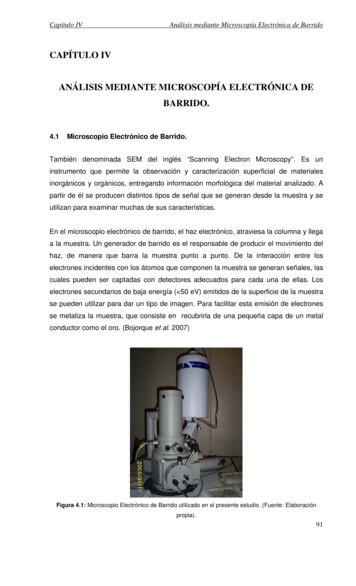
Transcription
Capítulo IVAnálisis mediante Microscopía Electrónica de BarridoCAPÍTULO IVANÁLISIS MEDIANTE MICROSCOPÍA ELECTRÓNICA DEBARRIDO.4.1Microscopio Electrónico de Barrido.También denominada SEM del inglés “Scanning Electron Microscopy”. Es uninstrumento que permite la observación y caracterización superficial de materialesinorgánicos y orgánicos, entregando información morfológica del material analizado. Apartir de él se producen distintos tipos de señal que se generan desde la muestra y seutilizan para examinar muchas de sus características.En el microscopio electrónico de barrido, el haz electrónico, atraviesa la columna y llegaa la muestra. Un generador de barrido es el responsable de producir el movimiento delhaz, de manera que barra la muestra punto a punto. De la interacción entre loselectrones incidentes con los átomos que componen la muestra se generan señales, lascuales pueden ser captadas con detectores adecuados para cada una de ellas. Loselectrones secundarios de baja energía ( 50 eV) emitidos de la superficie de la muestrase pueden utilizar para dar un tipo de imagen. Para facilitar esta emisión de electronesse metaliza la muestra, que consiste en recubrirla de una pequeña capa de un metalconductor como el oro. (Bojorque et al. 2007)Figura 4.1: Microscopio Electrónico de Barrido utilizado en el presente estudio. (Fuente: Elaboraciónpropia).91
Capítulo IVAnálisis mediante Microscopía Electrónica de Barrido4.1.1 Interacción haz incidente con muestra en SEM.Cuando el haz de electrones choca contra la muestra, ocurren interacciones entredichos electrones y los átomos que componen la muestra. De allí surgen señales talescomo: electrones secundarios, electrones retrodifundidos, rayos x ia.Todasestasseñalesseproducensimultáneamente pero cada una de ellas son captadas por detectores diferentes.El microscopio electrónico de barrido puede estar equipado con diversos detectores,entre los que se pueden mencionar: un detector de electrones secundarios para obtenerimágenes de alta resolución SEI (Secundary Electron Image), un detector de electronesretrodispersados que permite la obtención de imágenes de composición y topografía dela superficie BEI (Backscattered Electron Image), y un detector de energía dispersivaEDS ( Energy Dispersive Spectrometer) permite colectar los Rayos X generados por lamuestra y realizar diversos análisis e imágenes de distribución de elementos ensuperficies pulidas.El haz de electrones se puede concentrar en una zona diminuta ( 20 Å) que puedebarrer la superficie del espécimen al ser reflectado por bobinas adecuadas. Loselectrones secundarios se detectan por encima del espécimen y la imagen muestra laintensidad de los electronessecundarios emitidos por las diferentes partes de lamuestra.El detector capta una señal y las convierte en una señal electrónica que es proyectadaen un tubo de rayos catódicos (CRT). El barrido del haz está sincronizado con el barridodel CRT y produce una relación uno a uno entre puntos de la muestra y puntos en elCRT.4.1.2 Aplicaciones del Microscopio Electrónico de Barrido en Hormigones y áridos.-Mineralogía de cementos: clínquer, alitas, etc.-Mineralogía de áridos: granito, calizas, etc.-Crecimiento cristalinos, texturas, figuraciones, porosidades, fragilidad, etc.-Identificación de fases reactivas y productos expansivos.-Apreciación de interferencia árido-pasta e índice de vacíos.-Composición microquímica.-Cuantificación de parámetros de caracterización.92
