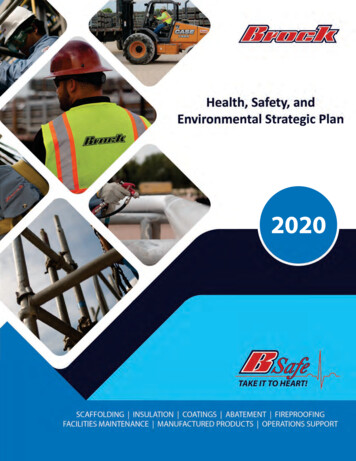
Transcription
Table of ContentsBrock Vision, Mission, and Values . 4Message from the Vice President of Health, Safety & Environmental . 6Tools of Engagement . 7Bbest and Bsafe: Better Together . 10Bbest: Better Every Day . 112019 Craftsperson of the Year . 122019 Supervisor of the Year . 142019 CEO Site of the Year. 162019 HSE Recognition . 18Brock HSE Core Elements System . 222020 Corporate HSE Initiatives . 32HSE Training Program . 40Bsafe Initiatives Monthly Focus Calendar. 41American Fuel & Petrochemical Manufactures (AFPM)Contractor Achievement Award - Brock Industrial ServicesBayway Refinery of Phillips 66Brock received 42 AFPM Contractor Achievement Awards in 2019 2020 The Brock Group10343 Sam Houston Park Dr., Suite #200 Houston, TX 77064 1 281.807.8200*Bsafe is a mark of Brock Holdings III, Inc.www.brockgroup.com 2020 HSE Strategic Plan 3
Message from the VP of Health, Safety & Environmentalown duties. It extends to our partners and customers onthe job site. In a highly hazardous industry such as ours,safety is an investment that consistently delivers real benefits. A safe work environment helps to keep skilled employees on the job and projects on track. I am proud tosay Brock employees work in the safest manner possibleand our programs are consistent with best-in class safetypractices.The 2020 HSE strategic plan establishes the expectationsand minimum requirements to govern all operations forBrock. All employees are required to report any hazardous activities to their supervisors and to exercise constantvigilance. It is a condition of employment at Brock that allemployees comply with the requirements of this programand the safety regulations and procedures issued in conjunction with it. All employees have the full support ofmanagement in enforcing the provisions of this policy.Ultimately, we must remember that Brock is committed toproviding a zero harm work environment for all employees,subcontractor employees, temporary employees, jobsitevisitors, and members of the public. We must work together Helping Everyone Reach Zer0, as we are all accountablefor our performance.Our dedication to safety must be unwavering.Brock’s reputation is one of our most valuable assets andpreserving it is essential to retaining our talented employees and loyal customers. We’ve worked hard over theyears to build our reputation as a safety-focused company,a distinction earned through the actions of our employees.However, like all reputations, all it takes is one questionable act to damage it. Therefore, our continued successhinges on our employees being engaged with our safetyprograms every day.Bsafe is our approach to making safety personal. As an extension of our culture of respect and caring, Brock’s Bsafeculture is backed by the company’s commitment to anincident-and-injury-free environment. This commitmentinvolves principles that include making safety personal, always intervening, taking pride in quality work, and achieving operational excellence. These guiding principles serveto support every decision made across the company at alllevels.We continually seek to improve all aspects of our safetyperformance, but particularly our leadership and engagement at every level. Engagement goes beyond making surewe are physically and mentally prepared to perform our6 2020 HSE Strategic Plan www.brockgroup.comDrew Ashcraft, CSPVice President of Health, Safety, & Environmental
Tools of EngagementEngagement is a workplace culturethat inspires all members of an organization to give of their best each day,commit to their organization’s goalsand values, and contribute to organizational success, with an enhancedsense of their own well-being.Engagement is based on trust, integrity, and two-way commitmentand communication between an organization and its members. It is anapproach that increases businessand safety success, contributing toorganizational and individual performance, productivity, and well-being.Leadersdriveengagement.Employees are more actively engaged when their supervisor actsconsistently, keeps the employees’well-being in mind, coaches for improvement, and exhibits traits of aBrock HER0, such as honesty, integrity, and veracity.At Brock “Be a Her0” is not just a slogan. It is a call to action. It is a demandto use our tools of engagement to befully immersed in our company’s wellbeing and the wellbeing of all of