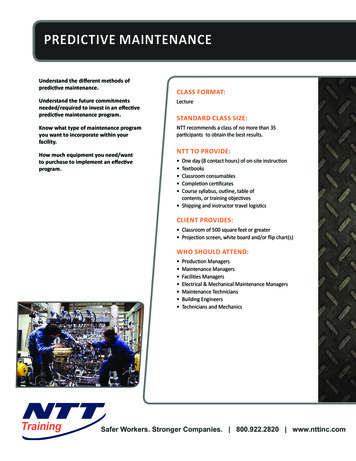
Transcription
PREDICTIVE MAINTENANCEUnderstand the different methods ofpredictive maintenance.CLASS FORMAT:Understand the future commitmentsneeded/required to invest in an effectivepredictive maintenance program.LectureKnow what type of maintenance programyou want to incorporate within yourfacility.NTT recommends a class of no more than 35participants to obtain the best results.How much equipment you need/wantto purchase to implement an effectiveprogram.STANDARD CLASS SIZE:NTT TO PROVIDE: One day (8 contact hours) of on-site instructionTextbooksClassroom consumablesCompletion certificatesCourse syllabus, outline, table ofcontents, or training objectives Shipping and instructor travel logisticsCLIENT PROVIDES: Classroom of 500 square feet or greater Projection screen, white board and/or flip chart(s)WHO SHOULD ATTEND: TrainingProduction ManagersMaintenance ManagersFacilities ManagersElectrical & Mechanical Maintenance ManagersMaintenance TechniciansBuilding EngineersTechnicians and MechanicsSafer Workers. Stronger Companies. 800.922.2820 www.nttinc.com
PREDICTIVE MAINTENANCECOURSE AGENDAINTRO TO PREDICATIVE MAINTENANCETRIBOLOGY – OIL ANALYSIS Overview of PDM practices Overview of Oil Analysis programs and best practicesFINANCIAL IMPLICATIONS AND COSTJUSTIFICATIONULTRASONIC TESTING Benefits of developing a PDM program Overview of Ultrasonic Testingprograms and best practicesVIBRATION MONITORING ANALYSISFAILURE-MODE ANALYSIS Overview of Vibration Analysisprograms and best practices Overview of Failure-Mode Analysis Identify all possible failures within a systemINFRARED THERMOGRAPHYESTABLISHING A PREDICTIVEMAINTENANCE PROGRAM Overview of Infrared ThermographyTraining Total-Plant Predictive Maintenance Program Maintaining the program World-Class MaintenanceSafer Workers. Stronger Companies. 800.922.2820 www.nttinc.com
Infrared ThermographyThermography can be used to monitor thecondition of structures, plant machinery,and systems. It is a predictive maintenancetechnique using an infrared camera designedto monitor the emission of infrared energy.Infrared Thermography is a useful tool formaintenance of electrical and mechanicalindustrial systems.Using infrared technology effectively withina predictive maintenance program is allabout gathering the data correctly and theninterpretation of the data. In this one-dayseminar, our knowledgeable instructors relatetheir real world experience to help you learnthese valuable techniques, avoid the pitfallsand common mistakes, and create a steeplearning curve for you to immediately go backand apply what you have learned.What You’ll Learn:Participants will learn how to correctly operatean infrared camera in order to receive themost accurate data. You will also learn how tointerpret the resulting data and determine nextsteps for preventative maintenance.You will be able to use techniques learned inthis seminar to monitor electrical equipment,HVAC systems, motors, bearings, and muchmore.Seminar Description:Agenda Topics: Basics of infrared technology Theories associated with basic infraredtechnology Safety concerns and different types ofinfrared problems Data collection and reporting Use of an infrared camera (FLIR i7actually used in class)TrainingCLASS FORMAT:Hands-On and LectureSTANDARD CLASS SIZE:NTT recommends a class of no more than 35participants to obtain the best results.NTT TO PROVIDE: 1-day hands-on and lectureTextbooksClassroom consumablesCompletion certificatesShipping and instructor travel logisticsClient PROVIDEs: Classroom of 500 square feet or greater Projection screen, white board and/or flip chart(s)WHO SHOULD ATTEND: ElectriciansMechanicsApprentice and experienced HVAC techniciansLinemen & Utility workersWarehouse employeesMaintenance TechniciansEnergy management personnelPlant & facility maintenance techniciansBuilding engineers, managers & superintendentsPlant & facility managersStationary engineersSafety directorsUpon completion of this seminar,participants will be able to: Apply industry best practices of infrared thermographywithin their predictive maintenance program Apply effective techniques for operationand use of infrared cameras Interpret data correctly to increase equipment reliability800.922.2820www.NTTInc.com
