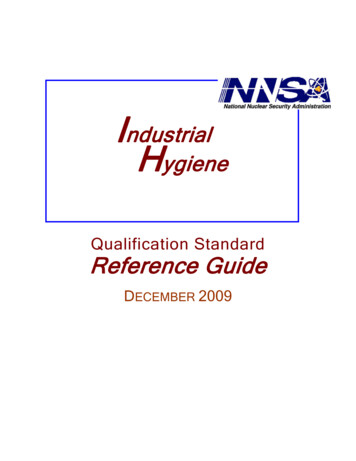
Transcription
IndustrialHygieneQualification StandardReference GuideDECEMBER 2009
This page is intentionally blank.
Table of ContentsLIST OF FIGURES . iiLIST OF TABLES . iiACRONYMS . ivPURPOSE. 1SCOPE . 1PREFACE. 1TECHNICAL COMPETENCIES. 31. Industrial hygiene personnel shall demonstrate an expert level knowledge of healthstressors that may be found in the workplace and the community. . 32. Industrial hygiene personnel shall demonstrate an expert level of knowledge and theability to anticipate and minimize exposure to health stressors during the planning anddesign phases of a work activity or from an operational description. . 123. Industrial hygiene personnel shall demonstrate a working level knowledge of study andobservation methods required to recognize and evaluate potential workplace healthstressors. 264. Industrial hygiene personnel shall demonstrate an expert level knowledge ofoccupational illnesses and their signs and symptoms and what their presence mayindicate about past and current workplace exposure. . 285. Industrial hygiene personnel shall demonstrate the ability to recognize potentialergonomic and office health hazards. . 436. Industrial hygiene personnel shall demonstrate a working level knowledge of datacollection plans for collecting data that accurately reflect exposure conditions. . 577. Industrial hygiene personnel shall demonstrate a working level knowledge of samplingtechniques. . 648. Industrial hygiene personnel shall demonstrate a working level knowledge of sampleanalysis, including the use of appropriate laboratory techniques. . 669. Industrial hygiene personnel shall demonstrate an expert level knowledge of the analysisand interpretation of sample results. . 7610. Industrial hygiene personnel shall demonstrate a working level knowledge of themethods used to educate people about how to protect themselves from health stressors. 8411. Industrial hygiene personnel shall demonstrate an expert level knowledge of personalprotective equipment (PPE) programs for controlling exposure, including their use andlimitations. . 8712. Industrial hygiene personnel shall demonstrate a working level knowledge of the designof engineering measures to control exposure. 9713. Industrial hygiene personnel shall demonstrate a working level knowledge of the designof administrative measures to control exposure or protect employees. . 11114. Industrial hygiene personnel shall demonstrate a working level knowledge of themethods used to promote effective communication and control of hazards. 11515. Industrial hygiene personnel shall demonstrate an expert level knowledge of industrialhygiene programs. 12116. Industrial hygiene personnel shall demonstrate a working level knowledge ofprofessional and ethical issues. . 12717. Industrial hygiene personnel shall demonstrate a familiarity level knowledge of theprincipal external committees, agencies, and associations relating to the field ofindustrial hygiene. 132i
Table of Contents18. Industrial hygiene personnel shall demonstrate the ability to evaluate the adequacy oflocal compliance or conformance with the following document sections:. 13819. Industrial hygiene personnel shall demonstrate the ability to determine the adequacy oflocal compliance or conformance with the industrial hygiene-related sections and/orrequirements of DOE Orders such as the following: . 14620. Industrial hygiene personnel shall demonstrate a working level knowledge of assessmentperformance, including assessment planning and the use of field observations, employeeinterviews, and document reviews in the assessment of industrial hygiene performance. 14921. Industrial hygiene personnel shall demonstrate the ability to prepare assessment reportsthat document assessment results, support assessment conclusions, and clearlycommunicate conclusions and recommendations for corrective action. . 14922. Industrial hygiene personnel shall demonstrate the ability to trend and analyze industrialhygiene-related information. 15023. Industrial hygiene personnel shall demonstrate a working level knowledge of theinterrelationship between quality assurance programs and industrial hygiene. 15024. Industrial hygiene personnel shall demonstrate the ability to apply recognized technicalpractices and guidance properly to DOE non-industrial or non-repetitive work activities. . 151Selected Bibliography and Suggested Reading . 152FiguresFigure 1. Areas of reach for a woman 5.5 feet tall.19Figure 2. Typical fields of vision at a manual workstation. Ideally, frequently usedcomponents and tools are placed in the area with 35 degrees on either side.20Figure 3. Based on AutoCAD, Bosch’s MASsoft package lets users quickly incorporateassemblies, 3-D models of humans, and workstation components into 2-D or 3-Ddrawings.22Figure 4. Single-handle tools with sleeve .44Figure 5. Single-handle tools for precision tasks.45Figure 6. Open and closed grip span.45Figure 7. Double-handle tools for precision tasks .45Figure 8. Tools with handles that are spring-loaded.46Figure 9. Tools without sharp edges .46Figure 10. Tools coated with soft material .46Figure 11. Tools with straight and bent handles .47Figure 12. Straight handles are better when force is applied vertically.47Figure 13. Tools that can be used with both hands.47Figure 14. Handle length longer than the widest part of your hand.47Figure 15. If the handle is too short, the end will press against the palm of your hand andmay cause an injury. .48Figure 16. Tools with a non-slip surface.48Figure 17. Typical process facility confinement zones.99TablesTable 1. Risk and precautions for level A laboratories .5ii
