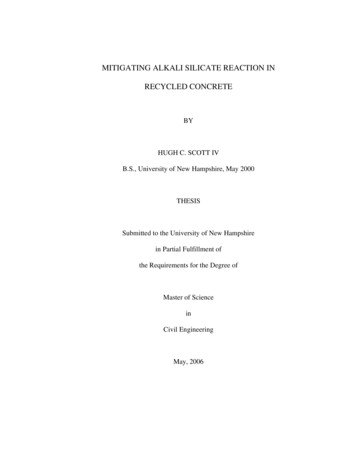
Transcription
MITIGATING ALKALI SILICATE REACTION INRECYCLED CONCRETEBYHUGH C. SCOTT IVB.S., University of New Hampshire, May 2000THESISSubmitted to the University of New Hampshirein Partial Fulfillment ofthe Requirements for the Degree ofMaster of ScienceinCivil EngineeringMay, 2006
This thesis has been examined and approved.Thesis Director, Dr. David L. Gress, ProfessorDr. Charles H. Goodspeed, Associate ProfessorDr. Jo Sias Daniel, Assistant ProfessorDate
DEDICATIONTo my parents that have always been there for guidance and given me the lifetools I use everyday to make myself a better person. I think of you both everyday andhope that I can make you as proud of me as I am of you. I could not have asked for abetter childhood, family, role-models, or friends. You are two very special people thathave shown me through example was it means to live life to the fullest. I love you bothvery much.iii
ACKNOWLEDGEMENTSDr. David L. Gress has served not only as an excellent advisor through thecompletion of this degree, but also with his knowledge in the field of Civil Engineeringand into my professional advancements. I have ever-lasting respect for his abilities as aprofessor, researcher, and advisor for students at the University of New Hampshire. Hehas taught me the importance of staying focused on goals and never being intimidated toapproach projects that require persistence and hard work to complete. I appreciate allthat he has done to give me the opportunity to continue my studies at the University ofNew Hampshire and reach the goal of a Master’s of Science degree. I look forward tocontinuing our relationship on a professional and personal basis.I would like to extend a special thank you to all of the people that made thisproject possible through research funding and development. This project would not havebeen possible without your contributions.iv
TABLE OF CONTENTSDEDICATION . iiiACKNOWLEDGEMENTS. ivTABLE OF CONTENTS .vLIST OF TABLES . ixLIST OF FIGURES .xABSTRACT. .xvCHAPTERPAGE1. INTRODUCTION .1INTRODUCTION .1PROJECT OBJECTIVES .3RECYCLED CONCRETE AGGREGATE (RCA).4ALKALI SILICATE REACTION (ASR) .9Reactive Aggregates .10Alkali.11Calcium.12Water .12MITIGATION PROCEDURES.13RCA: A NEW AGGREGATE SOURCE .13STANDARDIZED ASR TESTING .14v
Testing Modifications.152. MATERIALS .16INTRODUCTION .16MATERIALS.16Aggregates .16Cementitious and Mitigation Material .22MITIGATION MATERIALS .24Low Alkali Cement.24Class F Fly Ash .25Ground Granulated Blast Furnace Slag (GGBFS) .26Lithium Nitrate (Lifetime ).27Silica Fume .283. METHODS .30INTRODUCTION .30TESTING OVERVIEW.30LABORATORY PROCESS .31Specimen Preparation .31Specimen Mixing and Curing.32Specimen Testing .35Modified Testing Procedures.38ASTM C 1260 Prism Beam.39ASTM C 1260 Cube .39ASTM C 1293 Cube .41ASTM C 1293 Electrical Cylinder.43vi
Specimen Measuring .45Material Property Testing .45TESTING DEVELOPMENT.47PRELIMINARY TESTING .47MIX DESIGNS .50Mixture Overview.514. RESULTS .53INTRODUCTION .53PRELIMINARY TEST DEVELOPMENT .53TESTING RESULTS .54Rapid Testing Procedures.54ASTM C 1260 (Mortar-Bar Testing) .54ASTM C 1260 (Modified Prism Beam Test) .64Standard Testing Procedures .73ASTM C 1293 (Standard Prism Beam) .73ASTM C 1293 (Standard Prism Beam) w/ saturationtechniques .83Modified Testing Procedures.90Vacuum-Sealed Cubes (ASTM C 1293 Modification) .90Electrical Cylinders (ASTM C 1293 Modification).102Cubes in NaOH Solution (Modified ASTM C 1260) .114SUMMARY OF RESULTS .124Rapid Testing Procedures.124ASTM C 1260 (Mortar-Bar Method).124ASTM C 1293 (Modified Prism Beam Test) .124vii
Standard Testing Procedures .125ASTM C 1293 (Standard Prism Beam) .125ASTM C 1293 (Standard Prism Beam) w/ saturation .125Modified Testing Procedures.126ASTM C 1293 (Vacuum-Sealed Cubes).126ASTM C 1293 (Electrical Cylinders) .126ASTM C 1260 (Modified Cubes in NaOH Solution) .1265. CONCLUSIONS .135INTRODUCTION .135NATURAL BLUE ROCK AGGREGATE CONCRETE.135Natural Blue Rock Aggregate Conclusions.136RECYCLED BLUE ROCK AGGREGATE CONCRETE .137Recycled Blue Rock Aggregate Concrete InitialConclusions.138Recycled Blue Rock Aggregate Concrete FinalConclusions.139PROJECT OBJECTIVES .140FUTURE RECOMMENDATIONS.141REFERENCES .143APPENDIX A: Mitigation Material Characteristics. . A-1viii