Capítulo IVAnálisis mediante Microscopía Electrónica de Barrido4.2 Análisis de Microscopía Electrónica.4.2.1 Preparación de Muestras.Como primer requisito las muestras deben estar exentas de líquido, ser lo mas planasposibles para que así se genere una imagen más homogénea y ademáscuando se desea visualizar una muestra en un microscopio electrónico de barrido éstadebe ser conductora ya que, de no ser así, se carga durante la irradiación por unaacumulación de carga que desvía el haz electrónico y, como consecuencia de elloaparecen distorsiones en la imagen. Una solución a este problema es recubrir lamuestra con una película conductora, de espesor comprendido entre 10 y 25 nm.La elección del material con el que se va a recubrir la muestra dependefundamentalmente del estudio que se va a realizar. Así, para la observación deimágenes de electrones secundarios el oro y el oro-paladio son los materiales queconducen a los mejores resultados; al ser elementos pesados, producen mayor emisión.Cuando lo que se pretende es realizar un estudio micro analítico es recomendableemplear carbono. El bajo número atómico de este elemento lo hace prácticamentetransparente a los rayos X emitidos por la muestra.En el presente trabajo se requiere de los dos recubrimientos ya que las muestrasserán estudiadas mediante imágenes para conocer su morfología y también serealizarán microanálisis químicos por energía dispersiva de rayos x.4.2.1.1 Recubrimiento de muestras con oro.Se utiliza cuando las muestras sólo serán analizadas por concepto de imágenes sinincluir la obtención de espectro de Rx.En la figura se muestra lo que se conoce como "sputtering". Consiste en una fuente dealimentación en corriente continua regulable de 1 a 3 KV, conectada por una parte auna tarjeta de oro y por otra parte al portamuestras. El conjunto va acoplado a unabomba de vacío. La introducción de un gas tal como el argón en la campana de vacíoprovoca que los átomos de argon impacten en la tarjeta de oro y se desprendan átomosde dicha tarjeta que son atraídos hacia la muestra en la cual quedan depositados enforma de películas metálicas proporcionando un espesor de recubrimiento que dependedel tiempo de exposición.93
Capítulo IVAnálisis mediante Microscopía Electrónica de BarridoFigura 4.2: Maquina utilizada para sombrear las muestras con oro. (Fuente: Elaboración propia)Figura 4.3: Muestras de mortero con adición de nanosílice recubiertas en oro, dispuestas para seranalizadas en SEM. (Fuente: Elaboración propia)4.2.1.2 Recubrimiento de muestras con carbono.Se utiliza carbono porque es el elemento más transparente para los Rx. El metalizadorde carbono esta formado por dos electrodos conectados a una fuente de bajo voltaje yalta intensidad, entre ellos se ubica una barra de carbono que termina en forma decúspide, la cual se evapora a medida que pasa la corriente y a la vez rocía a la muestracon una fina capa de carbono, todo el sistema funciona aislado en vacío.94
Capítulo IV4.3Análisis mediante Microscopía Electrónica de BarridoMuestras caracterizadas en Estudio de Microscopía Electrónica.Para el análisis de microscopía electrónica por medio de imágenes y de microanálisisquímico se seleccionaron un total de 10 probetas:-Las 4 primeras corresponden a las muestras con menor y mayor pérdida dematerial, luego de ser sometidas a inmersión en Sulfato de Magnesio y con susrespectivas muestras controles (no ensayadas).Tabla 4.1: Muestras con menor y mayor pérdida de material y sus respectivas controles queserán analizadas mediante SEM.CLASIFICACIÓNDESCRIPCIÓNMuestra con menor pérdida de materialMuestra Control BuenaMuestra con mayor pérdida de materialMuestra Control MalaA/C 0.55 1.5% T4A/C 0.55 1.5% T0A/C 0.65 0.5% T6A/C 0.65 0.5% T0Fuente: Elaboración Propia.-Las 3 siguientes pertenecen a un grupo con iguales características de razón A/Cy adición de nanosílice que registró daño creciente en tres tiempos consecutivos.Tabla 4.2: Grupo de muestras con daño creciente que serán analizadas mediante SEM.CLASIFICACIÓNDESCRIPCIÓN1º muestra con daño creciente A/C 0.65 0.5% T22º muestra con daño creciente A/C 0.65 0.5% T33º muestra con daño creciente A/C 0.65 0.5% T4Fuente: Elaboración Propia.