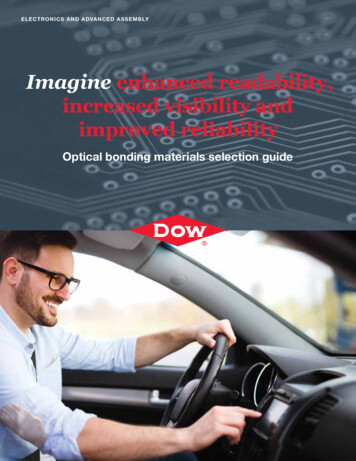
Transcription
EL EC T RO N I C S AN D A DVA NCE D A S SE MBLYImagine enhanced readability,increased visibility andimproved reliabilityOptical bonding materials selection guide
Why choose Dow Performance Silicones?Dow Performance Silicones has been a global leader in silicone-based technology for more than70 years. Headquartered in Michigan, USA, we maintain manufacturing sites, sales and customerservice offices, and research and development labs in every major geographic market worldwide toensure you receive fast, reliable support for your processing and application development needs.Unique product technologyCollaborative cultureOur substantial silicone legacy – showcased though theDOWSIL and SILASTIC brand names that encompass morethan 7,000 silicone products and services – offers a portfolio withbreadth and proven performance that few companies can match.We work closely with you to help reduce time and cost at everystage of your new-product development.Extensive know-howFor more than seven decades, we have been a global leader,investing in manufacturing and quality to help fuel yourinnovations, through a consistent supply of provensilicone products.We multiply our product value with deep in-house expertise andan extended network of industry resources.2Stability
DOWSIL VE Series silicone optical bonding for displaysApplications for optical bondingBenefits of optical bonding Improved viewing experience and readabilityCover window (glass or plastic)DOWSIL VE Seriesoptical bonding materialTouch sensorDisplay cell/panelKey characteristics ofDOWSIL VE Series siliconeoptical bonding materialsWe’ve tailored DOWSIL VE Series silicone optical bondingmaterials to meet your needs for cost, packaging, and a widerange of attributes – many of which are specific to opticallyclear resin (OCR) applications. High optical transparency High thermal stability Stable to UV degradationOur DOWSIL VE Series bonding materials – which offer theinherent benefits of silicone – are available with a broad range ofviscosities and mechanical properties. These materials provide: Good yellowing resistance under use conditions Good elongation Aging reliability Low modulus (to eliminate the mura effect) Choices for adhesion, hardness, viscosity, and refractive index A range of cure times and cure technologies Increased display ruggedness Extended display product lifeUnlike most displays, those used in automotive interiors endureharsh environmental conditions, including extreme temperatures,high humidity, and prolonged UV exposure. They consequentlydemand more robust adhesive materials that still support simple,cost-effective processing.The DOWSIL VE Series offers UV cure, UV/thermal dualcure and thermal-cure systems. These solutions are siliconebased optically clear resins that reliably bond a varietyof cover window materials – including glass, PMMA, and PC –to automotive LCD display modules. Their excellent opticalproperties help displays deliver superb performance properties,such as high transmittance, low haze, minimal yellowing, andsuperior reliability under common automotive environmenttest conditions.These silicone OCR solutions adapt easily to incumbentoptical bonding processes and deliver superior photothermalstability, mechanical properties, and optical performancefor optimized processing and performance of your nextautomotive display design.Why silicone optical bonding materialsfrom Dow?The inherent versatility of silicone chemistry can help expandyour design freedom, increase your processing options, andenhance the performance and reliability of your device. Asa class of materials, silicones generally offer demonstrablebenefits over organic-based solutions.Dow builds on silicone’s inherent potential by combining it withindustry-leading materials knowledge, application expertise,customer collaboration, and a global footprint.We’ve designed this guide to help you quickly narrow yoursearch for a bonding solution that will meet your specificapplication demands.Potential uses and applications Automotive displays Consumer displays requiring reliability in harsh conditions,such as micro/mini LED displays3
