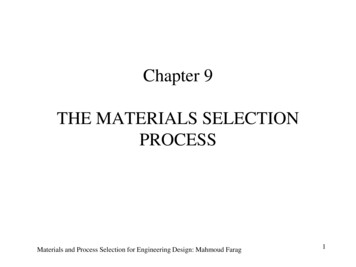
Transcription
Chapter 99.19.29.39.4Bearings and Expansion JointsContentsExpansion Joints . . . . . . . . . . . . . . . . . . . . . . . . . . . . . . . . . . . . . . . . . . . . . . . . . . . . 9-19.1.1General Considerations . . . . . . . . . . . . . . . . . . . . . . . . . . . . . . . . . . . . . . . . . . . . . . . . 9-19.1.2General Design Criteria . . . . . . . . . . . . . . . . . . . . . . . . . . . . . . . . . . . . . . . . . . . . . . . . 9-39.1.3Small Movement Range Joints . . . . . . . . . . . . . . . . . . . . . . . . . . . . . . . . . . . . . . . . . . . 9-69.1.4Medium Movement Range Joints . . . . . . . . . . . . . . . . . . . . . . . . . . . . . . . . . . . . . . . 9-159.1.5Large Movement Range Joints . . . . . . . . . . . . . . . . . . . . . . . . . . . . . . . . . . . . . . . . . . 9-19Bearings . . . . . . . . . . . . . . . . . . . . . . . . . . . . . . . . . . . . . . . . . . . . . . . . . . . . . . . . . . 9-279.2.1General Considerations . . . . . . . . . . . . . . . . . . . . . . . . . . . . . . . . . . . . . . . . . . . . . . . 9-279.2.2Force Considerations . . . . . . . . . . . . . . . . . . . . . . . . . . . . . . . . . . . . . . . . . . . . . . . . . 9-289.2.3Movement Considerations . . . . . . . . . . . . . . . . . . . . . . . . . . . . . . . . . . . . . . . . . . . . 9-289.2.4Detailing Considerations . . . . . . . . . . . . . . . . . . . . . . . . . . . . . . . . . . . . . . . . . . . . . . 9-299.2.5Bearing Types . . . . . . . . . . . . . . . . . . . . . . . . . . . . . . . . . . . . . . . . . . . . . . . . . . . . . . 9-299.2.6Miscellaneous Details . . . . . . . . . . . . . . . . . . . . . . . . . . . . . . . . . . . . . . . . . . . . . . . . 9-379.2.7Contract Drawing Representation . . . . . . . . . . . . . . . . . . . . . . . . . . . . . . . . . . . . . . . 9-379.2.8Shop Drawing Review . . . . . . . . . . . . . . . . . . . . . . . . . . . . . . . . . . . . . . . . . . . . . . . . 9-389.2.9Bearing Replacement Considerations . . . . . . . . . . . . . . . . . . . . . . . . . . . . . . . . . . . . 9-38Seismic Isolation Bearings . . . . . . . . . . . . . . . . . . . . . . . . . . . . . . . . . . . . . . . . . . . 9-399.3.1General Considerations . . . . . . . . . . . . . . . . . . . . . . . . . . . . . . . . . . . . . . . . . . . . . . . 9-399.3.2Suitability and Selection Considerations . . . . . . . . . . . . . . . . . . . . . . . . . . . . . . . . . . 9-399.3.3General Design Criteria . . . . . . . . . . . . . . . . . . . . . . . . . . . . . . . . . . . . . . . . . . . . . . . 9-409.3.4Seismic Isolation Bearing Submittal Requirements . . . . . . . . . . . . . . . . . . . . . . . . . . 9-419.3.5Seismic Isolation Bearing Review Process . . . . . . . . . . . . . . . . . . . . . . . . . . . . . . . . . 9-429.3.6Seismic Isolation Bearing Inspection . . . . . . . . . . . . . . . . . . . . . . . . . . . . . . . . . . . . . 9-43Bridge Standard Drawings . . . . . . . . . . . . . . . . . . . . . . . . . . . . . . . . . . . . . . . . . . . . 9-449.4.1Expansion Joints . . . . . . . . . . . . . . . . . . . . . . . . . . . . . . . . . . . . . . . . . . . . . . . . . . . . 9-44WSDOT Bridge Design Manual M 23-50.20September 2020Page 9-i
Chapter 9Page 9-iiBearings and Expansion JointsWSDOT Bridge Design Manual M 23-50.20September 2020
Chapter 9Bearings and Expansion Joints9.1Expansion Joints9.1.1General ConsiderationsAll bridges must accommodate, in some manner, environmentally and self-imposedphenomena that tend to make structures move in various ways. These movementscome from several primary sources: thermal variations, concrete shrinkage, creepeffects from prestressing, and elastic post-tensioning shortening. With the exceptionof elastic post-tensioning shortening, which generally occurs before expansion devicesare installed, movements from these primary phenomena are explicitly calculated forexpansion joint selection and design. Other movement inducing phenomena include liveloading (vertical and horizontal braking), wind, seismic events, and foundation settlement.Movements associated with these phenomena are generally either not calculated or notincluded in total movement calculations for purposes of determining expansion jointmovement capacity.With respect to seismic movements, it is assumed that some expansion joint damagemay occur, that this damage is tolerable, and