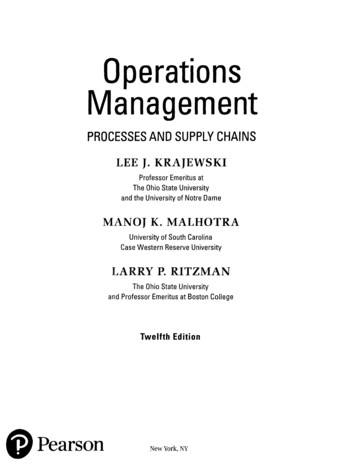
Transcription
OperationsManagementPROCESSES AND SUPPLY CHAINSLEE J. KRAJEWSKIProfessor Emeritus atThe Ohio State Universityand the University of Notre DameMANOf K. MALHOTRAUniversity of South CarolinaGase Western Reserve UniversityLARRY P. RITZMANThe Ohio State Universityand Professor Emeritus at Boston CollegeTwelfth EditionPearsonNew York, NY
ContentsPreface xvii2D USING OPERATIONSTO CREATEVALUE iDisney 1Role of Operations in an Organization 3Historical Evolution and Perspectives 4A Process View 5How Processes Work 5Nested Processes 5Service and Manufacturing Processes 6A Supply Chain View 7Gore Processes 7Support Processes 7Supply Chain Processes 8Operations Strategy 9Corporate Strategy 9Market Analysis 11Competitive Priorities and Capabilities 12Manageriaf Practica 1.1 Zara 13Order Winners and Qualifiers 14Using Competitive Priorities: An Airline Example 15Identifying Gaps between Competitive Prioritiesand Capabilities 15Addressing the Trends and Challenges in OperationsManagement 17Productivity Improvement 17Global Competition 18Ethical, Workforce Diversity, and EnvironmentalIssues 20The Internet of Things 21Developing Skills for Your Career 22Adding Value with Process Innovation 23Leaming Goals in Review 24MyLab Operations Management Resources 24Key Equations 25Key Terms 25Solved Problems 25Discussion Questions 26Problems 27Active Model Exercise 29Video Gase Using Operations to Create Value at Crayola 29Gase Chad's Creative Concepts 30SUPPLEMENT A Decision Making 31Break-Even Analysis 31Evaluating Services or Products 32Evaluating Processes 34Preference Matrix 35Decision Theory 36Decision Making under Certainty 37Decision Making under Uncertainty 37Decision Making under Risk 39Decision Trees 39Leaming Goals in Review 41MyLab Operations Management Resources 41Key Equations 42Key Terms 42Solved Problems 42Problems 44PART 1Managing Processes 49 2l PROCESS STRATEGYAND ANALYSIS 49CVS Pharmacy 49Process Structure in Services 53Customer-Contact Matrix 53Service Process Structuring 54Process Structure in Manufacturing 55Product-Process Matrix 55Manufacturing Process Structuring 55Production and Inventory Strategies 57Layout 57Process Strategy Decisions 58Customer Involvement 58Resource Flexibility 58Capital Intensity 59Strategie Fit 61Decision Patterns for Service Processes 61Decision Patterns for Manufacturing Processes 61Gaining Focus 62Managerial Practica 2.1 Plants-within-a-Plant at FordCamacari 63Strategies for Change 64Process Reengineering 64Process Improvement 64Process Analysis 65Defining, Measuring, and Analyzing the Process 66Flowcharts 66Work Measurement Techniques 68Process Charts 70Data Analysis Tools 72Redesigning and Managing Process Improvements 77Questioning and Brainstorming 77Benchmarking 78Implementing 78Leaming Goals in Review 80MyLab Operations Management Resources 80Key Terms 81Solved Problems 81Discussion Questions 84Problems 85Active Model Exercise 92Video Gase Process Analysis at Starwood 93Gase Custom Molds, Inc. 94Gase Jose's Authentic Mexican Restaurant 96XI