DOWSIL VE Series optical bonding materials –UV-cure technologyDOWSIL VE-6001 UVOptical Bonding MaterialDOWSIL VE-2003 UVOptical Bonding MaterialDOWSIL VE-3004 UHOptical Bonding Material(2)DOWSIL VE-3050 UHOptical Bonding Material(2)1-part1-part2-part2-part———3,6003 months withoutUV exposure 4,000mJ/cm²metal halide UV LEDat 365, 395, 405 nm———3,6003 months withoutUV exposure 4,000 mJ/cm²metal halide UV LEDat 365, 395, 405 nm1:14,1004,1004,1001:149,00039,00045,000 1 week under dark 1 week under dark 2,000 mJ/cm² at 365 nm 1 hr @ 25 C 2,000mJ/cm² at 365 nm 1 hr @ 25 CHardnessVolume shrinkage, %Lap shear strength(1), kgf/cm2Transmittance, %Refractive indexYellowness index(1)49 Shore OO 1.08.9 991.530.354 Shore OO 1.08.3 991.530.3240 Penetration 1.05.8 991.410.2820 Penetration 1.08.3 991.410.28Yellowness index(1)1.11.10.520.6Form factorProduct properties, uncuredMix ratio, A:BViscosity, Part A, mPa·sViscosity, Part B, mPa·sViscosity, Mixed, mPa·sPot life @ RT, minCure conditionsProduct properties, curedOptical properties after 1,000 hours at 85 C/85% RHSilicone thickness: 200 µm, glass/glass. (2)Developmental material. Specification writers: These values are not intended for use in preparing specifications.Please contact your local Dow representative or sales office before writing specifications on these products.(1)DOWSIL VE-2003 UV Optical Bonding MaterialOptical properties after reliability testVolumeSandwiched glass with 200 µm thickness, metal halide D bulb at 4,000 mJ/cm20.8960.6AtAtAtAt949290b*9885 C/85% RHTC105 C-40 CPer ASTM G1540200AtAtAtAt85 C/85% RHTC105 C-40 CPer ASTM G1540.40.2400600Time, hr8001,000002200400600Time, hr85 C/85% RHTC105 C-40 CPer ASTM G1541.510.504AtAtAtAt2.50200400600Time, hr5%4%3%2%1%0%Yellowness3Yellowness indexT% at 550 nm1Volume shrinkage, %b*Transmittance at 550 nm1008001,0008001,000DOWSIL VE-2003UV OpticalBondingMaterialAcrylic OCR
DOWSIL VE Series optical bonding materials –thermal-cure technologyDOWSIL VE-5002 HOptical Bonding MaterialDOWSIL VE-1204Quick Cure OpticalBonding MaterialDOWSIL VE-1204 HOptical Bonding Material(2)DOWSIL VE-1303 HOptical Bonding Material(2)Form factor2-part2-part2-part2-partMix ratio, A:BViscosity, Part A, mPa·sViscosity, Part B, mPa·sViscosity, Mixed, mPa·sPot life @ RT, minCure conditions1:1350264315 3601 hr @ 60 C1:13,8003,9003,9003.51 hr @ 25 C1:14,0004,0004,000 601 hr @ 60 C1:12,7002,8002,8003.00.5 hr @ 40 CHardnessVolume shrinkage, %Lap shear strength(1), kgf/cm2Transmittance, %Refractive indexYellowness index(1)21 Shore OO 1.06.9 991.410.340 Penetration 1.05.7 991.410.340 Penetration 1.06.1 991.410.345 Penetration 1.03.6 991.540.3Yellowness index(1)0.50.50.60.5Product properties, uncuredProduct properties, curedOptical properties after 1,000 hours at 85 C/85% RHSilicone thickness: 200 µm, glass/glass. (2)Developmental material. Specification writers: These values are not intended for use in preparing specifications.Please contact your local Dow representative or sales office before writing specifications on these products.(1)DOWSIL VE-1204 Quick Cure Optical Bonding MaterialOptical properties after reliability testSandwiched glass with 200 µm thickness, 1 hr @ 25 CTransmittance at 550 nmb*10.0980.8AtAtAtAt949290b*9685 C/85% RHTC105 C-40 C2000.685 C/85% RHTC105 C-40 CPer ASTM G1540.2Per ASTM G1540AtAtAtAt0.4400600Time, hr80001,0000200400600Time, hr8001,000Yellowness3.0Yellowness indexT% at 550 nm100AtAtAtAt2.52.085 C/85% RHTC105 C-40 CPer ASTM G1541.51.00.500200400600Time, hr8001,0005
