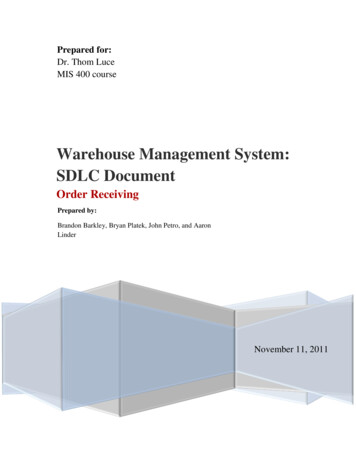
Transcription
Prepared for:Dr. Thom LuceMIS 400 courseWarehouse Management System:SDLC DocumentOrder ReceivingPrepared by:Brandon Barkley, Bryan Platek, John Petro, and AaronLinderNovember 11, 2011
Warehouse Management System: SDLC DocumentOrder ReceivingTable of ContentsCurrent State Analysis . 2System Overview . 2As-Is Use Case Diagram . 4As-Is Process Flows . 5Known Issues List . 6Requirements Definition . 7To-Be Use Case Diagram . 7To-Be Process Flows . 8Risk Assessment . 9Application Design . 10Functional Design Write-up . 10Site Map . 11Screen Prototypes. 12Database Design (ERD) . 161 Page
Warehouse Management System: SDLC DocumentOrder ReceivingCurrent State AnalysisSystem OverviewThe client for the project is interested in receiving an upgrade for their warehouse managementsystem. The mission of the project is to modernize, increase efficiency and reduce errors thattake place in their supply chain system. Currently the clients are using a fax based system to sendand receive orders. This system is crucial to the company because they need it to receive partsthat are required in their product. The company is looking to modernize this system and movetheir records into a database. Their reason for wanting to do this is because currently they areexperiencing manual errors caused by employees. They would like for us to increase processingspeed, reduce errors and create more standardization.The warehouse management system within the company is broken down into three differentdivisions. The first division is order placement (OP) which is where they will create orders,receive missing orders, reorder missing orders and send orders to be recorded. This division isused mostly at their assembly plant that is used to build vehicles. The clients would like thissystem to be able to order multiple products in multiple quantities as a single order. Theycurrently have been having issues with order fulfillment and would like the ability to listprevious orders that were either damaged or missing with the capacity to reorder them along withother items that have not been recently purchased. They would also like to be able to revieworder totals and have the power to edit their line items.The second division in their warehouse management system is order fulfillment (OF). In thisdivision they receive order information from order placement and store it on their data base.After that the products are placed onto pallets and then are identified by their RFID tags. Finallyas the pallets are shipped out an Advanced Shipping Notice (ASN) is then sent to the thirddivision. In this area of the warehouse management system they would like the ability to viewreceived orders and to be able to pack multiple orders on a single pallet. They would like to beable to do this because they follow the business accounting rule of first in first out (FIFO) fortheir inventory. The clients also need to be able to have more control over what pallets are beingshipped and the details of the order. They stress that the order fulfillment division must followwhat they call the Pack Three rule. This means that for every shipment they must pack at leastthree line items into a pallet and at least three pallets to a shipment.The final division of our client’s warehouse management system is order receiving (OR). Thisdivision is used for receiving orders of parts for their automobiles. They will simulate thedelivery of the products by using a RFID scanner. This information is then entered into the data2 Page
Warehouse Management System: SDLC DocumentOrder Receivingbase and will update the order placement division on the status of the order that was placed. Inthis area of the warehouse system the clients would like to have the capability of using the RFIDto update current statuses at the shipping dock. They would also like the RFID to be able to showif an order is missing or damaged.The issues that our client has been experiencing are causing them to slow down their businessand become less efficient. When we are done with the project we will have resolved most of theirissues by modernizing their technology. This technology will help aid them in being moreorganized and efficient through the use of the databases we created. It will also help resolve themanual errors that are occurring within the company because of the massive paper trail theircurrent fax based system is causing. Our goal for this project is to resolve all the issuessurrounding the current system while at the same time improving the functionality of our clientscompany.3 Page
Warehouse Management System: SDLC DocumentOrder ReceivingAs-Is Use Case DiagramFax Invioce to SupplierPlace New OrderFufill Orders fromOPReorderMissing/Damaged ItemsSend Order toWarehousePurchaser (Order Placement)Fax Missing/DamagedItems NotificationReview ShipmentContentsWarehouse (Order Receiving)4 PageRecieve OrderSupplier (Order Fulfillment)
Warehouse Management System: SDLC DocumentOrder ReceivingAs-Is Process FlowsPurchasingFulfillmentReceivingReady to orderitem(s)Order FaxedOrder RecievedOrder ProcessedAre supplyquantitiessufficient fororder?[[no]]Order Pending[[yes]]Order PackagedOrder ShippedSend Shipment NoticeReceive Shipment NoticeOrder RecievedDo thereceiveditemsmatchtheinvoice?Review Content of Order[[no]]Refax Order of Missing/DamagedNotify of Damaged or Missing Items[[yes]]Order Complete5 Page
