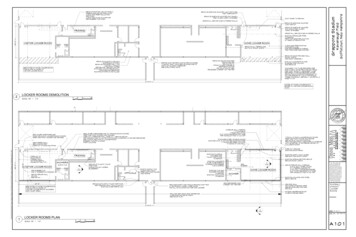
Transcription
REMOVE SURFACE MOUNTED EXIT SIGNS &FIRE ALARM HORN /STROBESDUCT WORK TO REMAINREINSTALL NEW DEVICES IN FURRED WALLSREMOVE SURFACE MOUNTEDLIGHT SWITCHREMOVE SURFACE MOUNTEDEXIT SIGN & FIRE ALARMHORN /STROBESTRAININGREINSTALL NEW DEVICES IN FURRED WALLS26'-0" /-EXISTING SPRINKLER PIPESTO REMAINPREP FOR HEAD RELOCATIONAT AREA OF DEMOLITIONVISITOR LOCKER ROOMHOME LOCKER ROOMREMOVE ALL FIBERGLASSBATTS AT ROOF JOISTSCLEAN AND PREP EXISTINGCONCRETE SLABFOR NEW RUBBER FLOORINGTEST FOR MOISTURE CONTENTREMOVE WOOD FRAMED WALL,WOOD JOISTS,AND ROOF ASSEMBLYREMOVE ACOUSTIC CEILING &SUSPENSION SYSTEMREMOVE DAMAGED WALL TILEAND WALL PANELSREPAIR AND REPOINT WATERDAMAGED CMU EXTERIOR WALLONCE NEW WATERPROOFROOFING SYSTEM IS INSTALLEDSEE NOTES AT HOME LOCKER ROOMFOR SCOPE OF WORK ATVISITOR LOCKER ROOMREPAIR AND/OR REPLACE WATER DAMAGEDTJI ROOF JOIST TAILS ABOVE DOOR AND ATWIDTH OF ACCESS CORRIDORSEE STRUCTURAL NOTEREMOVE CEILING MOUNTEDSPACE HEATERRELOCATE TOPIPING TO NEW CORNER INPREPARATION FORINSTALLATION OF NEWRECESSED CABINET UNIT HEATERGrappone StadiumREMOVE SURFACE MOUNTED LIGHT SWITCHESAND THERMOSTATKavanaugh FieldGoffstown, New HampshireREMOVE EXISTING CEILING FINISH &FIBERGLASS CEILING INSULATIONCLEAN AND PREP WALLS FORNEW FINISHCLEAN AND FLASH FLOOR FORNEW RUBBER TILE FINISHSAW CUT CONCRETE FLOORSLAB BEYOND COLUMNAND REMOVEDAMAGED TJI'S TO BE REPAIRED PERSTRUCTURAL NOTE. PROVIDE UNIT PRICEPER JOIST. QUANTITY REQUIRED TO BEREPAIRED TO BE DETERMINED AFTERDEMOLITION IS COMPLETE. BASE BID TOINCLUDE REPAIR OF TJI'S AT ENTRANCETUNNEL DOORWAY. SEE SKS-1 ON DETAIL 3SHEET A104212'-6" /NOTES AT HOME LOCKER ROOMREFER TO VISITOR LOCKER ROOMALSOLOCKER ROOMS DEMOLITION201'-0"4'8'16'6'SCALE: 1/8" NEW LEVER HARDWARE AND AT TRAINING ROOM DOORSPREP AND PAINT DOORS AND FRAMESFURR OUT CORRIDOR WALL: GWB TO 1' ABOVE CEILINGFRP WAINSCOTING TO 42" WITH PTD WOOD CHAIR RAIL AT ENTIRE PERIMETERSEE TYPICAL SECTION AT LOCKER ROOMRUBBER TILE WITH 6" BASEPAINT COLUMNSNEW LEVER HARDWARE ANDPANIC DEVICE AT LOCKER ROOM DOORSPREP AND PAINT DOORS AND FRAMESNEW FURRED WALLSEE HOME NOTESFURR OUT AT EXISTING PIPINGTYPICAL AT EACH LOCKER ROOM DOOR:PREP AND PAINT DOOR AND FRAMESEE NOTE AT COLUMN PAINTINGPROVIDE NEW PANIC HARDWARE AT INTERIORWITH LEVER SET AT EXTERIOR, KEYED TOCOLLEGE SYSTEMSTAINLESS STEEL DOUBLE HOOKSMOUNTED ON 5/4 X8 PAINTED WOOD BACKER17 HOOKS BETWEEN COLUMNS9 HOOKS AT CMU WALLFURR OUT AROUNDEXISTING ROOF DRAIN23'-5"EXISTING PLUMBINGFIXTURES ANDTOILET PARTITIONSTO REMAINTRAININGVISITOR LOCKER ROOMNEW SOLID PLASTIC TOILETPARTITIONSCRANTON HINY HIDERSBLUEBERRYCA104NEW RUBBER TILEAND 6" RUBBER COVE BASEOFFICIALSNEW EXTERIOR WALLON CMUSEE DETAIL 1EXISTG MOSAIC TILECLEAN AND CAULKPREP AND PAINT DOORAND FRAMENEW SOLID PLASTIC TOILET PARTITIONNEW CERAMIC WALL TILE TO MATCHEXISTING OVER PREP'D CMU29'-3"SEE NOTES AT HOME LOCKER ROOMFOR SCOPE OF WORK ATVISITOR LOCKER ROOM, SHOWERS,AND TOILET AREAEXISTING SPRINKLER PIPE ABOVEBELOW WOOD JOISTSEXISTING CONCRETESLAB TO BE PREP'D &FLASHED FOR RUBBERTILE FLOORINGSHOWERSEXSTG TILEEXISTING SUPPLY DUCT WORKSEE RCP FOR SOFFIT DROPEXISTING TILE ANDSHOWER FIXTURESTO REMAINEXISTING TILE FLOORTO REMAINPROVIDE SOFFIT AND FASCIA FRAMING AND TRIMAT ENTRANCE TUNNEL OVER DOORINSTALL HD ALUMINUM GUTTER AND LEADERBA104NEWRUBBERHOME LOCKER ROOMSHOWERNEW EXTERIOR WALL FURRING:3 5/8" GALV STEEL STUDSR13 FIBERGLASS BATTS6 MIL POLY VAPOR RETARDER5/8" MOISTURE RESISTANT GWBFRP WAINSCOTTING TO 42" AFFEXISTING COLUMNS AND STEELBEAM ABOVESEMI-RECESSED GASCABINET UNIT HEATERNEW END WALLWITH OPEN STORAGE AREASEE BUILDING SECTION ANDDETAILSEXTEND MEMBRANE ROOFOVER STORAGE AREAPROVIDE NEW SEAMLESS MEMBRANEOVER EXISTING METAL DECKSEE 'ROOF PLAN'The material contained in these