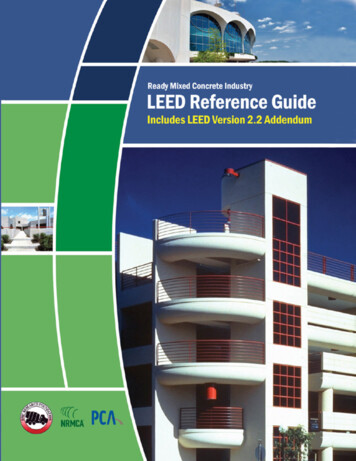
Transcription
The Ready Mixed Concrete IndustryLEED Reference GuideCopyright 2005 by the RMC Research Foundation
This document was underwritten by themixed concrete industry through leadership,Ready Mixed Concrete (RMC) Researchpromotion, education and partnering, ensuringFoundationthat ready mixed concrete is the buildingandthePortlandCementAssociation (PCA). It was researched andmaterial of choice.written by Steven Winter Associates, Inc.SWA, RMC Research Foundation, PCA(SWA), 50 Washington Street, Norwalk, CTand NRMCA would like to express their06854anthanks to the following people for theirindependent research and consulting firm withassistance in the preparation and review ofa long-standing commitment to achievingthis document: Edward R. Herbert III andenergy-,resource-efficientLionel Lemay, NRMCA; David Shepherd andbuildings. SWA works closely with projectBeatrix Kerkoff, PCA; David Goss, Americanarchitects, building owners, developers, andCoal Ash Association (ACAA); Jan Prusinski,otherapplySlag Cement Association (SCA); Martha Vansustainable, “whole building” strategies in aGeem, CTL Group; Jennifer LeFevre, RMCwide variety of building types: commercial,Research edAbstract: Ready mixed concrete opportunitiesfordesigners,architects,engineers, contractors, concrete producersandothersinthebuildingindustrytomaximize credits offered by the United Statesoperating costs, HVAC control ty and affordability. The guide isLeadership in Energy and Environmentalpublished by the RMC Research Foundation.Design (LEED ) New Construction (NC)The RMC Research Foundation is a non-version 2.1 standard. This document willprofit organization dedicated to improving theguide the reader in understanding the LEEDconcreteitsprogram and areas where ready mixedmission of promoting education and researchconcrete can be applied in a project to earnprojects that will strengthen and improve anLEED points, enhancing its sustainability.industrythroughachievingalready superior product in an gyenvironmentalfactors,organization of cement companies to improveLEED,mixedand extend the uses of portland cement ment,Reference: Steven Winter Associates,engineering, research, and public affairs work.Inc., Ready Mixed Concrete Industry LEEDNRMCA is a leading industry advocateReference Guide, RMC Research Foundation,working to expand and improve the readySilver Spring, Maryland, USA, October, 2005.
INDIT IS AGREED THAT SELLER’S LIABILITYANDPURCHASER’SSOLEREMEDY,RESPECTING THIS PUBLICATION OR ANYWHETHER IN CONTRACT, UNDER ANYINFORMATION CONTAINED HEREIN; ANDWARRANTY,ANY WARRANTY, EXPRESS OR IMPLIED,NEGLIGENCE), IN STRICT LIABILITY ORISOTHERWISE, SHALL NOT EXCEED THEEXCLUDEDANDDISCLAIMED,(INCLUDINGRETURNOF MERCHANTABILITY AND FITNESS FORPURCHASE PRICE PAID BY PURCHASER,A PARTICULAR PURPOSE; NOR IS THEREAND UNDER NO CIRCUMSTANCES SHALLANY WARRANTY THAT THIS PUBLICATIONSELLER BE LIABLE FOR ANY SPECIAL,ORINCIDENTAL,INFORMATIONCONTAINEDHEREIN WILL MEET OR COMPLY WITHTHE REQUIREMENTS OF ANY SAFETY ORENVIRONMENTAL CODE OF ANY STATE,MUNICIPALITY OR OTHER JURISDICTION.DAMAGES.THETORTINCLUDING THE IMPLIED WARRANTIESANYOFINORAMOUNTOFTHECONSEQUENTIAL
TABLE OF CONTENTSEXECUTIVE SUMMARY . 1INTRODUCTION . 1The LEED Certification Process . 2The Ready Mixed Concrete Industry LEED Reference Guide . 4USING READY MIXED CONCRETE TO ACHIEVE LEED-NC CREDITS . 5Sustainable Sites PREREQUISITE AND CREDITS . 5LEED Credit SS-C6.1 Stormwater Management - Rate and Quantity . 5LEED Credit SS-C6.2 Stormwater Management - Treatment. 5LEED CREDIT SS-C7.1 LANDSCAPE AND EXTERIOR DESIGN TO REDUCE HEATISLAND EFFECT . 14ENERGY AND ATMOSPHERE PREREQUISITE AND CREDITS. 19LEED EA-P2 MINIMUM ENERGY PERFORMANCE. 19LEED EA-C1 OPTIMIZE ENERGY PERFORMANCE. 19MATERIALS AND RESOURCES CREDITS . 27LEED Credit MR-C2 CONSTRUCTION WASTE MANAGEMENT . 27LEED CREDITS MR-C4.1 AND MR-C4.2 RECYCLED CONTENT. 32LEED CREDIT MR-C5.1 AND MR-C5.2 REGIONAL MATERIALS . 44LEED CREDIT MR-C7 CERTIFIED WOOD . 47INNOVATION IN DESIGN CREDITS. 52GENERAL DISCUSSION. 52LEED CREDIT ID-C1 EXEMPLARY PERFORMANCE IN MEETING CREDITREQUIREMENTS . 54LEED CREDIT ID-C1 FORTY PERCENT REDUCTION IN THE USE OF PORTLANDCEMENT. 58LEED CREDIT ID-C1 SITE-WIDE VOC REDUCTION . 61INCIDENTAL READY MIXED CONCRETE USE IN OTHER CREDITS . 65OTHER ENVIRONMENTAL ISSUES. 69Plant Waste Water Disposal. 69On-site Wash Water Disposal . 69Solid Waste . 70Site Protection. 71APPENDIX A – Potential LEED Credits from Ready Mixed Concrete . 72APPENDIX B – Sample Letter from Ready Mixed Concrete Producer. 74
