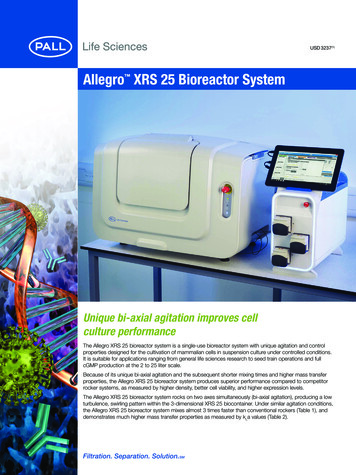
Transcription
USD 3237(1)Allegro XRS 25 Bioreactor SystemUnique bi-axial agitation improves cellculture performanceThe Allegro XRS 25 bioreactor system is a single-use bioreactor system with unique agitation and controlproperties designed for the cultivation of mammalian cells in suspension culture under controlled conditions.It is suitable for applications ranging from general life sciences research to seed train operations and fullcGMP production at the 2 to 25 liter scale.Because of its unique bi-axial agitation and the subsequent shorter mixing times and higher mass transferproperties, the Allegro XRS 25 bioreactor system produces superior performance compared to competitorrocker systems, as measured by higher density, better cell viability, and higher expression levels.The Allegro XRS 25 bioreactor system rocks on two axes simultaneously (bi-axial agitation), producing a lowturbulence, swirling pattern within the 3-dimensional XRS 25 biocontainer. Under similar agitation conditions,the Allegro XRS 25 bioreactor system mixes almost 3 times faster than conventional rockers (Table 1), anddemonstrates much higher mass transfer properties as measured by kLa values (Table 2).
Table 1Summary of best mixing times observed in pH equilibrationstudies, 20 liter working volumes with conventional pH probes¹SystemConditionMixing Time(s)Conventional rockerMaximum speed and rock angle:42 rpm, 10.4 50 to 98 seconds2Allegro XRS 25bioreactor system75% maximum speed,maximum long axis angle,1/3 short axis angle: 30 rpm,15 long, 5 short16 secondsTable 2Summary of mass transfer coefficients observed in 20 literworking volumes as measured with nitrogen purge and recovery3SystemConditionkLa per HourConventional rockerMaximum speed and angle:42 rpm, 10.4 42Allegro XRS 25bioreactor system40 rpm, 15 long, 15 short731 Mixing trial results from three repetitions for each device.2 Times significantly different for edge/center measurements.3 Mass transfer results from three repetitions for each device.For additional details on mixing and mass transfer studies,see Pall application note USD 2899: Performance Mappingin the Pall XRS 20 Bioreactor System.ApplicationsThe mixing properties of the 3D biocontainer design and bi-axialagitation lead to superior cell culture performance in mammaliansuspension systems. With faster delivery of nutrients to thecellular micro-environment (and faster removal of metabolites),the Allegro XRS 25 bioreactor system allows cells to attain higherdensities, with higher overall viabilities, leading to significantlyhigher protein expression levels. In the batch culture examplebelow (Figure 1), with identical media inputs and seeds, theAllegro XRS 25 bioreactor system produced 18% higher celldensities, and 30% more antibody titer compared to conventionalrocker technologies.Figure 1Summary of side-by-side growth and viability experiments (n 3) at 20 liter working volumes comparing conventional rocker system andAllegro XRS 25 bioreactor system. Simple batch culture of a CHO (Chinese hamster ovary) cell line expressing a monoclonal 0x107ViabilityViable Cells 200250300350400Culture Duration (Hrs)XRS 25 Bioreactor System ResultsConventional Rocker ResultsThe excellent mixing properties of the Allegro XRS 25 bioreactor system have also shown to be beneficial for growing batch, fed batchand perfusion cultures of mammalian (CHO, hybridoma) and insect cells.2
System Overview, Features and BenefitsFigure 2Allegro XRS 25 bioreactor system – featuring the agitation platform, the single-use biocontainer and the mPath control tower withPall Link supervisory control and data acquisition (SCADA) software package. The Allegro XRS 25 bioreactor system incorporates manyfeatures to ensure easy operation, robust performance, and suitability for cGMP operations.AllegroXRS S 25platformTable 3Table 4Allegro XRS 25 BiocontainerAllegro XRS 25 PlatformFeatureBenefitFeatureBenefit3 dimensional biocontainerdesign Superior mixing (with bi-axial platform),robust in operationBi-axial agitation (rockingmotion on two horizontalaxes at 90 separation) Improved agitation properties:shorter mixing times and highermass transfer ratesFully enclosed platform withsafety interlock Improved operator safety,suitable for productionenvironments, protects lightsensitive culture media True single-use system, ease ofBiocontainer with integratedinstallation, minimal