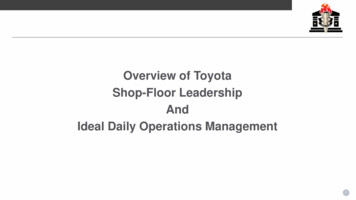
Transcription
Overview of ToyotaShop-Floor LeadershipAndIdeal Daily Operations Management1
What if?If, starting today, you could only hire yourfuture leaders by promoting from within?What if all future senior and executiveleaders had to come only from an entryassociate or supervisor?How would that change your approach toLeader and People development?It would fundamentally changeEVERYTHING!Your very management system could nolonger be just about the numbers couldit?2
Floor Management Development SystemManagement RolesMANAGEMENTPROCESS RESULTPROCESSACTIVITY ACTIONEXECUTIVE MANAGEMENTSENIOR MANAGEROPERATIONS MANAGERAREA MANAGERPROCESS MANAGERPROCESS MEMBER3
Understanding FMDS – Floor Management Development SystemFMDS is a Comprehensive System that aligns Floor Management and Human ResourceDevelopment activities to achieve Company Targets and Support the Succession Pipeline. FMDS ensures foundations skills are in place for Ideal Daily Work, and Aligns Daily Shop-Floor Activities with Hoshin goals and objectives. FMDS Visualizes Shop-Floor Management and Leader Development through: Visualization of Gap to Standard Promote Two-way Communication Defines and Develops Roles and Responsibilities for all members Supports Toyota’s On-the-Job Development for all membersFMDS is ingrains the Toyota Way Culture into the Managing Structures of FMDS4
FMDS as a People and Leader PlatformManagers and Assistant Managers: Quickly see how the groups are performing Coach Group and Team Leaders in the BusinessLeadership through Hoshin Support Group Leader activity with necessary resources Strengthen the groups’ commitment and pride as theystrive to achieve shared goalsGroup Leaders and Supervisors: Focus their management efforts and problem solvingactivities Play a key role in developing Team Leaders and TeamMembers Less reactive and more proactive Visually show the need for Support5
FMDS as a People and Leader PlatformTeam Leaders Help their teams improve skill by working with teammembers to solve team problems Develop their own skills as a coach and leader whilethey manage daily activities through the team leaderprocess and 3 Pillar ManagementTeam Members: Can see Group/Area/Shift performance Understand how important their job is to theCompany’s success Have access to information to help solve problems Improve team member knowledge and skill level Can see how their job impacts Company Success6
Leadership, Hoshin, FMDS and Three Pillar ManagementQuote:“From a Leadership perspective, we use our FMDS and Three Pillar Boardsand I try to be a leader from that perspective - of always challenging ourGroup Leaders and Assistant Managers to think of the next level.How do we get to the next level? How do we achieve the things that we do?The way I do that, I try to provide the vision for them and let them create theroad map.Jeff Hurst, Manager, Powertrain, TMMK7
Overview of Toyota Hoshin ManagementConnection toFloor Management Development System8
FMDS - A Leadership Development and Management Tool FMDS Uses Hoshin to Set Direction linked to the Company Hoshin Drives Activity through Problem Solving (Toyota Business Practice ) and Kaizen Engages all Levels of the team through Roll Specific Actions9
FMDS and the Five Mission of Shop-Floor ManagementThe Management ActivitiesOf the Shop-Floor GroupTHE FIVE MAIN MISSIONS OFFMDS SHOP-FLOOR ceDevelopmentActions of the Shop-floor Leadership Group areresponsible for the safety of members and ensuringthe quality, volume, cost, and delivery of the productcreated as well as the development of all members10
FMDS Management Review CadenceThe Management ActivitiesOf the Shop-Floor GroupTHE FIVE MAIN MISSIONS OFFMDS SHOP-FLOOR LEADERSHIPSafetyQualityProductivityTheWeekOf theMonthThe2nd WeekOf theMonthThe3rd WeekOf theMonth1stCostHumanResourceDevelopmentTheWeekof theMonthEveryOtherFriday4th5S is the focus if there is a 5th Week in the Month11
FMDS Board Layout StandardsFMDS REVIEWHoshinAnd theFive nCostHoshinHumanResourceDevelopmentHoshinPLANMain KPI Main KPI are derived from Sub-KPI’s one Management Level UpMain KPI’s Directly linked to the Annual HoshinVisualize Monthly and Historical TrendClear Target is Specified and VisualColor Coded/Symbol judgement of Current StatusPLANSub-KPI’s& ProcessSub-KPI’s Breakdown of Main KPI to Pro-active and Reactive Sub-KPI’sClear Visual Targets and Visual ManagementSpikes annotated using handwritten “call-out bubbles”Measures daily activity sub-KPI’s to the Process level to support Sub-KPIsPLANProcessActivities Evidence of GTS-PDCA Process and ThinkingBreakdown of Gaps (Issues) that effect Sub-KPI TrendsHandwritten Concrete Actions to tackle GapsTimetable and Status of ProgressOwnership and TeamworkDO Shows Results tracking from ActivitiesHandwritten using QC Tools/ChartsLogical Connection to Sub-KPI’sDid we achieve the target? What was the Result? Toyota Business Practice (Problem Solving Process) supporting documentsHistory of Process activities and Results (greater than 90 Days)A3, A3, Kaizen Sheet, etc.Used to share lessons learned and reflection as part of YokotenResultsTrackingHistoryBindersACTCHECK12
Hoshin Kanri Connected to the Genba with FMDSToyota Hoshin ManagementBy Shift throughFloor Management & Development System13
14
Who Attends the FMDS Five Mission Review?All Support Groups attend the FMDS Review, Including: Section or Department Manager* Assistant Manager All Plant Group Leaders/Supervisors Mission Leader (e.g. Safety Team Leader on Safety Review) Process Engineering Quality Engineering Occupational Safety Human Resource Representative for Group15