drawings and thedesign they are intended to convey are the exclusiveproperty of Dennis B. Mires. Possession and usehereof is granted only confidentially in connection withconstruction and / or sale of the structure depictedherein as authorized by him, and the recipient agreesto abide by these restrictions. Any use, reproductionor desclosure of any information, in whole or in part,contained herein, without written permission of DennisB. Mires, is expressly prohibited.FURR OUT ATROOF DRAINFURRED WALLWHITE BOARDS &WAINSCOTTING, TYP26'-0" /-/Volumes/ActiveProjects/St. Anselm Grappone Stadium-2016136/Archicad-2016136/St A Grappone Stadium.pln Wednesday, April 12, 2017INTERIOR WALL FURRING1" Z CHANNELS1" RIGID INSULATION5/8" MOISTURE RESISTANT GWBFRP WAINSCOTTING TO 42" AFFFOOTBALLSTADIUM/LOCKERROOMSrevisions:212'-6" /AA103date:4/12/17proj. no.: 20150781LOCKER ROOMS PLANSCALE: 1/8" 1'-0"04'8'16'A101
Kavanaugh FieldGoffstown, New HampshireGrappone Stadium6'APPROXIMATE LOCATION OF BLEACHER SUPPORTINGSTEEL BEAMSCLEARANCE VARIES FROM TOP TO EAVEAPPROXIMATE LOCATIONS OF TJI ROOF JOISTS BELOW26'-0" /-GACOFLEX S-20 SILICONE MEMBRANE OVERPRIMER AND EXISTING METAL DECKRUN UP HIGH WALL AND NEAR SIDE WALLMINIMUM 16" WITH TERMINATION DETAILPER MFTR.PREP AND FLASH ALL PENETRATIONS;STEEL COLUMNS, PIPING AND DUCTWORKEXTEND OVER EAVE OF EXISTING DECKINGEXTEND AT LOCKER ROOM STORAGE AREAPROVIDE DEDUCT ALTERNATE FOR USEOF TUFF-GUARD ELASTOMERIC SYSTEM(POLMER MODIFIED BITUMEN)EXISTING ROOF DECK SURFACES TO BEPREPARED AND CLEANED PER MFTR'SRECOMMENDATIONS. INSTALL PRODUCTPER MFTR'S RECOMMENDATIONS.LOCKER ROOMS AND TOILET ROOMS ROOFThe material contained in these drawings and thedesign they are intended to convey are the exclusiveproperty of Dennis B. Mires. Possession and usehereof is granted only confidentially in connection withconstruction and / or sale of the structure depictedherein as authorized by him, and the recipient agreesto abide by these restrictions. Any use, reproductionor desclosure of any information, in whole or in part,contained herein, without written permission of DennisB. Mires, is expressly prohibited./Volumes/ActiveProjects/St. Anselm Grappone Stadium-2016136/Archicad-2016136/St A Grappone Stadium.pln Wednesday, April 12, 2017212'-6" /-LOWERBLEACHERROOF AREArevisions:date:4/12/17proj. no.: 2015078A102
PROVIDE SUPPLY DIFFUSER ANDEXHAUST GRILLE WITH DUCTWORKTO EXISTING MECHANICAL SYSTEMEXHAUST FANS28'-0" LEDWALL UP & DOWN LIGHTNULITE RW4MOUNT AT 6'-6"LED RECESSED LENSSHOWER FIXTURELISTED FOR WET LOCATIONLED RECESSED LENSSHOWER FIXTURELISTEDFORWET LOCATION3'-0" LEDWALL UP & DOWN LIGHT3'-0" LEDNULITE RW4 SERIESWALL UP & DOWN LIGHTMOUNT AT 6'-6"NULITE RW4 SERIESMOUNT AT 6'-6"SLOPED ACTDENSARMOR PLUS AT SHOWER CEILINGEXHAUST FAN REINSTALLEDCONFIRM OPERATION AND CONTROLNEW GWB ANS STEEL STUD DROP AT SHOWERNEW TYPICAL 24 X24 ACOUSTIC CEILING PANELS &SUSPENSION SYSTEMLED TROFFERSPAINT EXPOSED STRUCTURE AND PIPINGPREP AND PAINT HEATER UNIT ENCLOSURE3NEW SOFFIT AND FASCIAPVC OVER PT BLOCKINGALUMINUM GUTTER ANDLEADERS2GWB SOFFIT DROP3 5/8" STEEL STUDSNEW EXIT SIGN &EMERGENCY LIGHTINGNEW TWO WAY LIGHT SWITCHEMPTY CONDUIT AND RECEPTACLE FORWALL MOUNTED CLOCK (FIELD CLOCK)24" x 24" ACOUSTICAL CEILING TILEARMSTRONG CERAMAGUARDFINE FISSURED SQUARE LAY IN15/16" PRELUDE XL FOREXTERIOR APPLICATION-WHITEDENSARMOR PLUS OVERSTEEL STUD DROPAT SHOWER OPENINGAT 6'-8" AFF /-24" X 48" RECESSED FLAT PANELLED FIXTURE: METALUX APOR APPROVED SUBSTITUTELED RECESSED LENSSHOWER FIXTURELISTED FOR WET LOCATION24" X 24" RECESSED FLAT PANELLED FIXTURE: METALUX APOR APPROVED SUBSTITUTE1/2" DENSARMOR PLUSFIBERGLASS FACED GWBTAPED AND FINISHEDEPOXY PAINT7/8" GLAV FURRING @16" OCKavanaugh FieldGoffstown, New HampshireNEW EXIT SIGN& EMERGENCY LIGHTINGRELOCATED