LIST OF TABLESTABLEPAGETable 1-1RCA and Natural Aggregate Comparisons .7Table 2-1Aggregate Material Characteristics .19Table 2-2Cement Material Characteristics .22Table 2-3Class F Fly Ash and GGBFS Material Characteristics .23Table 2-4PCC Mix Proportions for Original RCA Concrete and ResearchConcrete.24Table 3-1Concrete Mix Design Specifications.51Table 3-2Mix Designs and Testing Properties .52Table 4-1Test Result Summary .127ix
LIST OF FIGURESFIGUREPAGEFigure 1-1Recycled Aggregate Usage.5Figure 1-2Recycled Aggregate Sample from a Concrete Slab.8Figure 1-3Polished Concrete Sample with ASR Gel.10Figure 2-1Expansion versus time for ASTM C 1260 (natural bluerock and RCA) .20Figure 2-2Expansion versus time for ASTM C 1260 (limestone).21Figure 3-1Jaw Crushing Machine.31Figure 3-2Gilson Sieve Machine.32Figure 3-3Hobart Processing Mixer .33Figure 3-4Lancaster Counter Current Batch Mixer.33Figure 3-5Prism Beam Mold .34Figure 3-6Mortar-Bar Mold.35Figure 3-7ASTM C 1260 Mortar-Bar Samples.36Figure 3-8ASTM C 1293 Prism Beam and Storage Container .37Figure 3-9ASTM C 1293 Testing Oven .38Figure 3-10ASTM C 1260 Cube Plan View .40Figure 3-11ASTM C 1260 Cube Section View.40Figure 3-12ASTM C 1260 Prism Beam and Cube Test Specimens.41Figure 3-13Modified ASTM C 1293 Cube Sample .42Figure 3-14Modified ASTM C 1293 Vacuum-Sealed Cube Sample.42Figure 3-15Modified ASTM C 1293 Electrical Cylinder .44Figure 3-16Cube and Prism Beam Measuring Devices.45Figure 3-17Cylinder and Core Calibration Jig .47x
Figure 3-18Cylinder Calibration Jig with Finished Sample.48Figure 3-19Modified ASTM C 1293 Electrical Cylinder with PowerSource .49Figure 3-20Electrical Cylinder Testing Oven .49Figure 4-1Expansion versus time for ASTM C 1260 (limestone).58Figure 4-2Expansion versus time for ASTM C 1260 (natural bluerock and RCA) .59Figure 4-3Expansion versus time for ASTM C 1260 (natural bluerock and class F fly ash) .60Figure 4-4Expansion versus time for ASTM C 1260 (natural bluerock and GGBFS) .61Figure 4-5Expansion versus time for ASTM C 1260 (natural bluerock and lithium nitrate) .62Figure 4-6Expansion versus time for ASTM C 1260 (natural bluerock and silica fume).63Figure 4-7Expansion versus time for ASTM C 1260 (modifiedprism beam test) (limestone).67Figure 4-8Expansion versus time for ASTM C 1260 (modifiedprism beam test) (natural blue rock and RCA with highalkali cement).68Figure 4-9Expansion versus time for ASTM C 1260 (modifiedprism beam test) (natural blue rock and RCA with class Ffly ash) .69Figure 4-10Expansion versus time for ASTM C 1260 (modifiedprism beam test) (natural blue rock and RCA withGGBFS) .70Figure 4-11Expansion versus time for ASTM C 1260 (modifiedprism beam test) (natural blue rock and RCA with lithiumnitrate).71Figure 4-12Expansion versus time for ASTM C 1260 (modifiedprism beam test) (natural blue rock and RCA with silicafume).72xi
Figure 4-13Expansion versus time for ASTM C 1293 (standard prismbeam test) (natural blue rock and RCA with high and lowalkali cement).76Figure 4-14Expansion versus time for ASTM C 1293 (standard prismbeam test) (natural blue rock and RCA with class F flyash).77Figure 4-15Expansion versus time for ASTM C 1293 (standard prismbeam test) (natural blue rock and RCA with GGBFS) .78Figure 4-16Expansion versus time for ASTM C 1293 (standard prismbeam test) (natural blue rock and RCA with lithiumnitrate).79Figure 4-17Expansion versus time for ASTM C 1293 (standard prismbeam test) (natural blue rock and RCA with silica fume) .80Figure 4-18Expansion versus time for ASTM C 1293 (standard prismbeam test) (limestone with high and low alkali cement) .81Figure 4-19Expansion versus time for ASTM C 1293 (standard prismbeam w/ saturation techniques) (RCA with high alkalicement).85Figure 4-20Expansion