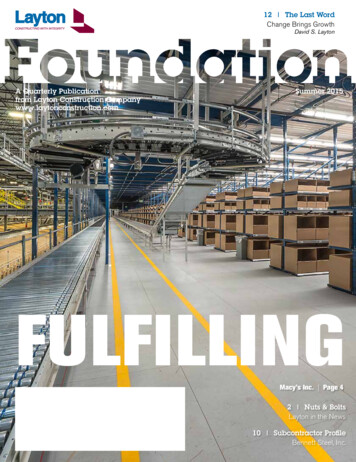
Transcription
12 The Last WordChange Brings GrowthDavid S. LaytonA Quarterly Publicationfrom Layton Construction Companywww.laytonconstruction.comSummer 2015FULFILLINGMacy’s Inc. Page 42 Nuts & BoltsLayton in the News10 Subcontractor ProfileBennett Steel, Inc.
[ Nuts & Bolts ]Featured ProjectLayton acquiresbay area companyLaytonhas acquiredthe assets ofCampbellFernandes andSons GeneralContractors ofCampbell, California. Fernandes,a general contractor with a 59-yearhistory specializing in healthcareprojects, brings a group of nearly30 construction professionals tothe Layton team, including projectmanagers, superintendents, projectengineers and carpenters.Fernandes excelled by buildingsound relationships with itscustomers, providing qualityconstruction and valued services.Through the transition, the SanJose office will operate as LaytonFernandes. The acquisition willhelp Layton build its northernCalifornia base, adding to projectsrecently completed or underconstruction, including MarriottCourtyard Sunnyvale, HamptonInn San Francisco Downtown/Convention Center, nineteen800Mixed-Use Development, and SanMateo County Jail.The Laie Courtyard by Marriott blends thefamiliar look and feel of other sister propertieswhile including truly Hawaiian features.Hawaii’s Beautiful CourtyardNorth shore hotel provides much-needed accommodations near PCCThe north shore of Oahu inHawaii is a sun-lovers dream.One of the most popular attractions in the area is the Polynesian Cultural Center, wherevisitors get a taste of numerouscultures from the Pacific islands.Layton built the new LaieCourtyard Marriott just feetfrom the Polynesian CulturalCenter. The new hotel addsmuch-needed accommodationsto the area.The 96,000-square-foot,three-story, 144-room hotel ispart of a vision to revitalize theKoolau Loa region. It includesan upscale pool, bistro, meetingspace, fitness area, laundry facility and media area.Courtyard Marriott propertiesare typically built in a uniformdesign, but unique featureswere approved by Marriottand added to the Laie property to make this facility trulyHawaiian. The lobby ceiling isspacious, creating an open viewof the pool and waterfall asguests enter. The facility passedMarriott’s detailed inspectionprocess on the first review — anachievement seldom, if ever,accomplished.The Laie Courtyard Marriott will also work closely withnearby BYU-Hawaii’s hospitality program to provide trainingand internships for students.Interior Construction Specialists giving A service to AAATravelers nationwide havecome to trust the AAA brandand their famous yellowroadside service trucks. AAA2 FOUNDATION selected Layton’s InteriorConstruction Specialists (ICS)to complete build-out of anew customer call center inClearfield, Utah.AAA’s “anytime serviceand reliability” is completelydependent on ICS’s construction schedule and phasingplan. Customer calls are beingLayton Construction Companytaken by AAA representatives in temporary space onsite while ICS completes the76,000-square-foot tenantimprovement project in fourcomplex phases over eightmonths. Temporary backupgenerators are in place, whileelectrical switch gear, meters, permanent generators,telecom equipment and officefinishes are completed. Powershut-downs and cross-overs tothe permanent space are coordinated and done live whileAAA representatives operate24/7.ICS has completed morethan 60 million of call centerprojects in the past few years.