SPRINKLER HEADSFLUSH MOUNT IN CENTER OF TILENEW LIGHT SWITCHES & OUTLETSTYPICAL ACT @8'-0" /-VISITOR LOCKER ROOM CEILINGSEE NOTES AT HOME LOCKERROOM FOR SCOPE OF WORK;INCLUDING CEILING AND SUSPENSION,LIGHTING, EXIT SIGNS, ELECTRICAL, ETC.LED RECESSEDDOWNLIGHTS (3)4" APERTUREGrappone Stadium24" X 48" RECESSED FLAT PANELLED FIXTURE: METALUX APOR APPROVED SUBSTITUTEPROVIDE SAME SCOPE OF WORK ATVISITOR LOCKER ROOM AND TOILET/SHOWER AREAREFLECTED CEILING PLANSCALE: 1/8" 01'-0"4'8'16'INSTALL ADDITONAL R21 FIBERGLASSBATTS AT EXISTING SIDEWALLCOVER WITH T1-11 PLYWOOD SHEATHINGDRIP CAP TERMINATION REGLET AT MEMBRANETO T1-11GACO SILICONE S-20 SINGLE COMPONENTWATERPROOF MEMBRANE OVEREXISTING METAL DECKPREP SUBSTRATE PER MANUFACTURER'S RECOMMENDATIONSSEAL COLUMN AND PIPING PENETRATIONS 19'2 Bleacher DeckEXISTING METAL DECK3" CLOSED CELL POLYURETHANE SPRAY FOAM (R21)2 LB/CF DENSITY15 MINUTE THERMAL FIRE RESISTANT TOP COATEXISTING METAL DECK, WOOD JOISTS, &FINISH CEILINGEXISTING WOOD FRAMED SIDEWALLPARTIALLY INSULATED AND SHEATHEDINSTALL NEW 1/2 EXTERIOR RATEDPLYWOOD SHEATHING FROM ROOF16" UPACCESS HATCH BEYONDThe material contained in these drawings and thedesign they are intended to convey are the exclusiveproperty of Dennis B. Mires. Possession and usehereof is granted only confidentially in connection withconstruction and / or sale of the structure depictedherein as authorized by him, and the recipient agreesto abide by these restrictions. Any use, reproductionor desclosure of any information, in whole or in part,contained herein, without written permission of DennisB. Mires, is expressly prohibited.WOOD JOISTS & STRAPPINGREMOVE EXISTING FIBERGLASS BATTS1'-4"/Volumes/ActiveProjects/St. Anselm Grappone Stadium-2016136/Archicad-2016136/St A Grappone Stadium.pln Wednesday, April 12, 2017 19'2 Bleacher DeckSTAINLESS STEEL DOUBLE HOOKSMOUNTED ON 5/4 X 8PAINTED WOOD BACKEREPOXY PAINTED CMU6" RUBBER BASERUBBER FLOOR TILES:NORAMENT GRANO.14" (3.5MM)COLOR AND PATTERN:4877 TANZANITE ORAS SELECTED BY OWNER1A104 0"1 Locker RoomAREFLECTEDCEILING PLANS &LOCKER ROOMSECTION 0"1 Locker Roomrevisions:HOME LOCKER ROOM SECTIONSCALE: 1/4" 1'-0"02'4'8'date:4/12/17proj. no.: 2015078A103
EXISTING STEEL COLUMNS:PREP AND PAINTSW INDUSTRIAL ENAMELB54 SERIESOVERKEM KROMIKUNIVERSAL METAL PRIMERSURFACE PREPSSPC-SP6/NACE 3ACT AT 8'-0" /-DOUBLE HOOKS ON PAINTEDWOOD BACKER3'-6"EXISTING CMU, PREP AND PATCHEPOXY PAINT FINISH AND PRIME6" RUBBER BASETYPICAL RUBBER TILE FLOOR 0"1 Locker RoomPAINTED WOOD CHAIR RAILSEE DETAIL 1FRP OVER 2 LAYERS5/8" GWBFRP: 3/32" MARLITE ARTIZAN FRPABSTRACTS - 211 GRIZELOR AS SELECTED BY OWNERADHESIVE BACK INSTALLATIONDIVISION MOLDINGS-PVC INSIDE & OUTSIDECORNERS, DIVISION, AND EDGE6" RUBBER BASERUBBER FLOOR TILES:NORAMENT GRANO.14" (3.5MM)COLOR AND PATTERN:4877 TANZANITE ORAS SELECTED BY OWNERPROVIDE TILE WITH NORA nTxADHESIVE BACKINGREINSTALLED MARKER BOARDS2 LAYERS OF 5/8" GWB BEHIND ALLWAINSCOTTING FRP 0"1 Locker RoomSECTION AT TRAINING ROOM1'2'4'INTERIOR ELEVATION @ LOCKER ROOMSSCALE: 1/2" 01'-0"1'2'4'SEAMLESS MEMBRANE TO RUN CONTINUOUSACROSS ENTIRE LOCKER ROOM/TOILET ROOMAREASExisting TJI withdamage at supportMEMBRANE OVERALUMINUM DRIP EDGE4'-4" /- VIFCOVER PANELT1-11 PLYWOODSOLID BODY STAINNew 2x x 5'- 0" long ripped to fit snug against existing flanges,typ. each side of TJI. Fasten through web with two rows of 1/4"Simpson SDS heavy duty screws 3" long @ 6". Fasten each 2xto top and bottom flanges with one row of 1/4" Simpson SDSheavy duty screws 3-1/2" long @ 6".3/4" EXTERIOR GRADEPLYWOODTIGHT TO METAL DECKING& TOP OF CMU COURSESEXISTING BLEACHER SUPPORTAND SEATING ASSEMBLYEXISTING BLEACHER SUPPORTAND SEATING ASSEMBLYGACO S20 SILICONE SEAMLESS MEMBRANEEXISTING METAL DECK OVER STEELFURRINGGACO S20 SEAMLESS