-Las 3 últimas pertenecen a otro grupo con iguales características de razón A/C yadición de nanosílice que registró daño decreciente en tres tiemposconsecutivos.Tabla 4.3: Grupo de muestras con daño decreciente que serán analizadas mediante SEM.CLASIFICACIÓNDESCRIPCIÓN1º muestra con daño decreciente A/C 0.55 1.0% T32º muestra con daño decreciente A/C 0.55 1.0% T43º muestra con daño decreciente A/C 0.55 1.0% T5Fuente: Elaboración Propia.95
Capítulo IVAnálisis mediante Microscopía Electrónica de BarridoMuestra con Menor pérdida de material: A/C 0.55 1.5% T4Figura 4.4: Imagen muestra con Menor Pérdida de material a Escala 1000x. Superficie en gran partehomogénea en distribución partículas que cubren incluso límites de grano. (Fuente: Elaboración propia)Figura 4.5: Imagen muestra con Menor Pérdida de material a Escala 5000x. Mayor detalle de lamorfología expuesta en la imagen anterior, con las distintas fases del concreto y distribución departículas. (Fuente: Elaboración propia)96
Capítulo IVAnálisis mediante Microscopía Electrónica de BarridoFigura 4.6: Imagen muestra con Menor Pérdida de material a Escala 12000x. Zona con detalle deformación de Etringita en la muestra de concreto, crecimiento y distribución homogénea. (Fuente:Elaboración propia)Figura 4.7: Imagen muestra con Menor Pérdida de material a Escala 60000x. Detalle más fino que fotoanterior, donde se aprecia la distribución y morfología de crecimiento de cristales en el concreto. (Fuente:Elaboración propia)97
Capítulo IVAnálisis mediante Microscopía Electrónica de BarridoMuestra Control Buena: A/C 0.55 1.5% T0Figura 4.8: Imagen muestra Control Buena a Escala 1000x. Superficie con cristales de concreto. (Fuente:Elaboración propia)Figura 4.9: Imagen muestra Control Buena a Escala 5000x. Superficie muestra morfología y topografíairregular con cristales de distinto tamaño. (Fuente: Elaboración propia)98
Capítulo IVAnálisis mediante Microscopía Electrónica de BarridoFigura 4.10: Imagen muestra Control Buena a Escala 12000x. Detalle de foto anterior en que se apreciandistintas morfologías y fases de los cristales y estructura del concreto (Carbonatos y Etringita). (Fuente:Elaboración propia)Muestra con Mayor pérdida de material: A/C 0.65 0.5% T6Figura 4.11: Imagen muestra con Mayor Pérdida de material a Escala 1000x.Distribución Heterogéneade partículas en la muestra con zonas sin cubrir debido a textura y topografía de cristales del material.(Fuente: Elaboración propia)99
Capítulo IVAnálisis mediante Microscopía Electrónica de BarridoFigura 4.12: Imagen muestra con Mayor Pérdida de material a Escala 5000x.Detalle de morfología departículas y cristales de concreto, con sustratos y fases intermedias bajo las partículas. (Fuente:Elaboración propia)Figura 4.13: Imagen muestra con Mayor Pérdida de material a Escala 12000x.Desagregación departículas en la superficie con distintos tamaños de aglomeración. (Fuente: Elaboración propia)100
Capítulo IVAnálisis mediante Microscopía Electrónica de BarridoMuestra Control Mala: A/C 0.65 0.5% T0Figura 4.14: Imagen muestra Control Mala a Escala 1000x. Muestra de topografía y tamaños de cristalesirregular, además de límites de granos irregulares. (Fuente: Elaboración propia)Figura 4.15: Imagen muestra Control Mala a Escala 5000x. Superficie con topografía muy irregular encuanto a cristales, límites de grano y textura de la muestra. (Fuente: Elaboración propia)101