EXECUTIVE SUMMARYuses and construction methods must beOf all the green building design anddocumented, and what issues must beconstruction evaluation programs in thecarefully considered in using ready mixedUnites States, the United States GreenconcreteBuilding Council’s (USGBC) LEED Ratingsustainability.toenhanceabuilding’sSystem is the most widely adopted standard.Public and private companies, governmentPotential LEED points gained throughagencies, trade groups, and other entitiesthe use of ready mixed concrete arethroughout the United States constructiondiscussed in the following areas: stormwaterindustry have adopted LEED as the standardmanagement; landscape paving; minimizingenergy use; optimizing energy ent; use of regional materials; use ofcertified wood; innovation in design; site-wideVOC reduction; and reduction in the use ofportland cement. The document also coversplant waste water disposal; on-site washwaterdisposal;solidwaste;andsiteprotection. In each of these areas, theConcrete offers several opportunities for buildingReference Guide presents information usefulprojects to gain LEED points.to the designer, the contractor, and the readymixed concrete supplier in achieving LEEDofpoints. This information is supplemented bysustainability. Recognizing the importance ofextensive lists of citations, references, andLEED,other resource documents, trade groups, elopment of a LEED Reference Guidethat could be used by architects, developers,clients, builders, manufacturers, suppliers,and others in the construction industry todetermine how the use of ready TRODUCTIONEstablished in 1998, the LEED GreenBuilding Rating System for New Construction(LEED-NC) is a voluntary, consensus-basednational standard for designing and D was developed by members of thedetailed discussion of the LEED program,USGBC representing many segments of thehow LEED points are assigned, how materialbuilding industry and environmental science.Theresultingdocumentpresents1
LEED’s mission is to: define that whichWhile the LEED-NC Rating System wasqualifies as a "green building" by establishinginitially designed for commercial high-riseameasurement;office buildings, the system can be used for apromote integrated, whole-building designwide variety of projects. LEED-NC Versionpractices;2.1, released in November 2002, ership in the building industry; ts.Also,theawareness of green building benefits; andUSGBC modified and added to the LEED-NCtransform the building market. While theRating System to create two new LEEDcurrent number of registered LEED projectsRating Systems; LEED-CI for Commercialonly accounts for about 5% of the UnitedInteriors and LEED-EB for existing buildings.States Commercial and Institutional BuildingIn addition, LEED-CS for Core and Shell andmarket, this number has grown from 12LEED-Hregistered LEED projects in 1999 to 2,164 byCommercial Interiors are currently in the pilotAugust projectsregistered between them. The USGBC isLEED Certification can be achieved at acurrently developing guidelines for residentialCertified, Silver, Gold, or Platinum leveland laboratory projects, and is making thebased on how many of the 65 LEED-NCfinal revision to the LEED-EB Rating SystemCredits are awarded after a project meetsfor Existing Buildings.seven LEED Prerequisites. The LEED-NCRating System divides these credits andThe LEED Certification Processprerequisites into six categories: alsandLEED is a voluntary rating system. AnResources,environmentally conscious building owner orEnergyandIndoor Environmental Quality, and Innovationdevelopermaychoosein Design. Prerequisites and Credits areconstructabuildingbased mostly on established governmental,environmental impact using the LEED ratingtrade group, or laboratory standards, such assystem as a guide. LEED certificationthe USEPA’s “Stormwater Management forquantifiesConstruction Activities,” or the standards forperformance for a building. Typically theenergyventilationowner’s representative, who is usually aneffectiveness of the American Society ofarchitect, is directed to design the building toHeating, Refrigerating, and Air Conditioningmeet a certain level of LEED certification.Engineers (ASHRAE). The number of pointsSome building owners have committed toathehaving all of their projects LEED certified andenvironmental performance criteria of theothers have committed to certifying onlyvarious LEED Credits determines the level atselected buildings. For example, severalwhich a project can be certified.public agencies such as city governments ofdesigntoandminimizeenvironmental