that it will be subsequently repaired. Incases where seismic isolation bearings are used, the expansion joints must accommodateseismic movements in order to allow the isolation bearings to function properly.Expansion joints must accommodate cyclic and long-term structure movements in sucha way as to minimize imposition of secondary stresses in the structure. Expansion jointdevices must prevent water, salt, and debris infiltration to substructure elements below.Additionally, an expansion joint device must provide a relatively smooth riding surfaceover a long service life.Expansion joint devices are highly susceptible to vehicular impact that results as aconsequence of their inherent discontinuity. Additionally, expansion joints have oftenbeen relegated a lower level of importance by both designers and contractors. Many ofthe maintenance problems associated with in-service bridges relate to expansion joints.One solution to potential maintenance problems associated with expansion joints is touse construction procedures that eliminate the joints from the bridge deck. The two mostcommonly used methods are called integral and semi-integral construction. These twoterms are sometimes collectively referred to as jointless bridge construction.In integral construction, concrete end diaphragms are cast monolithically with both thebridge deck and supporting pile substructure. In order to minimize secondary stressesinduced in the superstructure, steel piles are generally used in their weak axis orientationrelative to the direction of bridge movement. In semi-integral construction, concreteend diaphragms are cast monolithically with the bridge deck. Supporting girders rest onelastomeric bearings within an L-type abutment. Longer semi-integral bridges generallyhave reinforced concrete approach slabs at their ends. Approach slab anchors, inconjunction with a compression seal device, connect the monolithic end diaphragm tothe approach slab. Longitudinal movements are accommodated by diaphragm movementWSDOT Bridge Design Manual M 23-50.20September 2020Page 9-1
Chapter 9Bearings and Expansion Jointsrelative to the approach slab, but at the same time resisted by soil passive pressureagainst the end diaphragm.Obviously, bridges cannot be built incrementally longer without eventually requiringexpansion joint devices. The incidence of approach pavement distress problems increasesmarkedly with increased movement that must be accommodated by the end diaphragmpressing against the backfill. Approach pavement distress includes pavement and backfillsettlement and broken approach slab anchors.Washington State Department of Transportation (WSDOT) has implemented jointlessbridge design by using semi-integral construction. Office policy for concrete and steelbridge design is as follows:A. Concrete BridgesSemi-integral design is used for prestressed concrete girder bridges under 450feet long and for post-tensioned spliced concrete girder and cast-in-place posttensioned concrete box girder bridges under 400 feet long. Use L-type abutmentswith expansion joints at the bridge ends where bridge length exceeds these values.In situations where bridge skew angles exceed 30 degrees, consult the Bearing andExpansion Joint Specialist and the State Bridge Design Engineer for recommendationsand approval.B.Steel BridgesUse L-type abutments with expansion joints at the ends for multiple-span bridges.Semi-integral construction may be used in lieu of expansion joints for single spanbridges under 300 feet with the approval of the State Bridge Design Engineer.In situations where the bridge skew exceeds 30 degrees, consult the Bearing andExpansion Joint Specialist and the State Bridge Design Engineer for recommendationsand approval.In all instances, the use of intermediate expansion joints should be avoided whereverpossible. The following table provides guidance regarding maximum bridge superstructurelength beyond which the use of either intermediate expansion joints or modularexpansion joints at the ends is required.Page 9-2WSDOT Bridge Design Manual M 23-50.20September 2020
