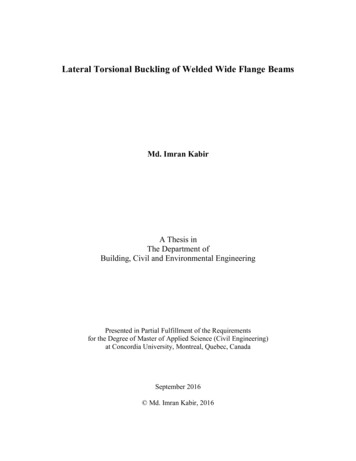
Transcription
Lateral Torsional Buckling of Welded Wide Flange BeamsMd. Imran KabirA Thesis inThe Department ofBuilding, Civil and Environmental EngineeringPresented in Partial Fulfillment of the Requirementsfor the Degree of Master of Applied Science (Civil Engineering)at Concordia University, Montreal, Quebec, CanadaSeptember 2016 Md. Imran Kabir, 2016
CONCORDIA UNIVERSITYSchool of Graduate StudiesThis is to certify that the thesis preparedMd. Imran KabirBy:Entitled:Lateral Torsional Buckling of Welded Wide Flange Beamsand submitted in partial fulfillment of the requirements for the degree ofMaster of Applied Science (Civil Engineering)complies with the regulations of the University and meets the accepted standards with respect tooriginality and quality.Signed by the final examining committee:Dr. Ashutosh BagchiDr. Lucia TircaExaminerDr. Anjan BhowmickSupervisorChair of Department or Graduate Program DirectorDate:ExaminerDr. Ramin SedaghatiApproved byDean of FacultyChair
AbstractLateral Torsional Buckling of Welded Wide Flange BeamsMd. Imran KabirLateral Torsional Buckling (LTB) can be defined as a combination of lateral displacement andtwisting due to an application of load on an unsupported beam. Design specifications of CanadaCSA S16-14 provides solutions for LTB of welded and rolled beams that were derived for constantmoment situation. Same equations have been used over the years for design of rolled and weldedshape beams. A recent study has shown that the current code equations might overestimate thecapacity of the welded wide shape beams, which make them unsafe to use. Thus a detailed studyis required to evaluate the existing LTB equations for welded wide flange (WWF) shapes. Thisthesis evaluates the performance of current equations in providing LTB capacities of WWF shapebeams. A nonlinear finite element (FE) model is developed to investigate the LTB capacity ofWWF shape beams. The validated FE model is used to analyze a series of simply supported WWFshape beams with varying unbraced lengths and subjected to equal end moments. Four differentpatterns of residual stresses and a constant initial imperfection of L/1000 are considered for theanalysis. In total, 320 FE models are analyzed, and it is observed that current code overestimatesthe LTB capacity of WWF shape beams as much as of 37% mainly using the measured residualstress of Lehigh University.Later, LTB capacity of WWF shape beams subjected to other loading configurations i.e. linearand non-linear moment gradient is investigated. Three types of linear moment gradient areconsidered i.e. end moment ratio of 0.5, 0.0, -1.0 while for non-linear moment gradient, two typesof transverse loading i.e. concentrated load at mid span and uniformly distributed load along thelength of the beam are considered in this research. In addition, for transverse loading, the effect ofiii
load height is taken into account by changing the position of load at top flange, centroid and bottomflange. Thus, in total 123 and 228 FE models are developed for linear and non-linear momentgradient respectively. From the parametric study conducted for linear moment gradient, it isobserved that current CSA S16-14 strength curve overestimates significantly for end moment ratioof 0.5 (40.1%) and 0.0 (34.57%) while it essentially coincides with FE results for end momentratio of -1.0.In the case of transverse loading, CSA S16-14 strength curve overestimates by 17% and 33% forconcentrated load and distributed load respectively when the load is applied at the top flange ofthe beam. Unlike the top flange loading, CSA S16-14 strength curve underestimates by 64% and44% for concentrated and distributed load applied at bottom flange respectively. However, in bothcases, CSA S16-14 reasonably matches with the FE results when the load is applied at shear centerof the cross-section. In addition, the mean value of equivalent moment factor, ω2 provides goodagreement with recommended values by CSA S16-14. In all cases, FE results are compared withother standards i.e. AISC, Eurocode as well as with latest equation proposed by the researchers inUniversity of Alberta. Although, Eurocode is found to be conservative in every cases but proposedequation by the researchers at University of Alberta shows good agreement only in the case ofunequal end moment and transverse loading condition. Hence, this equation can be used with alower resistance factor for LTB strength calculation of WWF beams.iv