federal agencies have declared that all ofThe process of documenting compliancetheir new buildings shall be LEED certified.with LEED Criteria can begin early in theSome private companies have built newdesign, but many of the credits related toheadquarters using LEED certification.construction activities and building materialsrequire documentation that is not availableA project formally begins the alCertification process by having it registeredAdministration,as a LEED project on the USGBC websiteCompletion.(www.usgbc.org) by one of the project teamcommissioning (the process of making finalmembers. This process requires completingchecks and adjustments to construction andan online form that asks for information onbuilding operations), may need to continuethe project and the design team. Registeringbeyond substantial completion for seasonalalso requires a fee based on the total squareor deferred testing, projects are usually ablefootage of the project. The registration feeto assemble all the documentation needed toranges from 750 to 3,000 depending onsubmit a LEED Application to the USGBC atproject size. The registration process entitlesaboutthe project team access to ingSubstantialportions of the USGBC’s website and to twoThefree Credit Interpretation Requests (CIR).LEEDApplicationCIRs are made to the USGBC online when adocumentationproject deems that compliance with a credit’scompliance for all LEED Prerequisites andintent can be met without meeting the lettertargeted LEED Credits. The USGBC websiteofTheincludes detailed information on the requiredUSGBCformat for the LEED Application. Once awebsite includes access to all prior CIRsrepresentative has submitted the two copiesmade by registered projects and subsequentof the application to the USGBC, the USGBCUSGBC responses or “Rulings.”forwards one copy to a contracted ent.oftheorlettersincludesdeclaringand the LEED third party review processInformally, most project representativesbegins. The USGBC will issue a formalbegin the LEED process by evaluatingreview of the LEED Application within 30criteria of the various LEED Credits anddays. This first formal preliminary review willtargeting those most compatible with thedetail which credits are accepted, whichproject scope, budget, and environmentalcredits need additional documentation, andgoals. Representatives who start this processwhichin the early stages of the design process arepreliminary review provides descriptions ofusually more successful because they canthetake advantage of synergies between LEEDrequired. The project team then has 30 daysCredits and because they do not need toto provide the requested materials to themake design changes to meet LEED Criteria.USGBC. The final Certification then onThematerials3
within 30 days from the date in which theand “Innovation in Design.” These fourUSGBC receives the additional requestedcategories are taken directly from the LEED-materials. At that time, a set of 10 LEEDNC standard. A fifth section, “IncidentalCertified,PlatinumReady Mixed Concrete Use in Other Credits,”Certificates are issued to the design team inoffers guidance in how the material canrecognition of the LEED Rating earned. Theenhance opportunities for gaining LEEDactual LEED Plaque is then ordered and isCredits in other areas.Silver,Gold,orusually available within four to six weeks.In each section, the discussion of theanLEED-NC Credits relevant to ready mixedandconcrete is separated into those issuesconstruction that involves all team membersprimarily affecting the project designers (inin the project, including the design andthe section “Design Issues”) and thoseconstruction team, owners, product suppliersprimarilyand manufacturers, construction managers,professionalscost estimators, specification writers, andContractorothers.However, each group needs to read ions,although it is typically coordinated by aresponsible for completing documentationLEED-accreditedalsorequirements. In general, “Design Issues”prepares CIRs, the final submittal, and thedeals with issues that must be decidedresponses to the USGBC during the reviewbefore the project begins construction, whileperiod.