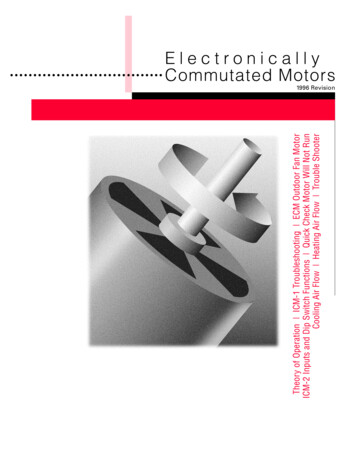
Transcription
Theory of Operation ICM-1 Troubleshooting ECM Outdoor Fan MotorICM-2 Inputs and Dip Switch Functions Quick Check Motor Will Not RunCooling Air Flow Heating Air Flow Trouble Shooter ElectronicallyCommutated Motors1996 RevisionHistory 1977–1991
ContentsTheory of Operation . 1ICM-1 Troubleshooting . 6ECM Outdoor Fan Motor . 7ICM-2 Inputs and Dip Switch Functions . 17Quick Check Motor Will Not Run . 27ICM-2 Will Not Run .Cooling Air Flow .Heating Air Flow .Trouble Shooter .33374553Theory of OperationWHAT IS ECM?Motor An Electronically Commutated Motor Three Phase Wound Stator Permanent Magnet RotorPERMANENT MAGNETAC MOTOR THEORY Rotating Magnetic Fields Squirrel Cage Rotor9623 11/21/96ECM Manual 1 EfficiencySQUIRREL CAGE1
Theory of OperationMOTOR SPEED 2 Pole MotorPOLE DISTANCE 180 4 Pole MotorPOLE DISTANCE 90 1 CYCLE 360 DISTANCE1 CYCLE 180 DISTANCE Frequency is measured in cycles per second R.P.M. is measured in revolutions per minute Synchronous Motor R.P.M. AC Frequency in Hertz x 120Number of Poles in Motor Motor Impedance Synchronous Torque Slip Maximum Current Motor Speed Varied by Changing Power and FrequencyMOTOR CONTROL Motor Speed Is Controlled By The Drive Output Frequency Motor Torque Is Controlled For Specific Requirement By Varying Output Current Rotor Position and RPM Sensed By Motor Back EMF29623 11/21/96 Motor Is Protected Under Abnormal Load ConditionsECM Manual 2 Performance and Efficiency Are Optimitized By Motor Drive
Theory of OperationVARIABLE SPEEDELECTRIC SYSTEM BLOCK DIAGRAMThe motor drive uses the latest technology inhigh current high voltage power switchingelectronics. The block diagrams show the powerfactor correction inductor, high frequency E.M.I.filter, full wave bridge rectifier, D.C. capacitor,microprocessor control circuit and the solid statepower switches for phase A, B and C.The power switches are drawn as mechanicalswitches for ease of explanation only. To showcurrent flow through motor, start at the powerswitch A and close its switch to the negativeterminal and close power Switch B to the positiveterminal and current can flow through two legs ofthe motor windings. Continue to open and closepower switches between their positive andnegative terminals to show how the motor statoris electrically commutated.In actuality, there are periods of times in a threephase cycle that the current will also be enteringtwo legs at the same time and leave through thethird leg.The time at which the switches are closed andopened to each entering leg is not the same.Remember, that current flows from negative topositive and current cannot flow in both directionsthrough any leg of the motor winding at the sametime. Three-phase current flow through the motorcan be simply explained this way.When in operation, the power electronic switcheswill be operated at different speeds to generate thefrequency (in Hertz) to cause the motor to run atdifferent speeds.9623 11/21/96ECM Manual 3ICM-2 VARIABLE SPEEDELECTRICAL SYSTEM BLOCK DIAGRAM3
49623 11/21/96ECM Manual 4Theory of Operation
9623 11/21/96ECM Manual 5ICM-1 MotorICM-15
ICM-1 Troubleshooting1. Is there 24 V.A.C. betweenterminals “R” and “B” at airhandlers, or furnace?YES: #2.W1Y1NO: Check 24 V.A.C. fuse and power to air handler.Repair as required.W2Y2Possible component faults which could causefuse to blow.Field wiring.Indoor fan relay.Thermostat.Switchover valve coil.O.D.S in the outdoor unit.W3BKBVOLTS A/COTRG2. ICM 1 to check for motor operationuse jumper as follows.Step 1 Unhook field wiring from terminal board.Step 2 Jumper “R” to “G” and “BK”. Blower shouldrun at cooling high speed. black wire tap.Step 3 Jumper “R” to “G”. Blower should run atlow speed, white wire tap.Step 4 Jumper “R” to “G” and “W1”. Blowershould run at red wire heat speed tap.ICM 1Will motor run and change speed?YES: Motor runs and changes speed, fault is in thefield wiring or thermostat.NO: If motor will not run, check all motor to terminalboard wiring. If wiring is OK, perform check No. 3.3. Check for power to the motordrive assembly, and can blower befreely spun. 115 V.A.C. for furnaces.230 V.A.C. for air handlers.MOTOR LEADSYES: If the voltage is correct and the blower willspin freely, replace motor and drive assembly.6ECM Manual 6MOTOR9623 11/21/96VOLTS A/CNO: Restore power or free-up motor and check forproper operation.
