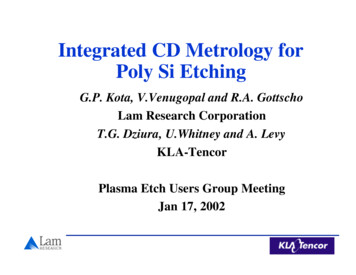
Transcription
Integrated CD Metrology forPoly Si EtchingG.P. Kota, V.Venugopal and R.A. GottschoLam Research CorporationT.G. Dziura, U.Whitney and A. LevyKLA-TencorPlasma Etch Users Group MeetingJan 17, 2002
Outlines Motivations Scatterometer concepts Results;;;;comparison to CD-SEM, x-SEM and AFMdifferent profilesrepeatability measurements193nm PR measurementss Summary
What Does CD Mean?s For smaller design rules, corner rounding, notching etccan make up a significant fraction of the line shape; Examples:?Pre etch?Post etch and cleans Where do we measure CD?; Not clear using CDSEM; Can measure CD at any height using SCD since the entire profileinformation is available
Demand For Profile Measurements For most processes, dimensional measurementsare required at specific locations on the features Example: STI applicationNitrideNitride bottom CDSilicon top CDSiliconTrench wall angleTrench depthSTI line
SCD Measurement ProcessOff-LineθProcessInfoFilm 2Film 1Wafer 240-780nmEllipsometer Amplitudeand phase areacquired Best ddataBest FitOn-ToolGratingInfoCD, HT, SWAetc.Offline:Library generationOnline:Film measurementProfile measurement
Advantages of SCDs Integrated metrology uses Low cost of ownerships High throughput; 100 wafers per hour with 5 measurement points for eachwafers CD as well as profile informations Non-destructive technique; prevent shrinkage of 193nm PRs Average profile of the grating area inspected
Disadvantages of SCDs Creation of off-line spectral librariess Library needs to be re-created if any of the grating parametersare changeds Test structures (grating) required; Current minimum grating size 50µm x 50µm50µm50µm
Applications of SCDs Integrated CD measurement (iCD) tool can beused in real time for; Feed forward control» measure pre etch CD/profile and adjust process recipe for desiredpost etch CD/profile; Feed back control» measure post etch CD/profile and adjust process recipe fordesired CD/profile; Fault detection» measure post etch CD/profile to detect any process excursionsand avoid further mis-processing of wafers
Stacks and Featuress Stack: resist / organic ARC / aSi / gate oxide / SilCD: 50, 55, 60, 65, 70, 75,80, 85, 90, 95, 100, 120, 140,160 nmlL/S ratio: 1:1, 1:2, 1:3, 1:5
Processess Process step: pre etch, postBARC etch, post a-Si etch,post a-Si etch and cleanla-Si etch: “nominal”,“tapered”, “bowed”
Sampling Plans 49 sites across the waferlMeasurements made atdifferent process steps weremade on sister wafersPreetchPostetchPostclean
Pre etch Results: XSEM & SCDs Good match to XSEM & spectral dataSCD profileresultresistBARCa-SiXSEM – SCD comparisonSCD model match to data160 1:1
Pre Etch Wafer Maps (160 nm 1:1)s wafer map data can be rapidlycollected at many sites acrossthe wafer, providing the processtool signatures limited sampling plans (5-site)heightwould not extract thisinformationwallangleMid CD
SCD compares well with AFM measurementPre etch wafer: PR thickness measurementsMeasurement TechniqueSCDx-SEMAFMPR thickness (nm)396390396
Post Etch Results: XSEM & SCDs 160 nm 1:5 L:Ss Mask erosion, a-Si profile are correctly measuredresistBARCetchresidueunderlyinga-Si profileXSEM – SCD comparisonSCD model match to data
Post Etch & Clean Results: XSEM & SCDs 160 nm 1:1 L:S, tapered etchscatterometry profile resulta-Sigate oxideXSEM – SCD comparisonSCD model match to data
Post Clean Wafer Bottom CD and Profile Mapss 160 nm 1:1 L:S; tapered etchs cross wafer profile uniformity is excellent400350300Y (nm)250200150100500-200 -150 -100-500X (nm)50100150200
Post Clean Wafer Sidewall Angle Maps 160 1:1 tapered etchs sidewall angle distribution is tight100%FrequencyCumulative %80%1560%1040%520%0%Gate sidewall angle (deg)88886 6.2586.86 5.75887 7.2587.87 5.750885 5.2585.85 5.75Frequency20Cumulative percentage (%)120%25
Post Clean Wafer Results: XSEM & SCDs 160 nm 1:1 L:S, bowed etchs sidewall profiles are accurately measuredSCD profileXSEM – SCD comparisonSCD model match to data
Good Correlation between CD-SEM and SCDCD-SEMSCDPre etch wafer1.1SCDnormalized SCD1.0510.950.90.90.951normalized CD-SEMCDSEM1.051.1
SCD: Static and Dynamic Repeatability 0.02nmPost clean wafer149.28MCD (nm)CD @ mid-height 30measurement #MCDaverage (nm)3*std dev (nm)range 219
CD-SEM Measurement Issues of 193nm PRs 193nm PR is known to shrink 10nm duringCD-SEM measurements (e-beam exposure); This can be minimized by using SCDs 193nm PR typically has rough sidewalls whichlead to ambiguity in CD measurements; This can be minimized by using a non-localizedmeasurement technique» SCD averages over the beam spot area» CD-SEM is a very localized measurement
Localized CD-SEM measurement can result inunrepeatable CD measurementsCD measurements on the same dieCD measurement 131.9CD measurement 125.5
193nm PR: Static Repeatability on pre etch wafer240230Line CD220210CD-SEM, 800V200CD-SEM, 300VSCD190180170012345measurement #CD drift after 5 measurements:CD-SEM, 800V 8.8 nmCD-SEM, 300V 8.1 nmSCD 0.16nm6
Summarys SCD provides accurate CD and profileinformation; low 3sigma dynamic and static repeatabilitys SCD shows good correlation to CDSEMand x-SEMs SCD enables process control; integrated on to the etch platform; feed forward, feed back and fault detections SCD better for measuring 193nm PR thanCD-SEM due to PR shrinkage
Integrated CD Metrology for Poly Si Etching G.P. Kota, V.Venugopal and R.A. Gottscho Lam Research Corporation T.G. Dziura, U.Whitney and A. Lev