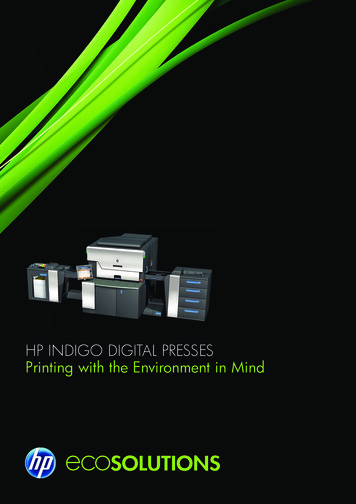
Transcription
HP INDIGO DIGITAL PRESSESPrinting with the Environment in Mind
Executive SummaryHP environmental commitmentHP has been a leader in environmental stewardshipfor decades, and efforts to innovate and design forthe environment represent a long-standing commitmentrather than a recent trend.In 2009, HP topped Newsweek’s first Green Rankingsof the 500 largest US companies(1) based on researchand analysis of the company’s actual environmentalperformance and reputation. HP has also been rankedfirst on the 100 Best Corporate Citizens List for 2010compiled by Corporate Responsibility Magazine.Today, under the HP Eco-solutions programme, HPtakes a comprehensive approach to designing productswith the environment in mind. This begins with carefulplanning in their design and extends to the materialsused in the manufacturing process, right down tothe product’s ”afterlife,” where many convenient andresponsible recycling options for equipment andprinting consumables are offered.HP Indigo presses and the environmentHP Indigo presses feature a range of technologiesthat reduce paper waste, energy usage andconsumables consumption, and assist print serviceproviders (PSPs) in achieving environmental andhuman health-related standards and certifications.Furthermore, there is a growing infrastructure fortake-back and reuse or recycling of consumables,and even the presses themselves.For PSPs, taking a more sustainable approach toprinting is increasingly recognised not just as goodpractice, but as good business. Selecting the rightprinting solution can play an important role in helpinga PSP improve the environmental profile ofits operations and of its printed output.These developments, and the very nature of digitalon-demand printing – that enables the printing ofjust what is needed, when and where it is required –can help PSPs and their print-buying customers meettheir own sustainability objectives.
A history of global citizenshipFor more than fifty years, environmental responsibilityhas been part of HP’s corporate culture.With a long-established track record for environmentalawareness and action, HP strives to integrate globalcitizenship practices into core business functionsbacked by public reporting and strong performance.Global Citizenship at HP encompasses corporateaccountability and governance, environmentalresponsibility and a commitment to communityinvestment and involvement. HP has rigorousprocesses in place to ensure its own compliance toestablished standards of responsible manufacturing,and has been widely acknowledged for its efforts.HP topped Newsweek’s first Green Rankings of the500 largest US companies based on research andanalysis of the company’s actual environmentalperformance and reputation. HP has also been rankedfirst on the 100 Best Corporate Citizens List for 2010compiled by Corporate Responsibility Magazine.HP Eco-solutions for printingHP places considerable focus on the environmentalprofile of its own operations and supply chain andis committed to being the most environmentallyresponsible IT company in terms of energy efficiency,resource conservation and end-of-life take-back andrecycling programmes.HP also designs its products to strict ‘Design forEnvironment’ criteria with an emphasis placed onhelping customers reduce the environmental impact oftheir printing, be it through reduced wastage of mediaor consumables, reduced consumption of energy orthrough programmes to take-back printing hardwareand used consumables, often for recycling or reuse.Responsible manufacturing for HP Indigopresses and consumablesHP Indigo is committed to conducting its business inan environmentally responsible manner and aims forcontinual improvement in the environmental profile ofits operations. Examples of this commitment include: All manufacturing facilities are ISO 14001 certified HP ElectroInk manufacturing site in Singapore iscertified as a Sony Green Partner The energy required to manufacture each inkcartridge has been reduced by18 percent between2008 and 2009 A 430m2 solar panel array provides energy at theink manufacturing plant in Kiryat Gat, IsraelHP Indigo environmental advances1993 – Starting from the first model, all HP Indigo presses incorporate a system to capture andcondense imaging oil vapour into a liquid1997 – Press reconditionings begin, significantly extending press lifetime2006 – Introduction of water-based primers as a suitable alternative to solvent-based ones– Dedicated press reconditioning line established2007 – The HP Indigo press 5500 includes an on-press oil recycling system that reduces the overalluse of imaging oil by 50 percent2008 – The HP Indigo 7000 Digital Press requires up to 30 percent less energy per printed pagethan its predecessor2009 – The HP Indigo WS6000 Digital Press is the first industrial digital press with an oil recyclingsystem. Binary Ink Developer take-back and parts re-use programme initiated2010 – The HP Indigo 7500 Digital Press improved on-press oil recycling system designed toeliminate the need for additional imaging oil.(2)– The HP Indigo 7500 Digital Press requires up to10 percent less energy per printed pagethan the HP Indigo 7000 Digital Press(3)