ECM Outdoor Fan MotorTROUBLESHOOTING1. Fan motor will not run.Use Chart # 1.2. Fan will not change speeds or is running at the wrong speed.Use Chart # 2.9623 11/21/96ECM Manual 73. Fan motor is changing speeds up and down and the fanthermostat is not switching back and forth.Go to Chart # 1, Step # 5.7
ECM Outdoor Fan MotorCHART #1ECM Outdoor Fan Motor Will Not Run89623 11/21/962. Caution – line voltage isnot switched by the contactor. Checkline voltage to motorbrown and black wires.Is the correct line voltage present?NO: Repair as needed.YES: Go to Step #3.ECM Manual 81. Is the motor shaft free?NO: Free up motor or replace.YES: Go to Step #2.
ECM Outdoor Fan Motor9623 11/21/96ECM Manual 93. Is there 24 V.A.C. present between pinsY and B on the fan control board?NO: Is the compressor contactor picked up?If not, repair as needed.YES: Go to Step #4.4. Is the red L.E.D. on the fan controlboard on?NO: Outdoor fan thermostat is inthe hot position or the L.E.D. circuit on thefan control board has failed. D.C. voltage inSteps #5 and #6 shouldbe 16 – 24 V. D.C.Go to step #5.YES: Outdoor fan thermostat isin the cold position.D.C. voltage in Steps #5 and #6should be 8 – 12 V. D.C.Go to Step #5.9
ECM Outdoor Fan Motor5. Is the correct D.C. voltage presentbetween terminals A and C on the fancontrol board?NO: Replace fan control board.YES: Go to Step #6.VOLTS D.C.6. Is the correct D.C. voltagepresent between the blue andyellow motor leads?NO: Repair motor plug orwires going to the fan controlboard terminals A and C.YES: Replace motor.109623 11/21/96ECM Manual 10VOLTS D.C.
ECM Outdoor Fan MotorCHART #2ECM Outdoor Fan Motor Will Not Change Speeds9623 11/21/96ECM Manual 111. Outdoor fan motor must be runningfor the test. Is the red L.E.D. on the fancontrol board on?NO: Outdoor fan thermostat is in thehot position, or has failed, or the L.E.D.circuit on the fan control board hasfailed. Go to Step #4.YES: Outdoor fan thermostat is inthe cold position switch closed.Go to Step #2.2. Take one of the wires off theoutdoor fan thermostat. The redL.E.D. on the fan control board willgo out. Does the outdoor fan motorgo to high speed?NO: If the red L.E.D. is still on, fault isin the unit’s wiring going to the fancontrol board. If the red L.E.D. is out,Go to Step #3.YES: Check the outdoor fanthermostat for proper operation.11
ECM Outdoor Fan Motor129623 11/21/96ECM Manual 123. Read the D.C. voltage between terminalsA and C on the fan control board.Plug the wire removed from thethermostat in Step #2 back on theoutdoor fan thermostat.The red L.E.D. must come on again,if not jumper both wires together on theoutdoor fan thermostat. Again, readthe D.C. voltage between terminalsA and C on the motor control board.Did the D.C. voltage drop to about half?NO: Replace motor control board.YES: Replace the outdoor fan motor.