Selecting an optical bonding materialLarge-size display ( 20")Slit-coating processScreen-printing processInjection processUsing precure processFill material: Large process window for precure conditionWith dam processDam material: Same as fill material with spot-cure systemFor thicker layer ( 400 µm)High-thixotropy OCR productsFor thinner layer ( 350 µm)High-viscosity OCR productsWith dam processLow-viscosity product for fill materialHigh-viscosity with thixotropic product for dam materialTypical-size display ( 6" to 13")Slit-coating processDam and fill processPatterning processUsing precure processFill material: Large process window for precure conditionWith dam processDam material: Same as fill material with spot-cure systemDam cure process windowLarge precure process window materialFor 10" size fillingFlowable-viscosity OCR productsPattern designProper-wettability OCR productsFlowable-viscosity OCR productsScreen-printing processSpecific-design display- Curved display- 3D auto displaySlit-coating processScreen-printing process6For thicker layer ( 400 µm)High-thixotropy OCR productsFor thinner layer ( 350 µm)High-viscosity OCR productsUsing precure processFill material: Large process window for precure conditionWith dam processDam material: Same as fill material with spot-cure systemFor thicker layer ( 400 µm)High-thixotropy OCR productsFor thinner layer ( 350 µm)High-viscosity OCR products
Optical bonding with siliconesCover glassOCRTouch sensorOCRLCM7
Typical processes for optical bondingLiquid optical bonding technology was introduced in late 1970s in the liquid crystaldisplay (LCD) industry and has been in use ever since. In the 2010s, optical bondingtechnology was being used widely due to the low total cost of ownership compared withthe dry-bonding process.The liquid optical bonding process can use either one-part UV-cure materials or twopart thermal-cure materials. The one-part materials, known as UV cure OCR or LOCA,are compatible with most bonding equipment and have faster cure times and easierhandling than two-part materials, making them the material of choice for many opticalbonding companies.There are three different liquid optical bonding processes: the dam and fill process,patterning, and the slit-coating process. In 2015, screen (stencil) printing processes anddam and injecting processes had been newly proposed for specific display designs,such as curved displays, 3D design displays, notch-design displays, and others.DOWSIL VE Series optical bonding materials are proven to be processable with awide range of optical bonding processes. Five representative liquid optical bondingprocesses are illustrated on the next page.Storage modulus, PaMaterials requirements for various process tionmaterial104100Large-size display ( 20")Especially for digitalinformation displays81,000Display ( 6" to 13")Typical auto display applicationDam materialScreen-printing material10,000Viscosity, mPa·sSpecific-design displayCurved or 3D autodisplay application
Representative optical bonding processes12345Dam and fillCover windowLCD moduleDispense OCR on moduleand precure it for DAMDispense OCR oncover window andlaminate cover glassLaminate glass andprecure the materialFull cureMaterials spreadFull cure(side cure addedif needed)PatterningCover windowLCD moduleDispense OCRon cover windowLaminate coverwindow on LCDSlit-coatingCover windowSlit-coat OCR oncover windowLCD moduleUV precureLaminate cover windowand precure the materialFull cureScreen printingCover windowMaskLCD moduleDispense OCR on maskframe to coat specific areaPrint OCR withsqueegee bladeDam and injectingLaminate coverwindow and LCDFull cureInjectionCover windowDispense dam material onLCD moduleLaminate cover glasson LCDInject OCR into laminatedLCD with cover windowFull cure(side cure added if needed)9