ouremployees.Our tools of engagement requiremore than meeting the minimum requirements; this means employeeswilling to go the extra mile, provideinnovative ideas, uphold their commitments and, most importantly, being engaged.When we utilize Bsafe, Respect andCaring, HER0 observations, pre-taskhazard analysis, peer conversations,performance measurements, stopwork authority, taking safety outsideof the work place, and taking safetyto heart, we can fulfill our industry'sneed for a workforce of employeesthat display characteristics of providing the best for their company andcoworkers.Each day, we have the opportunity to go above and beyond by beingengaged with our fellow employees,customers and communities. Will youseize the opportunity today?www.brockgroup.com 2020 HSE Strategic Plan 7
Bsafe and Bbest: Better TogetherBsafe is our approach to making safetypersonal. As an extension of our culture of respect and caring, Bbest is theembodiment of our relentless pursuitof, and overall commitment to, operational excellence.Our pledge to establishing a Bsafe culture is backed by our commitment toan incident and injury free environment. We understand that developing a long-term, sustainable culturebegins with making safety personal.Our corporate culture is built on interdependency, with each employee fullyengaged to work safely and be motivated “so no one gets hurt!”The Brock standard of caring and respect defines who we are and howwe operate to achieve excellence inevery aspect of our business. Bsafebegins with personal responsibilityfor our own safekeeping and extendsto include our fellow employees,our customers, our families, and ourcommunities.The Brock Bbest business objectivesand the values and attitudes of theBrock Bsafe culture work in conjunction to achieve our desired results ofbeing “Better Every Day”. We knowthat we cannot be “Better Every Day”by following a single path. Obtainingthese types of results are only achievedby harmonizing operational and safetyexcellence principles.Research by OSHA points out thatcompanies with excellent safety typically have a culture in which everyonefeels accountable and that successfulorganizations have integrated safetyinto their work processes so that safety isn’t something additional to do; it'show they get the job done.“First Pass Quality” and “Zero HarmWorksites” are unified results that arereached through a journey of mirroredelements essential to a mutual culture.Bbest and Bsafe are synonymous anddefy the perception of a non-cohesivesafety and production relationship.SafeTAKE IT TO HEART!10 2020 HSE Strategic Plan www.brockgroup.comOur culture combines: Best in Class Quality ServiceZero-Harm WorksitesStrategic PartnershipsRespect and CaringContinued GrowthMaking Safety PersonalTaking the company's mission, goals,values, vision, beliefs and behaviors,and assimilating them into our desired results is our main priority hereat Brock. Within the company, safetyand production work together to promote the big picture of our Bbest andBsafe culture. By working together, weare able to become “Better Every Day”by using these proven successful business qualities as our foundation.
Bbest: Better Every DayAs part of our ongoing commitment toall our stakeholders – our customers,investors, employees, and communities in which we work – we emphasizea company-wide culture of continuousimprovement.Bbest is Brock’s culture of seeking thebest possible ways to achieve our strategic goals and vision. Bbest brings together planning and accountability toensure best practices go beyond sharing to become standard procedurethroughout our organization.Our focus on being “Better Every Day”is based on our shared values of respect and caring. Bbest has five keyelements: Leading safety performance in our industry Building a strong teamfrom many individuals Delivering the same performanceexcellence to all customers Creating a solid future foreveryone who works at Brock Profitably growing revenuefor all our stakeholdersFor our customers, Bbest drives multiple benefits, particularly when combined with our strong safety culturethrough Bsafe and our execution approach built on alignment with eachcustomer’s goals and metrics. Bbestfor customers means: Consistency in service deliveryacross projects and facilities Continuous improvement inproject and maintenance safety,engagement, and performance Better services and solutionsplatforms based on