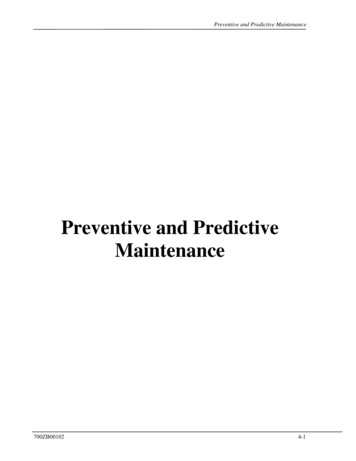
Transcription
Preventive and Predictive MaintenancePreventive and PredictiveMaintenance700ZB001024-1
Preventive and Predictive MaintenancePreventive/Predictive MaintenanceThe guiding principle of PPM is the regular and systematic application of engineering knowledge andmaintenance attention to equipment and facilities to ensure their proper functionality and to reduce theirrate of deterioration. In addition to dedicated engineering, PPM encompasses regular examination,inspection, lubrication, testing and adjustments of equipment without prior knowledge of equipmentfailure. PPM also provides the framework for all planned maintenance activity, including the generationof planned work orders to correct potential problems identified by inspection. The result is a proactive(rather than a reactive) environment, optimizing equipment performance and life.Properly developed PPM programs are engineered efforts, which optimize the relationship betweenequipment ownership and operating profits by balancing cost of maintenance with cost of equipmentfailure, and associated production losses. Equipment ownership cost is a function of three factors:purchase price, equipment life and maintenance cost. Total maintenance cost is the sum of material andlabor cost required to repair the item, the cost of preventive maintenance to avoid repairs, plus the cost oflost production while the unit is out of service for repairs. PPM includes actions which extend the life ofequipment and avoid unnecessary failures by substituting selective programmed effort for “fix it when itfails” maintenance.Actions that extend the life of equipment include: lubrication, cleaning, adjusting and the replacement ofminor components like drive belts, gaskets, filters, etc. Actions that avoid unnecessary failure includetimely, consistent equipment inspection and the aggressive use of nondestructive testing techniques suchas vibration analysis, infrared testing, oil analysis and other techniques.Predictive maintenance is the complement of preventive maintenance. Through the utilization of variousnondestructive testing and measuring techniques, predictive maintenance determines equipment statusbefore a breakdown occurs. With predictive devices currently available, it is incumbent uponmaintenance organizations to include the process of predictive maintenance in their maintenanceprograms.A total PPM program is absolutely essential to an efficient, reliable and safe production process. Benefitsare direct and substantial, including: high product quality, long machine life, avoidance of work stoppage,high safety, high morale and fewer frustrations. There are five essential requirements:1. Top management leadership and absolute commitment.2. Compliance and discipline. PPM must be a normal part of schedule and capacity determination.3. Process operators should be involved and perform daily maintenance checks.4. The “true cost of poor maintenance,” which is several times initial estimates must be thoroughlyunderstood by all.5. Good PPM practices must be instituted immediately to enable the facility to achieve an efficientproduction system that delivers high quality goods on time, every time.Although treated as separate elements, preventive/predictive maintenance, Reliability Engineering,equipment history and functional pride and quality assurance are inextricably supportive—each to theothers. Success of the preventive/predictive maintenance program is dependent upon the existence of theother three elements. While planning and scheduling assure the effective utilization of resources tosustain an established proactive maintenance program, it is these four elements working in concert thatdefine the proactive program.Logically, an effective maintenance program, supported by these four essential elements, begins withequipment history. Then, based upon this factual information foundation, Reliability Engineering beginsthe development and subsequent refinement of a preventive/predictive maintenance program. An700ZB001024-2
Preventive and Predictive Maintenanceeffective scheduling function assures that PPM routines are punctually performed as they become due, asfollows:A. The planning and scheduling program provides a structure into which PPM routines are woven.If PPM routines are continually shoved to one side, a proactive environment will never becomereality.As scheduling contributes to the success of preventive maintenance so preventive maintenancecontributes to the success of scheduling. The greatest obstacle to effective scheduling is thespasmodic occurrence of emergency breakdown repairs. Through scheduled inspections ofequipment and repairs during scheduled downtime, emergency breakdowns can be nearlyeliminated; thus the cause of interruptions to the planned schedule is removed or reduced to aminimum.B. Program consistency and punctuality is a must. PPM must be viewed and conducted as anongoing and controlled experiment to be continually nurtured and refined. It requires dedicated,uniquely talented effort (the maintenance engineer).700ZB001024-3