FMDS, Toyota Business Practice and Leader DevelopmentToyota Business Practice (TBP – 8 Step Problem Solving A3 Process) and Quality Circle Leadership andParticipation are activity drivers for Leader and People DevelopmentQuality Circle Leadership is the Original Leader development platform of ToyotaProduction Team Leaders must Lead at least one TBP or Quality Circle Activity per yearThe Group FMDS Board is the Source for TBP, Safety Circle, Quality Circle or Kaizen Circle Activity for TeamLeaders to LeadSome Focus activities may be the focus of a Manager Led or Cross Functional Problem Solving Activity (akaJishuken)16
FMDS, Three Pillar Toyota Business Practiceand Leadership Development“When I think of FMDS and Three Pillar, it’s REALY TBP (Toyota BusinessPractice). It’s all about how you get from a large, vague problem to pinpointthe exact issue that you can work on.When my Team Leaders are looking for a TBP to work on, I say ‘Let’s Go tothe FMDS Board.”– Jeremiah Duncan, V6 Assembly Group Leader, TMMK Powertrain17
The Role of the Production Group LeaderAndFloor Management Development System18
Supervisor Ideal Daily Management Process The Group Leader Role is supported by The GroupLeader Management Process (GLMP). The GLMP Process is made up of supportingmanagement, Leadership and People DevelopmentRoutines is Cycled before during and after the Work Shift.PDCA and Communicate (Observe to verify and adjust)Ensure ons forIdealProductionManage lityFollow-up Cycle (Observe to verify and adjust)19
Understanding Visual Management BoardsTop portion is daily routines andchecks aligned with shop-floorleadership roles.Problem activity is connect toGroup Leader FMDS BoardProactiveDailyActivitiesLeader RoutinesAligned with RoleAll problems that are foundthrough: Weak Point Management auditsCountermeasures forPrevious andCurrent month operator suggestion, scrap or rework events, premature tool failureAre logged on one set of sheetsdivided up by the 4Ms – called“Problem Registration ntsProblemActivity &TrackingProblemRegistrationSystem &SupportDocuments20
Toyota’s KPI Pyramid – Visualizing Leading Indicators21
Hoshin Main KPI’sStart with the Hoshin Statement – Quantitative andQualitative High Level Vision of the Dept orSection.Main KPI’s for the FMDS Board are High LevelIndicators deemed critical and Targets are derivedfrom the Department or Section HoshinFMDS Safety Hoshin Example: Respect our community andcreate a family-like environment through ensuring mental,emotional, physical and environmental Safety.FY 2018 Targets: Main KPI’sLost Time Accidents: 0%Note:Safetyis aFocusRecordables: 0%T/M Safety Dojo Training: 100%100% T/M Completion of Find and Fix Safety Kaizen: 1 per monthStimulate Team-member (T/M) involvement to support eyes for safetyand problem solving:1.Safety Culture: Create a culture for Safety and Health ThroughLeadership, Management and T/M engagement2.Safety System: Enhance safety performance throughimplementation of Safety Best Practices3.Environmental Management: Reduce non-Safe waste throughprocess kaizen and segregation22
Sub-KPI’s and Process Sub-KPI’sFMDS Sub-KPI’s are Proactive and ReactiveMeasures that can be measured to show potentialimprovement to achieve Main KPI.Sub-KPI’s are indicators that will support the overallachievement of the Main KPI and are Fact DrivenSub-KPI’s may change quarterly and may be Direct(reactive) or Indirect (proactive)Process Sub-KPI’s breakdown to process levelSub-KPI’s are tracked by area by shift. Safety Sub-KPI Example: Acute Injuries Incidents Ergonomic Incidents Behavior-based Near Misses Process Related Workplace Organization and Layout Related Eyes for Safety Dojo Training Completion23
Process Activity ScheduleFMDS Process Activities are activities at theProcess Level intended to Improve the Sub-KPI’sthrough Countermeasure implementation as aresult of Toyota Business Practice 8 Step ProblemSolving Process.There are 2 Measures of daily process activity:1. Completion2. OutcomeProcess Activity is measured by completionstatus and is typically displayed on the activityboard.Just as there are 2 measurements of Activitiesthere are also 2 types of Activities:1. Direct: Results from problem solving a Gap to astandard, defined cause and effect, quantifiableresults, and easily linked to Sub and Main KPI’s2. Indirect Activity: Results from a broad ProblemSolving activity with no specific Gap; generallyKaizen or effort to improve overall environment orculture24
Process Results TrackingFMDS Process KPI’s are the Quantifiable resultsindicators of the process level activity intended toimprove the Sub-KPI’sThe Process KPI is the measure of Outcomecompared to the target set for the ActivityProcess Results KPI answers the question: How will you Check? How often will you Check? How long will you Check? (e.g. 90 days) Did you achieve the desired outcome Do you understand both success and failure What did you learn?25
Now, It’s YourTurn26
FMDS Dojo Audit Dojo is used to train andrefresher – in a “hands-on” waythe leadership and managementconcepts of The Toyota Way,TPS, FMDS, Point Control, and3 Pillar Management to allLeaders Once per Quarter, the FMDSDojo team will audit FMDSBoards and ManagementBoards for Gaps. This Gaps are shared withGroups for Improvements Groups can earn Bronze, Silver,or Gold Status as they maturetheir FMDS and 3 PillarManagement Boards andProcess27
FMDS is a Comprehensive System that aligns Floor Management and Human Resource Development activities to achieve Company Targets and Support the Succession Pipeline. FMDS ensures foundations skills are in place for Ideal Daily Work, and Aligns Daily