MEMBRANEEXISTING METAL DECK OVER STEELFURRING3" SPRAY FOAM POYUREATHANECLOSED CELL INSULATION15 MINUTE THERMAL BARRIER(FIRE RATED FOAM/CEMENTITIOUSTOP COAT)EXISTING WOOD JOISTS3" SPRAY FOAM POYUREATHANECLOSED CELL INSULATION15 MINUTE THERMAL BARRIER(FIRE RATED FOAM/CEMENTITIOUSTOP COAT)EXISTING WOOD JOISTSNEW ACT PANELS AND SUSPENSIONSYSTEMSTORAGE 'CUBBIES':ROOF ASSEMBLY- MEMBRANE3/4" PLYWOOD2 X 4 RAFTERS @ 16" OC3" CLOSED CELL SPRAY FOAMCONTINUOUS FROM MAIN ROOF AREA2 X 4 CEILING BLOCKING @ 16" OC5/8" MOISTURE RESITANT GWBFRP CEILING PANEL AND TRIMSWOOD TRIM AT HEAD AND JAMB5/8" MOISTURE RESISTANT GWB6 MIL POLY VAPOR RETARDER3 5/8" - 33 MIL GALV STEEL STUDS@ 16" OC2 ROWS OF STUDS TO PROVIDECMU AND FURRING WIDTHFULL CAVITY FIBERGLASS BATTSREAR WALL:T1-11 PLYWOOD SHEATHING, STAINEDTYVEK WEATHER BARRIERR21 FIBERGLASS INSULATION2 X 6 WOOD STUDS LAGGED TORAFTERS AND SEAT JOISTS6 MIL POLY VAPOR BARRIER5/8" MR GWBFRP PANELS8 1/4"5/4 X 3" PAINTED WOOD CHAIR RAILRADIUS TOP AND BOTTOM EDGEREBATE AT FRP EDGEFRP WAINSCOTTING WITH BASE TRIM2 LAYERS OF 5/8" GWB0 3/4"Prepared for Dennis Mires, P.A.2" RIGID CLOSED CELLINSULATIONMECHANICALLY ATTACHED8" STANDARD WEIGHTCONCRETE MASONRY UNITS3 COURSESSTRIP APPLIED WATERSTOPSEAT ASSEMBLY:PAINTED 3/4" PLYWOODVAPOR BARRIER2 X 6 JOISTS @ 16" OCR21 FIBERGLASS BATTS1/2" PLYWOODKNEE BRACES AT 4'-0" OC /-2'1" RIGID INSULATION1" Z FURRINGPVC EDGE TRIM AT BASE OF FRPVINYL FINISH J BEAD AT GWB6" RUBBER BASE6"2'3'8"2'-6"The material contained in these drawings and thedesign they are intended to convey are the exclusiveproperty of Dennis B. Mires. Possession and usehereof is granted only confidentially in connection withconstruction and / or sale of the structure depictedherein as authorized by him, and the recipient agreesto abide by these restrictions. Any use, reproductionor desclosure of any information, in whole or in part,contained herein, without written permission of DennisB. Mires, is expressly prohibited.01'-0"B4'-4" /- VIFSCALE: 1/2" /Volumes/ActiveProjects/St. Anselm Grappone Stadium-2016136/Archicad-2016136/St A Grappone Stadium.pln Wednesday, April 12, 2017PRIME AND 2 COATS EGG SHELL LATEXTAPED AND FINISHED GWB OVER STEELFURRING8'4'-6"NEW SOLID PLASTICFLOOR MOUNTEDOVERHEAD BRACEDTOILET PARTITIONSSS HARDWAREEXISTING LAV AND COUNTER1" Z FURRING1" RIGID INSULATION5/8" MOISTURE RESISTANT GWBFRP WAINSCOTING TO 42"5/4 X 4 PAINTED WOODCHAIR RAILPVC EDGE TRIMAT BASE OF FRP6" RUBBER BASE1'-1" /-EXISTING SPRINKLER PIPEPREP AND PAINTKavanaugh FieldGoffstown, New Hampshire3" CLOSED CELL RIGIDSPRAY FOAMINSULATION OVER TRAINING RMCLOSURE AT END & SIDE WALLSAS REQUIREDEXISTING STEEL COLUMNSPREP AND PAINTSEE PAINT NOTE SECTION BPROVIDE 8' LONG PTD WDBACKER &7-DOUBLE HOOKSSEE DETAIL ASPECIFIC LOCATIONPER OWNERCGWB AND 3 5/8" STEEL STUDDROPEXISTING DUCTLINEAR SIDE WALL DIFFUSERSACT SOFFIT10" /-NEW SILICONE MEMBRANEOVER EXISTING METAL DECKNEW MEMBRANE OVERPREPARED METAL DECKFLASHED COLUMN PENETRATIONSNEW ASSEMBLY PER SECTION 2ACOUSTICAL CEILING TILE AND SUPPORTPER REFLECTED CEILING PLANGrappone StadiumCLEAN ALL SURFACES TO RECEIVE NEW MEMBRANETIGHTEN ALL FASTENERS AND SEAL WITH SEAM SEALPER SPECIFICATIONDETAILSrevisions:Saint Anselm Locker RenovationTJI ReinforcementSW&C3SKS-1: TJI Reinforcement4/10/17date:Sk-14/12/17proj. no.: 20150781DETAIL AT LOW WALLSCALE: 3/4" 1'-0"01'2'3'2DETAIL AT STORAGE CUBBIESSCALE: 3/4" 1'-0"01'2'3'A104