XIICONTENTS 3] QUALITYAND PERFORMANCE 9;QVC 97Costs of Quality 99Prevention Costs 99Appraisal Costs 100Internal Failure Costs 100External Failure Costs 100Ethical Failure Costs 100Total Quality Management and Six Sigma 101Total Quality Management 101Managerial Practica 3.1 Improving Quality ThroughEmployee Involvement at Santa Cruz Guitar Company 103Six Sigma 104Acceptance Sampling 105Statistical Process Control 106Variation of Outputs 106Control Charts 108Control Charts for Variables 110Control Charts for Attributes 114Process Capability 117Defining Process Capability 117Using Continuous Improvementto Determinethe Capability of a Process 118International Quality Documentation Standards andAwards 119The ISO 9001:2008 Documentation Standards 120Malcolm Baldrige Performance ExcellenceProgram 120Systems Approach To Total Quality Management 120Leaming Goals in Review 121MyLab Operations Management Resources 121KeyEquations 122Key Terms 123Solved Problems 123Discussion Questions 126Problems 126Active Model Exercise 134Video Case Quality atAxon 134Experiential Learning 3.1 Statistical Process Controlwith a Coin Catapult 136 4] CAPACITY FLANNING 137Tesla Motors 137Flanning Long-Term Capacity 139Measures of Capacity and Utilization 140Economies of Scale 140Diseconomies of Scale 141Capacity Timing and Sizing Strategies 141Sizing Capacity Cushions 141Timing and Sizing Expansion 142Linking Capacity and Other Decisions 143A Systematic Approach to Long-Term CapacityDecisions 143Step 1: Estimate Capacity Requirements 143Step 2: Identify Caps 145Step 3: Develop Alternatives 145Step 4: Evaluate the Alternatives 146Tools for Capacity Flanning 147Managerial Practica 4.1 Capacity Flanning at PacifiCorp 147Waiting-Line Models 148Simulation 149Decision Trees 149Leaming Goals in Review 149MyLab Operations Management Resources 149Key Equations 150Key Terms 150Solved Problems 150Discussion Questions 152Problems 152Video Case Gate Turnaround at Southwest Airlines 158Case Fitness Plus, Part A 159SUPPLEMENT B Waiting Lines 161Structure of Waiting-Line Problems 162Customer Population 162The Service System 163Priority Rule 164Probability Distributions 165Arrival Distribution 165Service Time Distribution 165Using Waiting-Line Models to Analyze Operations 166Single-Server Model 167Multiple-Server Model 169Little's Law 170Finite-Source Model 171Waiting Lines and Simulation 172SimQuick 172Decision Areas for Management 173Leaming Goals in Review 174MyLab Operations Management Resources 174Key Equations 174Key Terms 175Solved Problem 175Problems 176 5] CONSTRAINT MANAGEMENT 179Microsoft Corporation 179The Theory of Constraints 182Key Principles of the TOC 182Managing Bottlenecks in Service Processes 183Managing Bottlenecks in Manufacturing Processes 185Identifying Bottlenecks 185Relieving Bottlenecks 187Drum-Buffer-Rope Systems 187Applying the Theory of Constraints to ProductMix Decisions 188Managing Constraints in Line Processes 190Line Balancing 190Rebalancing the Assembly Line 195Managerial Practica 5.1 Assembly Line Balancingat Chrysler 195Managerial Considerations 195Leaming Goals in Review 196MyLab Operations Management Resources 196Key Equations 196Key Terms 197Solved Problems 197Discussion Questions 199Problems 199Experiential Learning 5.1 Min-Yo Garment Company 206Video Case Constraint Management at Southwest Airlines 210
CONTENTS 6] LEAN SYSTEMS 211ALDI 211Continuous Improvement Using A Lean SystemsApproach 213Strategie Characteristics of Lean Systems 215Supply Chain Considerations in Lean Systems 215Process Considerations in Lean Systems 216Managerial Practice 6.1 Alcoa 218Toyota Production System 221Designing Lean System Layouts 222One Worker, Multiple Machines 222Group Technology 223The Kanban System 224General Operating Rules 225Determining the Number of Containers 225Other Kanban Signals 226Value Stream Mapping 227Current State Map 227Future State Map 230Operational Benefits and Implementation Issues 232Organizational Considerations 232Process Considerations 233Inventory and Scheduling 233Leaming Goals in Review 234MyLab Operations Management Resources 234KeyEquations 