ACKNOWLEDGMENTSIt is a pleasure to convey my gratitude to numerous people who helped me in many ways for thelast two years to complete my degree. Without their asistance, this thesis would not have beenpossible.First and foremost, I owe my deepest gratitude to my supervisor Dr. Anjan Bhowmick for hiscontinuous encouragement, support and guidance to pursue my graduate studies. It has been aprivilege and an honor to work with and learn so many things from Dr. Bhowmick. Besides Iwould like to express his gratefulness for funding this research project by the Faculty ofEngineering and Computer Science, Concordia University, Montreal, Canada and the CanadianInstitute of Steel Construction (CISC). I would also like to gratefully acknowledge Dr. Gilbert Y.Grondin for his valuable suggestions in this project.A special thanks goes out to my colleagues and friends especially Kallol Barua, Md. Anwar UsSadat , Mrinmoy Nath and Manik Mia for their moral support and encouragement during mystudies. Finally, I would like to thank my parents and brother whose sacrifice, financial support,and lifelong encouragement allowed me to accomplish many of my academic and personal goals.v
CONTENTSAbstract . iiiACKNOWLEDGMENTS . vLIST OF FIGURES . xLIST OF TABLES . xiiList of Symbols . xiiiList of Abbreviations . xviChapter 1 Introduction . 11.1 General . 11.2 Background . 21.3 Motivation of this Research . 51.4 Research Objectives . 51.5 Scope and Limitations. 61.6 Outline of the Research . 7Chapter 2 Literature Review . 82.1 Introduction . 82.2 Classical Lateral Torsional Buckling Solution . 82.3 Design Approach of Different Standards . 92.4 Factors Affecting Lateral Torsional Buckling . 19vi
2.4.1 Residual Stress . 192.4.2 Initial Imperfection . 202.4.3 Effect of moment gradient . 202.4.4 Effect of load with respect to the shear centre . 212.4.5 Effect of supports and restraints . 222.5 Detailed Review of Studies on Lateral Torsional Buckling of Welded Beams . 23Chapter 3 Finite Element Modeling . 333.1 Introduction . 333.2 Model Description . 343.2.1 Elements and Mesh Configuration. 343.2.2 Material Properties . 363.2.3 Boundary Condition . 373.2.4 Load Application . 403.2.5 Analysis Type . 413.2.6 Initial Geometric Imperfections . 423.2.7 Residual Stress . 463.3 Preliminary Validation . 50Chapter 4: Lateral Torsional Buckling of Laterally Unsupported WWF-beams Subjected toUniform Moment . 524.1 Introduction . 52vii
4.2 Validation of Finite Element Model . 534.3 Simulation Parameters . 554.3.1 Sectional Dimension . 554.3.2 Initial Imperfection . 554.3.3 Residual Stress . 564.3.3.1 Residual Stress Measured at Lehigh University . 564.3.3.2 Residual Stress Measured by Fukumoto and Itoh (1981) . 584.3.3.3 Residual Stress Measured by Dux and Kitipornchai (1983) . 594.4 Sensitivity Analysis on Welded Beams . 604.5 Summary . 70Chapter 5: Lateral Torsional Buckling of Laterally Unsupported WWF-beams Subjected to Linearand Non-linear Moment Gradient . 725.1 Introduction . 725.2 Evaluation of CSA Strength Curve for Welded Beams Subjected to Linear Moment Gradient. 735.3 Validation of FE model for Non-linear Moment Gradient . 775.3.1 Fukumoto et al (1980) . 785.3.2 Fukumoto and Itoh (1981) . 815.3.3 Dux and Kitipornchai (1983) . 83viii
5.4 Evaluation of CSA Strength Curve for Welded Beams Subjected to Non-Linear MomentGradient. 855.4.1 Welded Beams Subjected to Concentrated Load at Mid-Span . 865.4.2 Welded Beams Subjected to Uniformly Distributed Load . 885.5 Equivalent moment factor, ω2 for WWF-beams subjected to moment gradient. 915.5.1 Equivalent moment factor, ω2 for WWF-beams subjected to linear moment gradient 925.5.2 Equivalent moment factor, ω2 for WWF-beams subjected to transverse loading. 945.5.2.1 Welded Beams Subjected to Concentrated Load at Mid-Span . 945.5.2.2 Welded Beams Subjected to Uniformly Distributed Load . 95Chapter 6 Conclusions and Recommendations. 986.1 Summary . 986.2 Conclusions . 996.3 Recommendations for Future Work. 104REFERENCES . 106APPENDIX A . 111APPENDIX B . 116ix