ECM Outdoor Fan Motor4. Jumper the two wires together on theoutdoor fan thermostat. Does the red L.E.D.on the fan control board come on?NO: Check for 24 V. A.C. between terminalsT2 and B on the fan control board.If 24V. A.C. is present and the L.E.D.is out, replace the fan control board.If 24V. A.C. is not present at terminalsT2 and B, fault is in the unit’s wiring.YES: If the outdoor fan motor changesspeed, check the outdoor fan thermostatfor proper operation. If the outdoor fanmotor does not change speed,go to Step #5.9623 11/21/96ECM Manual 13VOLTS A.C.13
ECM Outdoor Fan Motor149623 11/21/96ECM Manual 145. Read the D.C. voltage betweenterminals A and C on the fan control board,record this voltage. Remove the jumperinstalled in Step #4 on the outdoor fanthermostat. Again read the D.C. voltagebetween terminals A and C on the fancontrol board. Is the D.C. voltage nowabout double the recorded voltage?NO: Replace fan control board.YES: Replace fan motor.
ECM Outdoor Fan Motor9623 11/21/96ECM Manual 15OUTDOOR ECM FAN MOTOR CONTROL BOARD15
169623 11/21/96ECM Manual 16ECM Outdoor Fan Motor
9623 11/21/96ECM Manual 17ICM-2 Inputs and Dip Switch FunctionsICM-217
ICM-2 Inputs and Dip Switch FunctionsMOTOR CONTROL BOARDS12 3 45 6 7 8ONOFFFANCFMR BK ORETRO FIT KIT – CNT 1654YYLO G W1 W2 BFURNACE – CNT 1537PACKAGE UNITBRD 0986AIR HANDLERTRBKOYY LOGW1W2 W3BTRBKR18OYY LOGW1W2 W3BJBBCNT 1538FANCFMOFFBKJUMPERCNT 1866RECM Manual 18ON 1 2 3 4 5 6 7 8FANCFM9623 11/21/96ON 1 2 3 4 5 6 7 8OFF
ICM-2 Inputs and Dip Switch FunctionsThe ICM-2 motor is a Field Programmable Motor.The field programming is done with eight DipSwitches on the motor control board. The motor’scomputer has eleven inputs and one output. Theeight Dip Switched and four of the computerinputs are used to program the cooling airflow,heating airflow and a time delay or ramp cycle.The other seven inputs are used to turn the motoron or off, and command to run at a programmedCFM for heating or cooling. The one output fromthe computer is used to turn the green CFM L.E.D.on and off on the motor control board. Bycounting the number of flashes the CFM programcan be checked. Four different input commandscan be sent to the motor computer with 24 V.A.C.by using the Dip switches on the motor controlboard. 24 volts A.C. is supplied to the motorcomputer for power and it is also used as a timingreference.3. OUT OF TIME COMMANDICM-2 MOTORMOTOR CONTROL BOARD1D12D2R24 VACBTIME REFERENCEPOWERDip Switch #1 closed will cause a out of timecommand to be received by the motor computer,it will then run at it’s factory program for a out oftime command.4. NO COMMANDICM-2 MOTORMOTOR CONTROL BOARD1. IN TIME COMMANDICM-2 MOTORMOTOR CONTROL BOARD1D12D2R24 VACB1D12D2R24 VACTIME REFERENCEPOWERBTIME REFERENCEPOWERDip Switch #2 will cause an in time command tobe received by the motor computer. The motorwill now run at it’s factory program for an intime command.When Dip Switch #1 and #2 are open nocommand will be received on this input by themotor computer, it will then run at it’s factoryprogram for a no command input.2. DOUBLE COMMANDICM-2 MOTORMOTOR CONTROL BOARD1D12D2R24 VAC9623 11/21/96ECM Manual 19BTIME REFERENCEPOWERDip Switches #1 and #2 closed will cause a doubletime command to be received by the motorcomputer, it will then run at it’s factory programfor a double time command.19