OIL ANALYSISUnderstand terminology of oil analysis.Apply industry best practices ofoil analysis within their predictivemaintenance program.Apply effective techniques for operationand use of oil analysis equipment.Interpret data correctly to increaseequipment reliability.CLASS FORMAT:LectureSTANDARD CLASS SIZE:NTT recommends a class of no more than 35participants to obtain the best results.NTT TO PROVIDE: One day (8 contact hours) of on-site instructionTextbooksClassroom consumablesCompletion certificatesCourse syllabus, outline, table ofcontents, or training objectives Shipping and instructor travel logisticsCLIENT PROVIDES: Classroom of 500 square feet or greater Projection screen, white board and/or flip chart(s)WHO SHOULD ATTEND: TrainingProduction ManagersMaintenance ManagersFacilities ManagersElectrical & Mechanical Maintenance ManagersMaintenance TechniciansBuilding EngineersTechnicians and MechanicsSafer Workers. Stronger Companies. 800.922.2820 www.nttinc.com
OIL ANALYSISCOURSE AGENDALUBRICATION FUNDAMENTALSOIL TESTING & ANALYSIS The functions of a lubricant Additives and Their Functions Reasons for Performing Oil Analysis Common Oil Analysis TestsOIL ANALYSIS & CONDITIONS-BASEDMAINTENANCETARGETS, LIMITS, DIAGNOSTICS ANDDATA MANAGEMENT Reliability Centered Maintenance Setting Limits and Targets Interpreting and Applying Oil Analysis Results Monitoring TechniquesCONTAMINATION CONTROL Particle Contamination Moisture Contamination Field ContaminationOIL SAMPLING METHODS TrainingGUIDELINES FOR SELECTING ANDWORKING WITH COMMERCIAL OILANALYSIS Standards and best practicesSampling Locations on System ReturnsLive Zone SamplingSampling from Pressurized LinesSampling from Low Pressure LinesSampling from Wet SumpsDrop-Tube Vacuum SamplingOil Sampling FrequencySafer Workers. Stronger Companies. 800.922.2820 www.nttinc.com
ULTRASOUND TESTINGTeach maintenance personnel to operateultrasonic tester to enable a preventative/planned maintenance approach to systemmaintenance. Flaw detection an thicknessgauge of machinery material.This will help to evaluate a machine anddetect flaws that cannot be seen by thehuman eye. This helps improve predictivemaintenance programs and reducedowntime through flaw detection. Understanding terminology ofultrasonic testing. Apply industry best practices ofultrasonic testing within theirpredictive maintenance program. Apply effective techniques foroperation and use of ultrasonic testers. Interpret data correctly to increaseequipment reliability.CLASS FORMAT:Hands-onSTANDARD CLASS SIZE:NTT recommends a class of no more than 35participants to obtain the best results.NTT TO PROVIDE: One day (8 contact hours) of on-site instructionTextbooksClassroom consumablesCompletion certificatesCourse syllabus, outline, table ofcontents, or training objectives Shipping and instructor travel logisticsCLIENT PROVIDES: Classroom of 500 square feet or greater Projection screen, white board and/or flip chart(s)WHO SHOULD ATTEND: ElectriciansMechanicsApprentice and experienced HVAC techniciansLinemen & Utility workersWarehouse employeesMaintenance TechniciansEnergy management personnelPlant & facility maintenance techniciansBuilding engineers, managers & superintendentsPlant & facility managersStationary engineersSafety directorsSafer Workers. Stronger Companies. 800.922.2820 www.nttinc.com
ULTRASOUND TESTINGAGENDAINTRODUCTION TO ULTRASONIC TESTING Definitions of UltrasonicsHistory of UltraBasic Math reviewLevels of qualificationCertificationBASIC PRINCIPLES OF ACOUSTICS Sound wavesWave modesSound energyVelocity, frequency and wavelengthEQUIPMENT Dakota Ultrasonic TesterControl functionsFeaturesCalibrationAmprobe TMULD-300 Ultrasonic LeakDetector with TransmitterTRANSDUCER OPERATIONS AND THEORY Type of transducers Sensitivity, resolution and damping CouplantsBASIC ULTRASONIC TESTING METHODS Contact testing Immersion testing Air coupled ultrasonic applicationEVALUATION OF BASE MATERIALPRODUCT FORMS Material type Material form WeldsULTRASONIC TESTING APPLICATION Flat surface testing Curved surface testing Irregular surface testingTRANSDUCER CHARACTERISTICS Transducer characterization Recording of transducer beam profiles Analysis of transducer dataEVALUATION STANDARDS Typical approaches and standardsLEAK DETECTION The UT-300 transmits an ultrasonic signalfor non-pressurized applications Tests the “air-tightness” of weather seals,tanks, ovens, refrigerators, etc. Locating leaks in duct work Finds the ends of buried PVC pipes Detects any pressurized gas leak regardlessof type CFC’s, HFC’s, Nitrogen, etc.