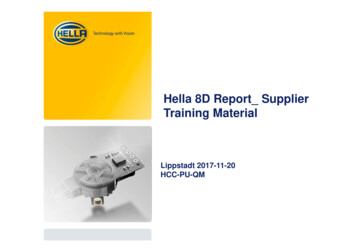
Transcription
Hella 8D Report SupplierTraining MaterialLippstadt 2017-11-20HCC-PU-QMHF-7761EN C (2013-10)
Motivation to make the 8D Report How to fill out Hella 8D Report 8D Report Evaluation8D Training suppliers Keppmann HCC-PU-QME - Lippstadt, Nov 2017
8D - Introduction 8 Disciplines Problem Solving (8D) is a method used to approachand to resolve problems, typically employed by quality engineersor other professionals; Its purpose is to identify, correct and eliminate recurring problems,and it is useful in product and process improvement.; It establishes a permanent corrective action based on statisticalanalysis of the problem and focuses on the origin of the problemby determining its Root Cause. Although it originally comprisedeight stages, or 'disciplines', it was later augmented by an initialplanning stage; The 8D follows the logic of the PDCA Cycle.38D Training suppliers Keppmann HCC-PU-QME - Lippstadt, Nov 2017
Advantages Easy and logically method, clearly shows next steps of problem solution. The method is known and used by all companies from the automotiveindustry. Often this is a required method of documenting the Corrective/Preventiveaction for the problem. An excellent way of reporting nonconformance’s to suppliers and theirCorrective/Preventive actions.48D Training suppliers Keppmann HCC-PU-QME - Lippstadt, Nov 2017
8D Problem Solving8D follows the logic of thePDCA Cycle18ProblemSolvingFinal meetingTeam7Prevention ofrecurrence ofthe mentCorrective actionsActioneffectiveness45validationRoot CauseCorrectiveAnalysisactions andtracking ofeffectiveness58D Training suppliers Keppmann HCC-PU-QME - Lippstadt, Nov 2017
Motivation to make the 8D Report How to fill out Hella 8D Report 8D Report Evaluation8D Training suppliers Keppmann HCC-PU-QME - Lippstadt, Nov 2017
8D Steps7D1Problem solving teamD2Problem descriptionD3Containment actionsD4Root cause analysisD5Corrective actions and tracking of effectivenessD6Corrective actions effectiveness validationD7Prevention of recurrence of the non-conformityD8Final meeting8D Training suppliers Keppmann HCC-PU-QME - Lippstadt, Nov 2017
D1 — Problem Solving TeamD1TaskD1D3D4D5D6D7D8Select team members Action Members with appropriate skills are nominated based onthe problem descriptionA team leader is appointedTargetConfirmation of the team structure and assignment ofresponsibilities among the team members88D Training suppliers Keppmann HCC-PU-QME - Lippstadt, Nov 2017
D1 — Problem Solving TeamHeader of 8D report filled with information come from Hella’s Quality Notification letter.23451Please fill in right information according to below explanation:1 Hella claim no. can directly get from Hella QN.2 Interim 8D Report: D8 not finished.3 Final 8D Report: D8 finished.4 First issue date: Official issue date to Hella, e.g. it’s always a date when supplierfinished D3 or D5, which is required by Hella SQA.5 When 8D is updated, supplier shall update with this date.98D Training suppliers Keppmann HCC-PU-QME - Lippstadt, Nov 2017
D1 — Problem Solving TeamInformation regarding Hella contact person and claim subject213465All above items can directly get from Hella QN. As following attachment show:-52021-6160xxxx43108D Training suppliers Keppmann HCC-PU-QME - Lippstadt, Nov 201716
D1 — Problem Solving TeamType of failure12341 If the failure part is detected from Hella plant. Please select ‘Hella internal’.2 If the failure part is detected from Hella’s customers, for example OEM, Tier 1. Pleaseselect ‘0-km Return’.3 If the failure part is detected from consumer side (e.g. 4S store or markets). Pleaseselect ‘Field return’.4 If the failure part is detected as logistic failure. Please select ‘Logistics failure’.118D Training suppliers Keppmann HCC-PU-QME - Lippstadt, Nov 2017