ICM-2 Inputs and Dip Switch FunctionsICM-2 CONTROL IMPUTAir Flow PriorityThe ICM-2 motor will run at the called for CFM. If two or more calls are being received atthe same time, G, Y and W1, for example a heat pump or cooling unit, air handler orpackage, the ICM-2 motor will run at the highest speed call it is receiving, Y or W1.A furnace or package gas electric W1, and W2 have priority over Y.BK#10W1#2W2#13G#15YLO#6G1#6Y#14CFM#16BO#1, 3, & 8#9R#12FUNCTIONHumidistat input for single, or two speed systems. Twospeed system may be a two speed compressor or a twocompressor system. If a humidistat is not installed, ajumper must be installed between “R” and “BK”. A XV1500 variable speed system BK is the input for the PWMblower speed command not humidistat.CFM, blower speed, for low heat. Packaged Gas/ElectricW1 and W2 are also used for a on or off command forthe motor.CFM, blower speed for high heat. W2 on gas furnaces orW3 on air handlers. Packaged Gas/Electric only bloweron/off common is also W2.On or off command for the motor. Air flow will be 50%of cooling Y CFM programmed.CFM, blower speed, for low speed cooling on a twospeed system.Package unit air flow will be 100 % cooling Y CFMprogrammed.CFM, blower speed, for high speed cooling on a twospeed system, or cooling CFM for a single speed system.LED, will flash the number of times programmed by theDip switches in the cooling or heating cycle. Cooling CFMis programmed by Dip switches # 1 and # 2 tonnagetimes dip switch # 3 and # 4 CFM per ton. Heating CFM isprogrammed by Dip switches # 7 and # 8.Common 24 VAC.Cooling cycle humidistat enable. Single or two speedsystem only. On a cooling system, “Y” must be jumperedto “O” for humidistat operation.Power and timing reference for ICM-2 motor computerand power to the Dip switches.ECM Manual 20PIN NO.9623 11/21/9620TERMINAL
ICM-2 Inputs and Dip Switch FunctionsICM-2 CONTROL IMPUTDip SwitchesSWITCHPIN NO.FUNCTION#1 & # 2#5Tonnage of outdoor unit.#3#7CFM per ton. 350, 400 or 450 CFM.#5#4Are used to set up indoor blower time delay at theend of a cooling cycle. If a delay or ramped on cycleis programmed, a heat pump or cooling only installation,the heating cycle blower off cycle will also be affected.The cooling air flow, CFM, will be reduced by 50%. A gasfurnace or Package gas electric installation, the ignitioncontrol will control the amount of time the blower is on atthe end of the heating cycle. See ICM-2 Motor OperationChart for type equipment installed. On a variable speedsystem # 5 & # 6 must be in their off position.#11CFM for low heat and high heat, 2 stage gas furnace orthree stage electric heat.9623 11/21/96ECM Manual 21#7̵
AIR HANDLER ICM-2MOTOR OPERATIONRAMPED OPERATION – Dip Switch No. 5 and No.6 ON, works in both the cooling and heating cycle.A call on “Y” and “G” is all that is needed to get aramped ON and OFF cycle in either the heating orcooling cycle.COOLING HUMIDISTAT OPERATION – Will beenabled when a call on “O” is received by themotor computer. Cooling only units - a jumpermust be installed between “Y” an “O” at theMotor Control Board (ICMC) plug. “BK” terminal isjumpered to “R” terminal on the Motor ControlBoard and this jumper must be cut to connect acooling humidistat.AIR FLOW PRIORITY is the highest speed call it isreceiving, “Y” or “W”. If “Y” and “W” are bothturned ON at the same time (heat pumpoperation), the air flow will be the highest of thetwo and the “W” will cause the ramped ON cycleto be canceled.BLOWER TIME DELAY to OFF is controlled by theICM-2 motor and Dip Switch No. 5 and No. 6 on the(ICMC) Motor Control Board. If a delay isprogrammed, 90 or 180 seconds, it will work inboth the heating and cooling cycles if the ICM-2motor sees a call on “Y” and “G”. When the ICM2 motor sees a call on “W” and “G”, the time delayto OFF is canceled.FAN CONTINUOUS OPERATION – The airflow is50% of the cooling air flow. If cooling air flow isrequired for continuous fan operation, jumper G1pin to G pin at the (ICMC) motor control boardplug. A factory installed jumper pigtail, (BK), isconnected to G1 pin for this purpose.AIR