LIST OF FIGURESFigure 1: Lateral torsional buckling . 1Figure 2: (a) The Marcy Pedestrian Bridge (Peraza, 2008), (b) Collapse of bridge girder atEdmonton, Canada . 3Figure 3: Different mode of LTB of beam. 4Figure 2.1: Moments at different position of a beam for any load configuration . 11Figure 3.1: Mesh Configuration of Finite Element Model . 36Figure 3.2: Boundary condition in finite element model . 38Figure 3.4: Longitudinal constraint for end points . 40Figure 3.5: Load Application in Finite Element Model . 41Figure 3.6: Sensitivity Analysis for initial geometric imperfection . 44Figure 3.7: Different eigen mode and associated state of failure for WWF-beams (half span only). 45Figure 3.8: Maximum flange sweep of L/1000 for initial imperfection . 46Figure 3.9: Recommended residual stress pattern by ECCS (1984) . 47Figure 3.10: Contour map of applied residual stress in finite element model . 48Figure 3.11: Distribution of residual stress across (a) flange and (b) web from FE model . 49Figure 3.12: Effect of residual stress on LTB capacity of steel beams . 50Figure 3.13: Preliminary validation of finite element model . 51Figure 4.1: Comparison between Finite Element and Test Results . 54Figure 4.2: Residual Stress measured (a) mill plate and (b) flame cut type at Lehigh University 57Figure 4.4: Residual Stress Measured by Fukumoto and Itoh (1981) . 58x
Figure 4.5: Residual Stress Measured by Dux and Kitipornchai (1983) . 59Figure 4.6: Simply Supported Beam with Equal End Moment . 60Figure 4.4. LTB resistance curves for various WWF-beams with different residual stress pattern. 64Figure 4.8: Finite element results vs CSA code values for (a) “Dux and Kiti”, (b) “Fuku and Itoh”,. 67(c) Mill Plate, (d) Flame Cut and (e) Zero type residual stress. 67Figure 5.1: Typical moment diagram for different moment gradient . 73Figure 5.2: Moment gradient LTB curves for (a) ω2 1.3, (b) ω2 1.75 and (c) ω2 2.3 . 75Figure 5.4: Test configuration and measured residual stress by Fukumoto et al (1980) . 78Figure 5.5: Load vs Deflection curve for 2.6 m long beam . 80Figure 5.6: Load vs Deflection curve for 2.0 m long beam . 80Figure 5.7: Load vs Deflection curve for 1.5 m long beam . 81Figure 5.8: Test configuration and measured residual stress by Fukumoto and Itoh (1981). 82Figure 5.9: Test Loading Configuration . 83Figure 5.10: Simply supported beam under concentrated load at mid-span and uniformlydistributed load acting at (a) (e) top flange, (b) (f) centroid, (c) (g) bottom flange, (d) typicalmoment diagram for concentrated load and (e) moment diagram for uniformly distributed load 85Figure 5.11: CSA strength curve for LTB and FE results for concentrated load applied at (a) topflange, (b) centroid and (c) bottom flange . 87Figure 5.12: CSA strength curve for LTB and FE results for uniformly distributed load applied at(a) top flange, (b) centroid and (c) bottom flange . 90xi
LIST OF TABLESTable 2.1: Eurocode 3 LTB Curve Selection* . 18Table 2.2: Length factor for end support conditions. 23Table 2.3: Recommended k values for different end condition . 23Table 2.4: Comparison of Proposed and Current equation with test data . 30Table 4.1: Comparison of Finite Element Results with Test Results . 54Table 4.2: Details of Cross-section . 55Table 4.3: Finite Element Results and Comparison with CSA S16-14 . 68Table 5.1: Mean values of material properties and comparison of FE result with test result . 79Table 5.2: Mean values of material properties and comparison of FE result with test result . 83Table 5.3: Dimension of test specimen and measured value of initial out-of- straightness . 84Table 5.4: Mean values of material properties and comparison of FE result with test result . 84Table 5.5: Equivalent moment gradient, ω2 for linear moment gradient and comparison with CSA. 93Table 5.6: Equivalent moment gradient, ω2 for concentrated load at mid-span . 95Table 5.7: Equivalent moment gradient, ω2 for uniformly distributed load . 96xii