customerfeedback and market needs Stronger alignment on customer goals and success metrics Proactive and responsivesupport functions for timely resolution of issuesBbest allows us to combine the verybest ideas, practices, and processes from Brock’s abundant talent intothe expectations for how we operate. Bbest requires that we improveconstantly and without hesitation tosupport our commitment to being thevery best.Brock’s leadership has also made acommitment that these practices andideas will be evaluated, prioritized,and implemented based on the value to our company, employees, andcustomers.Across Brock regions and businessunits, we are all committed to thestandardization of excellence in howwe execute our work, behave and support each other, both internally andexternally.Bbest is an ever-rising target in ourconstant pursuit of the next level ofexcellence for safe and flawless service delivery, consistent execution tostandards, and employee engagementand development, ultimately drivingprofitable revenue growth.www.brockgroup.com 2020 HSE Strategic Plan 11
2019 Craftsperson of the Year: Kaylyn BestThe Craftsperson of The Year award ispresented annually in recognition ofoutstanding professionalism and workethic. It also recognizes those who foster Brock’s commitment to caring andrespect for others. This year’s awardrecipient, Kaylyn Best, has been withBrock Canada for seven years workingin scaffolding.Kaylyn received seven nominationsfrom co-workers in a variety of positions at her facility. Overwhelmingly,the nominations described Kaylyn asa caring mentor who embodies whatit means to be a good leader. As amentor, Kaylyn is patient, yet stern asshe instills safety practices and properscaffold building techniques with allher mentees.She is genuinely dedicated to Brock’sBsafe culture and is not only a HER0who calls attention to potential hazards within her work areas, but alsorecommends solutions to eliminatethose hazards when they are found.Kaylyn’s work-ethic is also widely noted among the customer and her peers.She takes great pride in her work andis a positive representative for Brock.She goes above and beyond every dayand her team truly appreciates herdedication.Mike Nameth, Kaylyn’s supervisor, described an example of one of Kaylyn’sHER0 moments stating that she wasworking with a crew to erect a scaffold in a confined space when sheKaylyn BestCraftsperson of the Year12 2020 HSE Strategic Plan www.brockgroup.comidentified a valve that was not properly locked out. She used her stop workauthority, then notified the client ofthe potential hazard. This act provideda safe workspace for the entire crewand allowed them to complete theproject without incident.Kaylyn has been promoted toSupervisor since receiving the CEOCraftsperson of the Year Award andhopes to be able to earn the CEOSupervisor of the Year Award for 2020.Thank you, Kaylyn, and congratulations on being named Craftsperson ofthe Year.
www.brockgroup.com 2020 HSE Strategic Plan 13
2019 Supervisor of the Year: Burnell HowardThis award identifies the Brock supervisor who continuously performedhis or her daily tasks in an exemplarymanner and one whose leadershipachievements promote and foster anincident and injury-free work environment based on respect and caring.Amongst several nominations, thisyear’s award goes to Burnell Howard,the General Foreman at ExxonMobilePlastics Plant in Baton Rouge, LA.For many years, Burnell worked as themaintenance scaffolding general foreman, but in recent years has been theproject and turnaround multi-craftgeneral foreman. He has made a respectable name for himself at BRPP asa model supervisor for others to emulate in regard to safety, performance,expectations, and job execution.Burnell has been recognized as anexceptional advocate for safety andBrock’s Bsafe culture of respect andcaring. His execution of safety relatedprograms is far above what is expected. For example, each month Burnellwill often exceed the expectation ofloss prevention of observations com-Burnell HowardSupervisor of the Year14 2020 HSE Strategic Plan www.brockgroup.completed and exceeds quality expectations as well.Burnell’s crews are a direct reflectionof his leadership and dedication toBrock’s values and safety initiatives,as well as his dedication and commitment to champion ExxonMobil’s LPSprogram into Brock.Thank you, Burnell, and congratulations on being named Supervisor ofthe Year.