Table of ContentsTable 2. Permissible noise exposures.6iii
American Board of Industrial Hygieneair change effectivenessactual cubic feet per minuteAmerican Conference of Governmental Industrial HygienistsAmerican Industrial Hygiene AssociationAmerican National Standards InstituteAmerican Society of Heating, Refrigeration, and Air Conditioning Engineersair sampling instrumentsAmerican Society of Mechanical EngineersAmerican Society of Safety EngineersAmerican Society for Testing and Materialsbiological exposure indicesBureau of Labor Statisticsbiosafety levelComputerized Accident/Incident Reporting Systemchronic beryllium diseaseCenters for Disease Control and Preventioncubic feet per minuteCode of Federal Regulationscentral nervous systemchronic obstructive pulmonary diseasecerebrospinal fluidcarpal tunnel syndromedensity, g/cm3decibelA-weighted decibelU.S. Department of EnergyU.S. Department of TransportationU.S. Environmental Protection Agencyenhanced work planningFood and Agriculture OrganizationFactory Mutualfilter test facilityGlobally Harmonized Systemgigahertzglomerulonephritishigh-efficiency particulate air (filter)Health and Human Servicestritium oxideheating, ventilation, and air conditioningintegrated safety managementInternational Organization for Standardizationkilocalorieiv
zkilopascalliterlower confidence limitlaminar flow fume hoodslower limit of detectionLaboratory Quality Assurance Programsmeterminimum efficiency reporting valuemilligramminutemillilitermiles per hourmedical removal protectionmusculoskeletal disordersmaterial safety data sheetMine Safety and Health AdministrationNational Fire Protection AssociationNational Institutes of HealthNational Institute for Occupational Safety and HealthNational Institute of Standards and TechnologyNational Laboratory Certification ProgramNational Laboratory Training NetworknanometerNational Nuclear Security Administrationoutside airOffice of Management and BudgetOccurrence Reporting Binned Information Trending ToolOccurrence Reporting and Processing Systemoccupational safety and healthOccupational Safety and Health Administrationpersonal apparel assessmentpermissible exposure limitPublic Lawpersonal protective equipmentparts per millionparticle size efficientyperformance testingpolyvinyl chloridequality assurancequality product listradio frequencyrepetitive stress injuryv
BGTself-contained breathing apparatussite occupational medical directorspecies (plural or group)structures, systems, and componentsshort-term exposure limitsecond microgramtask/ambient conditioningthreshold limit valuetime-weighted averageunder-floor air distributionupper confidence limitUnderwriters Laboratorieswet bulb globe temperaturevi
PURPOSEThe purpose of this reference guide is to provide a document that contains the informationrequired for a Department of Energy (DOE)/National Nuclear Security Administration (NNSA)technical employee to successfully complete the Industrial Hygiene Functional AreaQualification Standard (FAQS). Information essential to meeting the qualification requirementsis provided; however, some competency statements require extensive knowledge or skilldevelopment. Reproducing all the required information for those statements in this document isnot practical. In those instances, references are included to guide the candidate to additionalresources.SCOPEThis reference guide addresses the competency statements in the November 2007 edition ofDOE-STD-1138-2007, Industrial Hygiene Functional Area Qualification Standard. Thequalification standard contains 24 competency statements.Please direct your questions or comments related to this document to the NNSA Learning andCareer Development Department.PREFACECompetency statements and supporting knowledge and/or skill statements from the qualificationstandard are shown in contrasting bold type, while the corresponding information associated witheach statement is provided below it.A comprehensive list of acronyms and abbreviations is found at the beginning of this document.It is recommended that the candidate review the list prior to proceeding with the competencies,as the acronyms and abbreviations may not be further defined within the text unless specialemphasis is required.The competencies and supporting knowledge, skill, and ability (KSA) statements are takendirectly from the FAQS. Most corrections to spelling, punctuation, and grammar have been madewithout remark, and all document-related titles, which variously appear in roman or italic type orset within quotation marks, have been changed to plain text, also mostly without remark.Capitalized terms are found as such in the qualification standard and remain so in this referenceguide. When they are needed for clarification, explanations are enclosed in brackets.Every effort has been made to provide the most current information and references available asof December 2009. However, the candidate is advised to verify the applicability of theinformation provided. It is recognized that some personnel may oversee facilities that utilizepredecessor documents to those identified. In those cases, such documents should be included inlocal qualification standards via the Technical Qualification Program.1