Bearings and Expansion JointsSuperstructure TypeChapter 9Maximum Length (Western WA)Maximum Length (Eastern oncrete SuperstructurePrestressed Girder*450 ft900 ft450 ft900 ftP.T. Spliced Girder**400 ft700 ft***400 ft700 ft***C.I.P.–P.T. box girder400 ft700 ft ***400 ft700 ft***300 ft700 ftSteel SuperstructurePlate Girder Box girder300 ft900 ft*Based upon 0.16 in. creep shortening per 100 feet of superstructure length and 0.12 inch shrinkageshortening per 100 feet of superstructure length** Based upon 0.31 in. creep shortening per 100 feet of superstructure length and 0.19 inch shrinkageshortening per 100 feet of superstructure length*** Can be increased to 800 ft. if the joint opening at 64º F at time of construction is specified in theexpansion joint table to be less than the minimum installation width of 1½ inches. This condition isacceptable if the gland is already installed when steel shapes are placed in the blockout. Otherwise(for example, staged construction) the gland would need to be installed at temperature less than45º F.Because the movement restriction imposed by a bearing must be compatible with themovements allowed by the adjacent expansion joint, expansion joints and bearingsmust be designed interdependently and in conjunction with the anticipated behaviorof the overall structure.A plethora of manufactured devices exists to accommodate a wide range ofexpansion joint total movements. Expansion joints can be broadly classified into threecategories based upon their total movement range as follows:Small Movement JointsMedium Movement JointsLarge Movement Joints9.1.2Total Movement Range 1¾ in.1¾ in. Total Movement Range 5 in.Total Movement Range 5 in.General Design CriteriaExpansion joints must be sized to accommodate the movements of several primaryphenomena imposed upon the bridge following installation of its expansion joint devices.Concrete shrinkage, thermal variation, and long-term creep are the three most commonprimary sources of movement. Calculation of the movements associated with each ofthese phenomena must include the effects of superstructure type, tributary length, fixitycondition between superstructure and substructure, and pier flexibilities.A. Shrinkage EffectsAccurate calculation of shrinkage as a function of time requires that average ambienthumidity, volume-to-surface ratios, and curing methods be taken in consideration assummarized in AASHTO LRFD BDS Article 5.4.2.3.3. Because expansion joint devicesare generally installed in their respective blockouts at least 30 to 60 days followingconcrete deck placement, they must accommodate only the shrinkage that occursfrom that time onward. For most situations, that shrinkage strain can be assumed tobe 0.0002 for normal weight concrete in an unrestrained condition. This value mustbe corrected for restraint conditions imposed by various superstructure types.WSDOT Bridge Design Manual M 23-50.20September 2020Page 9-3
Chapter 9Bearings and Expansion JointsΔLshrink β · μ · Ltrib(9.1.2-1)Where:Ltrib Tributary length of the structure subject to shrinkageβ Ultimate shrinkage strain after expansion joint installation; estimated as 0.0002 inlieu of more refined calculationsμ Restraint factor accounting for the restraining effect imposed by superstructureelements installed before the concrete slab is cast 0.0 for steel girders, 0.5 for precast prestressed concrete girders, 0.8 for concretebox girders and T-beams, 1.0 for concrete flat slabsB.Thermal EffectsBridges are subject to all modes of heat transfer: radiation, convection, andconduction. Each mode affects the thermal gradients induced and deflectionpatterns generated in a bridge superstructure differently. Climatic influences varygeographically resulting in different seasonal and diurnal average temperaturevariations. Additionally, different types of construction have different thermal“inertia” properties. For example, a massive concrete box girder bridge will be muchslower to respond to an imposed thermal stimulus than would a steel plate girderbridge composed of many relatively thin steel elements.Variation in the superstructure average temperature produces uniform elongation orshortening. Uniform thermal movement range is calculated using the maximum andminimum anticipated bridge superstructure average temperatures in accordance withAASHTO LRFD BDS Article 3.12.2.1 Procedure A. For t
minimum design temperatures, T. U. and T. L, respectively, used for uniform thermal movement effects, taken from AASHTO LRFD BDS Table 3.12.2.1-1 are: Moderate Climate: Concrete Bridges: 10 F to 80 F Steel Bridges: 0 F to 120 F Cold Climate: Concrete Bridges: 0 F to 80 F Steel Bridges: -30 F to 120 F