Going green - good business; good practiceToday’s print buyers are making increasinglysophisticated demands of the PSPs with which theywork. These regard both the environmental profileof the prints that they purchase and the processesand technologies used to produce them. Often thecompanies they represent – especially internationalbrands – may have established their own formalprint buying criteria. Frequently, these cite relevant,respected environmental certifications such as ForestryStewardship Council (FSC) chain-of-custody certificationfor paper or, the Nordic Ecolabel for the PSPthemselves.For a PSP, being able to demonstrate that prints of acomparable price and quality to those from competitorshave a better environmental profile can be a powerfulpoint of differentiation and can help them to secureadditional business.In addition, taking measures to reduce media wastage,cut energy bills, bring down waste disposal chargesand address other environment-related costs can addup to significant savings.Leaders and laggards“The leading green printers are stepping upto these (green) practices pro-actively, andgaining market position as a result. Eventually,however, all printers will have to take up manyof these green practices, whether because oflegislative requirements or customer demand.The laggards will have to bear all of this cost,but without any of the marketing benefit.”Sustainable Print in A Dynamic Global Market:What Going Green Means, Pira, 2009Selecting the right printing solution can play animportant role in helping a PSP to improve theenvironmental profile of its operations and of itsprinted output.Furthermore, taking a more sustainable approach toprinting can boost employee engagement and helpto prepare for future legislation.The improved on-press oil recycling system of the HPIndigo 7500 Digital Press is designed to eliminatethe need for additional imaging oil.(4)Vapour HoodInk AdditivesFor Special Colours(e.g., spot colours)
Perception of the printing industry’s carbonfootprintLowering the carbon footprint with digitalprintingHP conducted an analysis of the carbon footprint ofthe world printing industry for its presentation to theIEEE International Symposium on Sustainable Systemsand Technology, 2009.(5)With digital printing, no plates need to be prepared,no chemical processing or disposal is required, andonce a simple pre-flight has been carried out on thedigital files, printing can begin – with the first copybeing saleable. Colour and register are immediatelyachieved, saving potentially significant quantities ofpaper.(9)The global carbon footprint for printing (excludingpackaging) for 2020 was calculated as either 370 or850 million tonnes of CO2e(6), based on two differentmethodologies for calculation. While paper accountsfor about 70 percent of those totals, moving fromanalogue to digital printing can produce a variety ofbenefits both in terms of environmental impact andbusiness efficiency because of the significant papersavings made in make-ready and in printing onlywhat is required.Today, about 88 percent of print is producedby conventional, analogue methods (offset litho,flexography, gravure, letterpress, screen, etc.),(7)but the advantages of digital printing, in terms ofboth environmental impact and good business, areincreasingly compelling.Conventional printing has been based on longruns and “unit cost,” models. While superficiallyan efficient model, even today, after majorimprovements in technologies for plate-making,consumables consumption and control ofhazardous materials, the legacy “unit cost”model still dominates. This model, which promotesincreased print volumes because of the lower“unit cost” leads to printing more copies than areneeded: increased shipping and storage costs,and, ultimately, increased waste disposal costs.For example, a survey of the US book industry(8)showed that 25 percent of books are returnedunsold. Similar waste occurs in other areas of print.Set-up and make-ready is another leading factorin reducing profitability and generating waste. Inaddition to the environmental impact of plate-making,make-ready, registration, colour adjustment, etc., canrequire hundreds of sheets before the first page ofusable output.HP Indigo 7500 Digital Press’s recycling systemfurther reduces oil consumptionThe HP Indigo press 5500 was the first to includean on-press imaging oil recycling system. During theprinting process, oil is separated from the image byevaporation. The oil vapour is drawn into a coolerwhere it condenses, along with water from theambient air.The oil recycling system separates the oil from thewater. The oil is pumped into the imaging oil tankand combined with ink additives (if needed). Therecycled oil is then fed back into the press and isready for use in the printing process, reducingimaging oil consumed by approximately 50 percent.The water generated during the separation processis normally clean enough to qualify for disposal viacustomers’ facility drainage systems.A similar system is also featured on the new seriespresses: The HP Indigo 7000 Digital Press, the HPIndigo WS6000 Digital Press and the HP IndigoW7200 Digital Press are equipped with recyclingsystems.The new HP Indigo 7500 Digital Press features amore advanced version system that is still moreefficient and eliminates the need to add imagingoil to the press.(10)