HANDLERS BUILT BEFORE JUNE, 1994 – ”O”is the ramp, on time delay and humidistat enableinput.AIR HANDLERS BUILT AFTER MAY, 1994 – ”O" isneeded only for the cooling humidistat enableinput.RAMPED OPERATION – Dip Switch No. 5 and No.6 ON, works in both the cooling and heating cycle.A call on “0”, “Y” and “G” on air handlers builtbefore 6/94 or a call on “Y” and “G” on airhandlers built after 5194, is all that is needed to geta ramped ON and OFF cycle in either the heatingor cooling cycle. If a cooling humidistat is notinstalled on air handlers built before June, 1994, ajumper must be installed between “R” and “BK”terminals.COOLING HUMIDISTAT OPERATION – Will beenabled when a call on “O” is received by themotor computer. Cooling only units – a jumpermust be installed between terminals “Y” and “O”at the Motor Control Board. When the humidity ishigh, the humidistat’s switch will be open and theblower air flow will be reduced 20%.AIR FLOW PRIORITY is the highest speed call it isreceiving, “Y” or “W”. If “Y” and “W” are bothturned ON at the same time (heat pumpoperation), the air flow will be the highest of thetwo and the “W” will cause the ramped ON cycleto be cancelled. “W1” and “W3” are the heatingair flow input terminals.BLOWER TIME DELAY to OFF is controlled by theICM-2 motor and Dip Switch NO. 5 and No. 6 onthe Motor Control Board. If a delay isprogrammed, 90 or 180 seconds, it will work inboth the heating and cooling cycles if the ICM-2motor sees a call on “Y” and “G”. When the ICM2 motor sees a calls on “W” and “G”, the timedelay to OFF is cancelled.FAN CONTINUOUS OPERATION – The airflow is50% of the cooling airflow. If cooling air flow isrequired for continuous fan operation, removefield installed wires from “Y” terminal on the lowvoltage terminal board and wire nut themtogether. Then connect “G” terminal to “Y”terminal with a jumper.100% IF NECESSARY80%DEHUMIDIFYWARM AIR HEATING50%OFF50%FAST COIL COOLINGFAST COIL 3 11/21/96HEAT PUMP & COOLINGPACKAGE UNITICM-2 MOTOR OPERATIONECM Manual 22ICM-2 Inputs and Dip Switch Functions
ICM-2 Inputs and Dip Switch FunctionsPACKAGE GAS ELECTRICICM-2 MOTOR OPERATIONFURNACE ICM-2MOTOR OPERATIONBLOWER ON/OFF OPERATION, is “G”, “W1” or“W2”.A Call on “Y” and “G” together. The indoorblower will run at 100%. “O” is the ramp, or timedelay and humidistat enable input. This “O” inputmust be received by the ICM-2 Motor Computerfor these cycles to operate. Cooling only unitsjumper “Y” to “O” at the low voltage MotorControl Board.RAMPED OPERATION, Dip Switch No. 5 andNo. 6 ON, will work in the cooling cycle only. Acall on the “Y”, “G” and “O” together must bepresent for a ramped ON and OFF cycle. Ifa humidistat for cooling is not used, “BK” terminalmust be jumpered to “R” terminal. If not, only80% of the cooling airflow will be delivered.COOLING HUMIDISTAT OPERATION – “BK” and“R” terminals are connected to the humidistat.When the indoor humidity is high, the humidstat’sswitch will be open and the blower air flow will bereduced 20%.AIR FLOW PRIORITY is “W1” or “W2”, not thehighest air flow of “Y” or “W1” or “W2”. A DualFuel installation, a furnace and a heat pump,the airflow is compressor “Y” airflow exceptduring the defrost cycle. Then the blower willrun at W1 airflow when the furnace is on.COOLING CYCLE – Blower Time Delay to offis controlled by the ICM-2 Motor and Dip SwitchNo. 5 and No. 6 on the Motor Control Board. TheWhite-Rodgers Ignition Control Dip Switch #1must be turned on, O seconds, when a rampedor time-delay cycle is selected.HEAT EXCHANGER COOL-DOWN CYCLE – Theair flow will go to 50% of the cooling air flow.Heating cool-down time is controlled by theWhite-Rodgers Ignition Control, Dip SwitchesNo. 