DIVISION 07 01 50.61:GACO WESTERN GACOFLEX S-20 ELASTOMERIC SILICONE COATINGFOR REHABILITATION OF AGED METAL ROOFSMR-38-GF20Page 5MR-38-GF20Page 3E. Equipment: All equipment used during the operations shall be located so as not to adversely affect the dailyoperations or endanger occupants, structure or materials on-site. All spray equipment must be grounded during theoperations.22.1 MANUFACTURERSGaco Western, LLC, www.gaco.com1.1 SUMMARYA. This specification provides a waterproof, weather resistant, color-stable silicone elastomeric membrane for renovation ofaged metal roofs of all types and shapes. GacoFlex Silicone Coatings, along with primer and joint treatment, willprovide excellent protection for metal roofs, effectively sealing seams and fastener penetrations and renewing theoverall finish in order to extend the useful life of the roof assembly.B. GacoFlex S-2000 White Silicone Coating will reflect the sun’s ultraviolet rays. This ultraviolet radiation is normallyabsorbed and turned to heat. The reflectivity of GacoFlex Series Silicone coating will help to keep roof temperaturescooler and thus reduce demand on air conditioning equipment.* GacoFlex S-2000 White Silicone Coating meets Energy Star performance levels for reflectivity.C. Suitable surfaces to receive the system include steel, aged one year or treated galvanized steel, anodized aluminumand pre-finished metal (other than siliconized and fluorocarbon finishes ). The system is designed to renew an existingfinish or add a high performance finish to bare metal.NOTE: The base coat shall be allowed to cure a minimum of 2 to 6 hours. For best results, apply at temperaturesabove 50 F. (10 C) to a dry, frost free surface. The surface must be dry, clean & free of debris between coats.2.2 MATERIALS:NOTE: The topcoat must completely cover the base coat (the base coat must be an alternate color from the top coat)including expansion joint covers and flashing.A. Cleaner: GacoFlex GacoWash Concentrated CleanerB. Primer: GacoFlex E-5320 Epoxy PrimerOptional Granular Coat: An additional granular coat may be added. Apply one coat of GacoFlex S-20 Series Silicone2Coating at the rate of not less than .5 gallon per 100 square feet (1.89 L / 9.3m ), (8 mils dry (.20 mm)). Immediately2broadcast roofing granules into the finish coat at the rate of 30 lbs per 100 square feet. (13.6 kg / 9.3m ).C. Sacrificial Tape: 3M Scotchblue Industrial Adhesive Masking Tape 2750 or equal.D. Tape: GacoFlex SF-2000 SeamSeal brush applied, or GacoFlex 66-S Polyester Tape embedded in two coats ofGacoFlex S-20 Series Silicone.E. Coating: GacoFlex S-20 Series Silicone Coating color shall be White.*GacoFlex S-2000 white meets Energy Star performance levels for reflectivity.Note: GacoFlex WalkPad SF-2036 is the only walk pad system approved for use with GacoFlex coating systemsPART 3. - EXECUTIONA. Cast-In-Place Concrete: Division 03 3 000B. Flashing and Sheet Metal: Division 07 60 00C. Drains, Vents, and Penetrations: Division 07 72 00Optional WalkPad: Apply one coat of GacoFlex WalkPad SF-2036 at a rate of 4 gallons per 100 sq. ft. (64 wet mils);Broadcast GacoWalkPad safety yellow granules into wet coating at a rate of 0.5 lb. per 100 square feet to helpensure good traction.Note: Tape off WalkPad area using duct tape. Remove duct tape while coating is still wet.F. Other Materials Required: Gaco Western, LLC shall approve all other materials.1.2 RELATED SECTIONS1. Base Coat: Apply GacoFlex S-20 Silicone Series at the rate of 1.25 gallon per 100 sq. ft. At all edges andpenetrations, an extra pass must be applied. Dry film thickness shall be a minimum of 19 mils.2. Top Coat: Apply GacoFlex S-20 Silicone Series at the rate of 1.25 gallon per 100 square feet (2.84 L / 9.3 m ).Coat all surfaces including expansion joint covers and flashing. At all edges and penetrations, an extra passmust be applied. Dry film thickness shall be a minimum of 19 mils.PART 2 - PRODUCTSPART 1 - GENERALOptional 2 Coat Application:Caution: While the use of granules will improve traction, caution should still be exercised when walking onWalkPad, especially in wet conditions.3.1 