“Trade Contractor and Manufacturer Issues”whobothtraderesponsibility of several team members,professional,astheareoftenis concerned with actual construction andThe Ready Mixed Concrete Industry LEEDclose-out.Reference GuideAfinalsectionofthedocumentThe document is organized into 11addresses environmental considerations insections that offer the best opportunities forusing ready mixed concrete with reference toachieving LEED Credits through the use ofplant waste water disposal, on-site washready mixed concrete. The term “readywatermixed concrete” and “concrete” are ngeably throughout this publicationand meant to describe concrete that isA handy checklist, “Potential LEEDdelivered to the project site in the plasticCredits for Ready Mixed Concrete,” is foundstate in concrete trucks. The 11 sections arein Appendix ies:“EnergyandAtmosphere,” “Materials and Resources,”4
USING READY MIXED CONCRETE TOaverageannualpost-developmenttotalsuspended solids (TSS) and 40% of theACHIEVE LEED-NC CREDITSSustainable Sites PREREQUISITE ANDaverageannualpost-developmenttotalphosphorous (TP) based on the averageCREDITSannual loadings from all storms less than orequal to the 2-year/24-hour storm. Do so byLEED Credit SS-C6.1 Stormwaterimplementing Best Management PracticesManagement - Rate and Quantity(BMPs) outlined in Ch. 4, Part 2 (UrbanGuidanceIntent: Limit disruption and pollution ofRunoff),natural water flows by managing stormwaterSpecifyingrunoff.Sources of Nonpoint Pollution in CoastaloftheUSEPA’sManagementMeasuresforWaters, Jan. 1993 (Document No. EPA-840-RequirementsIf existing imperviousness is less than orequal to 50%, implement a stormwaterB-93-001c) or the local government’s BMPdocument (whichever is more stringent).management plan that prevents the postdevelopment1.5year,24hourpeakdischarge rate from exceeding the predevelopment1.5year,24hourpeakdischarge rate;ORIf existing imperviousness is greater than50%, implement a stormwater managementplan that results in a 25% decrease in therate and quantity of stormwater runoff. LEEDwill also give credit for rainwater collectedand reused on-site.Example of uncontrolled water run-off.Summary of Concrete Applications andMaterials Relevant to the CreditsLEED includes Stormwater Managementand Treatment Credits to reduce the negativeLEED Credit SS-C6.2 Stormwatereffects of runoff created by development.Management - TreatmentIntent: Limit disruption of natural water flowsby eliminating stormwater runoff, nants.RequirementsConstruct a site stormwater treatmentsystem designed to remove 80% of theRoofs, sidewalks, parking lots, driveways,streetsandotherimpervioussurfacesprevent water from naturally infiltrating soil,filtering pollutants and recharging aquifers.As a result, large volumes of sheet runoffmustbecollected,concentrated,anddirected into waterways. These volumes ofstormwatercarrysedimentandother5
contaminants that compromise water quality.and recharge aquifers. Pervious paving isExpensivearecomprised of either ready mixed concrete,necessary to control the erosion and floodingasphalt, or precast pavers. Pervious concretethat occur when stormwater is concentratedconsists of specially formulated mixtures ofinfrastructureworksand released into waterways.Stormwater runoff picks up pollutantssuch as spilled oil, tire particles, detergents,pesticides, fertilizer, de-icing salt, llutantsotherarethendeposited into waterways with palitiessewageroutetreatmentfacilities, and when heavy storms cause flowrates to exceed treatment plant capacity,untreatedsewageisdischargedintoPervious concrete paving example –waterways.placing pervious screed.Concrete can be an important part ofstrategies to achieve these two credits: first,by controlling the rate and quantity ofstormwater runoff; and second by removingsome of the most important pollutants fromthe runoff.These conventional uses of concrete forstormwater management such as piping,collectionsystemsandwastewatertreatment are important, but are commonlyused and are well-documented. This reportwill concentrate on pervious pavement madefrom concrete, a very promising technologythat is rapidly gaining popularity throughoutthe United States.open-gradedcoarse aggregate, and water. It has