Typical failure modesEnvironmental reliability test conditions in the automotive industry have become morechallenging in recent years, with even more stringent conditions proposed in 2016.Consider the newly proposed reliability test conditions: 105 C for the high-temperature degradation test 85% RH or 90% RH at 85 C for the humid heat constant test -40 to 95 C for the thermal shock test and QUV or QSUN testsTo meet these exacting standards, increasingly reliable OCR materials arerequired for automotive displays. Acrylic OCR materials and other organic-filmmaterials have demonstrated weaknesses in their ability to meet these proposedreliability requirements.During the reliability tests based on the newly proposed conditions, variousfailure modes could be generated in optical bonding layers and films. Key factorsto prevent failures include changing the bonding process and/or changing theOCR and film materials.BubblesGenerated by the laminationprocess and outgassingPolarizer discolorationGenerated by the chemical reaction in PVABlack matrixDisplay and touch-sensing areaFlexible PCB for display and touch-sensingDelaminationCaused by volume shrinkageand adhesion changeYellowingTypical chemical reliability issuein the optical material industryMuraCaused by mechanical stress changesand bonding material color changes10
Reworkability methods for optical coupling resins (OCR)Chemical method1. Use wire to debond touchsensor and LCD module.2. Spray solvent (IPA or MICSOL 1620)on residual adhesives, or cloth wipecovering residual adhesives.3. Wait five minutes until residualadhesives soften.4. Rub with plastic blade toremove residual adhesives.5. Spray with solvent and cleanwith cloth wipe.Touch sensorOCR or OCALCD moduleSolventWireSolventCloth wipeorMark from wireremovalOCRLCD moduleadePlastic blOCRLCD moduleSoftened residualadhesivesOCRLCD moduleSamples cleanedwith IPA andMICSOL 1620IPAMICSOL 1620Mechanical method1.2.3.4.Use wire to debond touch sensor and LCD module.Store substrate with residual adhesives below -25ºC for 30 minutes.Rub with plastic blade to remove residual adhesives.Spray with solvent (IPA or MICSOL 1620) and clean with cloth wipe.Touch sensorOCR or OCALCD moduleWireStore below -25 CadePlastic blAfter rubbing withplastic bladeAfter cleaning with solvent(IPA or MICSOL 1620)OCRLCD moduleOCRLCD moduleSoftened residual adhesives11
Learn moreWe bring more than just an industry-leading portfolio of advanced silicone-basedmaterials. As your dedicated innovation leader, we bring proven process andapplication expertise, a network of technical experts, a reliable global supplybase, and world-class customer service.To find out how we can support your applications, visit consumer.dow.com/pcb.Images: 166347163, 190147254, 40680902676, 54346545405, 22010518, 1900147296, 172142592, 41989686783, 41958687688, 42006568975LIMITED WARRANTY INFORMATION – PLEASE READ CAREFULLYThe information contained herein is offered in good faith and is believed to be accurate. However, because conditions and methods of use of our products are beyond our control, this information should not be used insubstitution for customer’s tests to ensure that our products are safe, effective and fully satisfactory for the intended end use. Suggestions of use shall not be taken as inducements to infringe any patent.Dow’s sole warranty is that our products will meet the sales specifications in effect at the time of shipment.Your exclusive remedy for breach of such warranty is limited to refund of purchase price or replacement of any product shown to be other than as warranted.TO THE FULLEST EXTENT PERMITTED BY APPLICABLE LAW, DOW SPECIFICALLY DISCLAIMS ANY OTHER EXPRESS OR IMPLIED WARRANTY OF FITNESS FOR A PARTICULAR PURPOSE ORMERCHANTABILITY.DOW DISCLAIMS LIABILITY FOR ANY INCIDENTAL OR CONSEQUENTIAL DAMAGES. Trademarks of The Dow Chemical Company (Dow) or an affiliated Company of Dow. 2019 The Dow Chemical Company. All rights reserved.AMPM-19BDE435Form No. 11-3989-01 A
The one-part materials, known as UV cure OCR or LOCA, are compatible with most bonding equipment and have faster cure times and easier handling than two-part materials, making them the material of choice for many optical bonding companies. There are three different liquid opti