EXAMINATION:A. Verify that substrate is ready to receive work; surface is clean, dry and free of substances that could affect bond.1.3 SUBMITTALSG. No traffic shall be permitted on the coated surface for a minimum of 3 days. Damage to the surface by other tradesE.Kavanaugh FieldGoffstown, New HampshireMR-38-GF20May 2014Supersedes 10/11Grappone StadiumApplication Specification:shall not be the responsibility of the roofing contractor.A. Product Data: Submit manufacturers’ standard submittal package including specification, installation instructions, andgeneral information for each waterproofing material.B. Applicator Qualifications: Submit current “Qualified Applicator” Certificate from the specified waterproofingmanufacturer.C. Warranty must be supplied by product manufacturerB. Verify that all other work involved with this area, done under other sections, has been completed and accepted by thearchitect and general contractor prior to starting the waterproofing application.3.2 PREPARATIONA. Coating Thickness: The finished dry film thickness will measure a minimum of 38 dry milsIt is extremely important to get the roof clean and dry.B. Defects: There shall be no blisters, pinholes, voids or membrane defects of any kind.C. Variations: Any variations from specified procedures or limits found by the contractor or representatives of GacoWestern, Inc. or the owner shall be immediately corrected by the contractor.A. Inspect Fasteners: Tighten and/or replace all loose metal deck fasteners.1.4 QUALIFICATIONSA. Primary waterproofing materials shall be a product of a single source manufacturer. The primary manufacturer shallrecommend secondary materials. Manufacturer shall have a minimum of 10 years experience in the manufacture ofMR-38-GF20materials of this type.Page 2B. Applicators shall have a minimum of 5 years experience in the application of waterproofing materials of this typespecified. Applicator shall possess a current “Qualified Applicator” Certificate from the specified waterproofinggaco.com800.331.0196manufacturer. Made in the USAC. Pre Bid Conference: 10 working days prior to bid opening there is to be a mandatory Pre-Bid Conference. Anyone notattending the Pre-Bid Conference will not be allowed to bid the project. All products considered an equal to thespecified product or any changes in the scope of work of installation or specifications must be presented at the Pre-BidConference. If a change in the specification is accepted, it will be considered as an alternate and will be presented as abid amendment issued 5 working days prior to the bid opening. No other changes to the specification or bid documentswill be accepted.D. Pre-Installation Conference: Just prior to commencement of the fluid application waterproofing system, meet at the sitewith a representative of the coating manufacture, the waterproofing contractor, the general contractor, the architect andother parties affected by this section. Review methods and procedures, substrate conditions, scheduling and safety.E. Meets Energy Star performance levels for reflectivity.1.5 DELIVERY, STORAGE AND HANDLINGA. Store all coating materials in the original unopened containers at 50 - 80 F (10 - 27 C) until ready for use.B. Follow the special handling or storage requirements of the manufacturer for cold weather, hot weather, etc.C. Safety: Refer to all applicable data, including, but not limited to MSDS, PDS, product labels, and specific instructionsfor specific personal protection requirements.3.4 FIELD QUALITY CONTROLB. First remove heavy deposits of dirt, leaves and other debris from the roof using broom or air broomer, then inspectthe entire roof surface and flashings for any open seams, tears, cuts, etc. Repair these flaws so water is not blownin under membrane