enoughvoid space to allow rapid percolation ofliquids through the pavement.Theperviouspavementsurfaceistypically placed over a highly permeablelayer of open-graded gravel and crushedstone. Voids in the aggregate layers act as astorage reservoir for stormwater. A filterfabric may be placed beneath the gravel andstone layers to screen out fine soil particles.The amount of storage in the stone reservoirbeneath the pavement can be varied. If thesoil has low permeability, or is highlyreservoir to discharge excess stormwaterallowswatertopercolate to the ground, filter contaminants6uniform,pipes can be added near the top of thePervious Concrete Pavingpavingcement,vulnerable to freeze-thaw cycles, perforatedDESIGN ISSUESPerviousportlandafter the reservoir has been filled. Urban infillprojects or projects without adequate roomfor the required stone reservoir may not be
appropriate candidates for pervious paving.Pervious paving has many advantages inadditiontomeetingLEEDcreditenvironmental promotion function.Filteringbenefits that are still being discovered by theindustry.TreatingStormwaterwithPervious Concrete Pavingrequirements. It is a consistently improvingtechnology that shows great promise, withandPervious pavement pollutant removalmechanisms include absorption, straining,and microbiological decomposition in the soil.An estimate of pervious pavement pollutantremoval efficiency is provided by two long-MaintenanceThe advantages of pervious pavementcan only be realized if it is designed andmaintained to prevent clogging. To ensuresuccess, employ design strategies to helpprevent clogging. Grade site areas awayfrom paving to prevent the flow of dirt anddebris into pervious paving (alternatively,“pretreatment” borders can be added to filterout particles before they flow onto thepavement). Only employ pervious paving inappropriate areas under suitable conditions(see “Design Guidelines” below).Maintenance should include vacuumsweeping at least once per year (and asoften as four times per year if le, MD, and Prince William County,VA.Thesestudiesindicateremovalefficiencies of between 82% and 95% forsediment, 65% for total phosphorus, andbetween 80% and 85% of total nitrogen. TheRockville, MD, site also indicated highremoval rates for zinc, lead, and chemicaloxygen demand. There is some question ofhow closely these results reflect othersituations, but the treatment effectiveness ofproperly designed and maintained perviouspavement is not in doubt.Table 2. Effectiveness of porous pavementpollutant removal (Schueler, 1987)followed by high-pressure hosing to freepores in the top layer from clogging. ThePollutant Removal (%)pavement should be inspected several timesduringthefirstfewmonthsfollowinginstallation and annually thereafter. Annualinspections should take place after largestorms, when puddles will make any houldadjacentalsobeinspected.StudyPrince WilliamCounty, VARockville, MDTSSTPTNCOD Metals826580--9565858298–99Provide maintenance guidelines for thebuilding owner. Consider posted signage onsite to identify pervious pavement areas.These can also serve an educational andSomekeyfactors(otherthanmaintenance) that increase pollutant removal7
include a drainage time of at least 24 hours,and the use of clean-washed aggregate.Typically, the porous pavement system issized to treat a small event, called the “waterquality storm” (i.e., the largest storm that canbe treated for pollutant removal), which canrange from 0.5” to 1.5”.“Stormwater hot spots” are areas wherelanduseoractivitiesgeneratehighlycontaminated runoff, with concentrations ofPervious pavements allow for groundwaterpollutants in excess of those typically foundrecharging while also assisting with water pollutionin stormwater. Since pervious pavement isan infiltration practice, it should not be usedat stormwater hot spots due to the potentialfor ground water contamination. These areasinclude commercial nurseries, auto recyclefacilities, fueling stations, storage areas,marinas, outdoor container storage of liquids,removal.separation distances of at least 4’ betweenthe bottom of the structure and seasonal highground water levels. In theory, pretreatmentand treatment by the pervious paving shouldreduce the depth of soil above seasonal highground water levels.Another source lists the following criteria:hazardous materials generators (if containersare exposed to