versus time for ASTM C 1293 (standard prismbeam w/ saturation techniques) (RCA with class F flyash).86Figure 4-21Expansion versus time for ASTM C 1293 (standard prismbeam w/ saturation techniques) (RCA with GGBFS).87Figure 4-22Expansion versus time for ASTM C 1293 (standard prismbeam w/ saturation techniques) (RCA with lithiumnitrate).88Figure 4-23Expansion versus time for ASTM C 1293 (standard prismbeam w/ saturation techniques) (RCA with silica fume).89Figure 4-24Expansion versus time for vacuum-sealed cubes (ASTMC 1293 modification) (natural blue rock and RCA withhigh and low alkali cement).94Figure 4-25Expansion versus time for vacuum-sealed cubes (ASTMC 1293 modification) (natural blue rock and RCA withclass F fly ash) .95xii
Figure 4-26Expansion versus time for vacuum-sealed cubes (ASTMC 1293 modification w/ saturation techniques) (RCAwith class F fly ash) .96Figure 4-27Expansion versus time for vacuum-sealed cubes (ASTMC 1293 modification) (natural blue rock and RCA withGGBFS) .97Figure 4-28Expansion versus time for vacuum-sealed cubes (ASTMC 1293 modification w/ saturation techniques) (RCAwith GGBFS) .98Figure 4-29Expansion versus time for vacuum-sealed cubes (ASTMC 1293 modification) (natural blue rock and RCA withlithium nitrate) .99Figure 4-30Expansion versus time for vacuum-sealed cubes (ASTMC 1293 modification) (natural blue rock and RCA withsilica fume) .100Figure 4-31Expansion versus time for vacuum-sealed cubes (ASTMC 1293 modification w/ saturation techniques) (RCAwith silica fume) .101Figure 4-32Expansion versus time for electrical cylinders (ASTM C1293 modification) (natural blue rock with high and lowalkali cement).104Figure 4-33Expansion versus time for electrical cylinders (ASTM C1293 modification) (RCA with high and low alkalicement).105Figure 4-34Expansion versus time for electrical cylinders (ASTM C1293 modification) (natural blue rock with class F flyash).106Figure 4-35Expansion versus time for electrical cylinders (ASTM C1293 modification) (RCA with class F fly ash).107Figure 4-36Expansion versus time for electrical cylinders (ASTM C1293 modification) (natural blue rock with GGBFS).108Figure 4-37Expansion versus time for electrical cylinders (ASTM C1293 modification) (RCA with GGBFS).109Figure 4-38Expansion versus time for electrical cylinders (ASTM C1293 modification) (natural blue rock with lithiumnitrate).110xiii
Figure 4-39Expansion versus time for electrical cylinders (ASTM C1293 modification) (RCA with lithium nitrate).111Figure 4-40Expansion versus time for electrical cylinders (ASTM C1293 modification) (natural blue rock with silica fume) .112Figure 4-41Expansion versus time for electrical cylinders (ASTM C1293 modification) (RCA with silica fume) .113Figure 4-42Expansion versus time for cubes in NaOH solution(ASTM C 1260 modification) (natural blue rock andRCA with high alkali cement) .117Figure 4-43Expansion versus time for cubes in NaOH solution(ASTM C 1260 modification) (natural blue rock withclass F fly ash) .118Figure 4-44Expansion versus time for cubes in NaOH solution(ASTM C 1260 modification) (RCA with class F fly ash).119Figure 4-45Expansion versus time for cubes in NaOH solution(ASTM C 1260 modification) (natural blue rock withGGBFS) .120Figure 4-46Expansion versus time for cubes in NaOH solution(ASTM C 1260 modification) (RCA with GGBFS).121Figure 4-47Expansion versus time for cubes in NaOH solution(ASTM C 1260 modification) (natural blue rock withlithium nitrate) .122Figure 4-48Expansion versus time for cubes in NaOH solution(ASTM C 1260 modification) (natural blue rock andRCA with silica fume) .123Figure 4-49Modified ASTM C 1260 28-Day Prism versus ASTM C1260 14-Day Mortar Bar Results.131Figure 4-50Modified ASTM C 1260 56-Day Prism versus ASTM C1260 28-Day Mortar Bar Results.132Figure 4-51ASTM C 1293 365-Day Prism versus Modified ASTM C1260 28-Day Prism Results .133Figure 4-52ASTM C 1293 720-Day Prism versus Modified ASTM C1260 56-Day Prism Results .134xiv