www.brockgroup.com 2020 HSE Strategic Plan 15
2019 CEO Site of the Year: BSL at CPChem Cedar BayouChevron Phillips Chemical – CedarBayou facility in Baytown, Texas is located in the heart of the Houston ShipChannel region. The facility is situated on 1,800 acres with 33% devotedto petrochemical manufacturing. Theremaining acres are used for specialprojects and greenspace.The Cedar Bayou facility is a participant in the OSHA Voluntary ProtectionPrograms (VPP) and has been nameda Star Site six times. There are 12 VPPcompanies working at the Cedar Bayoufacility, including Brock Services.The Brock crew at this site has seen agreat deal of change over the past fewyears. They peaked at 550 employeesduring the summer of 2018. Just twoand a half years earlier, they had justover 150 employees.In August 2017, Hurricane Harveyflooded the plant with over 6 feet ofwater across the entire facility. Thechallenges that followed cannot beoverstated. Most of the plant wasstill not operating at the beginning of2018, and the Brock compound didnot have electricity.Despite the tough environment, sitemanagement was able to leveragebest practices and move forward. Theyadopted a "back to basics" approachto safety as they navigated throughthe unique challenges of operating in aplant with little to no power, and over300 employees working 7-12's. Allwhile managing a SSW program with aturnover rate of over 10%.The team’s commitment to Brock’sBsafe culture was strengthened andwas proven by their safety statistics.The site achieved almost two million work hours without a recordableincident.In 2018, Brock also played a key rolein the commissioning of a new unitonsite, which is one of Chevron Phillipslargest expansions in its history. Theteam was called on to close several gaps left by previous contractors.Due to Harvey, CUI work has continued to run strong and required Brockto maintain a team of over 400 employees throughout 2018. The crewslogged extended years for continuedHarvey recovery, new unit commissioning, CUI work, and maintenance.Though classified as a large site, thereis a deep sense of unity amongst theentire crew. The bond was forged asthey navigated the floodwaters ofHarvey and achieved a new level ofoperational excellence. They are driven by Brock’s culture of caring andrespect that they truly have for oneanother.Congratulations to everyone involvedin making Chevron Phillips Chemical –Cedar Bayou the CEO Site of the Year!Chevron Phillips Cedar Bayou site team with their CEO Site of the Year Eagle Award16 2020 HSE Strategic Plan www.brockgroup.com
2019 HSE RecognitionBrock takes pride in achieving an incident-free culture of respect and caring. Over the past year, The Brock Group has received multiple awards that signify our commitment to an incident and injury free work environment that strives toward aZero harm culture. Below is a list of awards our company has received over the past year:VPP (Voluntary Protection Programs) Region VI Star of Excellence Award— Americas Styrenics St. James— Chevron Phillips Cedar Bayou Complex— Chevron Phillips Pasadena Plastics Complex— Chevron Phillips Sweeny Complex— Dow Chemical OCD— Dow Chemical Freeport— ExxonMobil Beaumont— Flint Hills Resources Port Arthur— Phillips 66 Borger Refinery— Phillips 66 Lake Charles Refinery— Phillips 66 Sweeny Complex— Rubicon Geismar— Valero Ardmore Refinery— Valero Houston Refinery— Valero Three Rivers Refinery Region VI Super Star Award— Valero Texas City RefineryAFPM (American Fuel and Petrochemical Manufacturers) Award for Meritorious Safety Performance— BP Whiting Refinery (Brock Industrial Services)— Chevron Pascagoula— Chevron Salt Lake Refinery— Chevron Phillips Cedar Bayou Complex— Chevron Phillips Pasadena Plastics Complex— Chevron Phillips Sweeny Complex— CITGO Corpus Christi Refinery— CITGO Lake Charles Manufacturing Complex— CITGO Lemont (Brock Industrial Services)— CITGO Lemont— Dow Chemical Deer Park Plant— Dow Chemical La Porte Site— ExxonMobil Baytown Olefins Plant— ExxonMobil Baytown Refinery— ExxonMobil Beaumont Chemical Plant— ExxonMobil Beaumont Polyethylene Plant— ExxonMobil Beaumont Refinery— HollyFrontier Cheyenne Refinery— HollyFrontier Tulsa Refinery— INVISTA Victoria Plant18 2020 HSE Strategic Plan �———————————Koch Industries Port ArthurKoch Industries Houston ChemicalLyondellBasell Channelview ComplexLyondellBasell Corpus Christi ComplexLyondellBasell La Porte ComplexLyondellBasell Lake Charles Polymers PlantLyondellBasell Matagorda ComplexPBF Energy Chalmette RefineryPhillips 66 Bayway Refinery (Brock Industrial Services)Phillips 66 Borger RefineryPhillips 66 Lake Charles ComplexPhillips 66 Sweeny ComplexRubicon Geismar PlantTotal Port Arthur RefineryValero Ardmore RefineryValero Houston RefineryValero Port Arthur RefineryValero St. Charles RefineryValero Texas City RefineryValero Three Rivers RefineryWestlake Chemical Lake CharlesWestlake Chemical Natrium West VirginiaAssociation of Builders and Contractors ABC STEP Diamond Award— Central Florida Chapter— Greater Houston Chapter— Pelican Chapter— Texas Coastal Bend Chapter— Texas Gulf Coast Chapter— Texas Mid Coast ChapterGreater Baton Rouge Industry Alliance Safety Recognition AwardGulf Coast Safety Council— Innovation Award— Specialty Large Contractor AwardChevron Refining Chevron Salt Lake City— Chevron’s Contractor Gold Award
