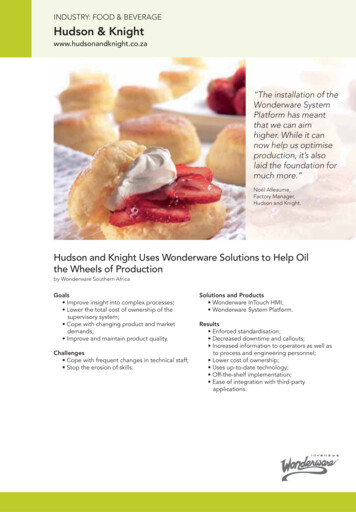
Transcription
INDUSTRY: FOOD & BEVERAGEHudson & Knightwww.hudsonandknight.co.za“The installation of theWonderware SystemPlatform has meantthat we can aimhigher. While it cannow help us optimiseproduction, it’s alsolaid the foundation formuch more.”Noël Alleaume,Factory Manager,Hudson and Knight.Hudson and Knight Uses Wonderware Solutions to Help Oilthe Wheels of Productionby Wonderware Southern AfricaGoals Improve insight into complex processes; Lower the total cost of ownership of thesupervisory system; Cope with changing product and marketdemands; Improve and maintain product quality.Challenges Cope with frequent changes in technical staff; Stop the erosion of skills.Solutions and Products Wonderware InTouch HMI; Wonderware System Platform.Results Enforced standardisation; Decreased downtime and callouts; Increased information to operators as well asto process and engineering personnel; Lower cost of ownership; Uses up-to-date technology; Off-the-shelf implementation; Ease of integration with third-partyapplications.
Food & BeverageBoksburg, South Africa - Whether for cooking,flavouring, in margarine or any number of other uses,we come in contact with edible fats and oils everyday and their manufacture follows critical health andquality criteria. As a leading producer of edible fatsand oils, Hudson and Knight recognised the need toupgrade their extensive supervisory system toprovide operators a greater degree of insight intocomplex processes, to lower the total cost ofownership and to cope with changing product andmarket demands.BackgroundHudson and Knight found itself with an outdatedsupervisory system that was difficult to maintain andimprove, wasn’t really based on Object OrientedTechnology (OOT), had no built-in development securityand auditing facilities and no server scripting facility.Constant changes in technical staff meant that thesystem standards started to diverge becauseupdating of the redundant servers could often not besynchronised with the result that the quality of thesystem was slowly being eroded. At the operationallevel, a lack of understanding of the process coupledwith a non-intuitive control system was affectingdowntime and production efficiency.The ProcessThe plant receives various crude and semi-refinedoils from an on-site sunflowerseed mill and from tankers withmaterial sourced from all overthe world.Wonderware InTouch HMI, Wonderware System Platform.temperatures in excess of 180 C for hours on end inthe customer’s fryers.The processed oils are then shipped to on-sitecustomers (e.g. for margarine production), tankersfor national distribution and to packaging lines forthe retail market.Solution SelectionIt was decided to replace the supervisory system withone that is:Truly object orientated and secure – This wouldenable improvements to be made easily, quickly andin a controlled fashion so that standards would beprotected and maintained at all times. This wouldalso protect the investment made in the new controlsystem. The ability to easily include improvementswould also facilitate a lower-cost, continuousoptimisation process that would address the skilllevels of operational staff by providing them withmore pertinent information and a control systeminterface that was easier to understand.Reliable and scalable – Wonderware’s ArchestrA (V2and V2.1) has a proven track record of coping withsmall as well as very large systems. “We have onesystem running 350 000 I/O very successfully,” saysMartyn Daniels, Operational Unit Manager at QuadAutomation (chosen system integrator for thisproject). “We also know that the redundancy systemworks very well. On the old system, there was noautomatic changeover of servers.”All oils refined at the Hudsonand Knight refinery go througha process of refining anddeodorising to remove anyodours that could taint thecustomer’s finished product.Seed oils are then subjected toa winterising process toremove any waxes which couldcloud the oil if chilled. Oils thatare destined for deep fryingthen have antioxidants andantifoaming agents added tothem to enable them to handlethe treatment that they willFigure 1: System topology at Hudson and Knight.receive when heated to
Food & BeverageWonderware InTouch HMI, Wonderware System Platform.Managed and server-sidescripting code – This wouldenable the protection andsecuring of source code all inthe same environment andthere would be less need forexternally-developed ActiveXcode and controls and theirmaintenance. Server-side codewould enable commonfunctions to be implementedat the back end making the jobof plant-wide changes fareasier. Server-side codingwould also help in reducing theduplication of code, using thehigh-end server hardware moreFigure 2: InTouch HMI view of a portion of the plant.effectively and lowering thehardware specification ofclients together with thealarms, the great majority of which were not theircomplexity of setting them up.responsibility but in someone else’s area. Theoperator’s login data provided the system with theMinimum downtime - Any changes andnecessary information to do this selective alarming;improvements to the new system would have to be Easier future application of area-based functionsdone with the minimum production downtime by– These include intelligent and conditional alarmsusing scheduled stock-takes while the old systemand events as well as SOP and HAZOP handling;would still be in operation should it be required. Easier future application of MES – An accurateand detailed area model would facilitate theHudson and Knight chose system integrator Quaddeployment of Manufacturing Enterprise Solutions.Automation. Software solutions selected for the newEqual attention was paid to the design of thesystem included the Wonderware System Platformderivation model which involves detailed Objectbased on