during the cleaning process. Pressure wash roof with water and allow to dry completely.C. For general cleaning, after the roof is dry from initial cleaning, apply GacoWash Concentrated Cleaner according tolabel instructions with sprayer of choice, using a 3-4 foot (0.91-1.22 m) arc pattern. A Hudson-type agriculturalsprayer, conventional pressure sprayer or airless sprayer is recommended. Allow solution to stand for 10-15minutes, adding a light mist of water to prevent drying. While it sets, lightly agitate any heavily soiled areas with abroom or brush. Do not allow dirt to settle in low areas. Use a commercial power washer 3,000 psi (20.69 MPa) toremove debris and continue rinsing until all suds are gone. Start at the lowest point of the roof and work towards thehighest point. For low-sloped roofs, work away from and then back towards, roof drains. It is important to keep thesurface wet until all of the GacoWash and other residue has been completely rinsed off and the surface is clean.After cleaning and rinsing the roof, ensure no dirt or debris is present.D. Biological Control: Areas of algae, mildew or fungus on the roof membrane or the existing coating should be treatedwith a solution of 1 part household bleach and 3 parts water, followed by a power washer rinse using clear water.E. Drying: Allow surfaces to thoroughly dry to prevent blistering. Examine roof, paying particular attention to areas ofMR-38-GF20physical damage to determine that residual water has in fact dried before applying GacoFlex S-20 coating.Page 4in theNote: Drying timeMadedependsonUSAweather conditions suchgaco.comas temperature, humidity and800.331.0196air movement. The above dryingtimes assume good weather (70 F / 21 C daytime temperature) and no rain. Conditions of lower temperature and rainwill require a longer period for drying.Made in the USAgaco.com800.331.0196F. Substrate Condition: Loose paint, powdery or friable rust and scale must be completely removed by power brushing toprovide a sound, tight surface. Soft asphalt, and/or bitumastics and silicone caulking shall be completely removed.NOTE: Care must be taken to insure that the substrate is structurally sound and is properly prepared. The owner and/orcontractor must correct any defect in the condition of the substrate existing prior to the coating; otherwise these defectsmay adversely affect the condition of the coating over time, necessitating maintenance and/or repair.3.3 INSTALLATIOND. Ventilation: General room ventilation is satisfactory.E. Environmental requirements: Proceed with work of this section only when existing and forecasted weather conditionswill permit the application to be performed in accordance with the manufacturer’s recommendations.B. General Primer:1. No rust: Apply 1 coat of GacoFlex E-5320 Primer at a rate of one gallon per 300 sq. ft.A. The contractor shall guarantee that all work performed under this section will be free from defects in material andworkmanship. Upon notice of a defect in writing to the contractor within one year after completion of the work, thecontractor shall, at his own expense, make the necessary repair or replacement of the defective work.2. Minimal rust: Apply 2 coats of GacoFlex E-5320 Primer at a rate one gallon per 300 sq. ft per pass, resulting in a totalof one gallon per 150 sq. ft. of finished primer.B. Warranty must be supplied by product manufacturer3. Pronounced rusting: Apply 2 coats of GacoFlex E-5320 Primer at one gallon per 150 sq. ft. per pass, resulting in onegallon per 75 sq. ft. of finished product.C. A warranty is available with this system provided it has been installed by a Gaco Western Qualified Applicator and isinstalled according to this specification .An application for Warranty must be made prior