2 and No. 3.FAN CONTINUOUS OPERATION – The air flow is50% of the cooling air flow. If cooling air flow isrequired for continuous operation, removefield installed wires from “Y” terminal on thelow voltage terminal board and wire nutthem together. Then connect “G” terminal to“Y” terminal with a jumper.RAMPED OPERATIONS, Dip Switch No. 5 andNo. 6 ON, will work in the Cooling Cycle Only.A call on “Y” and “G” together is all that isneeded to get a ramped ON and OFF cycle. Thismotor computer program is different from afurnace for it does not need “O” input to enablea ramped cycle.COOLING HUMIDISTAT OPERATION – “BK”terminal is jumpered to “R” terminal, at the (ICMC)Motor Control Board plug. This jumper must becut to install a cooling humidistat.AIR FLOW PRIORITY is W1 or W2, not the highestair flow of “Y” or “W” programmed.HEAT EXCHANGER COOL-DOWN CYCLE – Airflow will go to 50% of the cooling air flow. Theheating cool-down time is controlled by theignition module.COOLING CYCLE – Blower Time Delay to offis controlled by the ICM-2 Motor and Dip SwitchNo. 5 and No. 6 on the (ICMC) Motor ControlBoard. The ignition module cooling time delaydip switch must be set to O seconds if rampedoperation or a time-delay cycle is selected.FAN CONTINUOUS OPERATION – The airflowis 50% of the cooling air flow. If cooling air flow isrequired for continuous fan operation, jumperG1 pin and G pin at the (ICMC) motor controlboard plug. A factory installed jumper pigtail,(BK), is connected to G1 pin for this purpose.100% IF NECESSARY9623 11/21/96ECM Manual 2380%DEHUMIDIFY50%50%FAST COIL COOLINGEFFICIENCYOFFOFF1Minute7.5Minutes3Minutes23
ICM-2 Inputs and Dip Switch FunctionsFURNACE MOTOR CONTROL BOARD SCHEMATICCNT 153712345678DIP 78D8L2 FANN/CLEDBRW2W1OGYLOYBKL5LEDL416 WIRECONNECTIONTO DD9L3LEDR1C1R2TT TPP P64 7FACTORY TEST PINST T T TP P P P1 2 3 5FACTORY TEST PINSDIAGRAM “A”OD UNIT SIZEAIRFLOW ADJUSTOFF-DELAY OPTONSAUX HT. AIRFLOWCOMMONREFERENCECOMMONW1 CFMOG FAN ON/OFFYLO CFMY CFMBKW2 CFMCFM LIGHT CFM LIGHT P2P2P2P2P2P2P2P2DIAGRAM 156141013816P2P2P2P2P2P2P2P2W1 INW2 INGR OUTG OUTN.C.W2 CFM OUTB OUTINTEGRATED FURNACE CONTROLTYPICAL CONNECTIONCOMPUTERK2K3TRK1TH1RB/C24 VAC INFrom Dwg 21B860551249623 11/21/96ECM Manual 2416 WIRECONNECTION TO ICM812345678
ICM-2 Inputs and Dip Switch FunctionsAIR HANDLER MOTOR CONTROL BOARD SCHEMATICCNT 1538DIP SWITCHESSEEDIAGRAM“A”5741111232915614101381616 WIRECONNECTIONTO ICM1D1234D2D3D45678D5D6D7D8AUXILLARYHEAT CONNECTOR13L2 MINALBLOCKBL5L1W1W2W4J – INTERLOCKC3N/CL4P2P2P2P2LEDLEDLEDCFMLED R5R41C1 C2D9R4R2K1R116T T TP P P1 2 5FACTORY TEST PINST TP P4 3FACTORY TEST PINSDIAGRAM “A”OD UNIT SIZEAIRFLOW ADJUSTOFF-DELAY OPTONSAUX HT. AIRFLOWCOMMONREFERENCECOMMONW1 CFMOG FAN ON/OFFYLO CFMY CFMBKW2 CFMCFM LIGHT CFM LIGHT 57411112329156141013816From Dwg 21B80033816 WIRECONNECTION TO ICMAUXILLARYHEAT CONNECTORDIP SWITCHES9623 11/21/96ECM Manual 25SEEDIAGRAM“A”5741111232915614101381616 WIRECONNECTIONTO ICM1D123456D2D3D4D5D678D7D8W1W213L2 FAN4K1K1W39J – INTERLOCKR8R6LEDBC3N/CL5L4L1CFMLEDT T TP P P1 2 5FACTORY TEST PINSD15R5R3LEDD10 1C1LED C2R4R4K116CNT 1866BRTW1OGYLOYBKW2W3TERMINALBLOCKD9R2R1T TP P4 3FACTORY TEST PINS25
ICM-2 Inputs and Dip Switch FunctionsPACKAGE UNIT MOTOR CONTROL BOARD SCHEMATICBRD 0986R7DIP IPI5741111232915614101381616 WIRECONNECTIONTO ICM123456785WD11DSD1D2D3D4D5D6D7D8C4L2 FAN4K1K2R8138G EDBKR4R5C1C21K1W2W2D9R116DIAGRAM “A”OD UNIT SIZEAIRFLOW ADJUSTOFF-DELAY OPTONSAUX HT. AIRFLOWCOMMONREFERENCECOMMONW1 CFMOG FAN ON/OFFY G1 CFMY CFMBKW2 CFMCFM LIGHT CFM LIGHT 13816From Dwg 21B664167269623 11/21/96ECM Manual 2616 WIRECONNECTION TO ICM
Quick Check Motor Will Not Run9623 11/21/96ECM Manual 27ICM’S CANNOT BETESTED UNLESSUNDER LOAD!27