turn-around timeoptical sensors, integrated filters,pre-assembled tubing setsGas inlet and exhaust filtersare integrity testable, sterilizinggrade 0.2 µm Improved suitability for cGMP operationsIntegrated bottom drain withrotary lift valve Improved suitability for cGMP operations,minimal hold-up volume, ease of useMultiple liquid addition ports Improved ease of use, easily handlesfed batch operations, acid/base pHcontrol feedsIntegrated single-use pH anddissolved oxygen (DO) sensors Ease of use and reduced probabilityof contaminationIntegrated sampling port Ease of use – very low hold up volume(less than 5 mL), capable of samplingwithout stopping agitationSingle-use biocontainer builtwith Allegro film Assurance of robustness, qualityand supply, track record of use offilm in cGMP operations, validationguide availablewww.pall.com/biopharm3
Table 5Table 5 continuedmPath Control Tower and Pall Link ServerFeatureBenefitFeatureBenefitmPath control tower designedfor operation with Pall Link –a SCADA software package Capable of accessing data anywhereon any networked device includinglaboratory workstations, desktopcomputers or remote devices such aslaptops, mobile phones and tabletsGas handling by sixoxygen-rated thermal massflow controllers (TMFCs)pre-calibrated for process gases Accurate gas mixing for two gasstreams enabling accurate parametercontrol and complex gas control regimes,each gas within the mix delivered by adedicated TMFC Operates as either a standalonenetwork or integrated with site ITsystems, compatible with multiplenetwork security approaches(e.g. virtual private network [VPN])and password protection to protectbioreactors from unauthorized access Primary gas mix: N2, O2, air and CO2 Intuitive visual displays for easyinteraction with bioreactors to calibratecomponents, set critical parameters,and fine tune process control Onboard pressure sensors, combinedwith alarming capability enablenotification of empty gas cylindersor biocontainer overpressure Advanced trending capability includingcreation of custom trends of anyprocess variable for both historic andlive processes Database centric design supportsnaming, logging and exportingexperiments for traceability anddata analysis Secondary gas mix: CO2 and air Calibrated flow rates up to 1 L/minfor each TMFC Onboard regulators ensure accuracy ofTMFCs even with higher input pressures Fast fill button – quick and safe inflationof biocontainers with airLiquid handling with threevariable speed pumps,integrated load cells andbiocontainer hangers Accurate delivery of feeds and titrantswithout compromises, standard variablespeed pumps enable smoother processcontrol and feed profiles for lessprocess variability 8 mm max tubing outside diameter (OD) 14 - 211 rpm (control requiring speedsless than 14 rpm achieved through pulsewidth modulation [PWM]) Removable pump heads for easycleaning and serviceability Removable biocontainer hangers withintegrated load cells allow space efficientexecution of weight based feed profilesand accurate tracking of titrant deliveryErgonomic industrial design Extensive human factors researchto determine optimal placement ofconnections and control tower elements Flexibility in operation – choose whenand where to view data, choose howto design processes Compact design to limit bench spacerequirements – small form factor andbiocontainer hangers remove the needfor scales and bottles Elevated from bench for cleanability Full alarm customization to alert forprocess or safety critical events Management features for user-definablerecipes including scheduling, versioncontrol and retirement for recipes nolonger in use Compliance capability – designed foroperation following 21 CFR Part 11/Annex 11 regulationsMultiple alarm notificationmodalities to ensure responseto process critical events Color coded illumination ring aroundthe front face of the control towerallows identification of operatingstate from a distance Individual LED indicators for eachconnection on the connector panelidentify problems during set upand operation Highly visible color and textualalerts indicate alarm severity onall software interfaces Historical alarm logs to reviewequipment and process performance4
