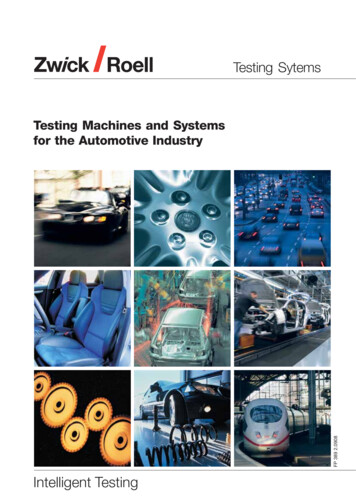
Transcription
Testing SytemsFP 389 2.0908Testing Machines and Systemsfor the Automotive IndustryIntelligent Testing
This brochure provides an overviewof testing machines, instruments andsystems produced by Zwick RoellAG and of their applications fortesting materials and componentsused in the various sectors of theautomotive industry and associatedancillary industries.As such this represents only a part ofour comprehensive overall program.Table of ContentsZwick Roell Group . 3Conditions in the Automotive Industry Today . 4Testing Situations in Research and Basic Development .Raw and Pre-Fabricated Materials .Fatigue Strength in Automobile Construction .Joining Technology in Automobile Construction .5578Testing Requirements in Series Development and Production . 9Engine and Drive Train . 9Chassis . 13Body . 20Electronics/Mechatronics . 22Interior/Safety . 24Quasi-Static Materials Testing: Products and Services . 26Hardness Testing . 26Materials Testing Machines . 28Drives for Quasi-Static Testing Situations . 30Measurement and Control Systems . 33testXpert II . 34Load Cells,Torque Cells and Load Measurment Platforms . 38Specimen Grips . 39Extensometers . 40Temperature Conditioning Devices . 43Additional Drive Options for Individual Solutions and Machine Expanding . 44Fatigue Strength and Dynamic Strength Testing: Products and Services . 45Fatigue Testing Machines . 45Components for Servo-Hydraulic Test Bench Solutions . 47Measuring and Control Electronics . 48Impact Strength Testing Machines . 52Modernization Packages for all Makes of Materials Testing Machines . 54Zwick Services . 552
Zwick Roell AG – Over aCentury of Experience inMaterials TestingMechanical testing is one of theoldest forms of materials testing. DaVinci and Galileo were alreadyturning their attention to bendingstrain and the elastic properties ofmaterials in the 15th and 16thcenturies. Time brought newinsights, culminating in theappearance of the first testingmachines in 18th-century France.Roell & Korthaus have been involvedin materials testing since 1920, whileZwick began building machines andinstruments for mechanical materialstesting in 1937. Many years earlier,in 1876, Professor Seger hadestablished a chemical laboratoryproviding scientific advice on acommercial basis to the stoneindustry. During the 20th century thisevolved into the present-dayconcern Toni Technik, leadingspecialists in the field of constructionmaterials testing systems.These companies have comprisedthe Zwick Roell Group since 1992.July 2001 saw the group become acorporation under the name ofZwick Roell AG, incorporating Zwick,Toni Technik and Indentec Ltd.Between them these companiesprovide a comprehensive materials,construction materials and functiontesting program – from manuallyoperated hardness testinginstruments to complex systems forprocess-parallel applications. AcmelLabo, the French manufacturer oflaboratory instruments for thecement, lime and plaster industry,has been part of the group sinceMay 2002.Zwick Roell AG’s expertise in sensortechnology for load and extensionmeasurement was enhanced andconsolidated by the acquisition ofGerman company GTM in 2007 andMessphysik of Austria in 2006.Zwick’s years of accumulatedexperience are reinforced by apolicy of maintaining regular contactwith our many customers. Thisprovides a solid platform from whichthe company supplies a wide rangeof products – from economicalstandard machines to customizedversions for specialized testingsituations. State-of-the-artengineering, powerful electronicsand application-orientated softwareare the keynote of these modern,versatile, highly intelligent testingmachines and systems.Zwick Roell AG is far more than justa manufacturer, however. As longago as 1994 the company receivedDIN EN ISO 9001 certification - aguarantee of consistently highproduct and service quality. Inaddition, accredited calibrationlaboratories allow companies in theGroup to inspect and calibrate testequipment and provide internationallyrecognized certification.Fig 1: Zwick Roell AG and Zwick GmbH & Co. KG: Administration Building, Ulm, Germany3
Conditions in theAutomobile Industry TodayA Comprehensive Range ofProducts and ApplicationsThe automotive market is subject tosevere global competition, markedby shifts within the vehicle segmentsand by new markets and suppliers,with resulting over-capacity.Zwick offers a comprehensive rangeof testing machines and systemsspecifically developed for the automotive industry. The program rangesfrom versatile portable hardnesstesters for use on rubber, throughmaterials testing machines, fatiguetesting machines and computercontrolled systems with actuatorsfor multi-axis testing, up to complexsystems capable of simulating actualroad conditions for components – orthe whole vehicle. An appreciation ofAgainst this background there iscontinuous growth in the use ofcomputer-based developmenttechniques. These simulation-basedapproaches must be accompaniedby actual testing during the variousdevelopment phases. For one thing,the systems require appropriatematerials data to dimension forstiffness, rigidity and life expectancy.In addition, the calculation modelsmust be calibrated as early aspossible using actual test data.Consequently laboratory testsremain a necessary and importantrequirement