In the cases where information about an FAQS topic in a competency or KSA statement is notavailable in the newest edition of a standard (consensus or industry), an older version isreferenced. These references are noted in the text and in the bibliography.Only significant corrections to errors in the technical content of the discussion text sourcematerial are identified. Editorial changes that do not affect the technical content (e.g.,grammatical or spelling corrections, and changes to style) appear without remark.2
TECHNICAL COMPETENCIES1. Industrial hygiene personnel shall demonstrate an expert level knowledge of healthstressors that may be found in the workplace and the community.a. Discuss the following types of health stressors and provide examples of hazardsthat may be anticipated: Chemical Biological PhysicalChemicalThe following is taken from the National Safety Council, Fundamentals of IndustrialHygiene.The majority of occupational health hazards arise from inhaling chemical agents in the formof vapors, gases, dusts, fumes, and mists, or by skin contact with these materials. The degreeof risk of handling a given substance depends on the magnitude and duration of exposure.To recognize occupational factors or stresses, a health and safety professional must firstknow about the chemicals used as raw materials and the nature of the products and byproducts manufactured. This sometimes requires great effort. The required information canbe obtained from the material safety data sheet (MSDS) that must be supplied by thechemical manufacturer or importer for all hazardous materials under the Occupational Safetyand Health Administration (OSHA) hazard communication standard.Many industrial materials such as resins and polymers are relatively inert and nontoxic undernormal conditions of use, but when heated or machined, they may decompose to form highlytoxic by-products. Information about these hazardous products and by-products must also beincluded in the company’s hazard communication program.Breathing of some materials can irritate the upper respiratory tract or the terminal passages ofthe lungs and the air sacs, depending on the solubility of the material. Contact of irritantswith the skin surface can produce various kinds of dermatitis.The presence of excessive amount of biologically inert gases can dilute the atmosphericoxygen below the level required to maintain the normal blood saturation value for oxygenand disturb cellular processes. Other gases and vapors can prevent the blood from carryingoxygen to the tissues or interfere with its transfer from the blood to the tissue, thus producingchemical asphyxia or suffocation. Carbon monoxide and hydrogen cyanide are examples ofchemical asphyxiants.Some substances may affect the central nervous system and brain to produce narcosis oranesthesia. In varying degrees, many solvents have these effects. Substances are oftenclassified, according to the major reaction they produce, as asphyxiants, systemic toxins,pneumoconiosis-producing agents, carcinogens, and irritant gases.3
BiologicalBiological stressors represent a distinct category of hazards. Unlike chemical or physicalhazards, biological stressors (1) grow, reproduce, and die, (2) disperse both actively andpassively, (3) interact with other biological populations in the ecosystem, and (4) evolve.Therefore, biological stressors as diverse as human pathogens (e.g., Salmonella and Bacillusanthracis), plant and animal pathogens (e.g., Asian soybean rust and avian influenza virus),and invasive species (e.g., Mediterranean fruit fly and kudzu) share many common features.The distinction between risk assessment for biological stressors and chemical risk assessmentmay be overstated, however, and a number of parallels can be drawn. For example, pathogeninactivation is analogous to chemical sequestration, and a population of invasive cells in thebody is analogous to a population of invasive species in the environment. To date, however,the practice of risk assessment for biological stressors has not adopted conventions assimplifying assumptions to the extent that they are generally applied in the more mature fieldof chemical risk assessment. As with risk assessment in other fields, managing the tensionbetween complexity and utility is likely to remain an ongoing challenge for the emergingfield of risk assessment for biological stressors.Title 29 CFR 1910.1030 defines bloodborne pathogens as pathogenic microorganisms thatare present in human blood and can cause disease in humans. These pathogens include, butare not limited to, hepatitis B virus and human immunodeficiency virus.Each employer having an employee(s) with