D1 — Problem Solving TeamSupplier information: contact person, location, material, tools126789⑩3451The name of supplier contact person;7Supplier internal part No.2Which department did supplier contact person work?Supplier internal claim tracking number;3Supplier contact person’s E-mail;894Supplier contact person’s telephone;5Supplier cross functional team member, includingname and Dept.6Supplier manufacturing site/plant/workshop for thisdefect part;12Type of machine, e.g. injection molding/stamping/die-casting, etc.⑩Equipment number which defect part manufactured;Devices number, e.g. tool number, fixture number whichdedicated for this part;The name of supplier which cavity or fixture be affected by thiscomplaint .8D Training suppliers Keppmann HCC-PU-QME - Lippstadt, Nov 2017
D2 — Problem DescriptionD1TaskD2DDDD3456Collect Information, data, facts and figures D7D8Describe the problem (defect/deviation) as accurately as possible givingquantitative detailsAnswer the questions belowProblemWho?What?When?Where?Why?How?How often?Action Target13Past(Target situation)Present(Present actual situation)The cause ofthe deviationis unknown at first}Describedeviation (problem)on the basisof factsAll problem solving team members must havea clear and fact based understanding of the problemPrecise problem description8D Training suppliers Keppmann HCC-PU-QME - Lippstadt, Nov 2017
D2 — Problem Description1Same as the description on Hella’s Quality Notification letter.1 124W1Hwhat: defects descriptionWhen: claim dateWhere: warehouse, production lineWho: Hella Incoming, production, orothershow many: defects quantity foundUse Supplier internal language to describe what defects happen. Which2 characteristic can’t meet Hella drawing/requirement. OK/NOK parts shown.148D Training suppliers Keppmann HCC-PU-QME - Lippstadt, Nov 2017
D2 — Problem Description1231 If this failure happened before, select ‘Yes’;2 If this failure 1st time happened, select ‘No’;3 If this is repeat issue, please fill in last Hella claim No. and last Supplier internalclaim No.4564 Can get directly from Hella’s Quality Notification Letter:5 Potential affected Quantity include :Hella warehouse Q’ty On the Way Q’ty Supplier warehouse Q’ty.6 All parts under the same production condition.Affected period15Affected production recordAffected quantity8D Training suppliers Keppmann HCC-PU-QME - Lippstadt, Nov 2017
D2 — Problem Description1234HellastockaffectedOn theway erstockaffectedPotentialaffected1 If Hella stock affected, please select ‘yes’, otherwise ‘no’. And fill in affectedquantity and corresponding ‘lot number’.2 If parts en route of transportation to Hella affected, please select ‘yes’,otherwise ‘no’. And fill in affected quantity and corresponding ‘lot number’.3 If Supplier consignation affected, please select ‘yes’, otherwise ‘no’. And fillin affected quantity and corresponding ‘lot number’.4 If Supplier stock affected, please select ‘yes’, otherwise ‘no’. And fill inaffected quantity and corresponding ‘lot number’.168D Training suppliers Keppmann HCC-PU-QME - Lippstadt, Nov 2017
D3 — Containment ActionsD1TaskD2D4D5D6D7Determine the most suitable containment actions Action TargetD3D8Containment actions must be taken to safeguard the situation, inorder to prevent a recurrence of the problem at the customer.Containment actions therefore serve only as a safeguard and oftenbear no relation to the cause of the problem.Cost considerations should play little or no part in the initialresponse.A schedule for implementing the containment actions must bedeveloped and the effectiveness of the measures must be assessed.Instant information and support to the customer andimplementation of containment actions as quickly as possible.1. 24 hours: quick response e.g.containment actions at HELLA2. 48 hours: containment actionsfully implemented (D3 completedand sent to HELLA)178D Training suppliers Keppmann HCC-PU-QME - Lippstadt, Nov 2017