within vehicledevelopment.Stiffness and rigidity characteristicsof materials, components and joiningtechnology, under both standard andcrash conditions, together with theirfatigue characteristics – all rankalongside the simulation of formingprocesses as important results.Flexible modular programs, a widerange of accessories, digital electronics and intelligent user software– and all subject to continuousdevelopment and updating!VisualCustomers Priorities Fuel effiency Handling dynamics Acceptable comfort High safety factorCompetition Styling Impact QualityFinancial Return Process efficiency Short innovation cycles Cost-effective materials Production in target area Unique selling points Innovations PriceLegal / Environmental Emission reduction Recycling SafetyFactors InfluencingVehicle TechnologyTypical Areas of Responsibilityin the Automotive IndustryResearch and BasicDevelopmentSeries Developmentand ProductionOngoing ChallengesOngoing Challenges Identifying new materials for lightweight Verifying calculation models withvehicle constuction and efficient drivesystems4the whole breadth of testingapplications allows Zwick to providesoftware, data analysis tools andsolutions for laboratory informationmanagement (LIMS) – the key tomeaningful test results.actual test data Validating design decisionsOngoing ActionsOngoing Actions Releasing new materials Detremining typical materials values Quality management in productionfor simulations Determining characteristics of components for verification of simulations Examining goals Specifying/checking production limits Safeguarding production processand supply
Test Requirements inResearch and BasicDevelopmentRaw and Pre-FabricatedMaterialsZwick testing machines are used todetermine the mechanical propertiesof virtually all materials and components employed in the manufactureof automobiles.Tests on metals play a central rolehere. For example, steels and lightmetals are used in lightweightconstruction of certain areas ofbodywork. Their stiffness and rigiditycharacteristics under standardconditions are determined by meansof quasi-static testing machines. Asthese results are highly dependenton loading rate, they must also beobtained under crash conditions, i.e.using impact or high-speed testingmachines. To obtain approval of thematerial, fatigue and ductilitycharacteristics must also bedetermined.Due to the trend to alternativematerials and/or hybrid materials andtheir use in various areas of thevehicle, similar tests on plastics,elastomeres, foams and compositesare now routine in vehicleconstruction.Fig 2: Sheet metal testingFig 3: Tensile test using high-temperaturefurnaceAs the characteristics of thematerials vary to a greater or lesserextent with temperature, tests atactual working temperatures mustalso be carried out. Tests of this nature are equally essential in the fieldof joining technology: Zwick providessolutions for a temperature rangefrom -80 C to 1,600 C.Quasi-Static Testing of MetalsFig 1: Tensile test on metal specimenTesting Fatigue Strength and Dynamic Strength of MetalsFig 4: Pendulum impact testFig 5: Fatigue test on connecting rodsFig 6: Fatigue test using high-temperaturefurnace5
Quasi-Static Testing of Plastics, Rubber and CompositesFig 1: Tensile test on rubber specimenFig 2: 3-Point flexure testFig 3: Compression test on compositesTesting Fatigue Strength and Dynamic Strenght of Plastics, Rubber and CompositesFig 4: Pendulum impact testFig 5: Fatigue test on rubber dampersFig 6: Tear test with temperatureconditioning and videoXtensFig 8: Fatigue testFig 9: Rebound resilience testerTesting of FoamsFig 7: Indentation hardness test6
Fatigue Strength inAutomobile ConstructionBasic PrinciplesFatigue strength is an interdisciplinaryscience, involving interaction betweenstress, manufacturing process,material and design.Fatigue lifeThe next step in the developmentprocess is the testing of componentassemblies and the vehicle as awhole. If these are successful,development can be approved.DesignLoads(including environment)Materialpulsator). If the component’s estimated life expectancy shows it to besuitable, tests will be carried out onprototypes of the component. Servohydraulic testing machines can beused for this; Vibrophores are alsoused to some extent.ValidationVirtual PrototypesManufacturingDesignHardware PrototypesComponentEndurance testLoad distributionSystem testingCostsFig 1: Factors of fatigue strength (Source:Prof. Dr. Sonsino)Automotive engineers must thereforebe aware of the load imposed upona vehicle and/or its components,including any ‘unusual events’, inorder to estimate the fatigue strengthmathematically and by experiment.Linkage with characteristic valuesof materialsSubsystem testingComponents testingLinkage with load dataComponents fatigue life till crackFig 2: Component design process in automobile development (Source: Prof. Dr. Stauber)Determining MaterialCharacteristicsThe mechanical characteristics ofthe materials and the manufacturingquality of the components representthe input data required to measurethe fatigue strength of the components. To estimate life expectancymathematically, desig
Fig 1: Tensile test on metal specimen Fig 2: Sheet metal testing Fig 3: Tensile test using high-temperature furnace Fig 4: Pendulum impact test Fig 5: Fatigue test on connecting rods Fig 6 .