occupational exposure shall establish a writtenexposure control plan designed to eliminate or minimize employee exposure. Occupationalexposure means reasonably anticipated skin, eye, mucous membrane, or parenteral contactwith blood or other potentially infectious materials that may result from the performance ofan employee’s duties. Each employer who has an employee(s) with occupational exposureshall prepare an exposure determination. Engineering and work practice controls shall beused to eliminate or minimize employee exposure. Where occupational exposure remainsafter institution of these controls, personal protective equipment (PPE) shall also be used.When there is occupational exposure, the employer shall provide, at no cost to the employee,appropriate PPE such as, but not limited to, gloves, gowns, and laboratory coats; face shields/masks and eye protection; and mouthpieces, resuscitation bags, pocket masks, or otherventilation devices. PPE will be considered appropriate only if it does not permit blood orother potentially infectious materials to pass through or to reach the employee’s workclothes, street clothes, undergarments, skin, eyes, mouth, or other mucous membranes undernormal conditions of use and for the duration of time the protective equipment will be used.The risk and precautions for level A laboratories are described by agent in table 1.4
Table 1. Risk and precautions for level A laboratoriesAgentBSLSpecimenExposure RiskRecommended Precautions forLevel A LaboratoriesSpecimen CultureHandling HandlingBacillusanthracis22Blood, skin lesionexudates, CSF,pleural fluidsputum, and rarelyurine and feces.Brucella 23Yersiniapestis422Blood, bonemarrow, CSF,tissue, semen andoccasionally urine.Toxin may bepresent in foodspecimens, clinicalmaterial (serum,gastric and feces),and environmentalsamples (soil,surface water).Toxin is extremelypoisonous.Skin lesion exdates,respiratorysecretions, CSF,blood, and urine.Tissues frominfected animals andfluids from infectedarthropods.Bubo fluid, blood,sputum, CSF, feces,and urine.Smallpox544VHF644Lesion fluid orcrusts, respiratorysecretions, or tissue.Blood, urine,respiratorysecretions, orsemen, and tissue.BSL2: Activitiesinvolving clinicalmaterial collectionand diagnosticquantities ofinfectious cultures.BSL2: Activitieslimited to collection,transport and platingof clinical material.BSL2: Activitieswith materialsknown or potentiallycontaining toxinmust be handled in abiological safetycabinet with a labcoat, disposablesurgical gloves, anda face shield.BLS2: Activitieslimited to collection,transport and platingof clinical material.BSL3: Activitieswith high potentialfor aerosol or dropletproduction.BSL2: Activitiesinvolving clinicalmaterial collectionand diagnosticquantities ofinfectious cultures.BSL4: Specimencollection/transportBSL3: Activitieswith high potentialfor aerosol or dropletproduction.BSL3: All activitiesinvolvingmanipulations ofcultures.BSL3: Activitieswith high potentialfor aerosol or dropletproduction.BSL3: All activitiesinvolvingmanipulations ofcultures.BSL4: Specimencollection/transportSource: CDC Microbiology Biosafety1.Laboratory-acquired brucellosis has occurred by sniffing cultures; aerosols generated by centrifugation;mouth pipetting; accidental parenteral inoculations; sprays into eyes, nose, and mouth; and by directcontact with clinical specimens.5
2.3.4.5.6.Exposure to toxin is the primary laboratory hazard since absorption can occur with direct contact with skin,eyes, or mucous membranes, including the respiratory tract. The toxic can be neutralized by 0.1 M sodiumhydroxide. C. botulinum is inactivated by 1:10 dilution of household bleach. Contact time is 20 minutes. Ifmaterial contains toxin and organisms, the spill must be sequentially treated with bleach and sodiumhydroxide for a total contact time of 40 minutes.Laboratory-acquired tularemia infection has been more commonly associated with cultures than withclinical materials/animals. Direct skin/mucous membrane contact with cultures; parenteral inoculation;ingestion; and aerosol exposure have resulted in infection.Special care should be taken to avoid the generation of aerosols.Ingestion, parenteral inoculation, and droplet or aerosol exposure of mucous membranes or broken skinwith infectious fluids or tissues are the primary hazards to laboratorians.Respiratory exposure to infections aerosols, mucous membrane exposure to infectious droplets, andaccidental parenteral inoculation are the primary hazards to laboratorians.PhysicalTitle 29 CFR 1910.95 states that when employees are subjected to sound levels exceedingthose listed in table 2, below, feasible administrative or engineering controls shall be utilized.If such controls fail to reduce sound levels to permissible limits as specified in table 2, PPEshall be provided and used to reduce sound levels so that they fall within the levels of thetable.Table 2. Permissible noise exposuresDuration per day(hours)Sound level, dBASlow Response864321½1½¼ or less90929597100102105110115Source: 29 CFR 1910.195The employer shall administer a continuing, effective hearing conservation programwhenever employee noise exposures equal or exceed an eight-hour time-weighted averagesound level of 85 decibels measured on the A scale (slow response) or, equivalently, a doseof 50 percent.According to 29 CFR 1926.54, employees working in areas where there exists a potentialexposure to direct or reflected laser light greater than 0.005 watts (5 milliwatts) shall beprovided with anti-laser eye protection devices. Areas in which lasers are used shall beposted with standard laser warning placards. Employees whose occupation or assignmentrequires exposure to laser beams shall be furnished suitable laser safety goggles which will6