[ Nuts & Bolts ]Layton employeedoes a good turnfor elderly manThe new on-campus housing complex at DixieState University in St. George, Utah, will offerthe latest in student-friendly living.Decked-out DormsQuick turnaround will bring better life to studentsWith a goal to combine “the amenities ofhome with a sense of community and theenergy of student life,” Layton has been selected to build an 88,000-square-foot, 350bed student housing complex on the campusof Dixie State University in St. George, Utah.Suites are designed to accommodate fromthree to six students in single or double roomformats. Designed to enhance social andacademic engagement, the complex includescomputer study and activity/lounge areas,laundry, conference, exercise and multipurpose rooms. Outdoor amenities includedecks, courtyards, volleyball courts, barbequepits and grassy areas.Construction begins in late August 2015and must be done for the start of classesin August 2016. Construction crews’biggest test will be an aggressive 12-monthschedule.Layton received anemail from a gratefulresident of Boise.“We are writing tothank one of youremployees in Boise.JD CROOKThree weeks agomy elderly father fell at the crosswalkon 13th and Myrtle. A young manfrom Layton Construction stopped andhelped him to the grass, and let himuse his phone to call me. He waiteduntil I showed up and helped him intothe car. The truly blessed thing is thatmy father actually had a stroke andprobably wouldn’t have made it. Wewould love the opportunity to thank himand tell him we appreciate his help.”The young man is JD Crook, aformsetter carpenter. Layton, too, isgrateful that he demonstrated Layton’svalues of kindness and helpfulnessby stopping to render aid. Congratulations, JD. We salute you.Airgas partners with Layton for state-of-the-art plantAirgas selected Layton to build a productionfacility in Tooele, Utah, that produces highpurity and precision-blended specialty gases.Airgas is one of the nation’s leading suppliersof industrial, medical and specialty gases usedin research and commercial laboratories, forenvironmental monitoring and for generatinglasers used in healthcare and manufacturing.A highly technical process piping systemwas designed and built by the Layton andMSS Mechanical team to move high-pressuregases at over 550 psi. Pipe made of Monel , anickel-copper alloy with high tensile strengthand resistance to corrosion and friction is usedto move high pressure oxygen, reducing thelikelihood of explosion. The 21,000-square-footbuilding features a unique colored concreteblock called the “Pasker Blend” developed byproject architect PGAW. Xeriscape landscapingenhances the facility’s sustainable design.ENR names LaytonNo. 76 on Top 40076#EngineeringNews-Recordhas namedLayton as the76th largestcommercialcontractor on its 2015 Top 400 Contractors list.In 2014, Layton completed 820million work in 23 states. Top construction sectors include healthcare,distribution/warehouse, hotels/hospitality, manufacturing and retail.Layton Construction Company FOUNDATION 3
Macy’s Inc.Tulsa, OklahomaFULFILLINMutual respect and trust led to successful completion of2 million-square-foot fulfillment center for Macy’sBY GREG BENNETTH4 FOUNDATIONaving the right team makes all the difference when it comes to the success of a project. The right team comes from having the best possible people who, through sharedand individual perspective and experience, develop trust in each other. Layton Construction Company
[ Project Profile ]NGMacy’s stressed the importance of hiring local contractors. Layton worked closely with the local workforce andfound capable subcontractors. In fact, 95 percent ofwork was performed by Oklahoma companies. The facilitywas named by Site Selection magazine as the largesteconomic development project in Oklahoma. When fullyoperational, the facility will employ 1,500 full-time workersand another 1,000 seasonal workers during the holidays.Layton Construction Company FOUNDATION 5
[ Project Profile ]The project is located on a bed of limestone with a 25-foot elevation change from the east to west. The team added 384,000cubic yards of engineered fill on the west side of the site andremoved 50,000 cubic yards of limestone. The excavation tooknine months of the project’s duration, with crews working sevendays a week, 12 hours a day.The Details Start DateApril 2014End DateMarch 2015Total Square Footage2 millionArchitectWare MalcombPhoenix6 FOUNDATION Bruce Quisno, vice presidentof construction for Macy’s Inc.,found a dream team during theconstruction of a fulfillment centerin Goodyear, Arizona. LaytonConstruction and Ware Malcombwere a contractor/architect matchmade in construction heaven.“Layton came highlyrecommended,” Bruce says.“Layton and Ware Malcomb did agreat job in Goodyear. It couldn’thave gone better.”Layton Construction Company“These types of jobs are big and complicated, but the Layton team makes the project run seamless and smooth.”Nicole DarlingArchitect, Ware MalcombA GROWING OPPORTUNITYWith Macy’s online retail business growing at a large rate, and tomaintain a competitive advantagein the online retail game, Macy’stook the same Layton/Ware Malcomb team — almost to a person— to Tulsa, Oklahoma to builda 2 million-square-foot facility inthe middle of the country to speeddistribution to customers.“We’ve been doing great businessin both brick-and-mortar and online,” Bruce says. “We’ve outgrownour capacity and needed a newbuilding to keep up with direct-tocustomer shipping demads. Tulsahas great access to two highwaysand good access to shipping partners like UPS and FedEx.”