ABSTRACTMITIGATING ALKALI SILICATE REACTION IN RECYCLED CONCRETEByHugh C. Scott IVUniversity of New Hampshire, May, 2006The objective of this study was to investigate the reactivity of concrete containingrecycled concrete aggregates (RCA) that had shown distress due to alkali silicate reaction(ASR) prior to being recycled. This study evaluated several mitigation techniques tocontrol ASR in concrete containing RCA. RCA was studied to investigate expansioncharacteristics during early age hydration. The development of mitigation guidelines andinformation on the behavior of concrete containing RCA are important issues as naturalaggregate supplies dwindle and alternative aggregate sources become necessary.Mitigation work was done with three different aggregate types; an igneous finegrained quartzite blue rock, as presently quarried, RCA blue rock, and limestone. Thenatural blue rock aggregate concrete was used as a control.Concrete’s containinglimestone was used to investigate the reactive characteristics of the fine aggregate and thebehavioral differences of the cements used. The mitigation strategies include the use oflow alkali cement, class F fly ash, ground granulated blast furnace slag (GGBFS), lithiumnitrate, and silica fume blended cement. These materials were incorporated into concretemixtures by cement substitution and direct application.xv
Concrete mortar-bars, prism beams, cubes and cylinders were used to investigatethe mitigation strategies. ASTM C 1260, ASTM C 1293, and modified versions of thesetests were used to evaluate expansion caused by ASR.Low alkali cement, class F fly ash, ground granulated blast furnace slag, andlithium nitrate showed potential in controlling ASR distress in natural aggregate concreteand RCA concrete. In general, RCA concretes showed larger expansion rates thannatural aggregate concretes. RCA is a viable aggregate source in new portland cementconcrete mixtures when ASR mitigation strategies are properly applied.xvi
CHAPTER 1INTRODUCTIONINTRODUCTIONAlkali silicate reaction (ASR) distress in concrete structures has been observed inthe United States since before 1940.1 Thomas E. Stanton reported concrete pavementfailure in early 1938 on a section of concrete pavement north of Bradley in the SalinasValley, Monterey County, California.Failure was attributed to coarse and fineaggregates used in the portland cement concrete (PCC). The concrete distress led toexcessive cracking throughout the length of concrete slabs and buckling at expansionjoints. This diagnosis of ASR has prompted numerous reports of concrete deteriorationthat show ASR to be at least one of the leading causes of distress in structures located inhumid environments.2Much of the concrete infrastructure in the United States is inadequate and in needof rehabilitation or even reconstruction. The construction of the interstate highwaysystem in the United States began in the 1950's and as many roadways are constructedwith 50 year life expectancies the roadways are starting to become obsolete and in needof major rehabilitation or replacement. It will cost trillions of dollars to complete thisrebuilding process. Problems with ASR distress and concrete durability, seen throughoutthe country, are direct results of reactive aggregates being used in concrete structures.Although non-reactive aggregates do exist in this country, they are often located in1
remote locations and are very expensive to transport in large quantities.A viablealternative to this aggregate problem is recycling waste concrete. This not only reducesconstruction and demolition waste, but it also gives a potential aggregate source for newconcrete.Recycling waste concrete has been done in European countries since the end ofworld war two. Recycling concrete waste is a large part of the aggregate industry inpresent-day practice. Little is known about recycling concrete that has undergone ASRdistress. Although the use of RCA in new concretes has not been popular, there is a needto understand the behavior of ASR distressed RCA in new concrete environments. Forexample, the