Houston Business Roundtable Mentor - Specialty Contractor Soft Crafts LargeThree Rivers Manufacturers' Association Gold Award— Brock Services— Brock Industrial Services Meritorious Award— Brock Services— Brock Industrial ServicesContractor Safety Council of the Coastal Blend Safety Excellence Award— BASF Bishop— Celanese Bishop— CITGO Corpus Christi— INVISTA Victoria— LyondellBasell Corpus Christi— Valero Three Rivers— Voestalpine TexasExxonMobil Baytown Safe Operation Index Gold Medal Award Excellence in Safety Performance— Outstanding overall safety performanceOne Million Exposure Hour CategoryNational Maintenance Policy Agreements Committee Zero Injury Safety Award— BP Whiting— Citgo Lemont— Procter & Gamble Lima— PSEG BridgeportUtah Safety Council Perfect Record Award Seatbelt Safety Award Robert F Parenti Individual Achievementin Safety – Josh CaronSafety Council of Southwest Louisiana Specialty Contractor Best in Class Specialty Contractor GoldNorthwest Indian Business Roundtable Contractor Safety Award (Brock Industrial Services)Golden Triangle Business Roundtable Finalist Award— ExxonMobil Beaumont Refinery Meritorious Award— Dow OrangeDow Chemical Freeport Best in Class Award Safety Excellence AwardPhillips 66 Bayway Refinery Craftsperson of the Year— Mike Craftsmen of Brock Industrial Services Contractor of the Year— Brock Industrial ServicesExxonMobil 2018 Shining Star for Outstanding Commitment andContributions to BTCX's Journey to LPS Excellence— 2018 Outstanding Safety Performanceand Achieving the Goal of "Nobody GetsHurt"Outstanding overall safety performanceOne Million Exposure Hour CategoryJosh Caron received the Robert F. Parenti IndividualAchievement in Safety Award from Utah Safety CouncilPresident, John C. Wojciechowskiwww.brockgroup.com 2020 HSE Strategic Plan 19
Brock HSE Core Elements SystemThe Brock HSE Core Elements System is a comprehensive safety process integrated into Brock’s core business model.Because most operations focus on staffing, training, and equipping the soft-skilled labor force, the HSE Core ElementsSystem is built around that business cycle. The core elements system includes a defined organizational culture, a processfor hiring and training new employees, a comprehensive hazard recognition program, and a program to measure theresults. This integrated system provides a full-spectrum approach to improving human performance. With this model,Brock is able to include additional HSE requirements depending on the client specification, local regulations, and taskrequirement, so that the company HSE model can be effective for job sites of any size across a variety of service offerings.This section details the system elements.BsafeSafety cultures consist of shared beliefs, practices, and attitudes that exist across an establishment. The Bsafe culture is the culmination of all we do to ensure Zero Harm.Measures include promoting an atmosphere to create beliefs and attitudes that shape behaviors, focusing on a positive impact, and fostering a culture of respect and caring.The Bsafe culture brings all levels of our organization together to work on common goals that everyone holds inhigh value and will strengthen the organizational culture.It encourages everyone to feel responsible for safety andpursue it on a daily basis. It also encourages everyone to gobeyond “the call of duty” to identify unsafe conditions andbehaviors, and then intervene to correct them. Our Bsafeculture drives an attitude of caring and fortifies our beliefthat ZERO is an attainable goal.Bsafe CommitmentThe Brock Bsafe commitment is the personalization of thecompany’s commitment to achieving zero harm at theworksite. Brock believes every individual deserves a cultureof respect and caring. Therefore,as a company we commit to: Making safety personal Always intervening Taking pride inquality work Committing to HSEcore elements Achieving operational excellence Being a HER0 by “HelpingEveryone Reach ZER0” through interventionThese are guiding principles which serve to support everydecision made in the company at all levels. They are an expectation of performance and are inherent to what we do.22 2020 HSE Strategic Plan www.brockgroup.comBsafe Rules for LifeBsafe Rules for Life is at the heart of our safety vision andthe result of our ongoing commitment to safety. Theserules are used to mitigate risk and reduce potential injuries,and are intended to supplementand support existing companymanagement systems, proprograms, and policies.Bsafe Rules for Life focus on modifying workerand supervisor behaviors in the workplace byraising awareness of activities that are most likelikely to result in catastrophicevents. Such activities include:falls, permit violations, isolationof energy sources, confined space entry, disabling safetydevices, use of drugs and alcohol, working under suspended loads, and a willful lack of intervention. We all have aresponsibility to comply with the Bsafe Rules for Life andto personally intervene if we feel others may be workingunsafely.Our Bsafe Rules for Life have a zero tolerance enforcementand underpin our safety values and vision. Compliance isofrequired by everyone, whether office based or on the front line.CARE ProgramWe want our employees to be able to focusat work as life continues outside the workenvironment. To helpour employees deal withproblems that life canpresent, we offer counseling