List of Symbols𝐶𝑏 Modified equivalent moment factor𝐶𝑏Moment gradient factorCw , 𝐼𝑤Warping constant𝐹𝑦Yield stressℎ𝑜Centre to centre distance between flanges𝐼𝑡Torsion constantI𝑦 , 𝐼𝑧Moment of inertia about weak axis,𝑘𝑙Load height coefficient𝑘𝑟Constant for weak axis restraint𝑘𝑡Coefficient for end twist restraint𝐿𝑒Effective span𝐿𝑝Minimum unbraced length for attaining yielding of a memberLuUnbraced length of beamMbElastic buckling capacity of unbraced beam𝑀𝑐𝑟Critical lateral torsional buckling moment𝑀𝑚𝑎𝑥Maximum moment capacity from test/finite element analysis𝑀𝑚𝑎𝑥Absolute values of maximum moment𝑀𝑎Absolute values of first quarter moment𝑀𝑏Absolute values of second quarter moment𝑀𝑐Absolute values of third quarter momentxiii
𝑀𝑛Nominal moment capacity𝑀𝑝Plastic momentMuMoment derived from classical solution𝑀𝑦Elastic resistance𝑃𝑚𝑎𝑥Ultimate strength,𝑅𝑚Coefficient for single curvature bending𝑟𝑡𝑠Effective radius of gyration𝑟𝑦Radius of gyration about the y-axis𝑆𝑥Elastic section modulus about the x-axis𝑊𝑦Section modulus of a section𝑧𝑔Distance between load application point and shear centre𝑍𝑥Plastic section modulus𝛼𝑚Equivalent moment factor𝛼𝑠Slenderness reduction factor𝛾𝑀1Partial safety factor for resistance to instability𝜆̅LTNon-dimensional slenderness parameter𝜙𝐿𝑇Dimensionless parameterdTotal depth of beamEModulus of elasticity,GShear modulus of elasticity,JSaint-Venant torsion constant𝑘, 𝑘𝑤Effective length factors,xiv
K1Factor for end fixity,K2Factor for both lateral bending and warping restraint,pMagnitude of the concentrated loadyLocation of the applied load relative to the shear centreβEnd moment ratio𝜅Ratio of the absolute value of smaller factored moment and larger factoredmoment at ends of the unbraced length𝜆Modified slenderness ratio𝛷Resistance factor𝛽(𝑙𝑒)Rotation about the longitudinal direction.𝜁(𝑙𝑒)Displacement of the center of the cross-section along the longitudinaldirection𝜂(𝑙𝑒)Displacement of the center of the cross-section along y axis (along thevertical direction)𝜉(𝑙𝑒)Displacement of the center of the cross-section along x axis (along thelateral direction)𝐶1 , 𝐶2Coefficients for loading and end restraint conditions.𝜔2Uniform moment factor𝜆̅𝐿𝑇,0Corresponds the maximum resistance value of a given section at a plateaulevel𝛽Constant for the shape of the strength curvexv
List of AbbreviationsAASHTOAmerican Association of State Highway and Transportation OfficialsAISCAmerican Institute of Steel ConstructionASAustralian StandardCISCCanadian Institute of Steel Construction.COVCoefficient of VariationCSACanadian Standards AssociationECEuro CodeECCSEuropean Convention for Constructional SteelworkFEFinite ElementFEAFinite Element AnalysisLTBLateral Torsional BucklingSSRCStructural Stability Research CounsilUDLUniformly Distributed LoadWWFWelded Wide Flangexvi
Chapter 1 Introduction1.1 GeneralSeveral limit states are taken into account while designing a steel beams which includes theultimate flexural limit states of local buckling, full section yielding, inelastic and elastic lateraltorsional buckling. In addition to this failure in shear, yielding or buckling under concentratedloads, fatigue limit states and serviceability considerations for deflection and vibration need to bechecked during design. Among these limit states, lateral torsional buckling (LTB) is a state ofbuckling where a member exhibits both lateral deflection and twisting as shown in Fig.1.Figure 1: Lateral torsional bucklingEach steel specification has its own way of determining the strength of a steel beam that undergoesLTB and CAN/CSA is not exception to this. CAN/CSA follows same beam design formulas forboth W-beams and WWF-beams and provides the flexural capacity of these members consideringequal moment applied to the ends of a simply supported beam. Additionally, it recommends anequivalent moment factor for other loading configuration. However, several experimental test1