(unaffected by contaminants)PRINCIPLES OF ULTRASONICS Review of ultrasonic testing techniques Five basic elements of ultrasonic testingEQUIPMENT CALIBRATION Performance checks Instrumentation Straight beam / Angle beam calibrationSafer Workers. Stronger Companies. 800.922.2820 www.nttinc.com
VIBRATION ANALYSIS—BASIC FUNDAMENTALSCLASS FORMAT:This three day course was developed to assistindividuals who work in the field on variousequipment to learn how to use, read, and apply theinstruments and feedbacks related to vibration onrotating machinery.Lab classroomThe participant is able to “learn-by-doing” in thecourse; this knowledge can be transferred tothe workplace.Basic vibration theory will be discussed along withthe existing maintenance systems, predictive andpreventative maintenance programs, and proceduresfor a good condition monitoring system. You maynot walk out as an expert, however, you will leavethe seminar with a very good understanding of whatis necessary to make a valuable contribution at yourfacility.STANDARD CLASS SIZE:NTT recommends a course size of 12 participants toobtain the best results.NTT PROVIDES: 3-day on-site course—Lab Classroom formatOn-site instructionTextbooksClassroom consumablesCompletion certificatesShipping and instructor travel logistics.TOPICSVIBRATION BASICSCONCEPTS AND THEORIESCLIENT PROVIDES: Classroom of 500 square feet or greater Projection screen, white board and/or flip chart(s).INSTRUMENTSTYPICAL VIBRATION PROBLEMSTECHNIQUESMACHINE DIAGNOSTICSTRENDINGACOUSTICSFINAL REMARKS23Training800.922.2820 www.NTTInc.com
VIBRATION ANALYSIS—BASIC FUNDAMENTALSCOURSE AGENDA 3-Day Classroom LabVIBRATION BASICSWhat is vibration (causes and characteristics) Earthquakes and WindMusicAcousticsFinite Element AnalysisModal AnalysisVibration TestingShockGenerating VibrationMachine MonitoringHistoryCONCEPTS AND THEORIES OscillationMass, Spring, DamperSine WavesAmplitude, Frequency, PhaseRandom Vibrations and Shock PulseTime and Frequency DomainsVectorsDisplacement, Velocity, and AccelerationNatural Frequency and Resonant frequencyDampingMechanical ImpedanceIsolationCritical speedLife Cycle of MachineryINSTRUMENTS TrainingEars, Hands, and WatchTypes of vibration transducersCablesMeters and FiltersFFT analyzerSampling, Allasing, and WindowsAveragingZoomLinear and Log ScalingTriggersComparator Memory Data Loggers and Computers Ancillary InstrumentsTYPICAL VIBRATION PROBLEMS Sources of rsVane PassingFanMotor VibrationCavitationOil WhirlPipingBent Shaft and Bowed RotorLoosenessBelts and pulleysStructural VibrationFoundationsSympathetic VibrationsMachinery Soft FootAssembly VariablesBeatsTurbulenceReciprocating MachinesTurbomachineryTorsional VibrationsCase HistoriesTECHNIQUES Amplitude MappingLoose Part MonitoringTransducer Mounting MethodsPhase RelationshipBode, Polar, and Waterfall PlotsTest for ResonanceSand PatternsDeflection- Mode ShapesUncoupled Driver800.922.2820 www.NTTInc.com
VIBRATION ANALYSIS—BASIC FUNDAMENTALSCOURSE AGENDA 3-Day Classroom LabTECHNIQUES, continued OrbitsSynchronous Time AverageCrack DetectionTime Wave FormMACHINE DIAGNOSTICS Narrow Band Frequency Standards Acceptance TestingTRENDING Managing MaintenancePreventive vs Predictive MaintenanceScreensSetting upPermanent MonitoringACOUSTICS The Physics of SoundMachinery NoiseSound MeasurementsBuildingsCase HistoriesFINAL REMARKS Safety Precautions Approaching a Vibration Problem Do’sTraining800.922.2820 www.NTTInc.com
Teach maintenance personnel to operate ultrasonic tester to enable a preventative/ planned maintenance approach to system maintenance. Flaw detection an thickness gauge of machinery material. This will help to evaluate a machine and detect flaws that cannot be seen by the human eye. This helps improve predictive maintenance programs and reduce