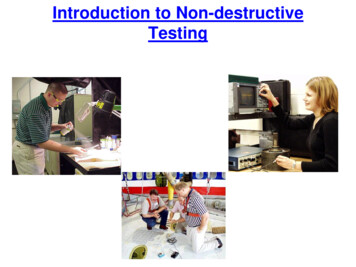
Transcription
Introduction to Non-destructiveTesting
Definition of NDTThe use of noninvasivetechniques to determinethe integrity of a material,component or structureorquantitatively measuresome characteristic ofan object.i.e. Inspect or measure without doing harm.
Methods of NDTVisual
What are Some Uses of NDE Methods? Flaw Detection and Evaluation Leak Detection Location Determination Dimensional Measurements Structure and MicrostructureCharacterization Estimation of Mechanical andPhysical Properties Stress (Strain) and DynamicResponse Measurements Material Sorting and ChemicalComposition DeterminationFluorescent penetrant indication
When are NDE Methods Used?There are NDE application at almost any stagein the production or life cycle of a component.–To assist in product development–To screen or sort incoming materials–To monitor, improve or controlmanufacturing processes–To verify proper processing such as heattreating–To verify proper assembly–To inspect for in-service damage
Six Most Common NDT Methods VisualLiquid PenetrantMagneticUltrasonicEddy CurrentX-ray
Visual InspectionMost basic and commoninspection method.Tools includefiberscopes,borescopes, magnifyingglasses and mirrors.Portable video inspectionunit with zoom allowsinspection of large tanksand vessels, railroad tankcars, sewer lines.Robotic crawlers permitobservation in hazardous ortight areas, such as airducts, reactors, pipelines.
Liquid Penetrant Inspection A liquid with high surface wetting characteristicsis applied to the surface of the part and allowedtime to seep into surface breaking defects. The excess liquid is removed from the surfaceof the part. A developer (powder) is applied to pull thetrapped penetrant out the defect and spread iton the surface where it can be seen. Visual inspection is the final step in theprocess. The penetrant used is often loadedwith a fluorescent dye and the inspection isdone under UV light to increase testsensitivity.
Magnetic Particle InspectionThe part is magnetized. Finely milled iron particles coated with a dyepigment are then applied to the specimen. These particles areattracted to magnetic flux leakage fields and will cluster to form anindication directly over the discontinuity. This indication can bevisually detected under proper lighting conditions.
Magnetic Particle Crack Indications
RadiographyThe radiation used in radiographytesting is a higher energy (shorterwavelength) version of theelectromagnetic waves that wesee as visible light. The radiation cancome from an X-ray generator or aradioactive source.High Electrical PotentialElectrons -X-ray Generatoror RadioactiveSource CreatesRadiationRadiationPenetratethe SampleExposure Recording Device
Film RadiographyThe part is placed between theradiation source and a piece of film.The part will stop some of theradiation. Thicker and more densearea will stop more of the radiation.X-ray filmThe film darkness(density) will vary withthe amount of radiationreaching the filmthrough the test object. less exposure more exposureTop view of developed film
Radiographic Images
Eddy Current TestingCoilCoil'smagnetic fieldEddy current'smagnetic fieldEddycurrentsConductivematerial
Eddy Current TestingEddy current testing is particularly well suited fordetecting surface cracks but can also be used to makeelectrical conductivity and coating thicknessmeasurements. Here a small surface probe is scannedover the part surface in an attempt to detect a crack.
Ultrasonic Inspection (Pulse-Echo)High frequency sound waves are introduced into amaterial and they are reflected back from surfaces orflaws.Reflected sound energy is displayed versus time, andinspector can visualize a cross section of the specimenfshowing the depth of features that reflect sound.initialpulsecrackechoback surfaceechocrack02468Oscilloscope, or flawdetector screen10plate
Ultrasonic ImagingHigh resolution images can be produced by plottingsignal strength or time-of-flight using a computercontrolled scanning system.Gray scale image produced usingthe sound reflected from the frontsurface of the coinGray scale image produced using thesound reflected from the back surfaceof the coin (inspected from “heads” side)
Common Application of NDT Inspection of Raw Products Inspection FollowingSecondary Processing In-Services DamageInspection
Inspection of Raw Products Forgings, Castings, Extrusions, etc.
Inspection FollowingSecondary Processing Machining Welding Grinding Heat treating Plating etc.
Inspection For In-Service Damage Cracking Corrosion Erosion/Wear Heat Damageetc.
Power Plant InspectionPeriodically, power plants areshutdown for inspection.Inspectors feed eddy currentprobes into heat exchangertubes to check for corrosiondamage.Pipe with damageProbeSignals producedby variousamounts ofcorrosionthinning.
Wire Rope InspectionElectromagnetic devicesand visual inspections areused to find broken wiresand other damage to thewire rope that is used inchairlifts, cranes and otherlifting devices.
Storage Tank InspectionRobotic crawlersuse ultrasound toinspect the walls oflarge above groundtanks for signs ofthinning due tocorrosion.Cameras onlongarticulatingarms are usedto inspectundergroundstorage tanksfor damage.
Aircraft Inspection Nondestructive testing is usedextensively during themanufacturing of aircraft. NDT is also used to find cracksand corrosion damage duringoperation of the aircraft. A fatigue crack that started atthe site of a lightning strike isshown below.
