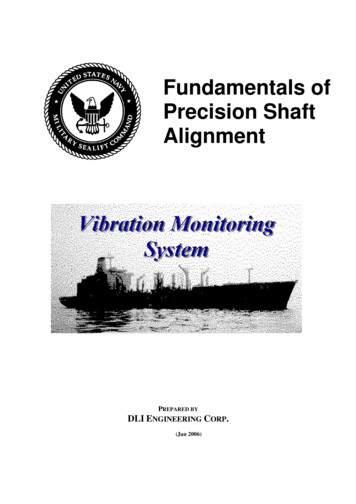
Transcription
Fundamentals ofPrecision ShaftAlignmentPREPARED BYDLI ENGINEERING CORP.(Jan 2006)
2
TABLE OF CONTENTSPreface and Table of Contents .iList of Figures and Tables.iiSafety Precautions.iiiGlossary .vi1. Introduction To Alignment .11.1 Overview.11.2 Basic Concepts.11.3 Causes And Corrections Of Misalignment .31.4 Section 1 Quiz.82. Pre-Alignment Procedures .92.1 Outline.92.2 Trial And Error Alignment Method .92.3 Dial Indicator Method .102.4 Section 2 Quiz.153. Measurements And Calculations .163.1 Outline.163.2 Three Methods .163.3 Section 3 Quiz.214. Horizontal Machinery Alignment .224.1 Outline.224.2 Alignment Procedures.224.3 Section 4 Quiz.285. Vertical Machinery Alignment .295.1 Outline.295.2 Alignment Procedure .295.3 Section 5 Quiz.366. Supplemental Information.376.1 Rim & Face Method Of Alignment .376.2 Case of Obstruction.39Workbook and Lecture Guide.41
LIST OF FIGURES AND TABLESFigure 1-1, Parallel and angular misalignment.2Table 1-1, Alignment Tolerances .2Figure 1-2, Coupling alignment.3Figure 1-3, Assembly of Indicator reverse method. .4Figure 1-4, Dial indicator placements. .5Figure 1-5, Indicator Sag .6Figure 1-6, Soft foot .6Figure 1-7, Thermal growth curve.7Figure 2-1, Effect of end play on indicator placement. .11Figure 2-2, Indicator placement for soft foot check. .12Figure 2-3, Indicator setup for checking sag. .13Figure 3-1, Measurements needed for alignment. .16Table 3-1, Alignment Formulas .17Figure 3-2, Graphing the alignment. .18Figure 3-3, Graphical representation of adjustments.19Figure 3-4, Dial indicator placement for horizontal movement. .26Figure 5-1, Dial indicator setup for checking alignment.29Figure 5-2, Dial indicator setup for correcting alignment .29Figure 5-3, Measurements for alignment check. .30Figure 5-4, Dial indicator placement for measuring bent flange.32Figure 5-5, Numbering the hold down bolts.33Figure 5-6, Indicator placement for offset adjustment. .35Figure 6-1, Setup for rim face method of alignment. .37Figure 6-2, Measurements for rim face method. .39ii
PREFACEThis manual began as a set of paper copy notes at DLI Engineering. The original authoris unknown.SAFETY PRECAUTIONSMachinery alignment is often accomplished in areas that are hazardous, unless properprecautions are observed. Equipment and materials used must be appropriate to the workarea and handled correctly to ensure safety of personnel. Constant vigilance by bothworkers and supervisors is necessary to eliminate hazardous conditions that could cause afatal or injurious accident.1.Ensure that neck chains and loose bracelets are removed or properly securedwhen working with rotating machinery or in close quarters.2.Ensure that loose clothing is properly secured when working near rotatingmachinery.3.Ensure that appropriate protective items, such as gloves, eye shields, and safetyshoes are worn to prevent injury.4.Ensure that all sources of electrical power have been secured and tagged byqualified electricians before undertaking any repairs.5.Never bypass any electrical safety or control equipment. When it is necessarythat a bypass be made for a specific test or check, only qualified electriciansshould conduct the test or check. Upon completion of test or check, the safetyor control device must be restored immediately.iii
GLOSSARYAlignmentThe process of adjusting a piece of machinery so that its shaftcenterline will be in line with the shaft centerline of the machine towhich it is coupled.AngularityIs the angle of the shaft centerline of the machine to be moved(MTBM) in relation to the shaft centerline of the Stationary Machine(SM). The angle amount is expressed in rise over run (Thousandthsof an inch per inch), rather than in degrees.Back FeetMachine supports opposite the coupled end. Sometimes these arereferred to as the free end or as the outboard feet.Cold Alignment This is intentional angularity and offset misalignment entered into themachine to be shimmed, during the cold alignment check, tocompensate for thermal growth. Always establish and verify a"Corrected Cold Alignment Specification".Cold Alignment SpecificationSome manufacturers provide a cold alignment setting that allows thealignment engineer to know how thermal growth will affect the finalrunning alignment. The manufacturer's technical manual should beconsulted to obtain this setting.Face ReadingReadings obtained with a dial indicator as both shafts are rotatedwhen the centerline of the dial indicator stem is set parallel to theshaft centerline.Front FeetThe machine supports on the coupled end, also known as the drivenend or inboard feet.Horizontal MisalignmentMisalignment which requires horizontal movement of the machine tobe moved (MTBM) for correction. Shims are not typically used tocorrect horizontal misalignment.Hot Alignment CheckThe act of measuring shaft alignment after the machinery has beenoperated for a period sufficient to allow it to attain its normaloperation temperature and therefore undergo thermal growth. Thischeck should be performed as soon as possible after securing the unit.iv