Tubing management systemIn-process samplingDrain and optical sensorsCustomizationPall Quality StandardsPall has standard Allegro XRS 25 biocontainers equipped with allliquid and gas connections for the most typical processes andmost operations. The three feed lines, the accessory line, and thedrain are fitted with standard laboratory connections. Processliquids, including media and inoculum, can easily and safely betransferred into the bioreactor.Pall maintains a very stringent approach to quality of purchasedand manufactured components. Allegro bioreactor systems aredesigned and built to well recognized industry standards. TheAllegro XRS 25 bioreactor system hardware meets many qualitystandards including:Pall can assist in customizing the bioreactor systems.This includes adding aseptic connectors (Kleenpak sterileconnectors), and small changes on the biocontainer up to andincluding integrating the bioreactor with all surrounding unitoperations into a fully automated process.Documentation and CertificatesThe Allegro XRS bioreactor is delivered with completedocumentation that qualifies the system. All units are testedprior to shipment and witnessed Factory Acceptance Testing(FAT) is available on request.The biocontainers are delivered with all the batch specificcertificates and calibration information for the includedsingle-use sensors.Pall also can assist with hardware qualification, and standardinstallation verification (IV), operational verification (OV), factoryacceptance test (FAT) and site acceptance test (SAT) testprotocols are available. Good automated manufacturing practice (GAMP)current version 21 CFR Part 11 for electronic records Electromagnetic compatibility (EMC) to EN 61326-1: 2013 andFCC CFR 47 Part 15B: 2013 The product is made in a manufacturing facility where thequality management system is ISO9001: 2008 certified.A full list of quality standards is available on requestThe Allegro XRS 25 biocontainer quality standards include: The product is made in a manufacturing facility where thequality management system is ISO13485 and ISO9001 certified 100% of Allegro XRS 25 biocontainers are checked for correctcomponents, configuration, welding standard and dimensionalcorrectness. A visual inspection confirms there are noembedded particles in the film or any loose particles inside oroutside of the biocontainer 100% of Allegro XRS 25 biocontainer chambers undergo apressure leak test during manufacturing Samples from each biocontainer manufacturing batch undergoa tensile test of the film weld area and a microscope inspectionof the weld area to ensure the quality of the welded seal Fluid path endotoxins: periodically, rinse effluents fromrepresentative samples of Allegro systems are tested forendotoxins in accordance with USP 85 using limulusamoebocyte lysate (LAL) reagent. Fluid path rinses meet theinternal specification of 0.25 EU/mL Fluid path cleanliness: periodically, rinse effluents fromrepresentative samples of Allegro systems are tested forparticulates. Fluid path rinses meet the current limits underUSP 788 particulate matter in injectionsIntegrated drain simplifies harvest operationswww.pall.com/biopharm5
The materials of construction of the Allegro XRS 25biocontainer meet: USP 88 Biological reactivity test in vivo for class VI 50 C plastics USP 87 Biological reactivity tests in vivo, cytotoxicity USP 85 Bacterial endotoxin testsGeneral System SpecificationsTable 6DimensionsController230 mm x 600 mm x 450 mm (H 590 mm with hangersinstalled) USP 661 Physico-chemical testing for plastics(W x D x H)Platform900 mm x 600 mm x 620 mm(H 990 mm with lid open) USP 788 Particulate matter in injectionsWeightController20 kgPlatform(with filledbiocontainer)78 kg (104 kg filled)Materials of construction for all components in contact with fluidare TSE/BSE risk materials free.All Allegro XRS 25 biocontainers are supplied double bagged(outer layer opaque to protect the single-use sensors from light)and irradiated at a minimum dose of 25 kGy.GasesGas connectionsGas flow controlTMFCTMFC pressurized air0 - 1000 mL/minTMFC oxygen0 - 1000 mL/minTMFC carbon dioxide0 - 1000 mL/minTMFC nitrogen0 - 1000 mL/minPumpsQuantity and connection3 x variable speed peristalticpumps, 0 - 211 rpm,maximum tubing OD 8 mmAeration0.2 μm single-use filterInlet filterGas deliveryBi-Axial AgitationThe Allegro single-use bioreactor systems are supported withextensive maintenance and service packages. Pall has a globalnetwork of technicians and engineers available to assist withinstallation, qualification, training, technical support, preventivemaintenance and on-site repairs. Contact