The material handling system is the bestin the industry and the building needed torespond to the design needs of the system.ALL HANDS ON DECKLayton and Ware Malcomb wereinvolved early in the site selectionprocess, providing a wide array ofpreconstruction services as each sitewas evaluated.“Macy’s had to ultimately makethe call on which site they wanted,but we were there through theentire process to talk throughsite-specific issues,” says BrockGrayson, vice president withLayton Construction. “It was veryrewarding to help the client makedecisions early in the process thathad significant positive impacts tothe project during construction inregard to reducing cost and accelerating schedule.”“The whole preconstructionprocess was exciting,” says AndrewGeier, executive vice presidentwith Layton Construction. “Fromdownloading with Brock duringhis site selection travel, to competing with two local contractors, tofinally getting the call from Brucethat they had selected Layton tobuild the project, we were all so excited. Now all we had to do was goout and build a 2 million-squarefoot facility in 12 months. It’s toobad we didn’t have a meteorologiston our site selection team.”Key SubcontractorsConcrete. . . . . . . . . . . . . . . . . . . . . . . . . . . . . . Lithko Contracting, Inc.Drywall. . . . . . . . . . . . . . . . . . . . . . . . . . . Green Country Interiors, Inc.Earthwork / Paving. . . . . . . . . . . . . . . . . . . Cherokee Builders, Inc.Electrical. . . . . . . . . . . . . . . . . . . . . . . . . . . . . . . . . . Oil Capital ElectricSite Utilities. . . . . . . . . . . . . . . McGuire Brothers Construction, Inc.Fire Sprinkler. . . . . . . . . . . . . . . . . . . . Olympic West Fire ProtectionPlumbing. . . . . . . . . . . . . . . . . . . . . . . . . . . . . . . McIntosh CorporationMechanical. . . . . . . . . . . . . . . . . . . . . . . . . . . . . OCE Mechanical LLCRoofing. . . . . . . . . . . . . . . . . . . . . Saratoga Roofing & ConstructionStructural Steel. . . . . . . . . . . . . . . . . . . . . . . . . . . . Bennett Steel, Inc.Layton Construction Company FOUNDATION 7[ Project Profile ]Tilt-up concrete panels on theproject stand as tall as 45 ½feet. The fulfillment center has36-foot minimum clear heights.
[ Project Profile ]Located on a 72-acre site, the facility has a200-foot truck court on the south side of thebuilding, with more than 100 trailer positions.Oklahoma experienced a topfive season for rain, with 60 totalconstruction days impacted by rainthroughout the 12-month buildingcycle. This meant there had to beadjustments to the logistics of theproject. Many of those adjustmentsoccurred with strategic thoughtand were managed by Adam West,Layton’s senior superintendent onthe project.“The cadence of Layton is to stepback, analyze and then go do it,”Bruce says. “Adam is not only a greatcommunicator with the client, but8 FOUNDATION he’s great on-site, too. He handledjob-site adjustments smoothly and Ialways knew he had our back.”I’VE GOT YOUR BACKHaving each other’s backs is thekey to a successful team and thisability to see someone else’s perspective wasn’t lost on Nicole Darling,architect with Ware Malcomb.“Adam and his team were adream to work with — as always,”she says. “They have an attentionto detail and a perspective on theproject from every angle that leadsLayton Construction Companyto better buildings. They knowwhere we’re coming from on thearchitecture side and we trust themwhen they make suggestions tomake the project better.”When talking to those involved,you hear one word over and over:“trust.”“Trust. That’s how you workthrough things,” Bruce says.“When you know the other personis trying to see things from yourperspective, when you know theyhave your back, it’s easy to workthrough things together.”The respect and considerationwent both ways.“When we needed answers orapprovals, we would get themquickly,” says John Sirrine,construction manager for Layton.“We could count on them to comequickly.”‘I’M A HUGGER’Occasionally, the professionalrelationship morphs into a genuinefriendship. Such is the case withMacy’s and the teams at Laytonand Ware Malcomb.
[ Project Profile ]Layton’s construction team and WareMalcomb architects celebrate together at thededication and ribbon-cutting ceremony ofthe Macy’s fulfillment center on Aug. 6, 2015.“One of the things we appreciate about Layton isthat upper management is involved. Dave Laytonwas on site multiple times to personally see howthings were going.”Bruce QuisnoVice president of construction, Macy’s Inc.“It’s special when you developa genuine friendship with yourcustomer,” Andrew says. “This isone of those situations and thefriendship is enduring. As friends,we’re all focused on the collectivesuccess of the group — not onlyon this project, but on many moreto come.”This long-term approach andfriendship means you’re ableto keep short-term concerns inperspective a
4 FOUNDATION Layton Construction Company Macy’s Inc. FULFILLINGTulsa, Oklahoma Mutual respect and trust led to successful completion of 2 million-square-foot fulfillment center for Macy’s BY GREG BENNETT aving the right team makes all the difference when it comes to the success of a proj-