to staring the job.D. Protection of building and occupants:1. All surfaces not to receive the system specified shall be protected from overspray hazard i.e. windows, doors,exterior and vehicles. Protective coverings shall be secured against wind and shall be vented if used inconjunction with the application preventing collection and moisture.2. The contractor is to post signs noting a potential overspray hazard within 400’ (121.90 m) of the application.3. All air intake ventilation equipment shall be turned off to prevent fumes from entering the building.4. All surfaces damaged during the application shall be restored at no expense to the owner.5. No smoking signs are be posted as mandated by local fire officials.D. Substrate: Proceed with the work as specified only after the substrate construction, preparation, and detail work hasE.been completed.Made in the USAgaco.com800.331.0196NOTE: Mixed GacoFlex E-5230 in accordance to directions on the can.NOTE: Allow drying to the touch, but no more than 72 hours prior to coating. If more than 72 hours pass,mechanically abrade surface and recoat with GacoFlex E-5320 Primer at one gallon per 300 sq ft.C. Waterproofing:1. All exposed fasteners must be waterproofed by applying GacoFlex SF-2000 SeamSeal to the fastener heads bybrush.2. All seams, flashings, protrusions and terminations must be waterproofed by one of the following methods:a. Taping: Apply a 6” wide strip of GacoFlex S-20 Series Silicone at a rate of 1.5 gal per 100 square feet,centered on the seam. Immediately embed GacoFlex 66-S polyester tape in to the wet coating, andapply another coat of GacoFlex S-20 Silicone at a rate of 1.5 gal per 100 square feet to completelycover the polyester tape. The tape must be applied smooth, without wrinkles, “fish mouths”, blisters orpin holes.b. GacoFlex SF-2000 SeamSeal, applied by brush or roller, 4” wide, centered on the seam, at 1 gal per75-100 sq.ft. Please note that on horizontal seams (end laps) and other details where significantmovement due to expansion, contraction, or other factors may occur; it is necessary to apply sacrificialtape prior to the application of GacoFlex SF-2000 SeamSeal.D. Coating:Apply one coat of GacoFlex S-20 Series Silicone Coating at a coverage rate of 2 ½ gallon per 100 square feet (5.682L/ 9.3 m ) to achieve a nominal film thickness of 38 dry mils. Double coat flashings and edge terminations.The material contained in these drawings and thedesign they are intended to convey are the exclusiveproperty of Dennis B. Mires. Possession and usehereof is granted only confidentially in connection withconstruction and / or sale of the structure depictedherein as authorized by him, and the recipient agreesto abide by these restrictions. Any use, reproductionor desclosure of any information, in whole or in part,contained herein, without written permission of DennisB. Mires, is expressly prohibited./Volumes/ActiveProjects/St. Anselm Grappone Stadium-2016136/Archicad-2016136/St A Grappone Stadium.pln Wednesday, April 12, 20171.6 WARRANTYA. Exposed Fasteners:All exposed fasteners must be retightened or replaced as needed.MEMBRANESPECIFICATIONNOTE: Application rate based on theoretical coverage, actual coverage may be less due to surface profile,losses due to overspray and wind, and residual coating left in the container. Additional material may be requiredto achieve a minimum of 38 dry mils.revisions:Made in the USAgaco.com800.331.0196date:4/12/17proj. no.: 2015078A105
densarmor plus at shower ceiling exhaust fan reinstalled confirm operation and control new gwb ans steel stud drop at shower new typical 24 x24 acoustic ceiling panels & suspension system led troffers paint exposed structure and piping prep and paint heater unit enclosure densarmor plus