D3 — Containment Actions12345In order to ensure Hella restart production, supplier need carry out effective1 urgent action, e.g. sorting, rework, stock exchange.2 Supplier action date instead of week.3 Person who is responsible for containment action.4 Additional comments.5 Supplier shall fill in real effectiveness from Hella feedback.Containment action shall include ‘how to process affected stock’ and ‘how to ensuregood parts to Hella’.188D Training suppliers Keppmann HCC-PU-QME - Lippstadt, Nov 2017
D3 — Containment Actions3214Must update sorting result after sorting action5761 Location of supplier sorting2 Total sortingquantity3 Total defectsquantity4 Total defectsPPM5 Don’t forget to summarize this6 Mark/label of this delivery for better tracking7 First delivery after implementation of containment actions, PS: from supplier side198D Training suppliers Keppmann HCC-PU-QME - Lippstadt, Nov 2017
D4 — Root Cause AnalysisD1TaskD2 Action 20D4D5D6D7D8Determination of the root cause TargetD3All possible causes of the defect must be considered.All possible causes should be determined and compared withthe problem profile through systematic application of validprocedures, based on the physical, chemical and technicalrelationships and application of appropriate quality tools.The "Why" questioning technique should be applied determiningthe root cause.Confirmation of the root cause8D Training suppliers Keppmann HCC-PU-QME - Lippstadt, Nov 2017
D4 — Root Cause AnalysisDetail measurement methodology andprocedure should be specified here.Use appropriate measurement to measure potential characteristics forOK parts and failure parts, also show all test result for analysis.PS:It’s better that supplier provide specification or drawing for potentialcharacteristics.analysis for occurrence, non-detection, systemare mandatory218D Training suppliers Keppmann HCC-PU-QME - Lippstadt, Nov 2017
D4 — Root Cause AnalysisStudy criminalmotive(5 Why)Determine realmurderer(reproductivity orconfirm historyrecord) Appropriate quality tool to investigate allpotential root cause, e.g. Fishbone, FailureTree. It will help us to find all root cause. All root cause shall be analyzed with 5why. The analysis procedure should be clear &reasonable and in system methodology.Recommend to attach detail analysis report inthe last page.Identify criminalsuspect (Fish bone、FTA、flow chart、,module,FMEA, etc.)228D Training suppliers Keppmann HCC-PU-QME - Lippstadt, Nov 2017
D4 — Root Cause Analysis1.2.Why did ourmanufacturing processnot prevent theincident?Repeat asking "Why"until you found the rootcause (basicincidence), which isfeasible to becontrolled, e.g.‘operation WI’,weakness design,supplier management,etc.1.2.Why did our qualityprocess not detect theincident?Repeat asking "Why"until you found the rootcause (basicincidence), which isfeasible to becontrolled, e.g.‘inspection WI’,different requirementbetween xxx withcustomer or supplier,etc.Why did qualityplanning process notpredict this defects?For example, nolessons learned,different requirementbetween xxx withcustomer or supplier,Poke Yoka, etcThe 5 Whys is a question-asking technique used to explore the cause-and-effectrelationships underlying a particular problem. The primary goal of the technique is todetermine the root cause of a defect or problem.238D Training suppliers Keppmann HCC-PU-QME - Lippstadt, Nov 2017
D4 — Root Cause Analysis – example 1Put a example with possible root causes analysis and verification, and 5 why analysis.Problem description:HELLA complaint Lower Housing can not be welded properly and burnt on the topsurface. Defect rate around 6%. Transmission rate of Lower Housing is less than 18% (Spec:min.18%).Occurrence Root Cause:5M1E checked with fishbone by supplier, only MVR of raw material has variation.DOE was carried out to prove that MVR is a real factor/root cause.248D Training suppliers Keppmann HCC-PU-QME - Lippstadt, Nov 2017