service with a CARE (Caring and Respecting Everyone)Representative that is available to all employees 24/7. Theservices provided include: assisted guidance with family,substance abuse, depression, and emotional and spiritualquestions and concerns. CARE Representatives regularlyschedule visits to worksites and numbers are posted tocall between visits. The confidentiality of using the CAREProgram service promotes employee involvement and proactive assistance makes this program a successful benefitto our employees.Bsafe HER0We have all heard the word“hero” from time to time,but have you ever askedyourself “What is a hero?”Is a hero someone weadmire, respect, andlook up to, or is a herosomeone with “superpowers”?While there are many ininterpretations of what a herois, Brock considers a Bsafesafe HER0to be someone who transforms respect and caring into heroic actions. It takes more thanrandom acts of kindness to make a Bsafe HER0. It requiresacts that are very distinct and direct; a hero is a person whointervenes.Brock believes that everyone has the power and abilityto be a Bsafe HER0. We may not have super powers likeX-ray vision or super strength, but we all possess the personal qualities of respect and caring, which are the greatest attributes of all superheroes. Those qualities make ourworkforce a League of Heroes and fosters a work environment of ZER0 Harm, ZER0 Quality Defects, and ZER0 RuleViolations.Best Foot ForwardIn general, slips and trips occurdue to a loss of traction bebetween the shoe and thewalking surface or inad-vertent contact with afixed or movable object. Walking is considered routine however,the risk of injury is high.Although we naturallyplace as much “regular”or “routine” things we dounder autonomic control, wemust stay aware of what is around us when we are movingabout. This Emphasis helps employees to put their “BestFoot Forward” focusing on the elimination of hazards related to walking/working surfaces.OSHA VPPThe OSHA Voluntary ProtectionProgram (VPP) promotes effeceffective worksite-based safetyand health. By participat-ing in VPP, management,labor, and OSHA establishcooperative relationshipsat workplaces that haveimplemented a comprehensive safety and healthmanagementsystem.Approval into VPP is OSHA’sofficial recognition of the outoutstanding efforts by employers and employees who have achieved exemplary occupational safetyand health.As a company, we have decided to pursue VPP status because meeting the minimum expectations is not sufficient;we continuously seek to excel and be the best of the best.With this goal in mind, we structured our safety and healthmanagement programs to go above and beyond any regulatory or industry expectations. A jobsite that is adequatelyapplying our safety and health programs is already prepared for the rigorous auditing required in the VPP process.The thought process and commitment to VPP allows us tomeet our expectations and the high expectations of VPP.Corporate Recognition ProgramReinforcement of safety perforperformance should be positive,proactive, and designed tohelp employees understand when, where, andwhat forms of safety behaviors are expected.Recognizing and rewarding employees for compliance with safety protocols,successful progression, andachievement towards theirdesafety goals is one way to develop and, more importantly, reinforcean organizational norm that working safely is valued andexpected.www.brockgroup.com 2020 HSE Strategic Plan 23
BsafeWe, as a company, have developed a structured programwith a clear path to success through all levels of the corporation with recognition at the individual, site, corporatelevel, and, finally, with a Presidential Recognition from ourCEO. The required criteria are in the form of well-definedsafety goals, regular feedback, goal reinforcement, andclearly outlined recognition paired with specific behaviorsor outcomes.in lower accident and injury rates that will consequentlyderive benefits in terms of reduced absenteeism, turnover,workers’ compensation expenses, and increased employeemorale and productivity.Simply put, recognizing employees with exceptional safety performance improves the overall effectiveness of ourhealth and safety well-being.We believe that a strong commitment to safety will resultOnboardingBrock will hir
2020 The Brock Group 10343 Sam Houston Park Dr., Suite #200 Houston, TX 77064 1 281.807.8200 *Bsafe is a mark of Brock Holdings III, Inc. American Fuel & Petrochemical Manufactures (AFPM) Contractor Achievement Award - Brock Industrial Services Bayway Refinery of Phillips 66 Brock received 42 AFPM Contractor Achievement Awards in 2019