Capítulo IVAnálisis mediante Microscopía Electrónica de BarridoFigura 4.16: Imagen muestra Control Mala a Escala 12000x. Detalle foto anterior, que caracterizamorfología de la muestra a nivel superficial. (Fuente: Elaboración propia)Grupo de Muestras con Daño Creciente (en orden de menor a mayor daño)1ª muestra con daño creciente: A/C 0.65 0.5% T2Figura 4.17: Imagen 1ª muestra con daño creciente a Escala 1000x. Aglomeración de partículas condistintos tamaños sobre los cristales superficiales del concreto, hay distribución heterogénea. Se apreciaigualmente la interfase entre los cristales. (Fuente: Elaboración propia)102
Capítulo IVAnálisis mediante Microscopía Electrónica de BarridoFigura 4.18: Imagen 1ª muestra con daño creciente a Escala 5000x. Se observan partículas de tamañode 1 a 8 micras sobre la superficie del concreto, que cubren totalmente la superficie de la muestra, conuna distribución homogénea. (Fuente: Elaboración propia)Figura 4.19: Imagen 1ª muestra con daño creciente a Escala 12000x. Detalle de foto anterior con mayorresolución. Se observan partículas agrupadas preferentemente en zonas de límites de grano y sobrecristales de concreto. Hay otras zonas con menor número de partículas (superior) y cristales no cubiertosque dan cuenta de un efecto superficial del medio ensayado. (Fuente: Elaboración propia)103
Capítulo IVAnálisis mediante Microscopía Electrónica de Barrido2ª muestra con daño creciente: A/C 0.65 0.5% T3Figura 4.20: Imagen 2ª muestra con daño creciente a Escala 1000x. Fina distribución de partículas sobrela superficie del concreto. Límites de grano parcialmente cubiertos, según morfología y textura decristales. (Fuente: Elaboración propia)Figura 4.21: Imagen 2ª muestra con daño creciente a Escala 5000x. Detalle foto anterior, en que resaltaforma de la distribución de las partículas a nivel de superficie. Hay zonas en que no se fijan o se handesprendido las partículas que corresponden a límites de grano del concreto. (Fuente: Elaboraciónpropia)104
Capítulo IVAnálisis mediante Microscopía Electrónica de BarridoFigura 4.22: Imagen 2ª muestra con daño creciente a Escala 12000x. Detalle con mayor resolución deldepósito de partículas a nivel de superficie, con tamaños de 1 a 9 micras aproximadamente. Laspartículas de fijan con distintos sustratos y tamaños, pero dejando cristales que no quedan cubiertos. Laszonas claras pueden corresponder a partículas con mayor estado de oxidación. (Fuente: Elaboraciónpropia)3ª muestra con daño creciente: A/C 0.65 0.5% T4Figura 4.23: Imagen 3ª muestra con daño creciente a Escala 1000x. Morfología de aglomeración departículas en superficie de cristales de concreto, en forma de sustratos y dejando zonas no cubiertas(más oscuras) dependiendo de topografía y textura cristales. (Fuente: Elaboración propia)105
Capítulo IVAnálisis mediante Microscopía Electrónica de BarridoFigura 4.24: Imagen 3ª muestra con daño creciente a Escala 5000x. En la superficie se observancristales del concreto y un estado intermedio de crecimiento de etringita. La morfología de partículas esirregular en la superficie cubriendo los límites de grano. (Fuente: Elaboración propia)Figura 4.25: Imagen 3ª muestra con daño creciente a Escala 12000x. Detalle foto anterior con mayorresolución donde se observa crecimiento de Etringita, sustratos localizados de partículas, dejandocristales sin cubrir en la superficie de la muestra. (Fuente: Elaboración propia)106
Capítulo IVAnálisis mediante Microscopía Electrónica de BarridoGrupo de Muestras con Daño Decreciente (en orden de mayor a menor daño)1ª muestra con daño decreciente: A/C 0.55 1.0% T3Figura 4.26: Imagen 1ª muestra con daño decreciente a Escala 1000x.Cristales casi completamentecubiertos con partículas. Hay zonas con menos densidad de partículas y zonas en que es posiblevisualizar límites parciales de grano. (Fuente: Elaboración propia)Figura 4.27: Imagen 1ª muestra con daño decreciente a Escala 5000x. Se aprecia morfología superficialde deposición de partículas de concreto sobre cristales, con una distribución heterogénea. (Fuente:Elaboración propia)107