recycling of construction and demolition waste as aggregates is wellunderway in Belgium with RCA representing 10% of the national market of aggregates.3With a decreasing supply of natural aggregates, the aggregate industry will be forced tofind other materials to satisfy the ongoing demand for construction materials.Although recycled aggregate concrete has not gained popularity in present dayconstruction, many concrete roadway projects have been done using recyclingtechniques. Iowa rebuilt U.S. Route 75 in 1976 with recycled coarse and fine aggregatesin new concrete mixtures. The project was successful using the old roadway for coarseaggregate and a mixture of recycled fine material with 15% concrete sand to give theconcrete a higher workability. With this successful project, the state of Iowa undertooktwo more roadway projects incorporating recycled aggregates. More recent projects weredone in Minnesota when a recycling project was conducted on U.S. 59 in the southeasternpart of the state in 1980. This project incorporated recycled material that had undergoneD-cracking as a major distress. The new pavement showed promising results with a2
durable product.4 Other states have used RCA in new concrete, such as MN, WY, MI, ID,TE, in the past, but only as unbound base material.4Information on projects incorporating recycled aggregate that has undergone ASRis very limited. Limited research has been done with RCA having undergone ASR, but itis recommended that recycled aggregate be tested for ASR prior to its use. It is importantto know if the ASR of the RCA has the potential to continue or reactivate if the distressedconcrete is recycled. Past recommendations included the use of the ASTM C 227 testwith various alkali contents to determine what level of alkali is acceptable for therecycled material to start showing ASR expansive behavior in new concretes.4 Newtesting procedures are presently being used to evaluate the potential for ASR distress withaggregate sources and concrete specimens.Recent publications show that proper mitigation procedures can control oreliminate destructive ASR in PCC.5 Accepted mitigation materials include low alkalicement, class F fly ash, ground granulated blast furnace slag (GGBFS), metakaolin,lithium nitrate, and silica fume. Mitigation materials are commonly used in naturalaggregate concretes as a means to make a high quality product material and to use thesematerials, especially class F fly ash, that would otherwise be land filled, and GGBFS in aproductive way.PROJECT OBJECTIVESThe main goal of this research project was to investigate the ability of presentlyaccepted ASR mitigation techniques to control ASR in concrete made with ASRdistressed RCA. Existing ASR potential testing methods were used to evaluate theirapplicability with concretes containing RCA.3The result of this project was the
development of ASR mitigation strategies to control ASR distress with concretecontaining ASR distressed RCA. This information is useful as natural aggregate suppliesare decreasing and new material resources are necessary for the future production ofPCC.RECYCLED CONCRETE AGGREGATE (RCA)Recycling waste concrete became a reality in Europe after the end of world wartwo.6 Cities faced the challenge to rebuild infrastructure and deal with large amounts ofdemolition debris. RCA has gained popularity as roadbase material, erosion control(riprap) material, and general fill throughout the United States and Internationally. Manystate department of transportation agencies (DOT's) have adopted the use of RCA as anacceptable natural aggregate substitution in new concrete and in asphalt concretepavements.6 RCA use breakdown shows 68% used as roadbase material,
beam test) (natural blue rock and RCA with silica fume) .80 Figure 4-18 Expansion versus time for ASTM C 1293 (standard prism beam test) (limestone with high and low alkali cement).81 Figure 4-19 Expansion versus time for ASTM C 1293 (standard prism beam w/ saturation techniques) (RCA with high alkali