HP Indigo and HP Eco-solutionsEnergy EfficiencyHP Indigo presses reduce environmental impact onthree different levels compared to conventional printing:digital on-demand printing, sustainable design andenergy efficiency. HP Indigo 7500 Digital Press uses up to 10percent less energy per printed page than itspredecessor(17)Digital on-demand printing Reduce wasted prints by printing only what isneeded, when and where it’s needed Greatly reduced set-up and changeoverwaste versus analogueSustainable design HP ElectroInk meets: The chemical requirements of the NordicEcolabel for printing companies In the USA: HP ElectroInk(11) complies with theFederal Food Drug and Cosmetic Act 21 U.S.C201 (FFDCA) requirements for printing onthe non-contact side of certain food packagingmaterials.(12) In the EU: HP ElectroInk complies withArticle 3 of the EU Framework Regulation Nr.1935/2004 for printing on the non-contact sideof certain food packaging materials.(13) HP ElectroInk is free from: HAPs(14) Particulate matter emissions Materials subject to California Proposition 65 Lead, lead compounds or phthalates as ingredients.Laboratory tests indicate that the inks meet mostrequirements of US CPSIA.(15) HP Indigo prints are deinkable and recyclableRecognising the environmental benefits ofdigital printingLocal and national governments are coming toappreciate the contribution to environmentalimpact that digital printing can make.The California Best Practices Manual - PrintingServices(18) states:Digital Printing“High-speed digital printing is an excellentalternative to the traditional lithographic*printing process. The digital printing processproduces a high-quality copy on the veryfirst page, thus eliminating paper waste.Lithographic presses have a higher amount ofwaste paper and chemical usage as the printedpress page is brought up to a usable quality.Lithographic printing is more affordable whenprinting large quantities of materials, suchas voter guides, driving handbooks, and taxbooklets.“Digital printing is also beneficial in givingon-demand publishing opportunities. Ondemand printing eliminates the need to storeand inventory larger quantities of printedforms, brochures, directories and publications.Additional quantities can be produced“on-demand” when needed. On-demandprinting works particularly well when printingdocuments that need frequent updating or arealso available on your office’s Web site. Starting with the HP Indigo press 5500, all newgeneration presses have a built-in Imaging oilrecycling technology that reduces consumptionby approximately 50 percent“Digital printing also may provide for regionaldistributed printing, thereby saving shippingcosts and reducing the demand for packagingmaterials. Large selection of media with environmentalcredentials* Lithography is a printing process based onthe chemical law that fatty oily inks do not mixwith water. It is usually referred to as offset.” Binary Ink Developer take-back and parts reuseprogramme(16)
The Dutch Ministry of Housing, SpatialPlanning and the Environment advocatesdigital printing:“Opt for digital printing instead of offsetprintingIn actual practice, financial and qualitativefactors play an important role in consideringwhether a purchaser opts for digital printing oroffset printing. From a sustainability perspectivehowever, the sources consulted by Agency NLindicate that digital printing is to be preferredover offset print technology. . . .”(19)Print recyclability, take-back and recycling,energy efficiencyHP operates sustainability initiatives for HP Indigopresses that address key areas of environmentalconcern in the printing industry. Continuing researchand development and work with internationalorganisations on print recyclability, take-back andrecycling programmes for consumables and hardware, and press re-manufacturing are all part of HP’ssustainability activities.Print recyclability and deinkingDeinking is a key initial step in paper recyclingwhere ink is separated from the fibres. The deinkingefficiency is evaluated by measuring the residual inkspecks in the deinked and processed pulp in terms ofsquare millimetre per square metre. Brightness is alsomeasured and compared to a target brightness andpurity of the resultant un-printed recycled paper.HP, in conjunction with leading paper researchinstitutes such as Centre Technique du Papier (CTP),Grenoble, is researching deinking and processes andtheir applicability to HP Indigo printed media.In 2009, single loop tests at CTP concluded that fiveout of six HP ElectroInk pages tested met generalEuropean Recovered Paper Council (ERPC) guidelinesfor deinkability.Furthermore, large volumes of HP Indigo prints havebeen successfully deinked in trials managed byNewPage Corporation (see box).In 2009, HP Indigo research and development andmanufacturing facilities sold 60 tons of HP ElectroInkprints each month for recycling.Take-back and recyclingHP operates take-back and recycling programmes forHP Indigo presses that cover both consumables andhardware. Binary Ink Developers (BID) are eligible fora widely available take-back programme.