Quick Check Motor Will Not RunMOTOR CONTROL BOARDS12 3 45 6 7 8ONOFFFANCFMR BK ORETRO FIT KIT – CNT 1654YYLO G W1 W2 BFURNACE – CNT 1537PACKAGE UNITBRD 0986AIR HANDLERTRBKOYY LOGW1W2 W3BTRBKR28OYY LOGW1W2 W3BJBBCNT 1538FANCFMOFFBKJUMPERCNT 1866RECM Manual 28ON 1 2 3 4 5 6 7 8FANCFM9623 11/21/96ON 1 2 3 4 5 6 7 8OFF
Quick Check Motor Will Not RunICM-2 QUICK CHECKBlower Motor Will Not Run1. Jumper 24 Volt A.C “R” Terminal to “G” terminal on theLow Voltage Terminal board.Does motor run?NO: Go to step #2.YES: Motor runs,check thermostatand thermostat wire.2. Unplug 16 wire low voltage harnass from the motor control board.Jumper 24 Volts A. C, to pins #12, #15 and common pins #1 and #3.Does the motor run?9623 11/21/96ECM Manual 29NO: Go to step #3.YES: Replace themotor control boardon Air handlers, orPackage units.On a furnace go tostep #5.29
Quick Check Motor Will Not Run3. Unplug 16 wire low voltage harness from the motor.Jumper 24 Volts A.C. to motor low voltage plug pins #12and #15 and pins #1 and #3 which are common.Does motor run?NO: Go to step #4.YES: Fault is in the16 wire low voltageharness. Repair orreplace it.4. Is the line voltage to the motor high voltage power plugpin #4 and pin #5 correct?Furnace ICM-2 motor correct voltage is 120 Volts A.C. and there mustbe a jumper wire in this plug between pins #1 and #2.Air handler ICM-2 motor correct voltage is 220 volts A.C.309623 11/21/96ECM Manual 30NO: Correct line voltage fault.YES: Live voltage correct andmotor will not run.Replace motor.
Quick Check Motor Will Not Run5. Plug the 16 wire low voltage harness from the motor back intothe motor control board. Jumper “G” in pin to “G” out pin of theWhite-Rodgers module which plugs into the low voltage motorcontrol board Does the motor run?YES: Replace White-Rodgers ignition module.JUMPER TO W/R PINS“G” IN & “G” OUTG R GW1 W2 IN OUT OUTNOT USEDW2 BCFM OUT9623 11/21/96ECM Manual 31JUMPER FROMSTEP # 1NO: Move the jumper to themetal part of the low voltagemotor control board plug.Does the motor run?YES: White-Rodgers ignitionmodule pins not making contactwith motor control board plugs.Clean pins & plugs by unpluggingand plugging board onto pins orreplace both if necessary.NO: Repair or replace the motorcontrol board.NOT USEDG R GW2 BW1 W2 IN OUT OUTCFM OUTJUMPER TOPLUG “G” IN & “G” OUT31
9623 11/21/9632ECM Manual 32
ICM-2 Will Not RunICM-2Blower Motor Will Not Run1. Jumper “R” terminal to “G” on the motor control boardIs the Fan Red LED on?NO: Go to step #2.YES: Go to step #5.2. Is there 24 V.A.C. between terminal “R” and “B” on themotor control board?9623 11/21/96ECM Manual 33NO: Check and repair as needed.Power to transformer, ortransformer or fuse.YES: Go to step #3.33
ICM-2 Will Not Run3. Is there 4.0 Volts D.C. at the motor low voltage control plug pin #15,G Fan On/Off, and pin #3 common? If 7 to 8 Volts D.C. is read, checkthese low voltage control plug connections at the motor, if connectionsare O.K. replace motor. “R” terminal to “G” still jumpered from step #1.NO: Go to step #6 if 0 volts is read. If voltage is low, less than 3 volts D.C., unpluglow voltage control plug from the motor and again read the voltage between pin#15 and pin #3. If voltage now is 7 to 8 volts D.C., replace the motor, if Voltage isstill low go to step #6.YES: Go to step # 4.4. Is there 24 Volts A.C. at the motor low voltage control pin #12,R timing reference and pin #1 common.349623 11/21/96ECM Manual 34NO: Check for 24 Volts A.C. at the other end of the low voltage control wireharness at the motor control board plug at pins #12, R timer reference and pin #1common. If voltage is not present, replace motor control board, if 24 Volts A.C. ispresent at this end of the harness fault is with the harness, repair or replace.YES: Go to step #5.