Capítulo IVAnálisis mediante Microscopía Electrónica de BarridoFigura 4.28: Imagen 1ª muestra con daño decreciente a Escala 12000x. Las partículas cubrenparcialmente la superficie del concreto, ya que hay cristales no cubiertos. Las partículas finas sedepositan preferentemente en bordes de cristales. (Fuente: Elaboración propia)2ª muestra con daño decreciente: A/C 0.55 1.0% T4Figura 4.29: Imagen 2ª muestra con daño decreciente a Escala 1000x. Morfología de distribución departículas en el concreto, con distintos sustratos y que cubre casi completamente la muestra, incluidos loslímites de grano. (Fuente: Elaboración propia)108
Capítulo IVAnálisis mediante Microscopía Electrónica de BarridoFigura 4.30: Imagen 2ª muestra con daño decreciente a Escala 5000x. La deposición de partículas espreferentemente en los bordes de los cristales del concreto y minimamente en toda la superficie. (Fuente:Elaboración propia)Figura 4.31: Imagen 2ª muestra con daño decreciente a Escala 12000x. Detalle foto anterior dedistribución de partículas en la muestra. Topografía irregular y los límites de grano parcialmentecubiertos. (Fuente: Elaboración propia)109
Capítulo IVAnálisis mediante Microscopía Electrónica de BarridoFigura 4.32: Imagen 2ª muestra con daño decreciente a Escala 23000x. Se muestra detalle de como laspartículas se van depositando en los límites de grano con mayor resolución del SEM. (Fuente:Elaboración propia)3ª muestra con daño decreciente: A/C 0.55 1.0% T5Figura 4.33: Imagen 3ª muestra con daño decreciente a Escala 1000x. Se observa toda la muestracubierta con partículas aglomeradas de distintos tamaños. (Fuente: Elaboración propia)110
Capítulo IVAnálisis mediante Microscopía Electrónica de BarridoFigura 4.34: Imagen 3ª muestra con daño decreciente a Escala 5000x. Se aprecia una distribuciónheterogénea de partículas en la superficie del concreto, cubriendo parcialmente límites de grano delmaterial. (Fuente: Elaboración propia)Figura 4.35: Imagen 3ª muestra con daño decreciente a Escala 12000x. Detalle de foto anterior conmayor resolución que muestra morfología de sustratos de partículas sobre el concreto. (Fuente:Elaboración propia)111
Capítulo IVAnálisis mediante Microscopía Electrónica de Barrido4.4 Microanálisis Químico por Energía Dispersiva de Rayos X (EDAX).Muestra con Menor pérdida de material: A/C 0.55 1.5% T4MicroanálisisFigura 4.36: Microanálisis Muestra con Menor Pérdida de material. Indica la composición química de lamuestra, los elementos detectados en mayor cantidad son Calcio, Silicioy Aluminio. (Fuente:Elaboración propia)LinescanFigura 4.37: Linescan de Muestra con Menor Pérdida de material. Análisis químico a lo largo de unalínea, los distintos colores indican la distribución de fases y constituyentes. Además se presentan losgráficos correspondientes a los elementos que se presentan en mayor cantidad Silicio y Aluminio, el restoen trazas más pequeñas, pero distribuidos en toda la muestra. (Fuente: Elaboración propia)112
Capítulo IVAnálisis mediante Microscopía Electrónica de BarridoMappingFigura 4.38: Distribución Mapping elementos químicos en la superficie de Muestra con Menor Pérdida dematerial. Las zonas claras, en imágenes a color, denotan una presencia más marcada del elemento. Eneste caso, se observa Silicio rodeando y cubriendo cristales de Aluminio y Calcio en la muestra. (Fuente:Elaboración propia)113
