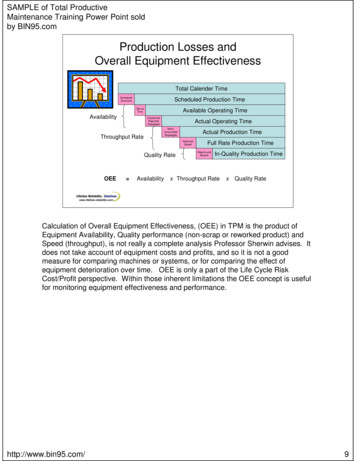
Transcription
SAMPLE of Total ProductiveMaintenance Training Power Point soldby BIN95.comProduction Losses andOverall Equipment EffectivenessTotal Calender TimeScheduledDowntimeScheduled Production TimeSet-upTimeAvailabilityAvailable Operating TimeUnplannedReportedStoppagesActual Operating TimeMinorUnrecordedStoppagesThroughput RateActual Production TimeReducedSpeedQuality RateOEE AvailabilityFull Rate Production TimeRejects andReworkIn-Quality Production Timex Throughput Ratex Quality Ratewww.lifetime-reliability.comCalculation of Overall Equipment Effectiveness, (OEE) in TPM is the product ofEquipment Availability, Quality performance (non-scrap or reworked product) andSpeed (throughput), is not really a complete analysis Professor Sherwin advises. Itdoes not take account of equipment costs and profits, and so it is not a goodmeasure for comparing machines or systems, or for comparing the effect ofequipment deterioration over time. OEE is only a part of the Life Cycle RiskCost/Profit perspective. Within those inherent limitations the OEE concept is usefulfor monitoring equipment effectiveness and performance.http://www.bin95.com/9
SAMPLE of Total ProductiveMaintenance Training Power Point soldby BIN95.comTotal Productive Maintenance is operator driven reliability:The Operators’ Creed of TPM – Keep it clean Keep it lubricated Monitor for degradation Maintain it before production is affected Simplify and improve itBreakdownsSetup nsZEROStoppagesZEROOperators are likely to recognise before anyone else that a machine needs to bereplaced or overhauled, or a system modified.David Sherwin, Maintenance and Reliability Professor, tells us that machinedeterioration is slowed under TPM by the primary care given to the machine by itsoperator. The operator can delay the need for maintenance by focusing on keyequipment health factors. TPM does not exclude Preventive Maintenance (PM) bytechnicians, in fact it is required, but there is no specific strategy for it within TPM,and it is almost bound to be neglected if the factory gets too busy, which is justwhen it is most needed. To address this risk the PM work is planned and scheduledby the maintenance group.http://www.bin95.com/12
SAMPLE of Total ProductiveMaintenance Training Power Point soldby BIN95.com7 Visual Quality Management Tools forTPM Problem SolvingIn a TPM program the Team are always looking to ‘see’ what causes the problems so thatthey know when it is time to act, and know what problem needs to be fixed. The sevenvisual quality control tools help to identify relationships and notice interactions between arange of factors that affect the problem. You come to understand better what to do.www.lifetime-reliability.comWhen solving a problem it is necessary to know what to do and what is, or is not,working. The 7 quality control tools shown on the slide let us view a problem in anumber of ways to help pinpoint the issues. They are used by the TPM team toanalyse the factors that have the greatest influence on a problem and to focus theirefforts for the highest payback when fixing the problem.http://www.bin95.com/46
SAMPLE of Total ProductiveMaintenance Training Power Point soldby BIN95.comThe People of Successful TPMPeople want tofeel valuable,and to bevalued. Youcan do bothwhen youincrease theirworth to abusiness. Thisdiagram showswhere youneed to takeyour people,and as aconsequencethey will bringyour businesswith them.Overcoming the /www.bin95.com/51
SAMPLE of Total ProductiveMaintenance Training Power Point soldby BIN95.comProviding the whole ‘TPM Mix’Vision Targets Team . Processes . Measurementwww.lifetime-reliability.comHopefully you are now more aware of what TPM will require of you and yourorganization. It has more to do with managing change and challenging mindsetsthan introducing a new way to run your operation. In time your productionequipment will be managed by the people on the ‘shopfloor’, while managers will bemore focused on developing new business opportunities. In order for this to happenthe people now running your plant and equipment will need to learn how to run theirmachines well. More importantly they will need to learn how to improve theproduction equipment so it can perform at highest productivity and efficiency. TPMis a process to let people master the skill they need to do that.http://www.bin95.com/58
SAMPLE of Total ProductiveMaintenance Training Power Point soldby BIN95.comA Case Study - Beginning with TPMThis is an example of applying the TPMphilosophy on mining equipmentJumbo Drill at WorkBecause TPM focuses on identifying the root causes of poor equipment performance itswww.lifetime-reliability.compurposeof improving equipment operation is universally applicable across all machinery.http://www.bin95.com/67
SAMPLE of Total ProductiveMaintenance Training Power Point soldby BIN95.comTPM Change Management RequirementsPressure for change Policy and action plan in place Regular reviews Active commitment from topmanagement Policy agreed and communicatedto all staff Board level “champion” appointedClear Shared Vision High level of awareness and support atall levels Staff highly motivated Representatives from all levels ofmanagement chain involved in planningprocess and drawing up action plan(s) All staff given opportunity to make aninputCapacity (resources)Action (and performance) Resources (staff and funding) routinelycommitted Cost savings re-invested for furtherimprovements Action being taken and embeddedthroughout the organisation Monitoring and reporting of progress Key staff working on plans andprojects. Staffing and funding needs identifiedand resources becoming available “Champion” appointed at middlemanagement level (to support theBoard’s “Champion”). Training & development needsassessment Wider engagement across theorganisation ‘Low-cost’ and more ‘no-cost’measures implemented Commencement of action at somelevels of the organisation. Some ‘no-cost’ measuresimplementedI can see Sam as the middle management ‘champion’, and Walt as the board ‘champion’.You and I are the ‘key staff’. The ‘no cost’ measures are the ‘early wins’ in Bill’s case study.We’ll only get Walt’s support if he can see the benefit of TPM.In that case we need to make justification a high priority in our planning.www.lifetime-reliability.comThe bullet points from the ‘Change Management Matrix’ become the requirementsand actions to be undertaken and achieved as the plan to make TPM part of normalbusiness practice unfolds.http://www.bin95.com/82
Total Productive Maintenance powerpoint sample Author: Business Industrial Network Subject: Introduction Total Productive Maintenance (TPM) Keywords: tpm,total productive maintenance,productive maintenance,tpm case study,tpm team,hidden fatory,oee,risk reduction,change management,nippondenso,nakajima,tqm Created Date: 2/19/2008 12:57:29 PM