D4 — Root Cause Analysis – example 2Put a example with possible root causes analysis and verification, and 5 why analysis.Problem description:HELLA complaint there is a dent on the LED hole surface as right picture show.Defect rate is around 1%.Occurrence Root Cause:5M1E checked with fishbone by supplier, no process change happened. However,no action for tooling surface cleaning (Comment: TPU fragment happen at parting line and it’s unavoidable.)258D Training suppliers Keppmann HCC-PU-QME - Lippstadt, Nov 2017
D4 — Root Cause Analysis1231Total sorting quantity, and total defects partsquantity and calculate PPM value.Total defect parts of lifetime6Total produced parts of lifetime *10Show mark/labeling to highlight the suspect parts.2 The problem is easy to find and identify, short period failure. If yes, pleasecalculate PPM and fill in.326The problem is difficult to find or neverfound but was existing, long periodfailure. Even from the SOP to now. Ifyes, please calculate PPM and fill in.8D Training suppliers Keppmann HCC-PU-QME - Lippstadt, Nov 2017
D4 — Root Cause AnalysisThe easiest lesson learned is spreading the experience to other similarproducts and processes.Read across is a good approach to gain lessons learned. Don’tneglect this process.278D Training suppliers Keppmann HCC-PU-QME - Lippstadt, Nov 2017
D5 – Corrective Actions and Tracking of Effectiveness tracking ofeffectivenessD1TaskD2D3D4D5D6D7D8Confirm "optimum" corrective actions All measures that can solve and ultimately eliminate the problemmust be compiled.The effectiveness of the measures must be verified and sideeffects must be assessed.Action Target28“Optimum" corrective action must be determined and confirmed.Action plan with introduction timing and responsibilities must bedetermined and released.Approval and application of the corrective measures8D Training suppliers Keppmann HCC-PU-QME - Lippstadt, Nov 2017
D5 – Corrective Actions and Tracking of Effectiveness tracking ofeffectiveness213451 Corrective actions must be provided and all of them could prevent the issue2from happening in the future.Supplier action date instead of week.Long termmeasures shouldlink to D4 rootcauses3 Person who is responsible for containment action.4 Additional comments.5 Supplier must confirm if countermeasure is carried out and effective.298D Training suppliers Keppmann HCC-PU-QME - Lippstadt, Nov 2017
D5 – Corrective Actions and Tracking of Effectiveness tracking ofeffectiveness1231 Please fill in the date after corrective action taken for occurrence.2 Please fill in the date after corrective action taken for detect.3 Please also attach the picture of the marking of the first delivery.308D Training suppliers Keppmann HCC-PU-QME - Lippstadt, Nov 2017
D5 – Corrective Actions and Tracking of Effectiveness tracking ofeffectiveness“Why was the failure not detected by yourself” links to “Detection” in FMEA“Why did the failure happened” link to “Occurrence” in FMEA. Attach updatedFMEA here.Severity only allowed to change when the design of component changesaccording to complaint.Occurrence only allowed to change when 5.0 take relevant actions to 4.0.Detection only allowed to change when 5.1 take relevant actions to 4.1.318D Training suppliers Keppmann HCC-PU-QME - Lippstadt, Nov 2017
D5 – Corrective Actions and Tracking of Effectiveness tracking ofeffectiveness121 Ensure all relevant documentations are updated on time.If the long term counter-measure in 5.0 related to test method or equipment2 changed, capability study must be re-checked.328D Training suppliers Keppmann HCC-PU-QME - Lippstadt, Nov 2017
D6 – Corrective Actions Effectiveness Validation of effectivenessD1Task Target33D3D4D5D6D7D8Establish plan to introduce corrective actions ActionD2As many actions as required, but as few as possible,should be implemented in accordance with D5 result.Decision about the need to continue containment actions.Determination of process monitoring requirements and needof documentation.Implementation of the corrective actions8D Training suppliers Keppmann HCC-PU-QME - Lippstadt, Nov 2017