234Key Terms 234Solved Problems 234Discussion Questions 237Problems 237Video Case Lean Systems atAutoliv 241Gase Copper Kettle Catering 242 T) PROJECT MANAGEMENT 243Burj Khalifa 243Defining and Organizing Projects 247Defining the Scope and Objectives of a Project 247Selecting the Project Manager and Team 247Recognizing Organizational Structure 247Constructing Project Networks 248Defining the Work Breakdown Structure 248Diagramming the Network 249Developing the Project Schedule 251Critical Path 251Project Schedule 252Activity Slack 254Analyzing Cost-Time Trade-Offs 255Cost to Crash 255Minimizing Costs 256Assessing and Analyzing Risks 259Risk-Management Plans 259Managerial Practice 7.1 San Francisco—Oakland BayBridge 260Statistical Analysis 261Analyzing Probabilities 263Near-Critical Paths 264Monitoring and Controlling Projects 265Monitoring Project Status 265Monitoring Project Resources 265Controlling Projects 266XIIILeaming Goals in Review 266MyLab Operations Management Resources 266KeyEquations 267Key Terms 267Solved Problems 268Discussion Questions 272Problems 272Active Model Exercise 279Video Case Project Management at Choice HotelsInternational 280Case The Pert Mustang 281PART 2Managing Customer Demand 2838 J FORECASTING 283Kimberly-Clark 283Managing Demand 286Demand Patterns 286Demand Management Options 286Key Decisions on Making Forecasts 288Deciding Whatto Forecast 288Choosing the Type of Forecasting Technique 289Forecast Error 289Cumulative Sum of Forecast Errors 289Dispersion of Forecast Errors 290Mean Absolute Percent Error 291Computer Support 292Judgment Methods 292Causal Methods: Linear Regression 293Time-Series Methods 295Naive Forecast 295Horizontal Patterns: Estimating the Average 295Trend Patterns: Using Regression 298Seasonal Patterns: Using Seasonal Factors 300Criteria for Selecting Time-Series Methods 302insights into Effective Demand Forecasting 303Big Data 304Managerial Practice 8.1 Big Data and Health CareForecasting 305ATypical Forecasting Process 305Using Multiple Forecasting Methods 306Adding Collaboration to the Process 307Forecasting as a Nested Process 308Leaming Goals in Review 308MyLab Operations Management Resources 308KeyEquations 309Key Terms 310Solved Problems 310Discussion Questions 314Problems 315Video Case Forecasting and Supply Chain Management atDeckers Outdoor Corporation 323Case Yankee Fork and Hoe Company 324Experiential Leaming 8.1 Forecasting a Vital Energy Statistic 326 9] INVENTORY MANAGEMENT 327Ford's Smart Inventory Management System (SIMS) 327Inventory Trade-offs 329Pressures for Small Inventories 330Pressures for Large Inventories 330
XIVCONTENTSManagerial Practica 9.1 Inventory Management at Netflix 331Types of Inventory 332Accounting Inventories 332Operational Inventories 333Inventory Reduction Tactics 335Cycle Inventory 335Safety Stock Inventory 335Anticipation Inventory 336Pipeline Inventory 336ABCAnalysis 336Economic Order Quantity 337Calculating the EOQ 338Managerial Insights from the EOQ 341Continuous Review System 342Selecting the Reorder Point when Demand and LeadTime Are Constant 342Selecting the Reorder Point when Demand IsVariable and Lead Time Is Constant 343Selecting the Reorder Point when Roth Demandand Lead Time Are Variable 347Systems Based on the Q System 348Calculating Total Q System Costs 348Advantages of the Q System 349Periodic Review System 349Selecting the Time Between Reviews 350Selecting the Target Inventory Level when DemandIs Variable and Lead Time Is Constant 351Selecting the Target Inventory Level when Demandand Lead Time Are Variable 352Systems Based