(20)Used ink cartridges take-back and recycling arealready available in some regions. Used imaging oiltake-back has been started with the used oil burnedto reclaim energy. For hardware, end-of-life trade-inoptions are available,(21) and presses taken back byHP are either re-manufactured as R-series presses, ormaterials reclaimed for recycling or disposed of in aresponsible manner.Energy efficiencyThe continuing energy improvements deliveredby the HP Indigo 7500 Digital Press include:consumption of 50 percent less imaging oil thanits predecessor, and up to10 percent less energyconsumed per printed page than the HP Indigo7000 Digital Press. The HP Indigo W7200 DigitalPress consumes up to 40 percent less energy perprinted page than its predecessor.(22)Energy is also saved in these presses with built-inauto-stand-by modes and an easy shut-down/power-up for nights and weekends.Print recycling pilotIn October 2009, Western Michigan University(WMU) Pilot Operations configured pilotunit operations and a trial design underthe direction of NewPage Corporation andTechnical & Investor LLC, to simulate theNewPage Duluth recycle pulp mill. The trialdesign adopted the flotation deinking processutilised at Duluth.“The results of the WMU pilot trial showed 5%Indigo content recycled pulp with other typicalmixed office waste can meet high recycledpulp quality dirt and brightness requirementsutilizing a process similar to that operated byNewPage Duluth. A commercial 5% Indigo trialat NewPage Duluth was recommended and willbe run as final proof. NewPage will proceedwith that (mill) trial.”HP Indigo prints are deinkable andrecyclableHP ElectroInk 4.0 (launched in 2004) showssignificant improvements in deinkabilitycompared to the previous generation ink.HP Indigo presses support 800 substrateswith environmental credentials, many of whichinclude recycled content (30 – 100 percentpost-consumer waste (PWC)).
Environmentally, how does digital printingcompare to offset litho?A comparative environmental life cycle assessment(LCA) was conducted on the impacts of printingmarketing collateral on an Indigo 7000 digitalpress and a specific competitive offset press withsizable market share. The study was conducted by athird-party company, Sylvatica, in accordance withISO standards for studies at making comparativeassertions, and was reviewed by an independentpanel of experts. The study focused on printing8-page letter-size full colour brochures. Environmentalimpacts were divided into four categories of humanhealth, ecosystem quality, climate change (carbonfootprint) and resources.Key findings of the report included:The most significant life cycle stages were the mediaproduction, power consumption and the consumableslife cycle. The actual press life cycle (includingmanufacture), the end-of-life of the paper and thebrochure distribution contributed very little to theenvironmental impact.The test runs were conducted at the economic breakeven point of the HP Indigo 7000 Digital Press (thenumber of pages below which digital printing is moreeconomical than conventional offset). The economicbreak-even point for this job and press was 993brochures, comprising 3,972 double-sided letter-sizedpages.The HP Indigo 7000 Digital Press had a potentially30 percent lower carbon footprint than the offsetpress. These results are yet more favourable for thedigital press at shorter run lengths.The environmental break-even point (where thepresses tested have equal potential environmentalimpact) is 2.4 – 4.1 times greater than the economicbreak-even point, in favour of the digital press. Theenvironmental break-even point in terms of carbonfootprint is circa 3,000 8-page brochures (12,000letter-sized double-sided pages).Sustainable mediaHP Indigo presses support a wide range of media,with 800 qualified papers meeting, amongstothers, these standards: Forestry Stewardship Council (FSC) Sustainable Forest Initiative (SFI) Programme for the Endorsement of ForestryCertification (PEFC) Recycled PapersHow digital printing supports theenvironment Reduced paper waste: print only what youneed Print near the place of use to reduce deliverydistances Higher returns on fewer pieces: leveragevariable data capabilities Reduced make-ready and change-over waste End-to-e
2009 – The HP Indigo WS6000 Digital Press is the first industrial digital press with an oil recycling system. Binary Ink Developer take-back and parts re-use programme initiated 2010 – The HP Indigo 7500 Digital P