call for missing information?Too many old requisitions in use1910
Current State Assessment:Current Wastes (con’t.)? Waste of Inventory?Multiple waiting stages for processing?Too many supplies piled up?Supplies scattered and disorganized?Need to 5S20Current State Assessment:Current Wastes (con’t.)? Waste of Waiting?Waiting for reqs to go to Registration?Waiting for reqs to come back from Registration?Signing in specimens (fluids, bone marrows)?Slow response time from label printer?Waiting for couriers to drop off specimens2111
Current State Assessment:Current Wastes (con’t.)? Waste of Motion?Staff milling about: miscellaneous reasonsfor staff to move off their stations (get morework, move bins, make copies, solveproblems, etc.)?Moving specimens around before they go tothe lab?Computer stations all over the lab for OrderEntry?Not enough/correct materials atworkstations22Current State Assessment:Current Wastes (con’t.)? Waste of Production (Over- or Under-)?Staff leaving workstations too frequently?Batching and counting reqs?Work not moving through (due to problems)?Holding finished work at Order Entry? Waste of Transport?Moving reqs back and forth?Moving bins around to Registration and OrderEntry2312
Current State Assessment:Current Wastes (con’t.)? Waste of Defects?Separating reqs from the samples?Workers working differently in the same job?Mislabeled specimens?Lost specimens?Missing tests on reqs?Ordering wrong tests24New Process Wish List U-shaped “line” to bring processescloser togetherTeam environment (small groups)Work station that is “work friendly”Support tech role serving work celland feeding the lineOne room for all staffEliminate binsBuild QC into the line; near-time;100%Reduce handwritingLess walking around by workers Logical flow to the space FIFO Production kanban Don’t take client calls in areabefore 5 PM Inventory more organized Keep workers working (lessmotion, less personal calls) Standardized work Better process for STATS2513
Timeline for EventWeek 1Week 2DevelopTest Cell ImplementationCross TrainPlanningIdentify Current StateWeek 3Review and Tweak26Post MortemWhat WorkedWhat Didn’t Work Had more control over the pace ofproduction FIFO for sure!Some staff thought theyworked slower; some thought itwas too controlling Waste of storage is gone Staff not used to sitting so long Mixed patient type “forces”production Space constraints still an issue Workers stayed at their stationsNeed a “pre-sort” stage fromgray bins to smaller bins Stats went immediately to thefront of the line No room on station for extratubes QC done before samples get tolab Need better storage forconsumables at work stations Problems get addressed on thespot2714
Insert video clip28Future Outreach Registration AreaSix work cells will support other consolidation opportunities and/oradditional growth in outreach volume.15
Measures of Success Reduced lead-time through receiving/processing area withrapid hand-off to the automation line and other testing areas,resulting in improved overall test turnaround time Reduction in proportion of non value-added work as a percentof total work and improved staff productivity Reduction in the amount of staffovertime as an outcome of improvedworkflow Reduction in operator walking Significant reduction in wait times forunprocessed specimens Let’s check our outcomes . . .30Outcomes: Department Leave Times? Leave Times are tracked as a performanceindicator for department? Average Leave Time (past 6 months) 3:56 AM? Average Leave Time Through August is 1:08 AM? Reduction of 2 hrs and 48 minutes3116
Outcomes Current Accessions/Month of August40,874 Registration Accuracy – 99.81% Ordering Accuracy – 99.80%32Outcomes (con’t.)BeforeAfterChangeGoal(90 days)Lead Time Reduced4:02 hr2:20 hr42% decrease2:00 hrReduction in Wait Times183 min80 min56% decrease60 minWorker Steps Reduced36623735% decrease150Reduced as a % of Total Work75%57%35% decrease50%3:56 AM1:08 AM2:48 hr improvement12:00 AMLean IndicatorsLeave Time3317
The Follow Up? In many ways, kaizen events are never over? Results must be monitored? Improvements should be continually made? Monitor to do lists and complete follow-up itemsasap? Keep tracking and posting results –whatever you track will improve!34The Follow Up (con’t.)? Communication makes all the difference insuccess or failure? Continued support from the topcommunicates long-term intent? Describe what will happen over and over? Manager visible and available to answerquestions and support new way of work life? An employee idea board will improve staffownership of the new Lean culture3518
New Workflow36Questions and Answers3719
3 Serving Charlotte for more than a century St. Peters Hospital (1878) Carolinas Medical Center (2004) 4 5 Children's Hospital Busiest pediatric acute