on the P System 352Calculating Total PSystem Costs 353Advantages of the P System 353Leaming Goals in Review 353MyLab Operations Management Resources 353KeyEquations 354Key Terms 355Solved Problems 356Discussion Questions 360Problems 361Active Model Exercise 366Video Case Inventory Management atCrayola 367Experiential Leaming 9.1 Swift Electronic Supply, Inc. 368Case Parts Emporium 369SUPPLEMENT C Special InventoryModels 371Noninstantaneous Replenishment 371Quantity Discounts 374One-Period Decisions 376Leaming Goals in Review 379MyLab Operations Management Resources 379Key Equations 379Key Term 379Solved Problems 380Problems 382TO) OPERATIONS FLANNINGAND SCHEDULING sssCooper Tire and Rubber Company 385Levels in Operations Flanning and Scheduling 388Level 1: Sales and Operations Flanning 388Level 2: Resource Flanning 390Level 3: Scheduling 390S&OP Supply Options 391S&OP Strategies 392Chase Strategy 392Level Strategy 392Constraints and Costs 392Sales and Operations Flanning as a Process 392Spreadsheets for Sales and Operations Flanning 395Spreadsheets for a Manufacturer 395Spreadsheeets for a Service Provider 396Scheduling 398Job and Facility Scheduling 399Workforce Scheduling 400Managerial Practica 10.1 Scheduling Major League BaseballUmpires 401Sequencing Jobs at a Workstation 404Software Support 406Leaming Goals in Review 406MyLab Operations Management Resources 406Key Terms 407Solved Problems 407Discussion Questions 411Problems 411Active Model Exercise 418Video Case Sales and Operations Flanning at Starwood 418Case Memorial Hospital 419SUPPLEMENT D Linear Programming 42Characteristics of Linear Programming Models 421Formulating a Linear Programming Model 422Graphic Analysis 424Plotthe Constraints 424Identify the Feasible Region 426Plotthe Objective Function Line 427Find the Visual Solution 428Find the Algebraic Solution 429Slack and Surplus Variables 429Sensitivity Analysis 430Computer Analysis 431Simplex Method 431Computer Output 431The Transportation Method 433Transportation Method for Sales and OperationsFlanning 433Leaming Goals in Review 437MyLab Operations Management Resources 437Key Terms 438Solved Problems 438Discussion Questions 440Problems 440IT) RESOURCE FLANNING «9Philips 449Material Requirements Flanning 451Dependent Demand 451Master Production Scheduling 453Developing a Master Production Schedule 454Available-to-Promise Quantities 455Freezing the MPS 456
CONTENTSReconciling the MPS with Sales and OperationsPlans 456MRP Explosion 456Bill of Materials 457Inventory Record 458Flanning Factors 460Outputs from MRP 463MRP and the Environment 467MRP, Gore Processes, and Supply ChainLinkages 467Enterprise Resource Flanning 468How ERP Systems Are Designed 468Managerial Practice 11.1 ERP Implementationat Valle del Uli Foundation 469Resource Flanning for Service Providers 470Dependent Demand for Services 470Bill of Resources 471Leaming Goals in Review 474MyLab Operations Management Resources 474Key Terms 475Solved Problems 475Discussion Questions 480Problems 481Active Model Exercise 493Case Flashy Flashers, Inc. 493PART 3Managing Supply Chains 497J2) SUPPLY CHAIN DESIGN 497Amazon.com 497Creating an Effective Supply Chain 499Supply Chains for Services and Manufacturi
Gase Copper Kettle Catering 242 T) PROJECT MANAGEMENT 243 Burj Khalifa 243 Defining and Organizing Projects 247 Defining the Scope and Objectives of a Project 247 Selecting the Project Manager and Team 247 Recognizing Organizational Structure 247 Constructing Project Networks 248 Defining the Work Breakdown Structure 248 Diagramming the Network 249 Developing the Project