Capítulo IVAnálisis mediante Microscopía Electrónica de BarridoMuestra Control Buena: A/C 0.55 1.5% T0MicroanálisisFigura 4.39: Microanálisis Muestra Control Buena. Se detectan los elementos presentes en mayorcantidad, que son Sílice, Calcio y Aluminio, todos en estado de óxido. (Fuente: Elaboración propia)LinescanFigura 4.40: Linescan de Muestra Control Buena. Análisis químico a lo largo de una línea horizontaltrazada sobre la muestra con una extensión de 400µm. En los gráficos correspondientes a los elementosquímicos se observa una distribución más o menos homogénea. (Fuente: Elaboración propia)114
Capítulo IVAnálisis mediante Microscopía Electrónica de BarridoMappingFigura 4.41: Distribución Mapping elementos químicos en la superficie de Muestra Control Buena. Seobservan Silicatos rodeando los cristales de Calcio y Aluminio en la muestra. (Fuente: Elaboraciónpropia)115
Capítulo IVAnálisis mediante Microscopía Electrónica de BarridoMuestra con Mayor pérdida de material: A/C 0.65 0.5% T6MicroanálisisFigura 4.42: Microanálisis Muestra con Mayor Pérdida de material. Mayor detección de Magnesio yCalcio. Hay presencia de cloro que puede provenir del agua utilizada en el ensayo o del agua de lamezcla del concreto. (Fuente: Elaboración propia)LinescanFigura 4.43: Linescan de Muestra con Mayor Pérdida de material. Se observa gran cantidad de cristalesde calcio en el centro, sulfuro y aluminio en menor cantidad. (Fuente: Elaboración propia)116
Capítulo IVAnálisis mediante Microscopía Electrónica de BarridoMappingFigura 4.44: Distribución Mapping elementos químicos en la superficie de Muestra con Mayor Pérdida dematerial. Se observa zona de cristales de Calcio rodeado por Oxido de Magnesio. (Fuente: Elaboraciónpropia)117
Capítulo IVAnálisis mediante Microscopía Electrónica de BarridoControl Mala: A/C 0.65 0.5% T0MicroanálisisFigura 4.45: Microanálisis Muestra Control Mala. Mayor Presencia de Calcio, Silicio y Aluminio en laestructura del concreto. (Fuente: Elaboración propia)LinescanFigura 4.46: Linescan de Muestra Control Mala. Análisis químico a lo largo de una línea horizontaltrazada sobre la muestra con una extensión de 600µm. (Fuente: Elaboración propia)118
Capítulo IVAnálisis mediante Microscopía Electrónica de BarridoMappingFigura 4.47: Distribución Mapping elementos químicos en la superficie de Muestra Control Mala. Destacauna zona de Sílice rodeada de Calcio y Aluminio. (Fuente: Elaboración propia)119
Capítulo IVAnálisis mediante Microscopía Electrónica de BarridoGrupo de Muestras con Daño Creciente (en orden de menor a mayor daño)1ª muestra con daño creciente: A/C 0.65 0.5% T2MicroanálisisFigura 4.48: Microanálisis de 1ª Muestra con Daño Creciente. Se detecta Calcio, Sílice y Aluminioprincipalmente, y el resto de los elementos químicos se presentan en trazas menores. (Fuente:Elaboración propia)LinescanFigura 4.49: Linescan de 1ª Muestra con Daño Creciente. Se destaca presencia de Magnesio a lo largode toda la muestra. (Fuente: Elaboración propia)120
Capítulo IVAnálisis mediante Microscopía Electrónica de BarridoMappingFigura 4.50: Distribución Mapping elementos químicos en la superficie de 1ª Muestra con DañoCreciente. Se presenta una distribución homogénea de Silicio, Aluminio y Calcio, en forma de óxidos enla muestra. (Fuente: Elaboración propia)121
Capítulo IVAnálisis mediante Microscopía Electrónica de Barrido2ª muestra con daño creciente: A/C 0.65 0.5% T3MicroanálisisFigura 4.51: Microanálisis de 2ª Muestra con Daño Creciente. Hay presencia de Calcio, silicio yMagnesio principalmente. (Fuente: Elaboración propia)LinescanFigura 4.52: Linescan de 2ª Muestra con Daño Creciente. Se observa Magnesio y Silicio más a laderecha de la muestra, a la izquierda se detecta más Calcio. (Fuente: Elaboración propia)122
Capítulo IVAnálisis mediante Microscopía Electrónica de BarridoMappingFigura 4.53: Distribución Mapping elementos químicos en la superficie de 2ª Muestra con DañoCreciente. Destaca la distribución irregular del Magnesio en la muestra. (Fuente: Elaboración propia)123