Preventive and Predictive MaintenanceProgram results will carry to the bottom-line in the form of:1. Reductions in the total cost of maintenance2. Fewer urgent and emergency interruptions to operations due to equipment breakdowns3. Level workloads and a stabilized work force4. Reductions in the total labor needed to maintain facilities in the required condition5. Controlled reductions in the inventory of materials and spare parts6. Increases in the volume of work that can be planned and scheduled repetitively, and a decrease inhigh priority, randomly occurring and unscheduled work7. Reduced unnecessary damage to equipmentPreventive/Predictive MaintenanceIndicators of Ineffective PPM1. Low equipment utilization due to unscheduled stoppages2. High wait or idle time for machine operators during outages3. High scrap and rejects indicative of quality problems4. Higher than normal repair costs due to neglect of proper lubrication, inspections or service.5. Decrease in the expected life of capital investments due to inadequate maintenanceEffective PPM Requires:1. Top management understanding of the true cost of poor maintenance, which is several timesinitial estimate2. Sustained management leadership and absolute commitment3. Knowledge of equipment/process conditions required to yield quality, output, safety, andcompliance standardsA. One cannot determine what problems exist until knowing what conditions are proper4. PPM and other programmed maintenance must be a normal part of schedule and capacitydetermination. Management must insure that PPM is never delayed.A. PPM must be conducted as a Controlled Experiment1. Plan2. Do3. Evaluate4. RefineB. Weekly adherence to a balanced PPM schedule700ZB001024-4
Preventive and Predictive MaintenanceThe PM Program a“Controlled Experiment”HighLost ProductionCaused by FailuresLack of PM ntenance CostsMaintenanceChallenge(A ControlledExperiment)OpratingBudgetTotal Maintenance CostCost of RepairsCost of PMLowDo not attempt toimmediately PM everythingApply A-B-C Analysis ToEquipment CriticalityBuild upon earlysuccesses.LowLevel of MaintenanceReactive MaintenanceExcessive Repairs & FailuresHighExcessive PMNo Failures & No RepairsTotal Maintenance Related Cost Cost of PM Cost of Repairs Cost of Production* Excessive TinkeringLosses caused by Failures& PM TimeManage Maintenance – Do not allow it to control Operations!PM does not achieve reliability, it preserves reliability!5. Dedicated staffing is preferable6. Operator should participate in daily machine checks7. Efficient PPM routes8. Effective PM checklists defining program required limits of equipment condition9. Adequate Equipment Records and Equipment Histories10. Three phasesA. Detection—the key elementB. Analysis—defines the specific problem from which the symptom originatesC. Correction—the return of the PPM investment700ZB001024-5
Preventive and Predictive MaintenanceClassification of Maintenance WorkProactive MaintenancePPMPredictiveRegular examinationof equipment to determinewhat corrective actionsshould be performed withbest timing1. Vibration analysis2. Thermography3. Oil Sampling4. Ultrasound5. Electric PowerQuality AnalysisPlannedPreventiveRegular examinationof equipment for defectsby means of PM checklistsand sensory perception1. Lubrication2. Cleaning3. Adjustments4. Testing1. Repair of defectsfound by1. ComponentexaminationReplacement 2. Component2. Programmedreconditioningoverhauls at 3. Manufacture offixed intervalsspares3. Corrective4. Construction5. Replacement6. Salvage Operations7. Painting11. A beginning—Start PPM practices immediately if you expect to establish an efficientoperating system. One that delivers high quality output, on time, every time.A. Start smallB. Sell expansion upon early successesC. Therefore select your early efforts wiselyD. Applied A-B-C analysis to selection of equipment12. Focus On the Correction as well as The InspectionA. Inspection Is The InvestmentB. Correction Is The Return On The Investment13. Management Follow-upPPM Increases1. Maintenance staffing2. Repair parts costsA. Preventive tends to increase parts costB. Predictive reduces parts cost3. Volume of work that can be planned and scheduled repetitively4. Work load leveling5. Equipment reliability and uptime700ZB001024-6
