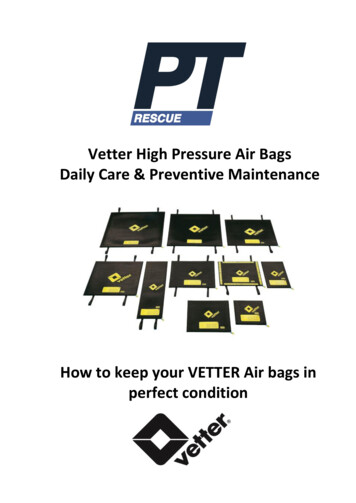
Transcription
Vetter High Pressure Air BagsDaily Care & Preventive MaintenanceHow to keep your VETTER Air bags inperfect condition
Preventive Maintenance and Testingof Vetter Air BagsIntroductionVetter High Pressure Air Bags (8/10 Bar – 116/145 psi) are designed to apply the greatest powerwith millimetre precision on flat or sloping surfaces. They can lift, push, press, prise and supportthe heaviest of loads. They are robust, powerful tools, ideal in countless applications. They act aslifesavers in rescue situations and natural disasters. They can lift and adjust heavy duty machines aswell as a range of industrial applications.Lifting bags may only be operated with compressed air. In exceptional circumstances they can beinflated using water using additional accessories. The lifting bags can only be operated usingoriginal Vetter fittings and in accordance with Vetter operating guidelines.Air bags are manufactured from elastic rubber and are subject to an ageing process. The actualageing of the bag is dependent on a number of factors: Type of use in operationStorage ConditionsHeatHumidityLight and radiation.Regular testing of air bags is important to ensure correct and safe operation.All new air bags are pressure tested after manufacture. Vetter recommends that a full pressure testshould take place after 5 years of use irrespective of the condition of the bag.Life of airbagsManufacturers statement“Mini Lifting Bags are constructed of rubber and are subject to natural aging processes. Even if thebags show no visible signs of wear or damage they should be replaced after 15 years since invisibleaging may have taken place in the composite material”.PTHA Sep 14Page 2 of 7
How to identify age of airbagAir Bags Manufactured Prior to 09/19801234No Date System within No.Air Bags Manufactured From 09/1980 to 08/199401 3 486Serial NoYear of Manufacture (1983 or 1993)Month of Manufacture (Jan)Air Bags Manufactured Since 08/199401 95 4864Serial NoYear of Manufacture (1995)Month of Manufacture (Jan)If the serial No cannot be read other features can be used to identify the age of the bagBags Manufactured prior to 09/1980 One part Brass Valve ConnectionBags Manufactured from 09/1980 to 08/1994 Two part Steel valve connectionLabel with round cornersPrinted technical detailsSafety instructions in 2 languagesBags Manufactured since 08/1994 Two Part steel valve connectionVulcanised technical dataSafety instructions in 4 languagesAramide LabelPTHA Sep 14Page 3 of 7
Preventive MaintenanceThe purpose of preventative maintenance is to ensure the safe operation of the air bags andassociated equipment. Different levels of maintenance need to be undertaken:1. Test following operation consisting of a Visual & Functional Checks2. Hydrostatic Testing of Air BagsVISUAL CHECKSThis series of visual check should be conducted after each use of the bags prior to stowage.RegulatorSTEPDESCRIPTIONINSPECTION345O Ring On cylinder connection(Inlet seal)DIN Thread (on cylinderconnection)Pressure gaugesPressure gauge protective capPressure adjusting valve6Flow control valve7Regulator hose8Hose connectorFree from wear anddamageRuns freely, no visualdamageFree from visual damageFree from visual damageMoves smoothly /Look for signs ofabrasionMoves smoothly /Look for signs ofabrasionFree from cracks, kinks,cuts, abrasion,hardening effects ofchemicals heat etcFree from visual damage12PTHA Sep 14CHECK OK ?Page 4 of 7
Inflation hosesSTEPDESCRIPTIONINSPECTIONCHECK OK ?12CouplingsHose3Coupling & nipple connectionFree from damageFree from cracks, kinks,cuts, abrasion,punctures, hardeningeffects of chemicals heatetcFirm positive couplingEasy connection anddisconnectionController (F Type) (D Type deadman)F TypeF TypeSTEPDESCRIPTIONINSPECTION1Entry coupling25Shut off valve (F) or controlstick (D)Pressure gaugePressure gauge (F) protectivecapPressure gaugeFree from damage,working freelyWorking smoothly6Safety valve (F)34D TypeCHECK OK ?Free from damageFree from damageCheck WP 8/10 barmaxFree from damageTop cap seal intact?Air BagsDirty Bags should be cleaned with warm soapy water after use.STEPDESCRIPTIONINSPECTION12Airbag connecting nippleAirbag surface and edges3Carry loopsFree from damageFree from cuts, crackspunctures, abrasions,heat marks, traces ofacidIntactPTHA Sep 14CHECK OK ?Page 5 of 7
FUNCTIONAL CHECKSSet up the air bags and accessories in accordance with standard operating procedures. Whenconnecting hoses to controller and bags ensure the couplings are working correctly and couple witha firm and positive action.Perform the following functional ECK OK?1Inlet pressure gauge2Discharge pressure gauge3Pressure adjusting valve4Flow control shut-off valve5Flow control shut- offvalveWorks correctly and showspressure of air in cylinderWorks correctly and showsset pressureAdjustable over range?, Setdischarge pressure at 8/10BarWorks correctly. Close so noair is flowing. Ensure thereis no pressure movementafter 5 mins,Open so air can flow.Controller (F Type) (D Type deadman)F TypeSTEPF TypeDESCRIPTIONINSPECTION/ACTION1Shut off valve (F) orcontrol stick (D)2Air LeaksEnsure smooth action of thevalve or control sticks. ClosevalvesWith valves in the closedposition listen for air leaks.3PTHA Sep 14GaugesD TypeCHECK OK?Ensure there are no leaks.Ensure correct operation ofgaugesPage 6 of 7
Air BagsSTEP1DESCRIPTIONINSPECTION/ACTIONAirbag (half WorkingPressure)Inflate air bag until 4 bar isshowing on the controllergauge.2Airbag surface and edges3Airbag (full WorkingPressure)CHECK OK?Check for uncommon dentsFree from opening cuts,punctures, cracks and bulgesInflate air bag until 8/10 baris showing on the controllergauge.Check again for opening cutspunctures cracks, bulges anduncommon dents.OVERPRESSURE HYDROSTATIC TEST by PT HYDRAULICS AUSTRALIAThe purpose of this test is to examine the lifting bags resistance against a pressure 1.3 timesthe maximum allowable working pressure and to ensure no deformation occurs indicatingfailure of the lifting bags structural components. Once charged the lifting bag is maintainedat the elevated pressure for a period of 5 minutes to check for failure.Airbags successfully tested hydrostatically to 1.3 times WP can, after thorough drying, besafely returned to normal service.Care & StowageThe lifting bags and equipment should be cleaned after each operation. Cleaning is normally carriedout with warm water and a detergent.Cleaning must never be carried out with a chemical cleaning agent or a high pressure cleaner device.Airbags and equipment should be stowed away from petroleum products and other corrosive liquids.Stowage areas should be dry and damp freeEnsure airbags are dry before stowing in vehiclePTHA Sep 14Page 7 of 7
of Vetter Air Bags Introduction Vetter High Pressure Air Bags (8/10 Bar – 116/145 psi) are designed to apply the greatest power with millimetre precision on flat or sloping surfaces. They can lift, push, press, prise and support the heaviest of loads. They are robust, powerful tools, ideal in File Size: 731KB