Capítulo IVAnálisis mediante Microscopía Electrónica de Barrido3ª muestra con daño creciente: A/C 0.65 0.5% T4MicroanálisisFigura 4.54: Microanálisis de 3ª Muestra con Daño Creciente. Priman en la detección Calcio, Magnesio ySilicio en estado de óxidos. (Fuente: Elaboración propia)LinescanFigura 4.55: Linescan de 3ª Muestra con Daño Creciente. Distribución homogénea de elementos en lamuestra, incluido el límite de grano. (Fuente: Elaboración propia)124
Capítulo IVAnálisis mediante Microscopía Electrónica de BarridoMappingFigura 4.56: Distribución Mapping elementos químicos en la superficie de 3ª Muestra con DañoCreciente. Se observa Sílice y Calcio en el límite de grano, el resto está ocupado por Magnesio de lamuestra. (Fuente: Elaboración propia)125
Capítulo IVAnálisis mediante Microscopía Electrónica de Barrido1ª muestra con daño decreciente: A/C 0.55 1.0% T3MicroanálisisFigura 4.57: Microanálisis de 1ª Muestra con Daño Decreciente. Predomina la presencia de Calcio, Silicioy Aluminio. (Fuente: Elaboración propia)LinescanFigura 4.58: Linescan de 1ª Muestra con Daño Decreciente. Distribución homogénea de elementos a lolargo de la línea en la muestra. (Fuente: Elaboración propia)126
Capítulo IVAnálisis mediante Microscopía Electrónica de BarridoMappingFigura 4.59: Distribución Mapping elementos químicos en la superficie de 1ª Muestra con DañoDecreciente. Se presenta una distribución homogénea de los elementos. (Fuente: Elaboración propia)127
Capítulo IVAnálisis mediante Microscopía Electrónica de Barrido2ª muestra con daño decreciente: A/C 0.55 1.0% T4MicroanálisisFigura 4.60: Microanálisis de 2ª Muestra con Daño Decreciente. Se manifiestan en mayor cantidad loselementos Calcio, Magnesio y Silicio. (Fuente: Elaboración propia)LinescanFigura 4.61: Linescan de 2ª Muestra con Daño Decreciente. Distribución homogénea de elementos en lalínea que atraviesa la muestra. (Fuente: Elaboración propia)128
Capítulo IVAnálisis mediante Microscopía Electrónica de BarridoMappingFigura 4.62: Distribución Mapping elementos químicos en la superficie de 2ª Muestra con DañoDecreciente. Se observa Magnesio uniformemente distribuido en la muestra. (Fuente: Elaboración propia)129
Capítulo IVAnálisis mediante Microscopía Electrónica de Barrido3ª muestra con daño decreciente: A/C 0.55 1.0% T5MicroanálisisFigura 4.63: Microanálisis de 3ª Muestra con Daño Decreciente. Se detectaron en mayor cantidad Calcio,Silicio y Aluminio. (Fuente: Elaboración propia)LinescanFigura 4.64: Linescan de 3ª Muestra con Daño Decreciente. Sílice, Calcio y Aluminio son los elementospresentes en mayor cantidad, el resto en trazas más pequeñas, pero distribuidas en toda la muestra.(Fuente: Elaboración propia)130
Capítulo IVAnálisis mediante Microscopía Electrónica de BarridoMappingFigura 4.65: Distribución Mapping elementos químicos en la superficie de 3ª Muestra con DañoDecreciente. Se aprecia Calcio, Silicio y Fierro bien distribuidos en la muestra. (Fuente: Elaboraciónpropia)131
Capítulo IVAnálisis mediante Microscopía Electrónica de Barrido4.5 Análisis Imágenes Microscopia Electrónica.4.5.1 Hipótesis de Trabajo.En el análisis están presentes dos razones de agua/cemento, la primera de 0.55 (conmayor cantidad de cemento) es más densa, homogénea y más compacta que la derazón agua/cemento 0.65, lo que ayuda a que sea más impermeable ante la solución deSulfato de Magnesio. Cabe destacar que la porosidad incrementada debido a unaumento de la relación agua / cemento acarrea una disminución de la compacidad y enconsecuencia de la resistencia química del hormigón. Por lo que se espera un mejorcomportamiento de las muestras con razón A/C 0.55.También se encuentran las