Preventive and Predictive MaintenancePPM Decreases1. Scrap and reject costs2. Downtime costs3. Cost of lost sales volume4. Total cost of maintenance5. Urgent or emergency interrupts due to breakdowns6. Unnecessary damage to equipment7. High priority, randomly occurring unscheduled work8. Material and spare parts inventories9. Total labor required to maintain the facility700ZB001024-7
Preventive and Predictive MaintenancePrope r Staffing isDepende nt Upon Workload150DeferredMaintenanceRequirement 40 PositionsUrgent ResponseRequirement 40 PositionsDeferredMaintenanceRequirement 40 PositionsUrgent ResponseRequirement 30 Positions90Internal StaffingRequired Staffing - Reactive Environment130Capital ProgramRequirement 35 PositionsNODeferredMaintenanceCapital ProgramRequirement 35 PositionsUrgent ResponseRequirement 20 quiredCapital ProgramRequirement 35 PositionsUrgent Response10 PositionsSteady State Backlog Relief ofPlannable Work 75 Positions15Required Staffing - Proactive EnvironmentCapital ProgramRequirement 35 PositionsIn-House StaffingExternal Staffing205PPM and Other Routine Activities 15 Positions0700ZB001021st Phase2nd Phase3rd Phase4th Phase4-8
Preventive and Predictive MaintenancePPM Is Comprised Of1. Proper organization2. Proper operation of equipment3. The proper lubricants, in the right quantities, in the right location, at the proper time4. Predicting wear and deterioration by regularly checking, measuring and adjustingA. Regular inspection to identify small repairs before they become major repairsB. Predictive techniques to replace components just before they faila. Vibration monitoring and analysisb. Infrared inspectionc. Sound detectiond. Lubrication and oil samplinge. Etc.5. Replacement of components on a regular basis before they fail6. Correction of potential failures when inspection indicates the need7. Overhauling equipment periodically to upgrade general equipment condition8. Reliability engineering to reduce or eliminate repetitive failures9. Reliability engineering to minimize failures through adjustments to the PPM program700ZB001024-9
Preventive and Predictive MaintenancePreventive Maintenance ImpactBreakdown MaintenanceAnnual Overhaul OnlyYear XYear YNewWith PMProgrammed MaintenanceEconomic LifeAnnual Overhaul OnlyEconomic LifeEconomic LifeEconomic Limit on Equipment ConditionBreakdown MaintenanceEquipment ConditionProgrammed PM MaintenanceYear ZReplacementTimeProactive MaintenanceProactive Maintenance Time Line(An Investment In Reliability Excellence)140Total Maintenance Cost ( MM)Total Maintenance CostAverage CostPrevious Years12010080Reliability ExcellenceCostReduction60Reactive Maintenance40Proactive Maintenance200Year123456Solid solutions require time foresight patience sacrifices and discipline. But they have large long-runpayoffs. The basic difference between solid solutions and quick fixes is the difference between investingin the future and mortgaging it. To invest too little in the pursuit of "Reliability Excellence" only leads tofailure. Like any investment, the Maintenance Investment precedes the Proactive Return.700ZB001024-10
Preventive and Predictive MaintenancePredictive MaintenancePredictive Maintenance (PdM) monitors the performance and condition of equipment or systems todetect/trend degradation. Techniques include:1. Vibration monitoring2. Thermographic inspection3. Oil analysis4. Visual inspection5. Shock pulse6. Ultrasonic leak detectors7. Electrical insulationA. Megger testsB. Surge comparison8. Performance testing9. Wear and dimensional measurements10. Signature analysis, time and frequency domain11. Nondestructive testingA. UltrasonicB. Borescope inspectionsC. Eddy currentWhy perform predictive maintenance?1. Monitoring detects degrading conditions2. Most cost failures result from degrading conditions3. Trending degradation permits planning for repair4. Trending degradation permits scheduling repairWhat are the concerns of predictive maintenance?1. Doing only predictive maintenance is living close to the edge2. Takes courage to make the initial calls for repairs3. Must be an adjunct to a sound preventive maintenance programWhen should you consider a predictive maintenance program?1. After the preventive maintenance program is established2. Only with corporate/management support700ZB001024-11
Preventive and Predictive MaintenanceTypical Predictive TechniquesMonitoringTechniquesUseProblem DetectionVibrationRotating machinery, e.g., pumps,turbines, com
maintenance organizations to include the process of predictive maintenance in their maintenance programs. A total PPM program is absolutely essential to an efficient, reliable and safe production process. Benefits are direct and substantial, including: high product quality, long machine life, avoidance of work stoppage, high safety, high morale and fewer frustrations. There are five essential .