protect for the specific wavelength of the laser and be of optical density adequate for theenergy involved.Lasers are classified in categories 1 (safe) to 4 (dangerous). Most precautions apply to Class3b and 4 lasers. The American Conference of Governmental Industrial Hygienists (ACGIH)provides threshold limit values (TLVs) for lasers, while ANSI Z136.1, American NationalStandard for the Safe Use of Lasers, provides more detailed guidance on acceptable practicesto provide safety. DOE O 420.2B, Safety of Accelerator Facilities, states that although eyeinjury from nonionizing radiation is generally the primary hazard, laser systems can presentelectrical and chemical hazards as well. In addition to the nonionizing radiation hazard,electrical hazards are associated with the high-voltage power supplies used in many lasersystems. In particular, Class 4 lasers often use large power supplies that carry an appreciablerisk of electrocution, especially in maintenance and adjustment procedures. Chemical hazardscan be associated with halogen and dye lasers, as well as with radiation decomposition.Electromagnetic radiation is restricted to that portion of the spectrum commonly defined asthe radio frequency (RF) region, which includes the microwave frequency region. DOEG 420.2-1, Accelerator Facility Safety Implementation Guide for DOE O 420.2B, Safety ofAccelerator Facilities, states that to avoid exposure of persons to unacceptable levels of RFfields, engineered control measures, such as shielding, prevention of wave guide leakage,enclosures, interlocks preventing accidental energizing of circuits, and dummy loadterminations, should be given first consideration over any use of PPE. Where exposure inexcess of the limits is possible, RF leakage tests should be conducted when the system is firstoperated and after modifications that might result in changes to the leakage. Area RFmonitors are appropriate when RF energy can be expected in occupied areas. The ACGIHspecifies guidelines for personnel protection in the form of TLVs. Use of the ACGIHguidelines in their most current form for RF and microwave fields is required as part ofworker protection management for DOE contractor employees.b. Describe how the following sources of information can be used to assist in theanticipation of health stressors: Standards Regulations Standard texts and references Material safety data sheet (MSDS) of materials in site inventoriesStandardsThe following is taken from DOE G 252.1-1.As defined in Public Law (PL) 104-113, technical standards are “performance-based ordesign-specific technical specifications and related management system practices” that aredeveloped and adopted by voluntary consensus standards bodies. The Office of Managementand Budget (OMB), Circular No. A-119 expands the PL 104-113 definition of standards toinclude (1) common and repeated use of rules, conditions, guidelines, or characteristics forproducts or related processes and production methods, and related management systemspractices; and (2) the definition of terms; classification of components; delineation ofprocedures; specification of dimensions, materials, performance, designs, or operations;7
measurement of quality and quantity in describing materials, processes, products, systems,services, or practices; test methods and sampling procedures; or descriptions of fit andmeasurements of size or strength.DOE describes technical standards in a manner similar to OMB A-119; that is, as aprescribed set of criteria concerned with classification of components; delineation ofprocedures; specification of materials, products, performance, design, or operations; anddefinitions of terms or measurements of quality and quantity in describing materials,products, systems, services, or practices.The most common topics for DOE technical standards are related to nuclear technology andenvironment, safety, and health aspects of nuclear technology, such as design, construction,maintenance, operational standards, performance, management systems, component andfacility classification, common practices, and technical specifications. Still others includedecommissioning, information management, training, standardized procedures, projectmanagement, services, and product specifications.RegulationsThe following is taken from the U.S. Department of Labor, OSHA, Informational Booklet onIndustrial Hygiene.Under the Occupational Safety
23. Industrial hygiene personnel shall demonstrate a working level knowledge of the interrelationship between quality assurance programs and industrial hygiene. 150 24. Industrial hygiene personnel sh