distintas adiciones de Nanosílice (0, 0.5, 1, 1.5 %), de lascuales y según lo expuesto en los resultados de Ensayo de Inmersión, se espera unmejor comportamiento por parte de las muestras con 1.5% de adición de nanopartículasde sílice, ya que éstas tienen una mayor formación de nano-cemento que rellena losporos y por ende presentaron la menor pérdida de material ante el ataque del sulfato demagnesio4.5.24.5.2.1Análisis de Muestras.Muestra Control Buena (A/C 0.55 1.5% T0) y Muestra Control Mala(A/C 0.65 0.5%T0).Las muestras controles, son las muestras que no fueron sometidas a Ensayo deInmersión, por eso se denominan con tiempo 0, poseen distintas razón agua/cemento ydiferentes adiciones de Nanosílice expresada en porcentaje.La muestra control buena presenta menor razón A/C, por lo que es más densa alposeer mayor cantidad de cemento que la control mala, además contiene mayor adiciónde nanosílice lo que la hace aún más compacta, por la producción de nanocemento yrelleno de poros que esto implica.Se analizan en el Microscopio Electrónico de Barrido, con el objetivo de compararlascon las muestras más y menos dañadas por la agresión química del Sulfato deMagnesio. La denominada Muestra Control Buena se compara con la probeta conmenor pérdida de material y la Muestra Control Mala con la probeta que ha sufridomayor pérdida de masa.132
Capítulo IV4.5.2.2Análisis mediante Microscopía Electrónica de BarridoMuestra con Menor pérdida de material: A/C 0.55 1.5%En la muestra que presentó menos perjuicio debido al ataque de sulfato de magnesio,con una disminución de peso de sólo un 0.06% a los 28 días de sumersión en lasolución, se aprecia una distribución homogénea de partículas y crecimiento de cristalesen el concreto, además de una incipiente formación de etringita, la cual se evidenciaque queda en la superficie, no logrando penetrar a la interfase del sólido.4.5.2.3Muestra con Mayor pérdida de material: A/C 0.65 0.5%En la probeta que resultó más afectada, con una pérdida de material del 0.985 % a los42 días de ensayo de inmersión, se evidencia una distribución heterogénea departículas, además de una segregación de las mismas y zonas en que se presentaremoción de microconstituyentes.Presencia de Etringita, aunque no de manera continua ni uniforme, si no que más bienpuntualizada, pero si con distintos grados de crecimiento.Al realizar la comparación entre ambas, se puede observar que la Muestra con Menorpérdida de material, se ve claramente más sólida, compacta, con una morfología másfina y regular que la denominada Muestra con mayor pérdida de material, ya que enesta última se evidencia la acción del ataque químico del Sulfato de Magnesio.Al hacer un paralelo entre las muestras con menor y mayor pérdida de material y susrespectivas muestras controles, se obtiene que para el caso de la Muestra ControlBuena se aprecia claramente la morfología y fases de los cristales y estructura delconcreto, a diferencia de la Muestra Control Mala en la que su superficie se caracterizapor ser muy irregular, en cuanto a cristales, límites de grano y textura de la muestra.4.5.2.4Análisis Grupo de Muestras con Daño Creciente.Se estudia en este grupo 3 muestras de razón A/C 0.65, con adición de 0.5% deNanosílice, correspondientes a tres tiempos consecutivos (T2, T3 y T4) y ordenadas demenor a mayor pérdida de material, con el objetivo de poder hacer un seguimiento en eltiempo al comportamiento de estas probetas de mortero con
en un tubo de rayos catódicos (CRT). El barrido del haz está sincronizado con el barrido del CRT y produce una relación uno a uno entre puntos de la muestra y puntos en el CRT. 4.1.2 Aplicaciones del Microscopio Electrónico de Barrido en Hormigones y áridos. - Mineralogía de cementos: clínquer, alitas, etc.