D6 – Corrective Actions Effectiveness Validation of effectiveness1231 Verify all effectiveness for both occurrence root cause and outflow root causeand fill in related date.2 How to check the effectiveness should be specified. At least should be more strictthan normal check method.3 Attach ‘Hella full run report’ or SPC report, or other verification report.Without this verification, this 8D report will not be closed by Hella. Pleaseattach all evidence in the last page of format.348D Training suppliers Keppmann HCC-PU-QME - Lippstadt, Nov 2017
D7 – Prevention of Recurrence of the non-ConformityD1TaskD2 D5D6D7D8Process-related evaluation and analysis is key.Identical and similar products and processes are in focus.Application of the "3 x 5 Why" questioning technique:Why was the problem . not predicted by the product planning/engineering process?. not prevented by the production/manufacturing process?. not protected by the quality assurance process?Action 35D4Formulate measures to improve and safeguard processes TargetD3Knowledge gained is used to improve processes.Release and application of corrective actions for system andprocess improvement8D Training suppliers Keppmann HCC-PU-QME - Lippstadt, Nov 2017
D7 — Prevention of Recurrence of the non-Conformity13241 Fill in date of supplier final judgement for below information.Whatever forfinal judgement,supplier mustfinish D4.2 If it is a supplier responsible issue, supplier need to select ‘claim is accepted’.3 If this issue is supplier responsible, please provide all failure part quantity aftersorting/rework for Hella stock.4 If this issue is not supplier responsible and get Hella agreement, supplier canselect “claim is not accepted’.368D Training suppliers Keppmann HCC-PU-QME - Lippstadt, Nov 2017
D8 – Final meetingD1TaskD2 Target37D4D5D6D7D8Final meeting of the 8-D team ActionD3During the concluding discussion, the problem solving teamconducts a critical evaluation of all 8-D steps and actions.The 8-D report is officially closed.Combined efforts by the team are acknowledged bysupervisors and praised accordingly.The customer is informed of the conclusion and sent the8-D report, signed by those responsible.The completed 8-D report is archived.Final conclusion of 8-D activities related to this problem8D Training suppliers Keppmann HCC-PU-QME - Lippstadt, Nov 2017
D8 — Final meetingPlease fill in interim 8D report submission date and responsible person’s name.Please fill in Final 8D report submission date and responsible person’s name.388D Training suppliers Keppmann HCC-PU-QME - Lippstadt, Nov 2017
Motivation to make the 8D Report How to fill out Hella 8D Report 8D Report Evaluation8D Training suppliers Keppmann HCC-PU-QME - Lippstadt, Nov 2017
8D Report EvaluationWhy need to do evaluation? Use the same criteria to assess 8D report objectively, to reflect thecapability of suppliers. Be able to clearly recognize which part of the report does not meet therequirements and make corrections accordingly. Suppliers can assess by themselves if 8D report meet the requirementsbefore submit to Hella, which can improve the effectiveness of the work. According to the evaluation results, the interior of Hella can define thetracking plan for each case. Evaluation result is one of the evidence for annual performance scoring.408D Training suppliers Keppmann HCC-PU-QME - Lippstadt, Nov 2017
8D Report EvaluationHow to fill out 8D quality survey?418D Training suppliers Keppmann HCC-PU-QME - Lippstadt, Nov 2017
8D Report EvaluationScoringsQuestionnaire - 8DR assessmentOccurenceOutflow to the customerAnalysis procedure:The following steps must be accomplished for a correct analysis procedure: 1.) Allpotential root causes of a problem must be identified. 2.) The real root causes a
Nov 27, 2017 · Occurrence Root Cause: 5M1E checked with fishbone by supplier, only MVR of raw material has variation. DOE was carried out to prove that MVR is a real factor/root cause . Put a example with possible r