Indicator SagThe bending of the indicator mounting hardware caused by gravity. Itoccurs when the shaft is rotated and the dial indicator moves from the“Top” position to the "Bottom" position.Jacking BoltsBolts on the machine foundation located at each foot used to adjustthe horizontal or vertical position of the machine.MTBMMachine to be moved or the machine which will have shims installedunder its feet. This will normally be the prime mover (e.g. electricmotor, steam turbine). Driven components (pumps, compressors),constrained by pipe connections, are not good candidates for theMTBM.OffsetThe amount of distance between the centerlines of each machine shaftwhen measured at the coupling center. Offset is typically expressed in"thousandths of an inch" or "mils".Rim ReadingsDial indicator readings obtained as the shafts are rotated and thecenterline of the dial indicator stem is set perpendicular to the shaftcenterline.Total Run-outThe total radial deflection of a shaft with respect to a fixed point asthe shaft is rotated through one complete revolution. Often called TIRfor total indicated run out. This measurement can also be performedin the axial direction when measuring a gear or pulley.Skewed MisalignmentCombination of parallel offset, and angular misalignment.Soft FootThe condition which exists when all of the machine's feet are notequally supporting the weight of the machine. Similar to a fourlegged chair with one of the legs slightly shorter than the other three.Stationary Machine (SM)The term "Stationary Machine" will be used to describe the machinethat will not be adjusted, usually the driven machine.Thermal Growth The expansion of a material which occurs when its temperatureincreases from room temperature to operating temperature.TIRTotal indicator reading. This is the total deflection of the dialindicator pointer between the furthest deflection positive to thefurthest deflection negative.Vertical Misalignmentv
Misalignment which requires movement of the machine in the verticaldirection for correction. Vertical movement is often accomplishedwith shims.Zero (O)The process of setting the dial indicator face to "zero" (O).vi
1.INTRODUCTION TO ALIGNMENT1.1OVERVIEWUpon completion of this lesson, the trainee will be able to:1.Explain the importance of using proper equipment for alignment.2.Explain two types of misalignment.3.Explain and define common alignment terminology, techniques, and tolerancesfor Pump-Driver alignment.4.Define the effects thermal growth has on shaft alignment.5.Explain the use of dowel pins in machinery alignment.1.2BASIC CONCEPTSA. GeneralThis guide will provide the trainee with the information necessary to performaccurate alignment of machinery shafting. The term "accurate" needs to beemphasized. Misalignment is measured in mils, thousandths of an inch. A smallalignment error can cause considerable vibration, and accelerated machine wear.Proper alignment plays an important role in the ability of a machine to providelong, reliable, service. Thus, accurate alignment is an important contributor toreduced maintenance and increased machinery plant readiness. The driver anddriven machine shaft centerlines (not the coupling halves) must be properlyaligned, ideally forming a straight line.B. Angular and Parallel MisalignmentShaft misalignment is usually a combination of angular misalignment and paralleloffset (refer to Figure 1-1). After alignment, both of these must be withinspecified tolerances. Adjustment is made in two planes, vertical and horizontal,for horizontally mounted equipment, "Back-Front" and "Left-Right", for verticallymounted units.
Centerlinesmeet atcoupling centerAngularityOffsetAngular MisalignmentParallel MisalignmentFigure 1-1, Parallel and angular misalignment.C. Alignment Tolerances1.Misalignment in excess of recommended tolerances will result in frequentrepairs to such machinery components as couplings, bearings, sleeves, packing,mechanical seals, etc.2.Recommended maximum allowable alignment tolerances for pump-driverunits are given in Table 1-1. These tolerances are given for units in a hot, i.e.normal operating temperature, condition and are stated in terms of angularityand offset.Table 1-1, Alignment TolerancesNEW INSTALLATIONRPMOFFSETANGULARITY0-40004000 & UP 2.0 mils 1.0 mils 0.500 mils/in 0.250 mils/inIN-SERVICERPMOFFSETANGULARITY0-2000 5.0 mils 1.000 mils/in2000-4000 4.0 mils 1.000 mils/in4000 & UP 2.0 mils 0.500 mils/in2
1.3CAUSES AND CORRECTIONS OF MISALIGNMENTA. Causes of Misalignment1.Misalignment can occur by the loosening of hold-down bolts, mechanicalshock, sh
4. Dial indicators are then attached in the Reverse Indicator fashion as shown in figure 1-3. Measurements are taken and the adjustments are calculated from the readings. Figure 1-3, Assembly of Indicator reverse method. 5. The driver, or machine being moved, is