Pall to arrange todiscuss any of these services.Pall Accelerator process development services provide customerswith expert advice and support for the implementation of fullyintegrated single-use processing solutions into new or existingprocesses, including process optimization, equipment selection,transfer of existing processes, scale-up and troubleshootingadvice. Details can be found in the Accelerator ProcessDevelopment Services brochure (USD 3079).Preventive maintenance packages are available to ensure thecontinuous reliable operation of the Allegro XRS 25 bioreactorand to minimize downtime. Preventive maintenance typicallyincludes a full functional test, exchange of wear parts, andcalibration of all sensors.6ProcessGas mix injected intobiocontainer headspaceExhaust filter0.2 μm single-use filterExhaust heaterSilicone heater matSpeed1 - 35 rpmAnglePreventive Maintenance and ServicePackagesInlet and outlet quickconnectors 6 mm OD-15 to 15 degrees in bothX and Y directionsControlStepper motor controlledWorking volumes2 - 25 litersTemperature controlmethodHeating blanket, ambientconvective coolingTemperature range10 - 40 CpH control6 - 8, integrated single-useoptical sensorDissolved oxygen control0 - 100%, integratedsingle-use optical sensor
The Allegro XRS 25 bioreactor system is available as astandard product; however, both the bioreactor hardware andconsumables can be customized. Our teams are specialized inupstream and downstream processing and will gladly help findthe right technology for any part of your manufacturing process.It is possible to combine the Allegro products to meet anyrequirement in the upstream part of the process: Media preparation Buffer preparation Media sterilization and aseptic transfer Liquid transfer into the bioreactor (e.g. glucose,anti-foam, base, etc.) Seed train solutions Cell harvest and separation Perfusion modulesPlease contact Pall for a total solution discussion onyour process.Ordering InformationTable 7DescriptionPart NumberAllegro XRS 25 Bioreactor System:System hardware – consists of Allegro XRS 25 platform,mPath controller, control cablesXRS25BRSPall Link server and SCADA softwareMPATHLINKStandard Allegro XRS 25 biocontainer609-40AAccessory Manifolds:KleenpakTM manifold with vent filter609-100ALuer to Y connection and Kleenpak connectors629-100BMPC to Y connection and Kleenpak connectors629-100C5 liter 2D Allegro accessory biocontainer with filling filter,Kleenpak connector609-100D1 liter 2D Allegro accessory biocontainer with filling filter,Kleenpak connector609-100E20 liter 2D Allegro accessory biocontainer with filling filter,Kleenpak connector609-100FAllegro XRS 25 bioreactor system integrated into total upstreamprocessing solutionVisit us on the Web at www.pall.com/bioreactorsE-mail us at bioreactors@pall.comCorporate HeadquartersPort Washington, NY, USA 1.800.717.7255 toll free (USA) 1.516.484.5400 phonebiopharm@pall.com e-mailEuropean HeadquartersFribourg, Switzerland 41 (0)26 350 53 00 phoneLifeSciences.EU@pall.com e-mailInternational OfficesPall Corporation has offices and plants throughout the world in locations such as: Argentina, Australia, Austria,Belgium, Brazil, Canada, China, France, Germany, India, Indonesia, Ireland, Italy, Japan, Korea, Malaysia, Mexico,the Netherlands, New Zealand, Norway, Poland, Puerto Rico, Russia, Singapore, South Africa, Spain, Sweden,Switzerland, Taiwan, Thailand, the United Kingdom, the United States, and Venezuela. Distributors in all majorindustrial areas of the world. To locate the Pall office or distributor nearest you, visit www.pall.com/contact.The information provided in this literature was reviewed for accuracy at the time of publication. Productdata may be subject to change without notice. For current information consult your local Pall distributoror contact Pall directly.Asia-Pacific HeadquartersSingapore 65 6389 6500 phonesgcustomerservice@pall.com e-mail, Pall, Allegro, Kleenpak and mPath are trademarks of Pall Corporation.Filtration.Separation.Solution. is a service mark of Pall Corporation. indicates a trademark registered in the USA. 2017 Pall Corporation.GN17.06891USD 3237(1)
Allegro XRS 25 bioreactor system – featuring the agitation platform, the single-use biocontainer and the mPath control tower with . Historical alarm logs to review equipment and process performance Accurate gas mixing for two gas . 21 CFR Part 11 for electronic records Electr