rainfall), vehicle service andmaintenanceareas,andvehicleand Soils need to have permeability between0.5” and 3.0” per hour. If this criterion isequipment washing/steam cleaning facilities.not met, a combination of an aggregateRecharging Ground Water Below Perviousbase and drainage pipes can be used toConcrete Pavingchannel the excess water to a holdingmedium.Pervious paving can be used either torechargegroundwater,ortostore The bottom of the stone reservoir shouldstormwater for later reuse (and/or diversionbe flat so that infiltrated runoff will beinto stormwater conveyance systems), orable to infiltrate through the entireboth. This section discusses its ground watersurface.recharge function. Porous pavement should be sited at leastSome data suggest that as much as 70%2’ to 5’ above the seasonally high groundto 80% of annual rainfall will go towardwater table, and at least 100’ away fromground water recharge (Gburek and Urban,drinking water wells.1980). These data will vary depending ondesign characteristics and underlying soils.Per the USEPA, systems that rely on soilabsorption require deep pervious soils at8Designs also require the inclusion ofdevices to convey to the storm drain systemexcess water from storms that exceed thedesign flow rate. One option is to use storm
drain inlets set slightly above the elevation ofto be compared to the costs of infrastructurethe pavement. This configuration would allowthat may be required by municipal or otherfor some ponding above the surface, butauthorities for which pervious paving is anwould bypass flows that are too large to beacceptable alternative (i.e. detention tanks).treated by the system, or that occur if theMaintenancesurface clogs.vacuuming of pervious paving, should alsocosts,suchasrequiredbe considered.Retention/Attenuation (or Tanked) SystemsThe gravel underlying the paving can beLimitationsofSeveral studies indicate that, with properstormwater, substituting for expensive ormaintenance, porous pavement can retain itsland-consumingstructurespermeability (e.g., Goforth et al., 1983;elsewhere on the property. This function ofGburek and Urban, 1980; Hossain andpervious paving incorporates base and sub-Scofield, 1991). Many pavement engineersbase storage in conjunction with standardand contractors lack expertise with thisdrainage infrastructure to provide a delayedtechnology. For infiltrating systems (the greatstormwater discharge. Retention systemsmajority of cases), the use of perviouscan also enable reuse of stormwater forpavement does create risk of ground watersome domestic purposes such as irrigation.contamination, depending on soil tionofmodifyingperviouspavement systems to function as reservoirsare (1) varying the amount of storage in thestone reservoir beneath the pavement and(2) adding perforated pipes near the top ofthe reservoir to discharge excess stormwaterafter the reservoir has been filled. Somemunicipalities have also added stormwaterreservoirs (in addition to stone reservoirs)beneath the pavement. These reservoirsshould be designed to accommodate runofffrom a design storm. For more information,see design criteria from the United Statesand aquifer susceptibility. Fuel may leak fromvehicles and toxic chemicals may leach fromasphalt and/or binder surface. spaving, are not designed to treat thesepollutants. Likewise, nitrates and chloridesmay continue to move through the soil waterpossiblysupplies.Therefore, until more scientific data isavailable, it is not advisable to constructporous pavement near ground water drinkingsupplies.Environmental Protection Agency Office ofBecause pervious paving is not in wideWater, Washington, D.C., document: EPAuse, special planning and expertise will be832-F-99-023, dated September 1999.necessary until it becomes routine. RetrofitBenefits and CostsAs with most stormwater runoff reductionmeasures, the initial incremental costs needmay not be possible in many cases withoutredesigning and rebuilding the sub-base forproper drainage. Anaerobic conditions may9
develop in underlying soils if the soils are The gravel sub-base under porousunabl
Concrete offers several opportunities for building projects to gain LEED points. EXECUTIVE SUMMARY Of all the green building design and construction evaluation programs in the Unites States, the United States Green Building Council’s (USGBC) LEED Rating System is the most widely a