results confirmed substantial reduction in flexural capacity of a welded beam due to the presenceof high amount of residual stress generated from welding action. Thus, this research investigatesthe LTB behavior of WWF-beams in detail as well assess the performance of the current Canadianprovision of determining the LTB capacity in case of WWF-beams considering various types ofloading configuration. Moreover, results from finite element (FE) analysis are compared withother standards, for example AISC and Eurocode, as well as with latest equation proposed by theresearchers at University of Alberta. The following sections provide the background of theresearch and thus delineates the motivation of this investigation. The objectives and scopes of thisresearch are also outlined in Sections 1.4 and 1.5 respectively. An overview of the thesis contentsand research investigation process is then presented in Section 1.6.1.2 BackgroundBeams are frequently used in many structures in various shapes and sizes mainly because of itscapability of withstanding loads by resisting bending and shear. Different types of steel sectionsare being produced and practiced by the designers since many years; however, I-sections areconsidered most popular to be chosen as a beam. Usually flexural member such as beams andgirders have much greater strength about the major axis compared to minor axis. As a result ofthis, laterally unsupported beams and girders might fail by lateral-torsional buckling before theattainment of its full in-plane capacity. Thus, lateral torsional buckling (LTB) can be consideredas a limit state of structural design where the deformation changes suddenly from in-plane bendingto combined lateral deflection and twisting (Ziemian 2010). The final failure pattern involveslateral deflection and twisting in combination with various extents of yielding and flange and/orweb local buckling depending on the specific member characteristics (Ziemian 2010). Theconsequences of such kind of premature failure is devastating particularly if it occurs during the2
construction phase i.e. collapse of Marcy pedestrian bridge at New York in 2002, damage of steelbridge girder at Edmonton, Canada in 2015. Therefore, it is very important to understand andinvestigate the behaviour of structures and ensuring the structural stability of its members as awhole.(a)(b)Figure 2: (a) The Marcy Pedestrian Bridge (Peraza, 2008), (b) Collapse of bridge girder atEdmonton, CanadaSince the mid-nineteenth century, research has been performed intensively on lateral torsionalbuckling of beams and reported in several text books (Bleich, 1952; Timoshenko and Gere, 1961;Vlasov, 1961; Galambos T. , 1968; Trahair 1993). However, the analytical procedure of obtainingLTB strength are complex and only for the simplest cases the closed form solutions can be found.Depending on this length behaviour of LTB can be divided into three parts such as (1) elasticbuckling, (2) inelastic buckling and (3) plastic behaviour. The relationship between criticalmoment (Mcr) and unbraced length (L) for lateral-torsional buckling can be presented graphicallyas shown in Figure 3.3
Figure 3: Different mode of LTB of beamDifferent structural steel design standards (e.g., CAN-CSA S16-14 (2014), AISC-ANSI 360-10(2010), AS 4100 (1998) , and Eurocode 3 (2005)) provide different algebric equations forestimating the LTB resistance. However, in a general sense, all of them use similar approach:staring from the calculation of elastic LTB resistance M u and followed by a reduction of thistheoretical resistance by considering various factors such as geometric imperfections, local and/ordistorsional buckling, residual stress etc. (Ziemian 2010). Depending on the variables considered,nominal resistance for LTB varies considerably from statndard to standard. Australian and theEuropean standards, AS 4100 and EC 3, provide a substantial penalty for geometric imperfections(Ziemian 2010). Another important difference between Eurocode 3 and other standards isEurocode 3 provides two different strength curves for rolled and welded section. However, twoNorth American standards AISC 2010 and CSA S16-14 implicitly assume that the beam has noinitial out-of-straightness for long members that fail by elastic LTB (Ziemian 2010). Moreover,both AISC 2010 and CSA S16-14 make no distinction between rolled and welded beams.4
1.3 Motivation of this ResearchCurrent CSA S16-14 provisions do not make any distinction between welded and rolled shapeswhen dealing with the flexural strength. However, dif
CSA S16-14 provides solutions for LTB of welded and rolled beams that were derived for constant moment situation. Same equations have been used over the years for design of rolled and welded shape beams. A recent study has sho