ArchestrA technology, WonderwareOriented modelling that would enable globalInTouch HMI (Human Machine Interface),changes to be made quickly and precisely.Wonderware Information Server (WIS) and theWonderware Historian; this latter and WIS are part ofSolutions were developed for event sequencing,Wonderware System Platform.formulation management, batch scheduling andmaterials management. “The refinery is an intricate“Selecting ArchestrA technology and its componentsplant where any type of oil can be routed virtuallywould also allow for better integration of otheranywhere, which adds another level of complexity tosubsystems such as InBatch, Formulationmaterials management,” says Daniels.Management Module, Performance Software and theManufacturing Execution (MES) module,” addsRaw materials, WIP and finished goods are stored allDaniels. “This would result in a further reduction ofover the plant in tank farms and there are manycustomised engineering and third-party componentsroutes leading to and from these tank farms whichas well as a reduction of the need for maintenanceare connected to several processes that can transferand technical skills.”these products in or out at any time. The status,quality and age of all materials is monitored andreported on by the control system. Access to theImplementationtanks is governed by strict rules which are enforcedto prevent contamination. “This is extremelyCareful attention was paid to defining an accurateimportant, especially when some of these rawarea model of the plant for three important reasons:materials can cost as much as R50 000 / ton,” says Operators were to be notified of problems inDaniels.their areas of responsibility only - In the past,ArchestrA object capability allowed these rules to beoperators would be confronted with hundreds ofimplemented and enforced in a structured fashion
Food & Beveragewhich is easy to maintain. This object capability alsoallowed the implementation of a real-time materialsearch algorithm which assists operators in findingvalid tanks quickly and reliably.Information IntegrationLarge amounts of data are being stored by thesystem including all the historian data which is usedfor real-time trending purposes as well as all materialtransfer and batching transactions. Other datainclude data logs of laboratory analyses which can beentered after completion of the batch, automaticstock take and quality analysis of all tanks as well asthe logging of all raw material receipts and dispatchnotices of finished products.Wonderware InTouch HMI, Wonderware System Platform.What’s Next?While Hudson and Knight’s supervisory needs havebeen met, this project has, at the same time, laid thegroundwork for the company’s real business needswhich include: Conversion of Crystal reports-based MIS Intranet toWonderware Information Server (WIS) and MicrosoftReporting Services; Wonderware Performance Software (Real-timeOEE); Wonderware InBatch Software; Wonderware MES.All future enhancements have the mandate to helpHudson and Knight have the ability to react quicklyto changing market conditions and customerrequirements as well as rawmaterial variances while beingable to adopt the latestprocessing technologies andadapting to changing skilllevels.ConclusionFigure 3: Part of the complex tank-switching matrix.“In the past, it has been costly to make this dataavailable to operators where and when they neededit,” says Daniels. “ArchestrA is the enabler that’shelping Hudson and Knight to make better use of allthis information in a cost-effective and maintainablemanner.”Wonderware’s SQL DataGrid is used for displayingsequencing history (sequence/phase performance,analysis of delays, etc.), device history (performanceanalysis of any or all devices – sequences, motors,valves, etc.), status history (device states, tracking ofmanual operations – available on all devices) andmaterial movement in and out of storage andprocess vessels (current stock levels, transactionhistory and on-the-spot mass balancing).Effective industrial businessmanagement is more thanthrowing in a supervisorysystem and hoping for thebest. These systems monitorand control the fundamentalwealth-creation processes oftheir companies and providevital decision-supportinformation at many levels. Assuch, they need to be agile andscalable. They also form part of a much broaderpicture and their design must include this vital aspectbecause, by themselves, they can’t do it all. Aproperly-designed supervisory system should neveractually get old (except perhaps for the hardware).Its design should also ensure that its owner’sinvestment is protected by playing its role in thebroader set of requirements of productioncompanies (MES, ERP, MIS, etc.). So, it’s no longerjust about supervisory systems. It’s about the future,protecting investments and helping companiesachieve their business goals rather than simplyaddressing process control needs.This document was realized thanks to the support of:Hudson and Knight.
Food & Beveragewww.wonderware.fiRīgatel. 371 6738 1617info@wonderware.lvWonderware InTouch HMI, Wonderware System Platform.Helsinkitel. 358 9 540 4940automation@klinkmann.fiSt. Petersburgtel. 7 812 327 3752info@wonderware.ruMoscowtel. 7 495 641 1616info@wonderware.ruYekaterinburgtel. 7 343 287 1919info@wonderware.ruSamaratel. 7 846 273 95 85info@wonderware.ruКievtel. 38 044 495 33 40info@wonderware.com.uaVilniustel. 370 5 215 1646info@wonderware.ltTallinntel. 372 668 4500info@wonderware.eeМinsktel. 375 17 200 0876info@wonderware.by
Food & Beverage Wonderware InTouch HMI, Wonderware System Platform. Yekaterinburg tel. 7 343 287 1919 info@wonderware.ru St. Petersburg tel. 7 812 327 3752 info@wonderware.ru Moscow tel. 7 495 641 1616 info@wonderware.ru Кiev tel. 38 044 495 33 40 info@wonderware.com.ua Helsinki tel. 358 9 540 4940 automation@klinkmann.fi Vilnius tel .