Jet Engine Inspection Aircraft engines are overhauledafter being in service for a periodof time. They are completely disassembled,cleaned, inspected and thenreassembled. Fluorescent penetrant inspectionis used to check many of the partsfor cracking.
Crash of United Flight 232Sioux City, Iowa, July 19, 1989A defect that wentundetected in anengine disk wasresponsible forthe crash ofUnited Flight 232.
Pressure Vessel InspectionThe failure of a pressure vesselcan result in the rapid release ofa large amount of energy. Toprotect against this dangerousevent, the tanks are inspectedusing radiography andultrasonic testing.
Rail InspectionSpecial cars are used toinspect thousands of milesof rail to find cracks thatcould lead to a derailment.
Bridge Inspection The US has 578,000highway bridges. Corrosion, cracking andother damage can allaffect a bridge’sperformance. The collapse of the SilverBridge in 1967 resulted inloss of 47 lives. Bridges get a visualinspection about every 2years. Some bridges are fittedwith acoustic emissionsensors that “listen” forsounds of cracks growing.
Pipeline InspectionNDT is used to inspect pipelinesto prevent leaks that coulddamage the environment. Visualinspection, radiography andelectromagnetic testing are someof the NDT methods used.Remote visual inspection usinga robotic crawler.Magnetic flux leakage inspection.This device, known as a pig, isplaced in the pipeline and collectsdata on the condition of the pipe as itis pushed along by whatever is beingtransported.Radiography of weld joints.
Special MeasurementsBoeing employees in Philadelphia were given the privilege ofevaluating the Liberty Bell for damage using NDT techniques. Eddycurrent methods were used to measure the electrical conductivity ofthe Bell's bronze casing at various points to evaluate its uniformity.
RADIOGRAPHYSub assembly Components:The sub assembly coach componentsfabricated by fillet welding are takenradiographs, where the load actingareas as prescribed by the relevantdrawing and suspected weld area duringvisual inspection.
MARKING OF RADIOGRAPHIC LOCATION,DIRECTION OF WELD BEAD AND PLACINGOF PENETROMETER
PLACING OF LOADED RADIOGRAPHICFILM
PLACING OF LEAD SHEET TO AVOIDSCATTER RADIATION
Sub-assembly ComponentsT1T2B2B1T2B2B1T1
RADIOGRAPHIC STANDARDS FOREVALUATION OF WELD DEFECTS.Two type of standards are generally used for evaluation1. IIW standard2. ASTM standard 1. IIW Standard:THERE ARE FIVE IIW STANDARDS– BLACK– BLUEDEFECT FREEVERY SLIGHT IMPERFECTIONS ASREGARDS HOMOGENITY IN THE FORM OF ONEOR MORE OF THE FOLLOWING DEFECT GASCAVITY, SHRINKAGE CAVITY, SLAG INCLUTIONAND UNDER CUT.
IIW RADIOGRAPHIC STANDARDS FOREVALUATION OF WELD DEFECTS.– GREEN SLIGHT IMPERFECTIONS AS REGARDSHOMOGENITY IN THE FORM OF ONE OR MORE OF THEFOLLOWING DEFECT GAS CAVITY, SHRINKAGE CAVITY, SLAGINCLUSION, UNDER CUT AND INCOMPLETE PENETRATION.– BROWN MARKED IMPERFECTIONS AS REGARDSHOMOGENITY IN THE FORM OF ONE OR MORE OF THEFOLLOWING DEFECT GAS CAVITY, SHRINKAGE CAVITY, SLAGINCLUSION, UNDER CUT, INCOMPLETE PENETRATION ANDFUSION DEFECT.
RADIOGRAPHIC STANDARDS FOREVALUATION OF WELD DEFECTS.– REDGROSS IMPERFECTIONS AS REGARDSHOMOGENITY IN THE FORM OF ONE OR MORE OFTHE FOLLOWING DEFECT GAS CAVITY,SHRINKAGE CAVITY, SLAG INCLUTION, UNDERCUT, INCOMPLETE PENETRATION, FUSION DEFECTAND CRACKIIW BLUE STANDARD IS FOLLOWED AT ICF WITHACCEPTANCE CRITERIA TO ICF SPECIFICATIONNO.ICF/M&C/SPEC/010
RADIOGRAPHIC STANDARDS FOREVALUATION OF WELD DEFECTS.RCF is using ASTM Standards for Radiographicevaluation. Specified Welding defects level as per ASTM E- 390 Vol-II–––––––Shrinkage /Crack of any kind are not allowedLack of Fusion is not allowedIncomplete Penetration is allowed up to level-IIBurn through is not allowedUndercut is allowed upto level-IVSlag Inclusion is allowed up to Level-IIIPorosity» Coarsed scattered Porosity is allowed upto level-II» Fine scattered Porosity is allowed up to Level-IV» Cluster Porosity is allowed up to Level-III» Elongated Porosity is not allowed
RADIOGRAPHIC STANDARDS FOREVALUATION OF CAST DEFECTS Specified Casting defects level asper ASTM E- 446– The castings should be significantlyfree from harmful casting defects like :» Shrinkage /Crack» Sand and Slag inclusions» Gas porosity or blow holes etc
For More Information on NDTThe Collaboration forNDT Educationwww.ndt-ed.orgThe American Societyfor NondestructiveTestingwww.asnt.org
NDT Education www.ndt-ed.org The American Society for Nondestructive Testing www.asnt.org . Title: PowerPoint Presentation Created Date: 9/28/2012 10:52:28 AM .