ICM-2 Will Not Run5. Is the line voltage to the motor high voltage power plug pin #4 and pin#5. correct?Furnace ICM-2 motor correct voltage is 120 Volts A.C. and there must bea jumper wire in this plug between pins #1 and #2, Air handler ICM2motor correct voltage is 220 Volts A.C.NO: Correct line voltage fault.YES: Line voltage correct andmotor will not run, replace motor.6. Unplug the 16 wire low voltage harness from the motor control board.Is there 7 to 8 Volts D.C. at the motor control board plug between pin#15, G fan On/Off and pin #3 common? “R” terminal to “G” terminalstill jumpered from step #1.9623 11/21/96ECM Manual 35NO: Replace motor control boardon an air handler or package unit,if trouble shooting a furnace.Go to step #7.YES: Fault is in the 16 wire lowvoltage harness or plugspin #15 or #3.35
ICM-2 Will Not Run7. Plug the 16 wire low voltage harness from the motor back into themotor control board. Jumper “G” in pin to “G” out pin of the WhiteRodgers module which plugs into the low voltage motor control board.Does the motor run?YES: Replace White-Rodgers ignition module.JUMPER TO W/R PINS“G” IN & “G” OUTG R GW1 W2 IN OUT OUTNOT USEDW2 BCFM OUTJUMPER FROMSTEP # 136ECM Manual 369623 11/21/96NO: Move the jumper to themetal part of the low voltagemotor control board plug.Does the motor run?YES: White-Rodgers ignition modulepins not making contact with motorcontrol board plugs. Clean pins andplugs by unplugging and plugging boardonto pins or replace both if necessary.NO: Leave this jumper in place and goback to step #6. If correct voltage is stillnot present repair or replace motorcontrol board. If correct voltage is nowread, fault is in 16 wire low voltage harness.NOT USEDG R GW2 BW1 W2 IN OUT OUTCFM OUT
Cooling Air FlowICM-2Correct Cooling Air Flow Can Not Be Obtained, Green CFM L.E.D.Will Not Flash The Correct Number Of Times Programmed.Ramped (Enhanced) Cycle Turned Off Or Has Timed Out.1. Is there 24 Volts A.C. between terminals “B” and “G” and “B” and“Y” at the low voltage motor control board terminals? The red fan L.E.D.and red “Y” L.E.D. should be on. Package units do not have a “Y” L.E.D.9623 11/21/96ECM Manual 37YES: Go to step #2 if thered “Y” L.E.D. is on.If the red “Y” L.E.D. isnot on, go to step #6.Package units go tostep #3.NO: Fault is in thethermostat orthermostat wires.37
Cooling Air Flow2. Is the red “BK” L.E.D. on?Package units go to step #3.YES: Go to #5.NO: Go to #3.389623 11/21/96YES: Go to step #4. If Humidistat operation or the ramped cycle does not workread #2 NO.NO: If a humidistat is installed it’s switch or it’s wire is open and the cooling airflow will be reduced by 20%. If the outdoor unit is an air conditioner a jumpermust be installed between “Y” and “O” terminals at the motor control board forhumidistat or ramped cycle operation. Heat pump installation “O” from thethermostat must be connected to “O” terminal on the motor control board forhumidistat or ramped cycle operation. If a humidistat is not installed a jumpermust be installed between “R” and “BK” terminal at the motor
TROUBLESHOOTING 1. Fan motor will not run. Use Chart # 1. 2. Fan will not change speeds or is running at the wrong speed. Use Chart # 2. 3. Fan motor is changing speeds up and down and the fan thermostat is not switching back and forth. Go to Chart # 1, Step # 5. 8 9623 11/21/96 ECM Manual 8