Warehouse Management System: SDLC DocumentOrder ReceivingKnown Issues List Outdated technologyo Current fax based management system is cumbersome and is inefficient Often responsible for causing manual errors and slow processing speeds Lacks the ability of error control and ability to detect delays on parts All data and information is saved on paper, there is so much paper it has becomemore difficult to store it, organize or track files Lack of a centralized information system that automatically inputs and updates order informationin databaseInability to list ordered items that never got fulfilled and reorder them with other new itemsInability to review the total of an order or change quantities or remove items from an orderLack of the ability to review data about previous shipments that have been moved on to ORThere is no way to review shipments and their contents or confirm status of the LineItems 6 Page
Warehouse Management System: SDLC DocumentOrder ReceivingRequirements DefinitionTo-Be Use Case DiagramReorder Missing/Damaged ItemsSend Order Status UpdateEnter into database/update statusesReview ShipmentContentsCreate OrderScan RFID'sPurchaser (Order Placement)Recieve OrderSend OrderShip Product & ASNShip Order toWarehouseFulfill OrderSupplier (Order Fulfillment)7 PageWarehouse (Order Receiving)
Warehouse Management System: SDLC DocumentOrder ReceivingTo-Be Process FlowsPurchasingFulfillmentReceivingReady to orderitem(s)Enter orderinto SystemAre supplyquantities sufficientfor order?[[no]]Review & Submit OrderOrder Pending[[yes]]Order PackagedOrder ShippedSend Shipment NoticeReceive Shipment NoticeShipment RecievedScan RFID'sReview Shipment/Confirm Pallet StatusReorder Missing/Damaged ItemsSubmit to Database/Send Status Updates to OPOrder Complete8 Page
Warehouse Management System: SDLC DocumentOrder ReceivingRisk AssessmentRiskTeam DynamicsInexperience with RFIDOther commitmentsconflict with groupmeetingsInability to form a reliablemedium forcommunicationClientEmployee trainingEmployee resistance tonew protocolClient may not havesufficient IT resources tosupport the proposedsystemCost of the system andmaintenanceApplicationComplexity of building anentire system from theground upDifficulty in having theapplications“communicate” with theother entities’ applications9 PageLikelihood ImpactApproach/mitigationHighMedMedHighPay attention in classFind a time that is repeatableweekly.Med-lowVeryHighSet up system early / fall backto emailHighMedHighHighCreate a training manualIncentivize attendance totraining sessionsHighVeryHighInform client, such that theymay procure needed server(s)variableVeryHighDescribe the relativecomplexity of the system to theclient and its associated costs.Med-highMedhighVigilance, commitmentMed-highVeryhighMeeting between the threeentitiesEarly WarningSignsFalling behindschedulePersons being“out of the loop”/ things notgetting doneLow attendanceat trainingsessionsFalling behindschedule
Warehouse Management System: SDLC DocumentOrder ReceivingApplication DesignFunctional Design Write-upModuleDescriptionHome/login Authenticate UsersOR portal Displays order anomalies Links to other modules(pages)Order Check-In Allows for check-in of ordersOrder Review Forces the user to do a line-by-line review of ordercontentsOrder Review Allows for searching or previously received orders Allows for reviewing of previously receivedorders.OF Data receiver Receives data from Order fulfillmentOP Data Sender Passes data to Order Placement10 P a g e
Warehouse Management System: SDLC DocumentOrder ReceivingSite MapHome/loginMainOrder LookupOrderCheck-InLine Item Review11 P a g e
Warehouse Management System: SDLC DocumentOrder ReceivingScreen PrototypesOR MAINAfter login, user will be taken here. The page displays the current date and also shows the user anyanomalies with expected arrivals, etc. Clicking on the [select] button with in this dashboard will take theused to a detailed report showing the contents of the late order. The [Order Check-in] Button will take theuser to an RFID entry page, where the user can enter received orders. The [Order Lookup] button willtake the user to an Order lookup page where the user will be able to look at previous orders.12 P a g e
Warehouse Management System: SDLC DocumentOrder ReceivingOR Check-InThis page is reached from the [Order-check-In] button from the main page. That button is now disabled,because we are already on that page. [The Order lookup] button will allow the user to look up specificorders. The cancel button will return the user back to the main page, and the submit button will take theuser to a shipment review page.13 P a g e
Warehouse Management System: SDLC DocumentOrder ReceivingOR ShipmentCheckThis page is reached from submitting an RFID on the order check-in page. Both the Present and Missingcolumns will contain checkboxes, once one and only one checkbox has been checked in each row then theSubmit button will become enabled. Clicking the enabled submit button will pass information along toOrder Placement and return the user to the order check-in page.14 P a g e
Warehouse Management System: SDLC DocumentOrder ReceivingOR LookupThis page will allow users to type in an Order ID# and a query will return information from that orderID#, if such an order exists. The Order Check-In button takes the user to the order check-in page. TheCancel button will take the user back to the main page.15 P a g e
Warehouse Management System: SDLC DocumentOrder ReceivingDatabase Design (ERD)16 P a g e
Warehouse Management System: SDLC Document Order Receiving 2 P a g e Current State Analysis System Overview The client for the project is interested in receiving an upgrade for their warehouse management system. The mission of the project is to modernize, increase efficiency and re